Seb Palmer
Established Member
I decided to try and make a drill-powered lathe, in the manner of Izzy Swan, as seen on his YouTube channel. I thought I'd share my misadventures, in the hope that folk here might help point me in the direction of some solutions to the myriad issues that caused me grief.
I made the 'two towers', pictured above, from some old off-cuts of oak parquet (that was what I was told it was when I bought it), and had a pig of a time trying to get it square. In the end I gave up. None of my tools are very good: e.g, I just got a cheap chopsaw (£20), off Gumtree, 'cause my Rage mitre-saw died on me (I have another post here on that topic!). Try as I might, I can't get it truly square in either direction. It's a helluva lot better than it was when I bought it, but it just ain't square.
My self-built table saw, ditto. My bandsaw, similar but different issues. And my only possibly decent bit of kit - Kity 636 planer thicknesser - is still not set up (need to work out pulley ratios and add a wheel/get the motor attached, etc.). In short, nothing is ever truly flat or square. It's a bloomin' pain.
Anyway, I decided what the heck and persevered with making these two components, fitting M8 threaded rod, nuts, and skateboard bearings. Izzy Swan's plans involve bending the tangs on T-nuts 180°. Whatever I tried, this simply snapped them off.
So, as pictured above, I drilled out the threads on one T-nut, and glued it back to back - using 5-min epoxy - with one that had all the tangs broken off it. I had high hopes for this solution to the problem of breaking tangs. Next issue: my Hitachi corded drill has the wrong sort of chuck, so I had to buy an adaptor, so as to have a normal old-fashioned one, with which to grasp the threaded rod in the head-stock.
Having set it all up, with a load of clamps, for a test, I found that there's a lot of play in the whole assemblage, as all the parts have slightly different diameters. This, coupled with the off-square-ness of everything, means the whole thing judders and wobbles a ridiculous amount.
My butchery! Partly done with chisels, partly with a rasp...
Perhaps the whole disaster I had today was also due to picking the wrong wood? I tried turning some rosewood. Very dense, hard stuff. I tried several chisels (I have no proper wood-turning tools), and all they did was knock the chuck loose, undo the epoxy glue (so my cherished pronged T-nut assemblage fell apart). Drilling the holes for the two lathe rods was easy enough. So I sharpened the chisels. No improvement.
I've made a second pronged nut, but that to was quickly rent asunder, so I'm regluing them both. And I'll try again with a softer wood tomorrow. I'll also get all my chisels razor sharp. But I found the whole thing, which has been two days work - Izzy Swan's video suggests it's a simple 10-minute build! - quite depressing.
I wish I just had the money to buy some decent tools!
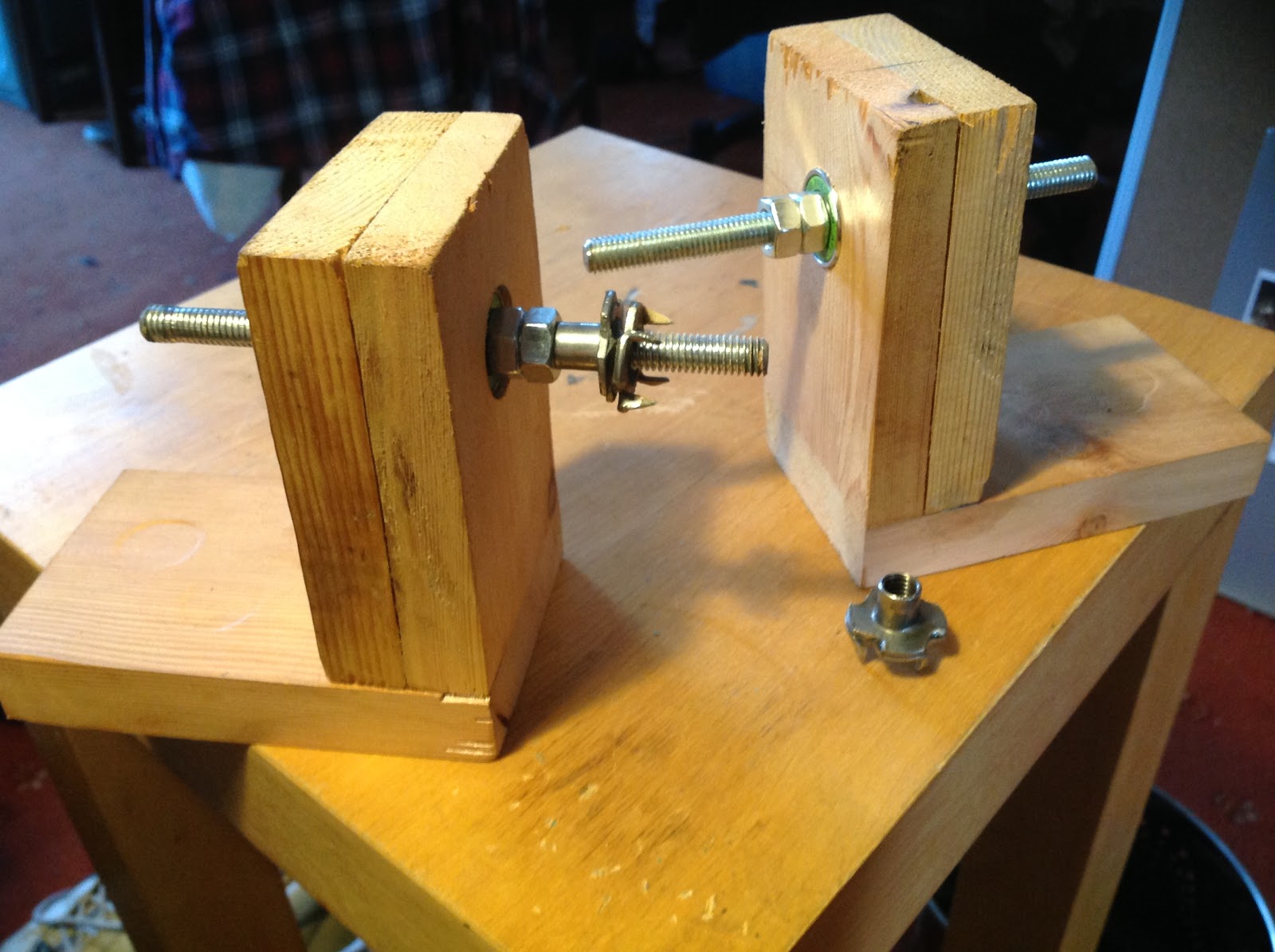
I made the 'two towers', pictured above, from some old off-cuts of oak parquet (that was what I was told it was when I bought it), and had a pig of a time trying to get it square. In the end I gave up. None of my tools are very good: e.g, I just got a cheap chopsaw (£20), off Gumtree, 'cause my Rage mitre-saw died on me (I have another post here on that topic!). Try as I might, I can't get it truly square in either direction. It's a helluva lot better than it was when I bought it, but it just ain't square.
My self-built table saw, ditto. My bandsaw, similar but different issues. And my only possibly decent bit of kit - Kity 636 planer thicknesser - is still not set up (need to work out pulley ratios and add a wheel/get the motor attached, etc.). In short, nothing is ever truly flat or square. It's a bloomin' pain.
Anyway, I decided what the heck and persevered with making these two components, fitting M8 threaded rod, nuts, and skateboard bearings. Izzy Swan's plans involve bending the tangs on T-nuts 180°. Whatever I tried, this simply snapped them off.

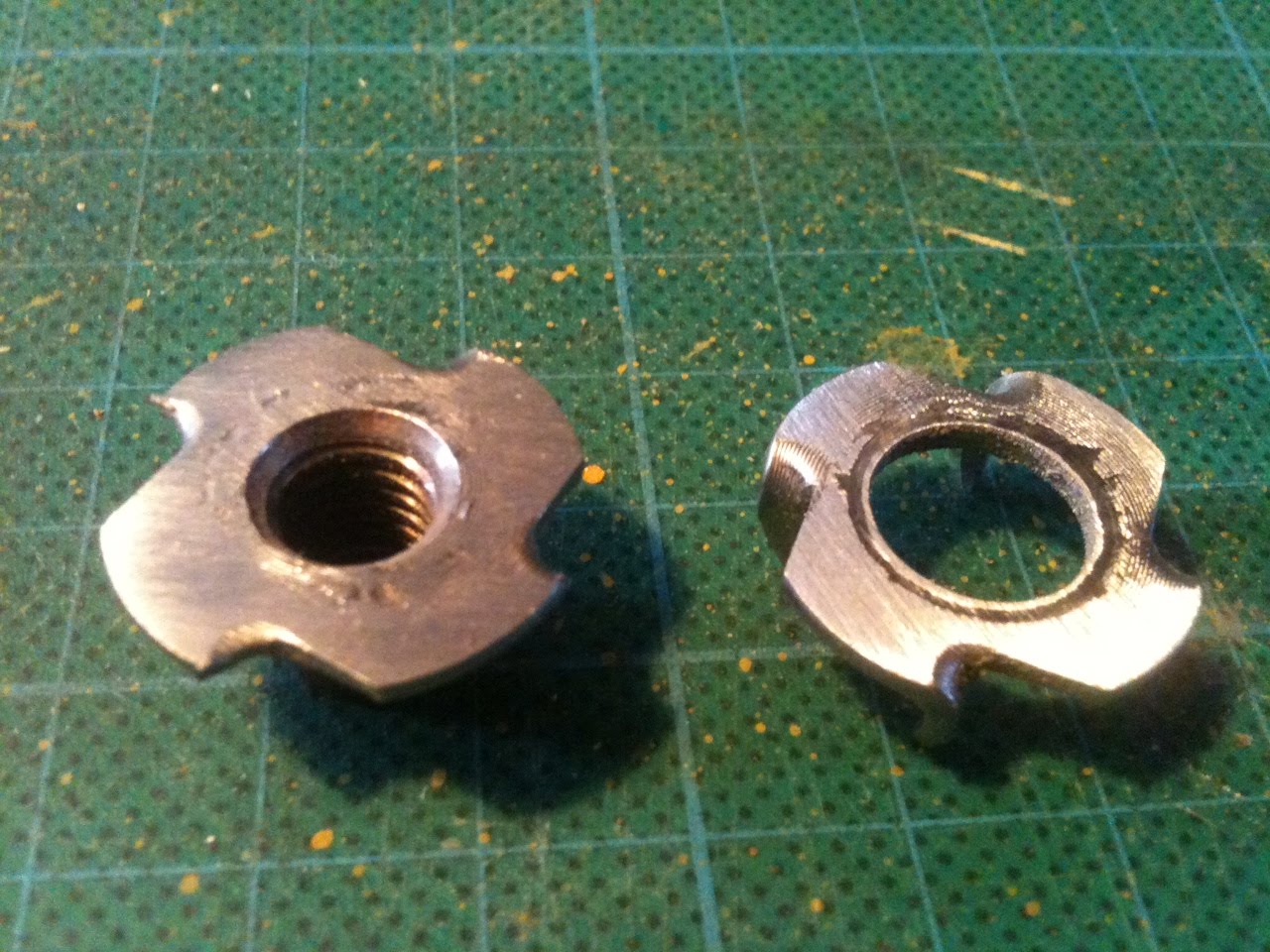
So, as pictured above, I drilled out the threads on one T-nut, and glued it back to back - using 5-min epoxy - with one that had all the tangs broken off it. I had high hopes for this solution to the problem of breaking tangs. Next issue: my Hitachi corded drill has the wrong sort of chuck, so I had to buy an adaptor, so as to have a normal old-fashioned one, with which to grasp the threaded rod in the head-stock.
Having set it all up, with a load of clamps, for a test, I found that there's a lot of play in the whole assemblage, as all the parts have slightly different diameters. This, coupled with the off-square-ness of everything, means the whole thing judders and wobbles a ridiculous amount.
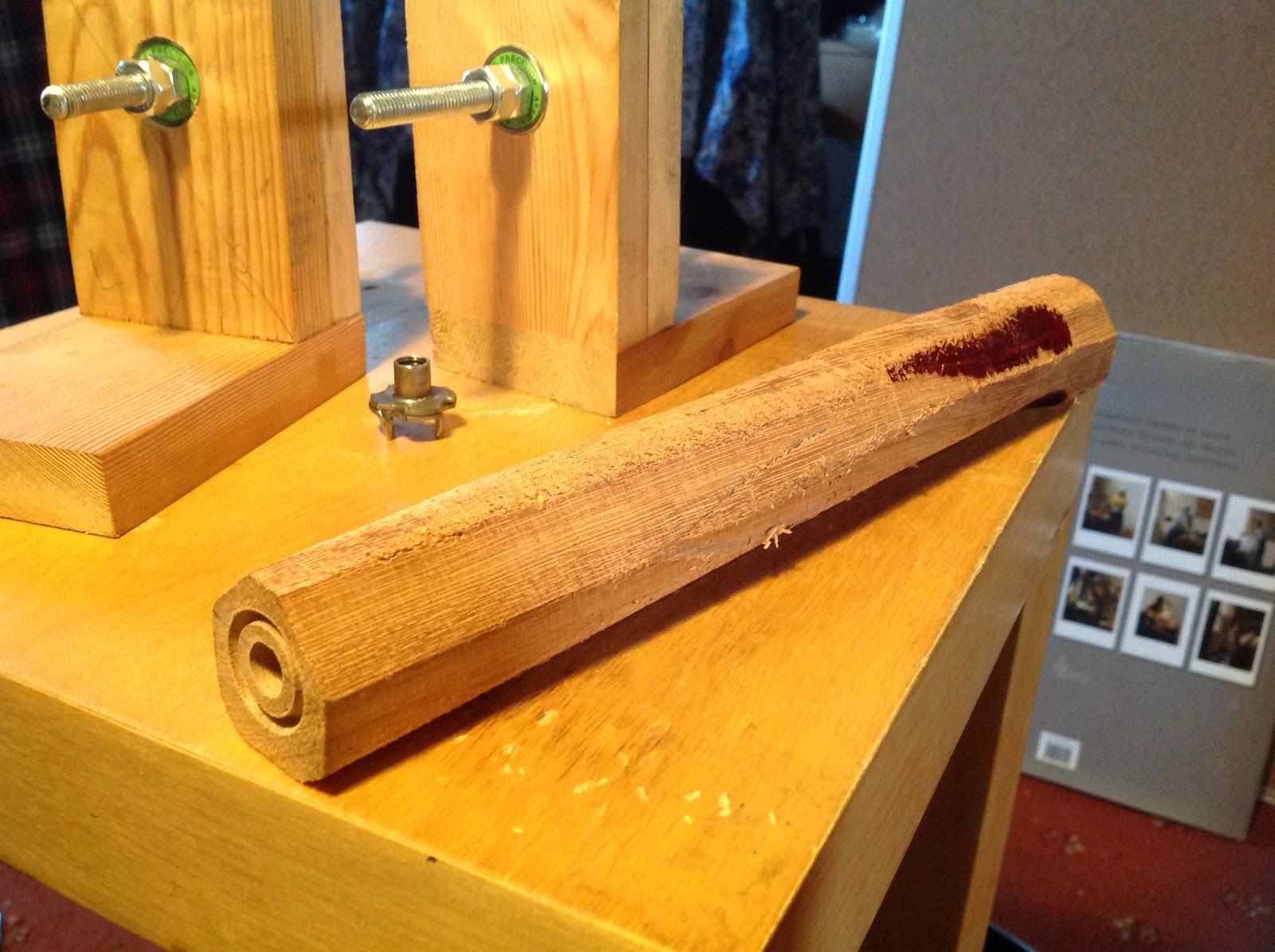
My butchery! Partly done with chisels, partly with a rasp...
Perhaps the whole disaster I had today was also due to picking the wrong wood? I tried turning some rosewood. Very dense, hard stuff. I tried several chisels (I have no proper wood-turning tools), and all they did was knock the chuck loose, undo the epoxy glue (so my cherished pronged T-nut assemblage fell apart). Drilling the holes for the two lathe rods was easy enough. So I sharpened the chisels. No improvement.
I've made a second pronged nut, but that to was quickly rent asunder, so I'm regluing them both. And I'll try again with a softer wood tomorrow. I'll also get all my chisels razor sharp. But I found the whole thing, which has been two days work - Izzy Swan's video suggests it's a simple 10-minute build! - quite depressing.
I wish I just had the money to buy some decent tools!