jimi43
Established Member
Hijack away Toby...that's partly what this thread is for...learning and development.
And on that very subject..we moved today to the making of the cap iron.
I say "we" because....yet again...I had help!
As always...ALFIE has to be involved at each stage!!
As I briefly mentioned before...I wanted something a bit more than just a bit of bent metal...so I have been doing some research.
I love the shape of the Clifton two part cap iron at the very front where it mates with the face of the iron.
And also there is a belief that when the cap iron and iron are mated tightly the spring in the cap iron should close down flat onto the surface of the iron to create a very thick and undeformed integrated unit.
To this end we cut a piece of 3mm x 70mm O1 Saxon Ground Flat Stock....
(apologies for the poor focus on this one...phone was used again!)
Having cut the rough shaped blank...this was draw filed to clean up saw marks from the hacksaw...
An 8mm tapping hole was then drilled in the correct place...and this is always just below the place the lever cap bolt will rest when the iron is new...as the iron is sharpened and is shortened...the whole slot moves down and the cap iron stays where it is so this is critical.
That's right isn't it ALFIE????
I tarted up an old original bolt for the cap iron in the standard way and used a 3/8" 16 BSW tap to tap the hole drilled with an 8mm clearance hole.
....and it fitted perfectly...
The cap iron was then given a slight bend at exactly the same place as the old Marples one.
On the inner face of the cap iron a recess was milled out...and this is where the design differs from the original...
The front lip has a bevel on it....this is shown in the "untightened" position...and as the nut is tightened...the rear main body of the cap iron moves downwards and mates with the iron...leaving the recess and the bevel pinching down very tightly at the leading edge contact point.
There will now follow questions and suggestions (if I know our forum members!)....and of course I welcome this. The definitive design however, won't be fully proven until I get the iron back from hardening and I can do some actual testing. In the meantime...I will be reinforcing the protruding cap iron screw with the brass boss common with planes of old.
I was going to bevel the top of the cap iron but I quite like the plain look...what do you think guys and gals?
All for today...tomorrow I work...but I may be able to rough out the lever cap bolts...or mark the next iron...we'll see.
Cheers
Jimi (and ALFIE!)
And on that very subject..we moved today to the making of the cap iron.
I say "we" because....yet again...I had help!
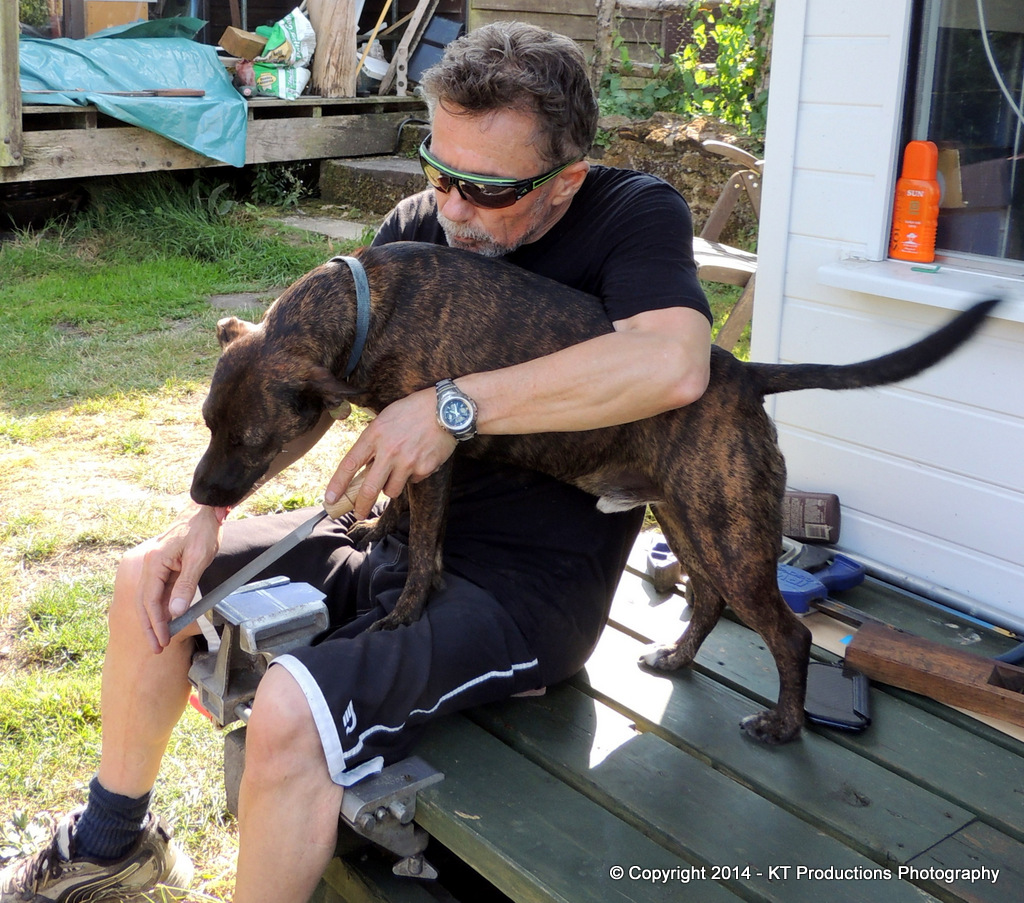
As always...ALFIE has to be involved at each stage!!
As I briefly mentioned before...I wanted something a bit more than just a bit of bent metal...so I have been doing some research.
I love the shape of the Clifton two part cap iron at the very front where it mates with the face of the iron.
And also there is a belief that when the cap iron and iron are mated tightly the spring in the cap iron should close down flat onto the surface of the iron to create a very thick and undeformed integrated unit.
To this end we cut a piece of 3mm x 70mm O1 Saxon Ground Flat Stock....
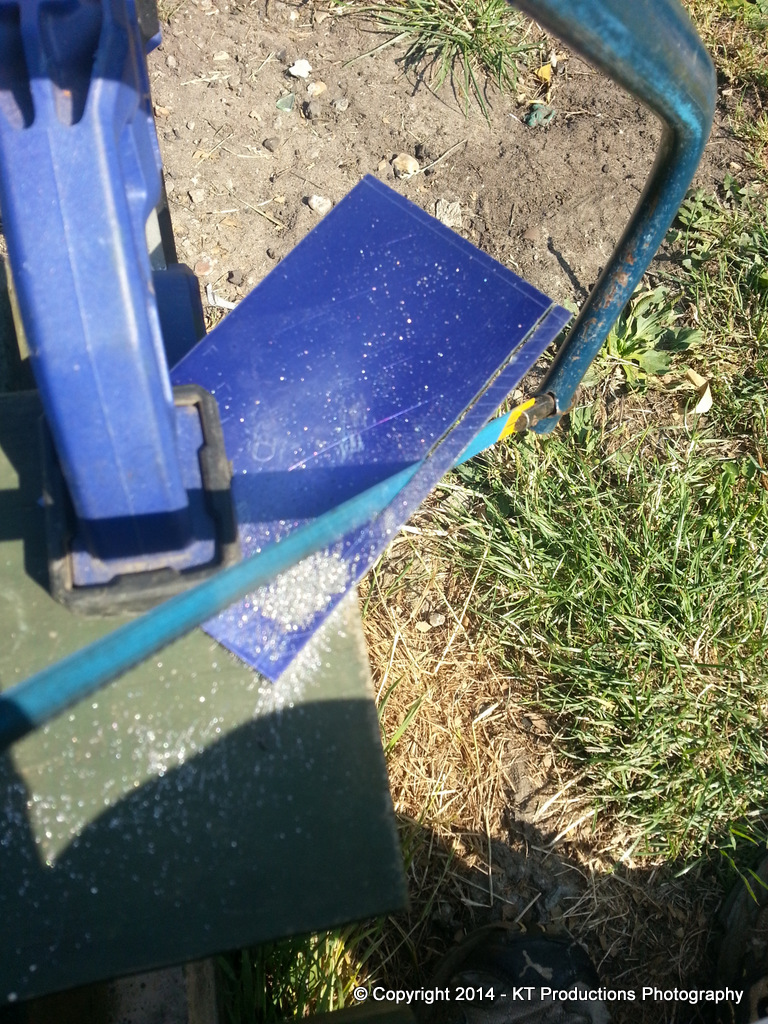
(apologies for the poor focus on this one...phone was used again!)
Having cut the rough shaped blank...this was draw filed to clean up saw marks from the hacksaw...
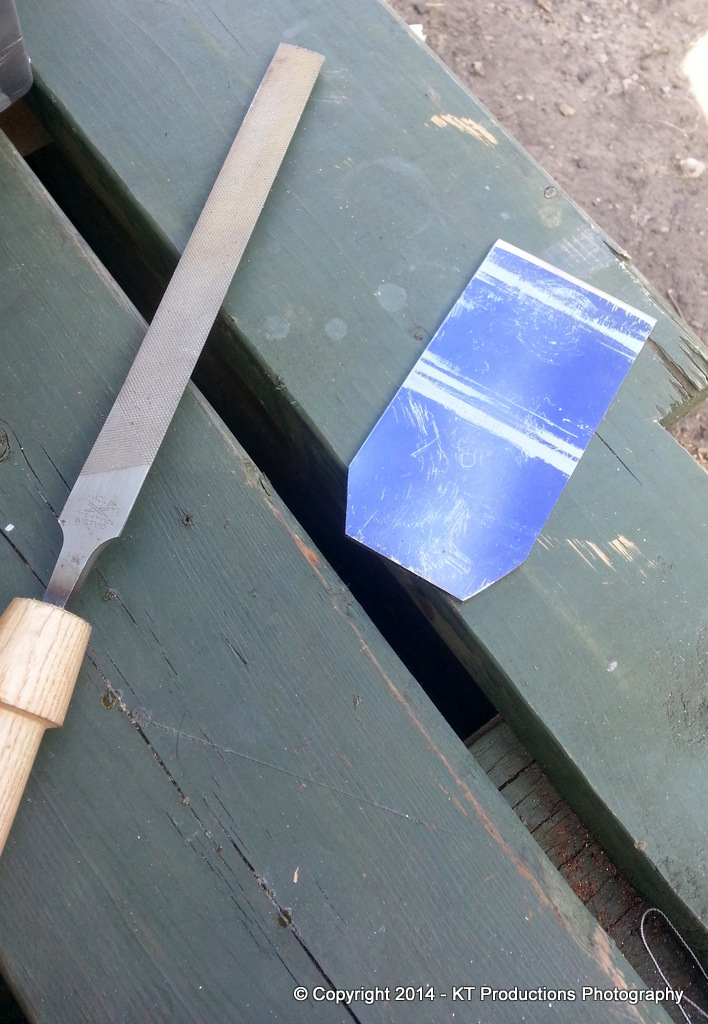
An 8mm tapping hole was then drilled in the correct place...and this is always just below the place the lever cap bolt will rest when the iron is new...as the iron is sharpened and is shortened...the whole slot moves down and the cap iron stays where it is so this is critical.
That's right isn't it ALFIE????
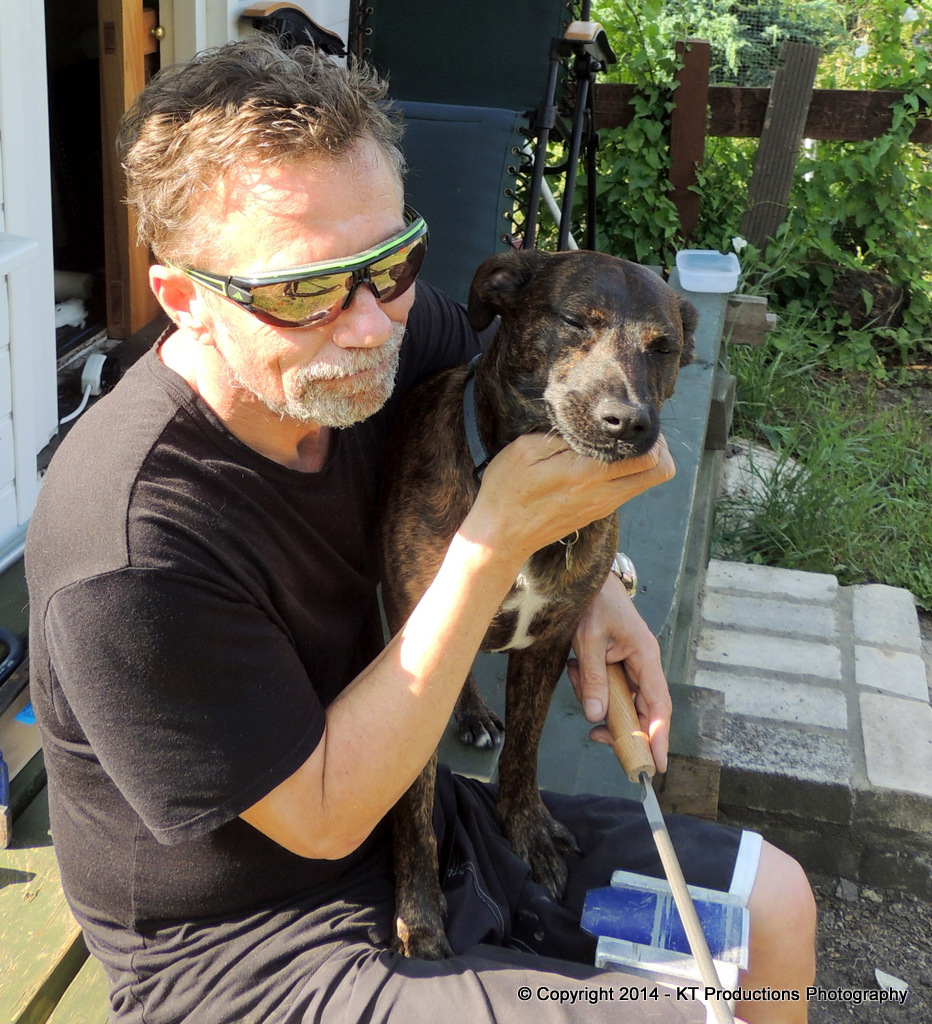
I tarted up an old original bolt for the cap iron in the standard way and used a 3/8" 16 BSW tap to tap the hole drilled with an 8mm clearance hole.
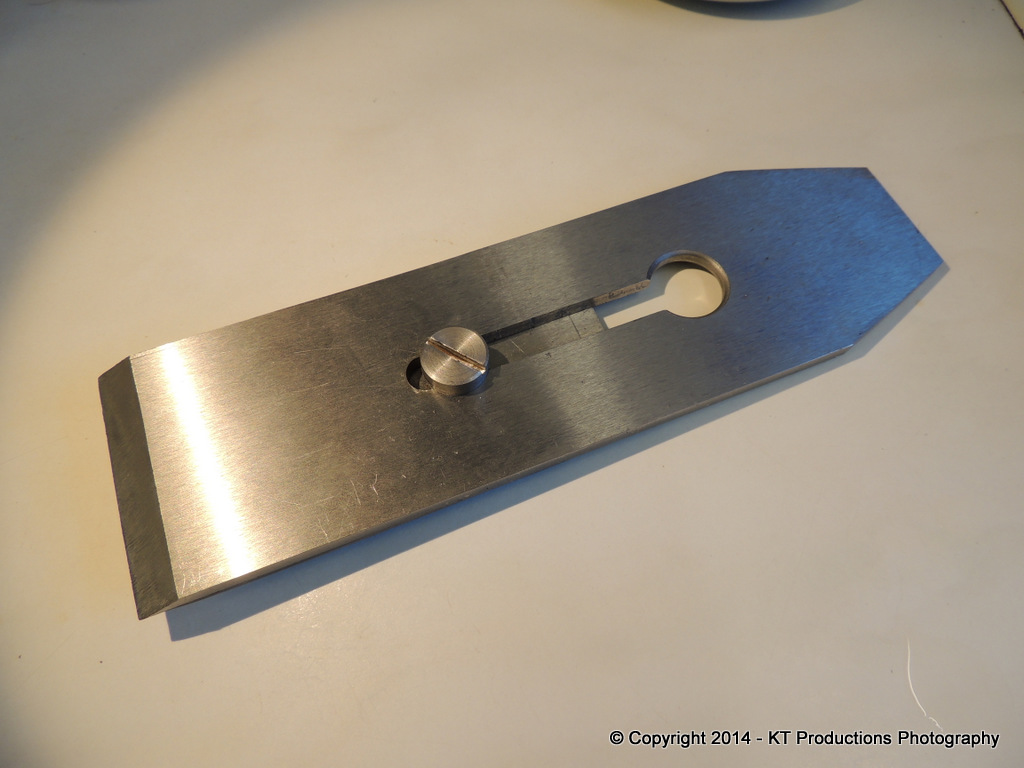
....and it fitted perfectly...
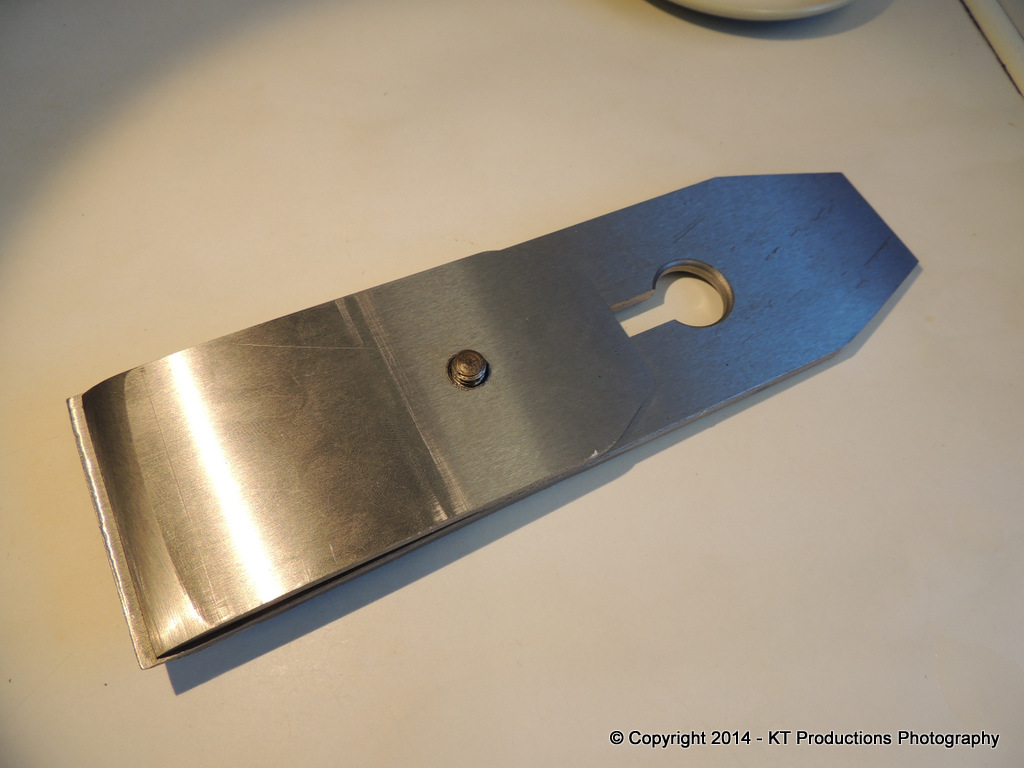
The cap iron was then given a slight bend at exactly the same place as the old Marples one.
On the inner face of the cap iron a recess was milled out...and this is where the design differs from the original...
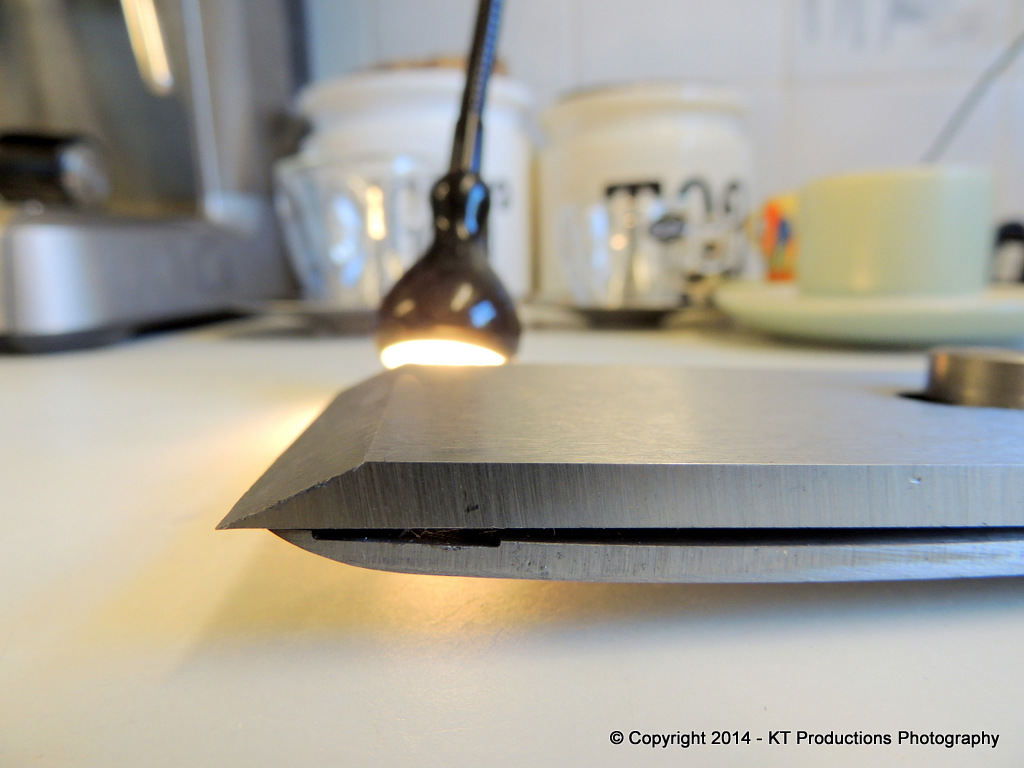
The front lip has a bevel on it....this is shown in the "untightened" position...and as the nut is tightened...the rear main body of the cap iron moves downwards and mates with the iron...leaving the recess and the bevel pinching down very tightly at the leading edge contact point.
There will now follow questions and suggestions (if I know our forum members!)....and of course I welcome this. The definitive design however, won't be fully proven until I get the iron back from hardening and I can do some actual testing. In the meantime...I will be reinforcing the protruding cap iron screw with the brass boss common with planes of old.
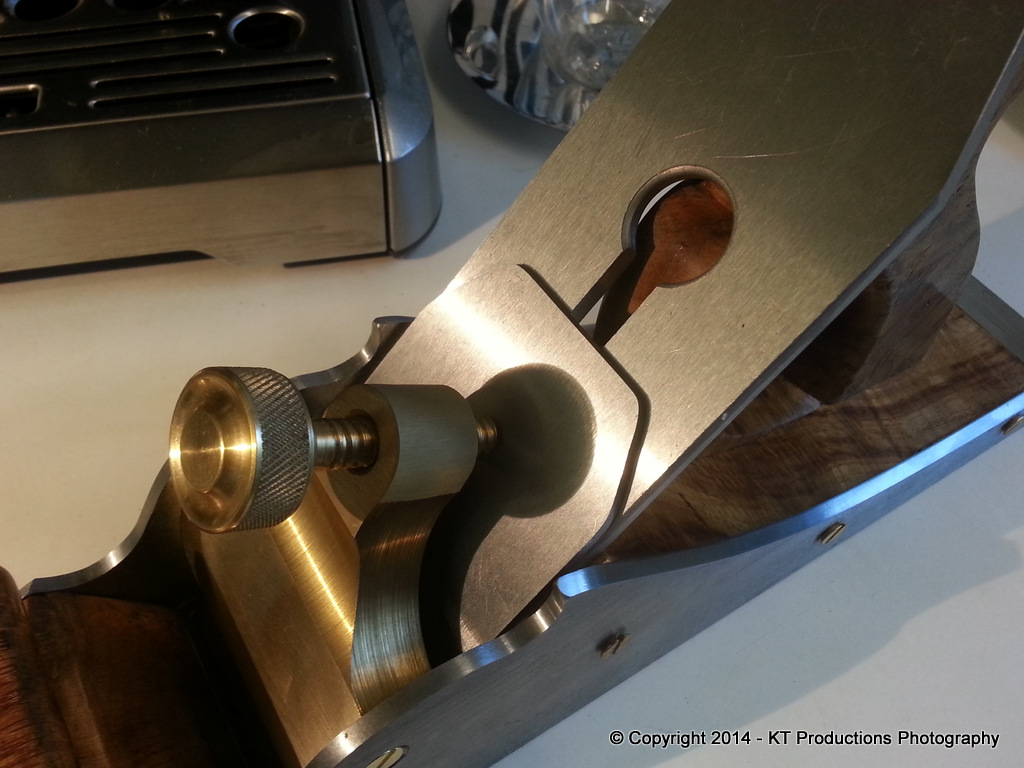
I was going to bevel the top of the cap iron but I quite like the plain look...what do you think guys and gals?

All for today...tomorrow I work...but I may be able to rough out the lever cap bolts...or mark the next iron...we'll see.
Cheers
Jimi (and ALFIE!)