wcndave
Established Member
There seems to be a gap where I am, nobody sells this:
Instead I get this:
Apart from the sheer effort and hassle of dealing with extremely large pieces without industrial strength tooling, I have a lot of cupped boards.
The plan was to make some 30cm wide by 12-16mm thick boards that were to be used for drawer sides.
The raw stock is 34mm nominal, however i think the bottom of the sides are higher than the top of the middle in this board!
The only way I can see to use this as planned, is to rip down middle, get the board all planed and thicked, and then join them back together again.
Does anyone think that would be a bad idea strength wise? Any other suggestions to achieve what I am hoping?
Thanks guys, you're the best!
(You can read more about it here)
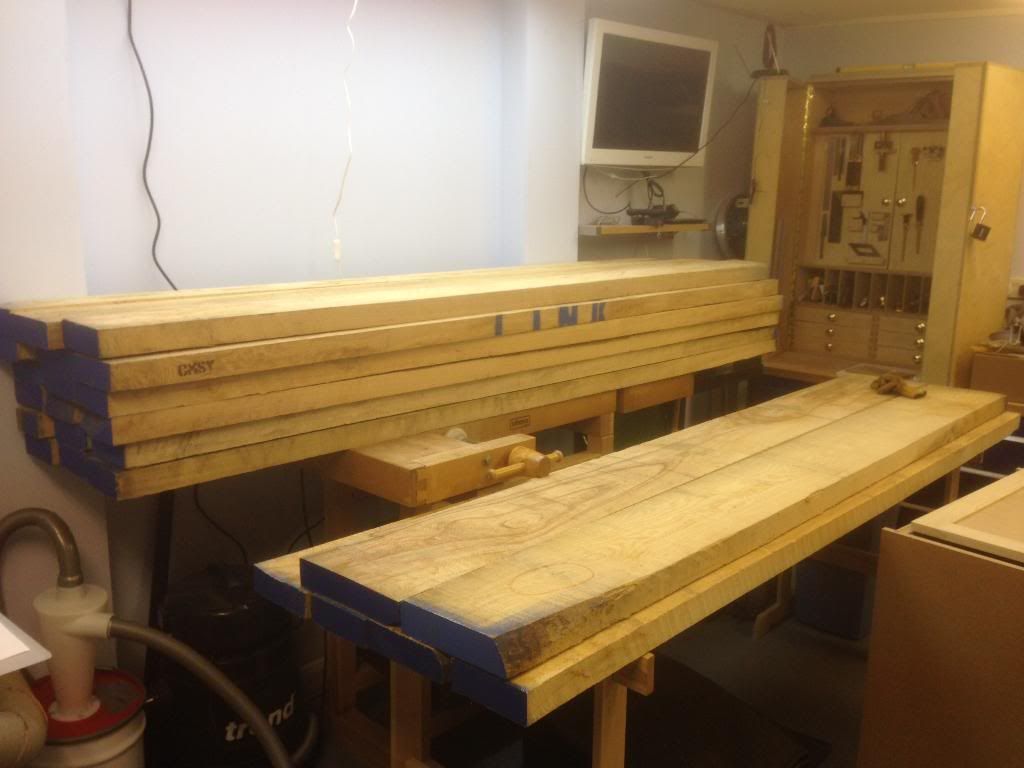
Instead I get this:

Apart from the sheer effort and hassle of dealing with extremely large pieces without industrial strength tooling, I have a lot of cupped boards.

The plan was to make some 30cm wide by 12-16mm thick boards that were to be used for drawer sides.
The raw stock is 34mm nominal, however i think the bottom of the sides are higher than the top of the middle in this board!
The only way I can see to use this as planned, is to rip down middle, get the board all planed and thicked, and then join them back together again.
Does anyone think that would be a bad idea strength wise? Any other suggestions to achieve what I am hoping?
Thanks guys, you're the best!
(You can read more about it here)