I've just found an old wooden spokeshave in a box of odds and sods, with really significant wear to the sole.
Not had a chance to try it on any wood yet, but my guess is that it's going to make it take a deep cut that's much easier to dig in.
With regards to sorting it out, would creating a shelf across the front of the sole and facing in brass be the best fix, or would an L-shaped front and sole facing of brass be better, or even letting in the brass just across the width of the blade?
See this sketch for clarity on what I mean.
Left to right: worn, sole faced, sole faced across mouth, front and sole faced.
Not had a chance to try it on any wood yet, but my guess is that it's going to make it take a deep cut that's much easier to dig in.
With regards to sorting it out, would creating a shelf across the front of the sole and facing in brass be the best fix, or would an L-shaped front and sole facing of brass be better, or even letting in the brass just across the width of the blade?
See this sketch for clarity on what I mean.
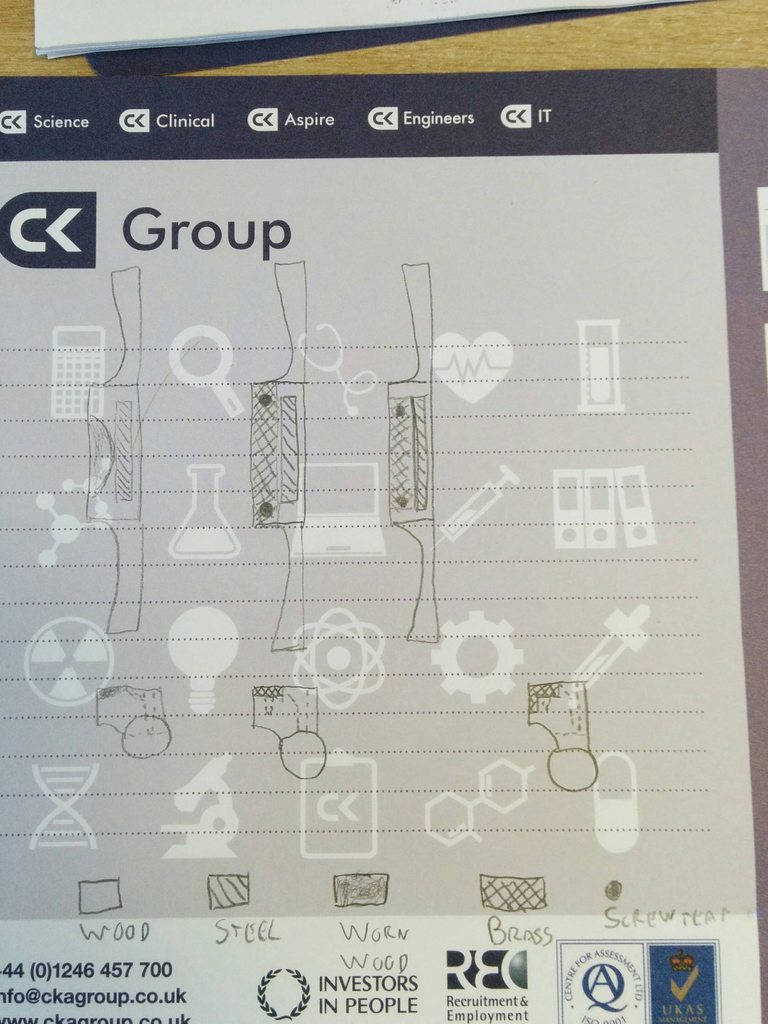
Left to right: worn, sole faced, sole faced across mouth, front and sole faced.