9fingers
Established Member
A while back I picked up a secondhand Startrite 18-S-1 bandsaw that was in a bit of a sorry state. New bearings and guides have got it running sweetly but it was missing band wheel brushes - normally two are fitted.
Metal dust was starting to get embedded in the tyres and new tyres are very expensive so I need to look after these ones
I've now fitted a brush to the driven bandwheel. I've also made a few other mods which may be of interest.
First the brush bought on ebay here http://cgi.ebay.co.uk/ws/eBayISAPI.dll? ... 0412799232
A simple angle bracket with the brush screwed on at an angle sweeps the full width of the tyre. I've only put one on for now and I'll see how it goes. For anyone retro fitting a brush, the thread tapped into the body of the saw is 5/16 Whitworth. If you don't happen to have a suitable bolt then the hole can be drilled out 8.5mm and tapped M10.
The "1" in the model number 18-S-1 means it is a single speed machine. Other models are -5 and -10 with that number of speeds.
Unmodified, the blade speed is around 3500 feet per minute which is fine for wood but I also work in plastic and metal which needs much lower speeds. My saw is a 3 phase model and I have fitted an inverter which gives me not only operation from a single phase supply but also gives variable speed.
Realistically, an inverter can only give useful power output down to 1/5th of normal speeds although mine is programmed for 1/10th of normal. The inverter is fitted in the space occupied by the NVR switch and performs this function as well.
and close up
The inverter alone really only gives useful minimum speed of 700 feet per minute which is still too fast for metal other than thin soft metals such as aluminium.
The next modification is to fit alternative belt drive.
This is the standard belt drive fitted with the driven V pulley hidden by the new MDF pulley
The new low speed belt drive uses a poly V belt - the sort you find in most washing machines. These are much more flexible and so give good grip on small diameter pulleys like the one below.
There is no need to cut the multiple Vs on the big pulley - another tip taken from the washing machine design that donated the belt.
Either belt is tensioned by the weight of the motor as per the original Startrite design.
Both new pulleys are bolted onto the existing ones and turned to run concentrically
In the low speed mode, the high speed belt hangs off the top bearing housing out of the way
The original belt drive gives a ratio of about 2.5 :1 and the low speed drive is about 8.5 :1
The result of combining the belts change and the inverter gives a working range of 100 to 3500 FPM which compares well to the manufacturers 10 speed version that offers 56 to 3200 FPM.
The inverter has a speed control knob fitted which I still use but the stop and start buttons are rather small and fiddly so I have remoted these to an eye level control box here
The grey box also has the transformer for the low voltage worklight. All these parts were robbed from a cheapo Argos desk lamp bought for a few quid in the sales. Eventually I will paint over the translucent blue lamp head which is "so last decade" :lol:
The photo also shows the Axminster fence fitted as the original one had been lost by previous owners.
All in the mods cost me about £50 plus the fence which was a present and have transformed the saw into a versatile machine.
Bob
Metal dust was starting to get embedded in the tyres and new tyres are very expensive so I need to look after these ones
I've now fitted a brush to the driven bandwheel. I've also made a few other mods which may be of interest.
First the brush bought on ebay here http://cgi.ebay.co.uk/ws/eBayISAPI.dll? ... 0412799232
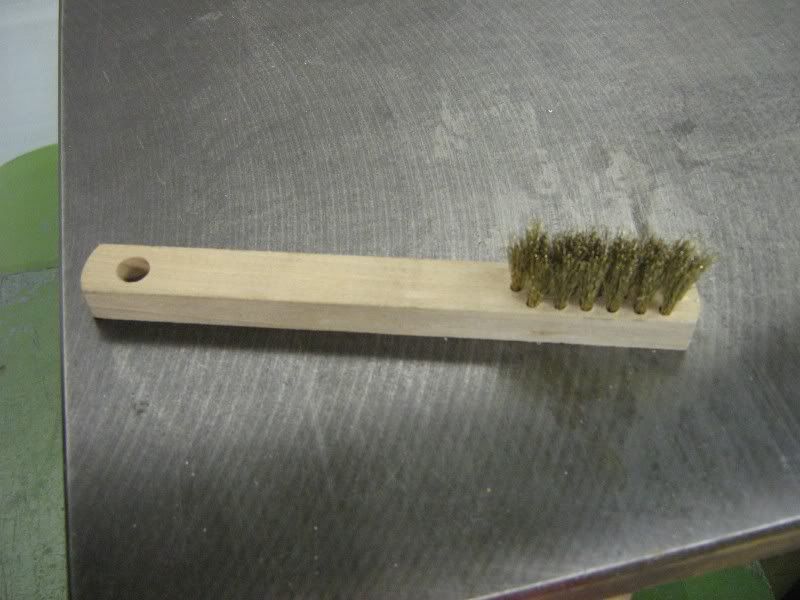
A simple angle bracket with the brush screwed on at an angle sweeps the full width of the tyre. I've only put one on for now and I'll see how it goes. For anyone retro fitting a brush, the thread tapped into the body of the saw is 5/16 Whitworth. If you don't happen to have a suitable bolt then the hole can be drilled out 8.5mm and tapped M10.
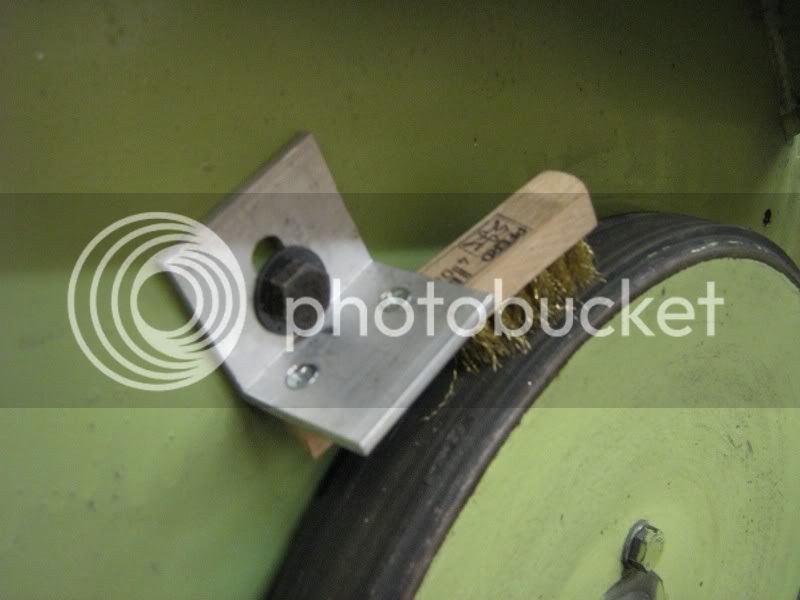
The "1" in the model number 18-S-1 means it is a single speed machine. Other models are -5 and -10 with that number of speeds.
Unmodified, the blade speed is around 3500 feet per minute which is fine for wood but I also work in plastic and metal which needs much lower speeds. My saw is a 3 phase model and I have fitted an inverter which gives me not only operation from a single phase supply but also gives variable speed.
Realistically, an inverter can only give useful power output down to 1/5th of normal speeds although mine is programmed for 1/10th of normal. The inverter is fitted in the space occupied by the NVR switch and performs this function as well.
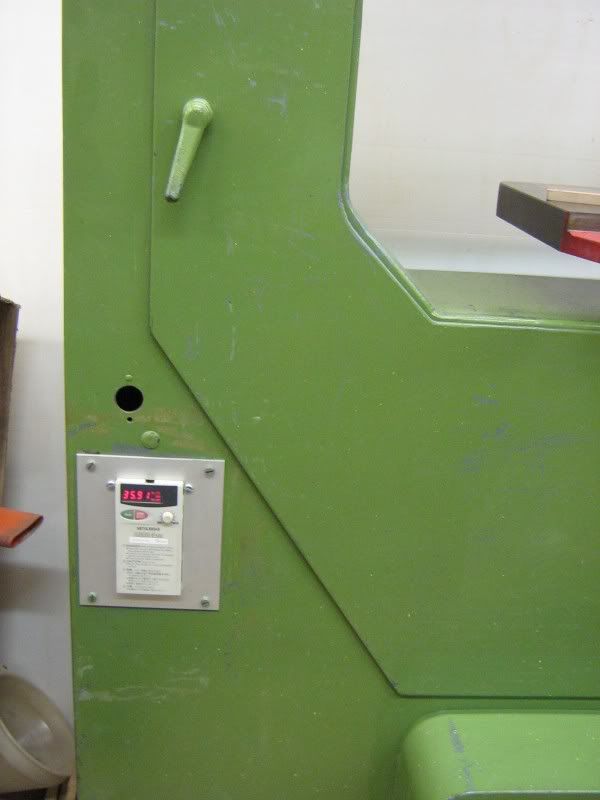
and close up
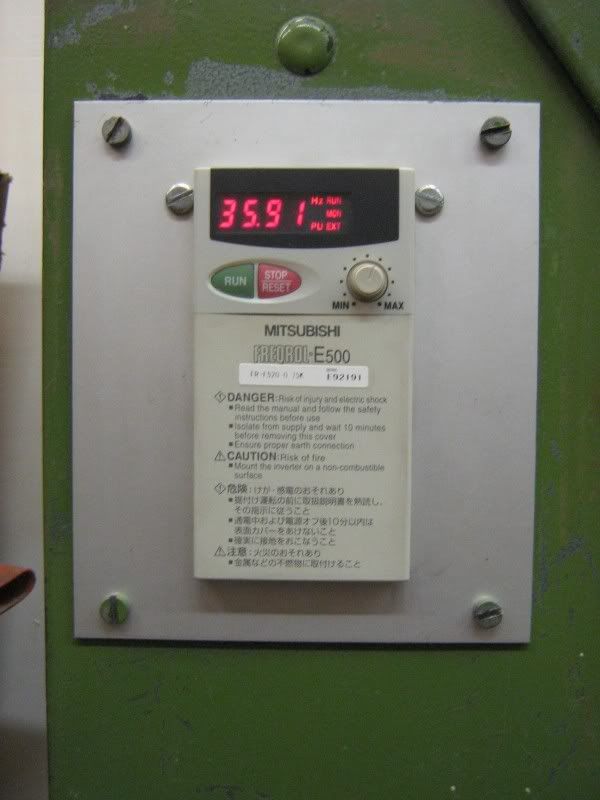
The inverter alone really only gives useful minimum speed of 700 feet per minute which is still too fast for metal other than thin soft metals such as aluminium.
The next modification is to fit alternative belt drive.
This is the standard belt drive fitted with the driven V pulley hidden by the new MDF pulley
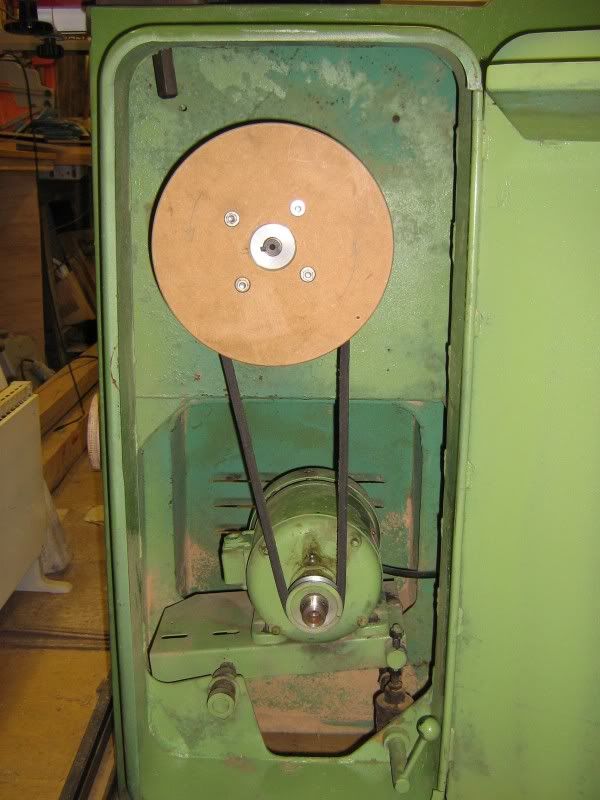
The new low speed belt drive uses a poly V belt - the sort you find in most washing machines. These are much more flexible and so give good grip on small diameter pulleys like the one below.
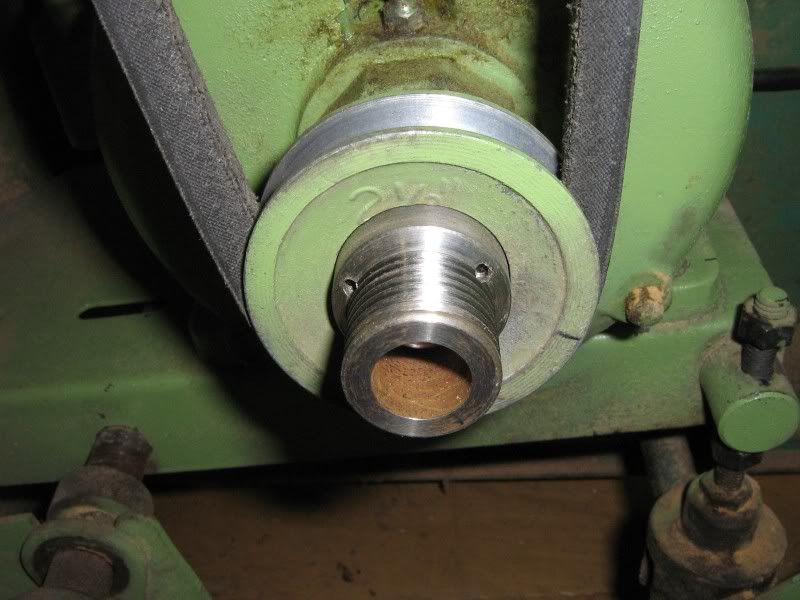
There is no need to cut the multiple Vs on the big pulley - another tip taken from the washing machine design that donated the belt.
Either belt is tensioned by the weight of the motor as per the original Startrite design.
Both new pulleys are bolted onto the existing ones and turned to run concentrically
In the low speed mode, the high speed belt hangs off the top bearing housing out of the way
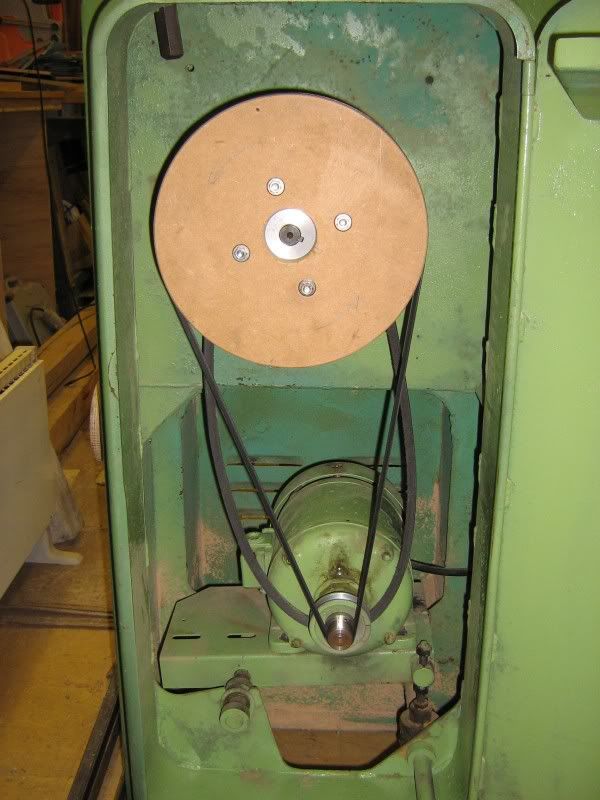
The original belt drive gives a ratio of about 2.5 :1 and the low speed drive is about 8.5 :1
The result of combining the belts change and the inverter gives a working range of 100 to 3500 FPM which compares well to the manufacturers 10 speed version that offers 56 to 3200 FPM.
The inverter has a speed control knob fitted which I still use but the stop and start buttons are rather small and fiddly so I have remoted these to an eye level control box here
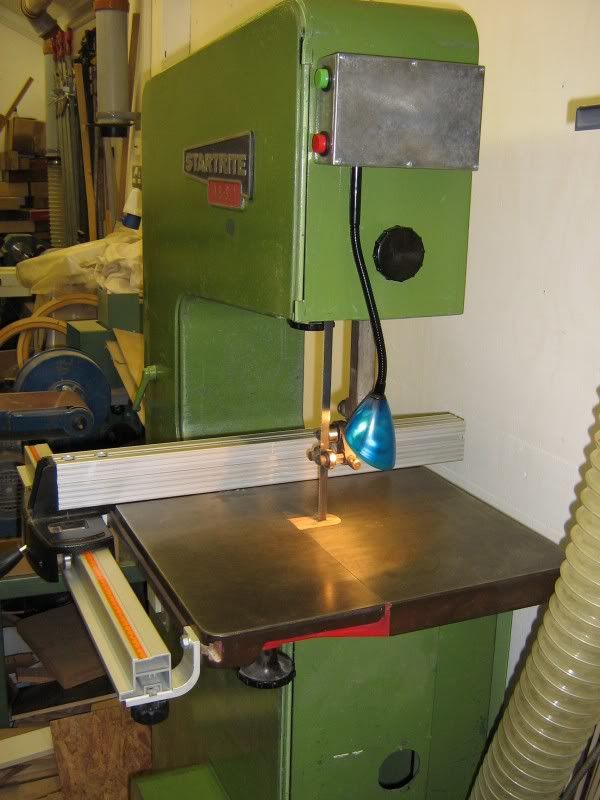
The grey box also has the transformer for the low voltage worklight. All these parts were robbed from a cheapo Argos desk lamp bought for a few quid in the sales. Eventually I will paint over the translucent blue lamp head which is "so last decade" :lol:
The photo also shows the Axminster fence fitted as the original one had been lost by previous owners.
All in the mods cost me about £50 plus the fence which was a present and have transformed the saw into a versatile machine.
Bob