So, having failed on the edge trimming thing I thought I'd deal with the next vital ingredient - the cutting guide for the router
As you can see my current straight edge is rather over endowed when cutting across the board, I also want to be able to reference the edge of the component rather than measure x cm off from the line.
I am using a trend up cutting shear cutter and was a little surprised at the amount of feathering I got off the first cut (which will form the guide for the router). A little work with a very blunt and poorly set plane sorted the feathers out without impacting on the straightness.
So now I've got the straight edge I need to screw it onto the bas board and then cut out the reference edge. To do this I set the router to the depth of the sacrificial MDF cutting surface with a thin bracket between the router turret and the depth stop. This means that once the bracket was removed the actual cut went 1.45mm into the MDF surface.
This resulted in a rather nicer cut straight off the board:
So now the jig is correctly set up but still attached to the 4x6' board which would make it rather unwieldy
Next job is to part it from the main board. I figured I'd be a cleaver clogs and use a different router to do this - I nice thin one so that I had a fine cut capability if I needed the thread the cut into a tight space. Sadly I manage to snap the cutter - nothing spectacular, it just came off during the first cut (set up the same way as the up cut one) - must be a basic user error, I guess I was taking too big a cut but I thought it would be able to handle 5mm or so.
Retreating from that Idea I just used the up cutter to part off the jig from the main board and the cut I get from it is great - it only needs a couple of wipes with 320 on a stiff board to get rid of the slight ridges from the router (why am I getting this - am I feeding too fast?)
Very pleased - this evening's job is to mark up all the components on one of the sheets ready to be cut out tomorrow.
Miles
As you can see my current straight edge is rather over endowed when cutting across the board, I also want to be able to reference the edge of the component rather than measure x cm off from the line.
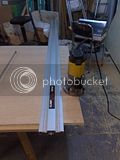
I am using a trend up cutting shear cutter and was a little surprised at the amount of feathering I got off the first cut (which will form the guide for the router). A little work with a very blunt and poorly set plane sorted the feathers out without impacting on the straightness.
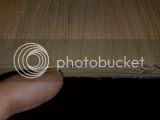
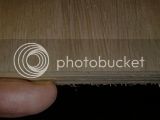
So now I've got the straight edge I need to screw it onto the bas board and then cut out the reference edge. To do this I set the router to the depth of the sacrificial MDF cutting surface with a thin bracket between the router turret and the depth stop. This means that once the bracket was removed the actual cut went 1.45mm into the MDF surface.
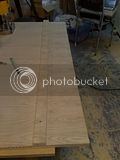
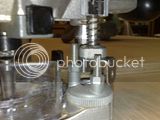
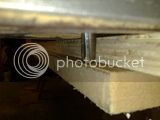
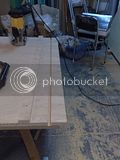
This resulted in a rather nicer cut straight off the board:
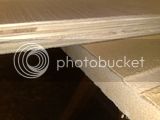
So now the jig is correctly set up but still attached to the 4x6' board which would make it rather unwieldy

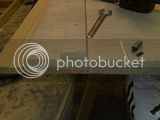
Retreating from that Idea I just used the up cutter to part off the jig from the main board and the cut I get from it is great - it only needs a couple of wipes with 320 on a stiff board to get rid of the slight ridges from the router (why am I getting this - am I feeding too fast?)
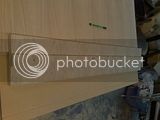
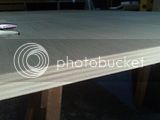
Very pleased - this evening's job is to mark up all the components on one of the sheets ready to be cut out tomorrow.
Miles