johnny.t.
Established Member
Took the camera out to the shed this morning.
Started off with a crotch of ash and split it in half with the chainsaw.
Trimmed it near round with the chainsaw and put it on the lathe with the screw chuck.
Flattened the back off enough to form the dovetail socket for the chuck and mark out the foot.
Formed the back and started to find holes! :shock:
Reversed, cut the front but sadly had to loose a couple of inches due to those holes...
The front was then finished and the whole piece reversed onto a disc of plywood and held in place with the tailstock to finish the foot(I forgot to take a pic
).
The finished article.
Comments welcomed.
JT
Started off with a crotch of ash and split it in half with the chainsaw.

Trimmed it near round with the chainsaw and put it on the lathe with the screw chuck.
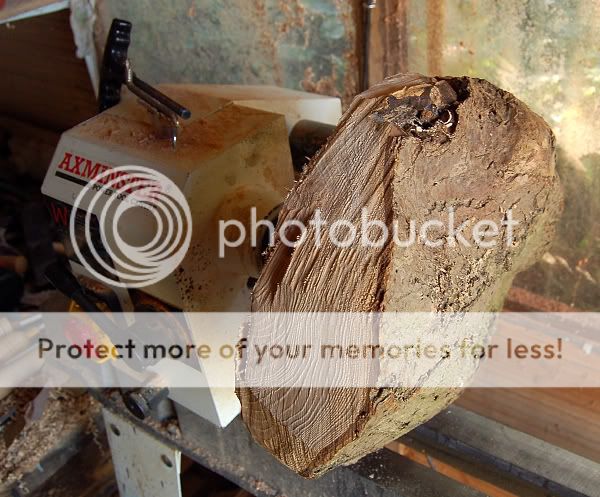
Flattened the back off enough to form the dovetail socket for the chuck and mark out the foot.
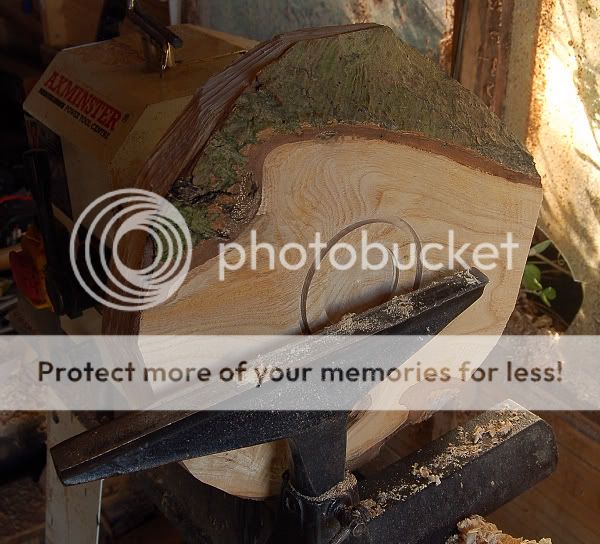
Formed the back and started to find holes! :shock:
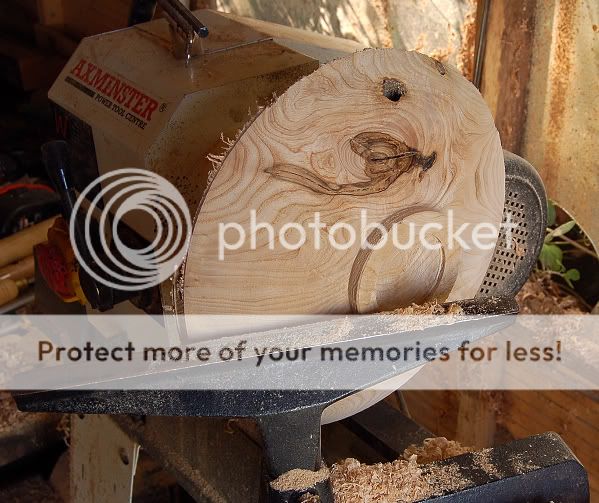
Reversed, cut the front but sadly had to loose a couple of inches due to those holes...
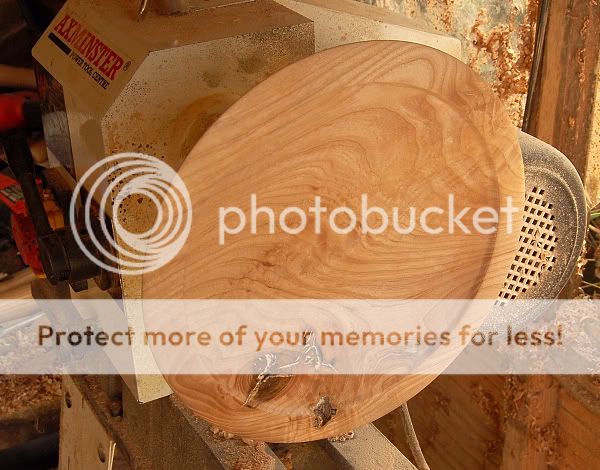
The front was then finished and the whole piece reversed onto a disc of plywood and held in place with the tailstock to finish the foot(I forgot to take a pic
The finished article.
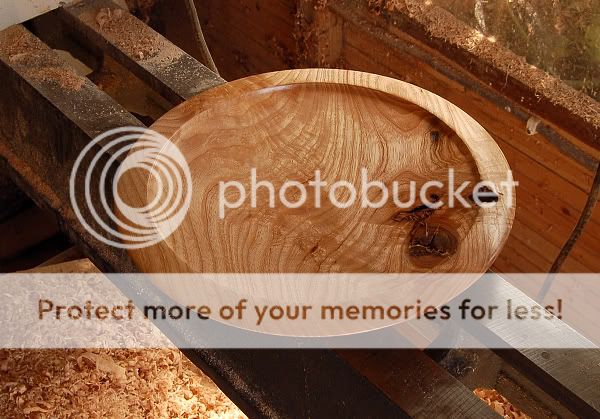
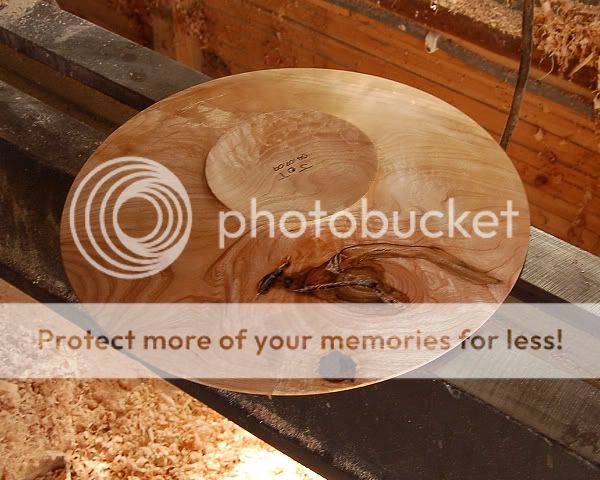
Comments welcomed.
JT