ratkinsonuk
Established Member
Well, since my last post (https://www.ukworkshop.co.uk/forums/view ... hp?t=10203), lots has happened on my workshop, so I thought it's about time I shared the high's and lows so far.
Where I got to last time
Lots of wood arrived
And more
And some more!
First job was to get the floor built
Then I started on the walls
Quite a span to handle
The weather turned
But we had some sun
Time for the tarp to come off for the roof
Starting to come together
Ridge Beam up and rafters starting to go on
Framing finally complete
Time to add a skin, oh, and a roof
Feels cosy already
My workbench seems a bit lonely
Not bad going on the wasteage
And then the BIG problem
At this point, it was down tools for about 5 months. One of my neighbours wasn't too happy with their new view, so the council got involved. Although I'd gone to some length to check the regs (cheers for the help Dave), they got me on one of them, so I had to go through the whole nine yards.
Although they 'normally wouldn't have passed the plans', as I'd already got the structure up, they were willing to allow me to continue, as long as I adhere to a few requisites regarding materials, colours, etc.
Anyway, off we go again - now early 2006, btw
So, with frame up and vapor barrier on, cladding was next.
And from the road
Now it's water tight, time to add some temporary electrics
And lighting
Ran out of cladding
But got some doors instead
Went with felt shingles for the roof
Facias and soffets ready to go on
Did I mention the double glazing - £100 for this lot
And £42 for this leaded one - Berty Bargain!
Oh, and got that last bit of cladding up
Time to put in some drainage shingle
And make it look a bit better
Turning to the inside, first a shiny new Consumer Unit
Starting the 1st fit electrics
Well, that brings everything up to date.
Still quite a bit to do on the outside, including 2nd coat of Cuprinol on entire skin, facias and soffets still to be made, then guttering.
The good news is that I should be ready for heating to be installed in the next few months, which means I can finally transfer my cast iron power tools into the new shop.
There's a few more pics at http://s51.photobucket.com/albums/f355/ ... /workshop/ if you'd like to see more.
Where I got to last time
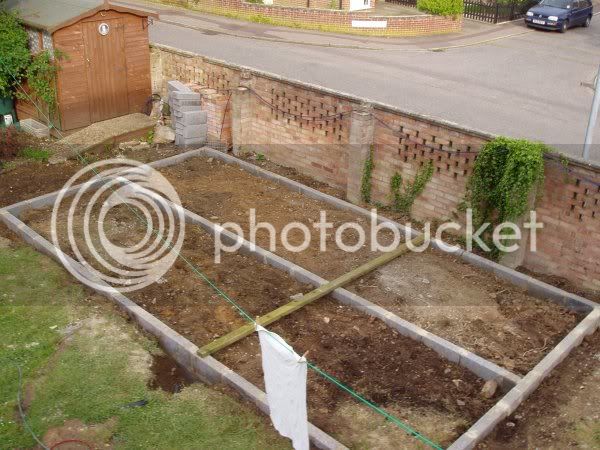
Lots of wood arrived
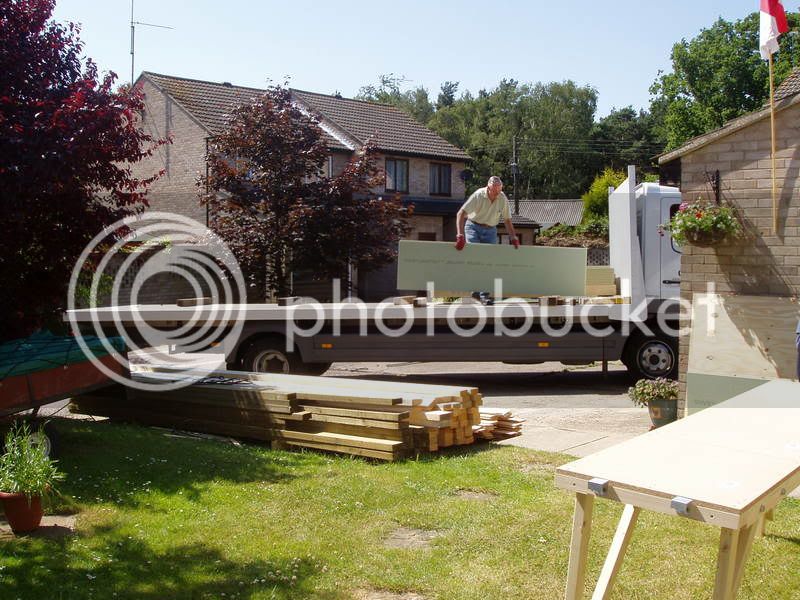
And more
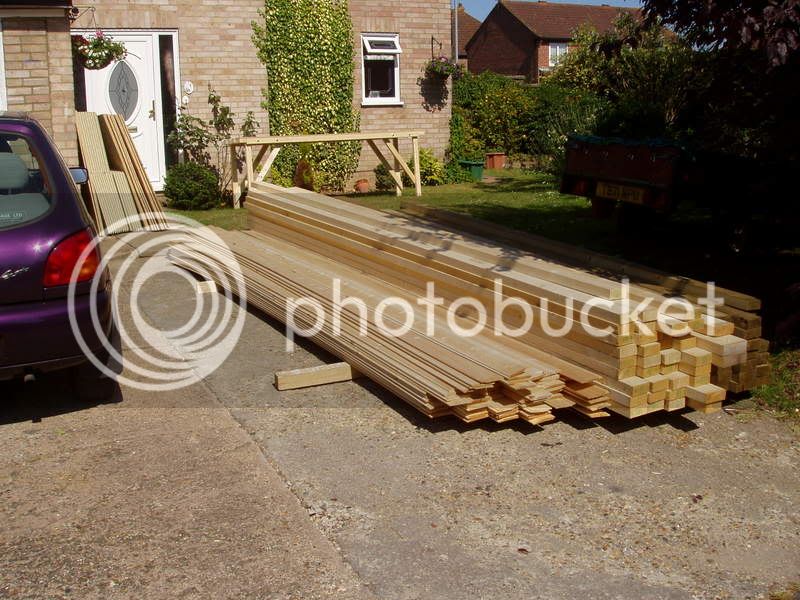
And some more!
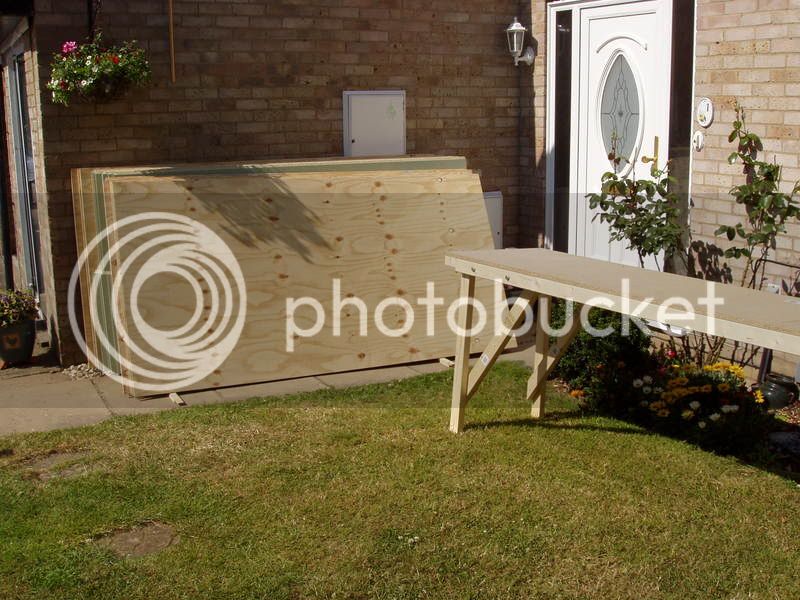
First job was to get the floor built
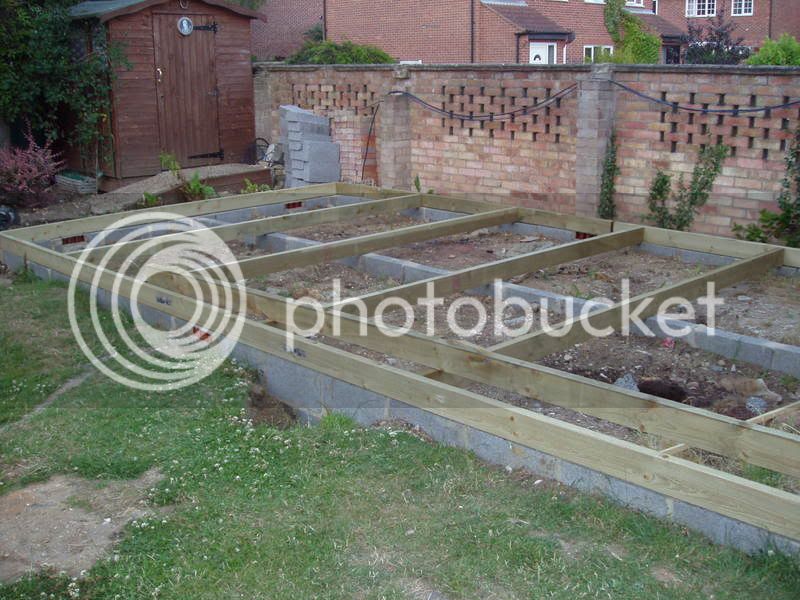
Then I started on the walls
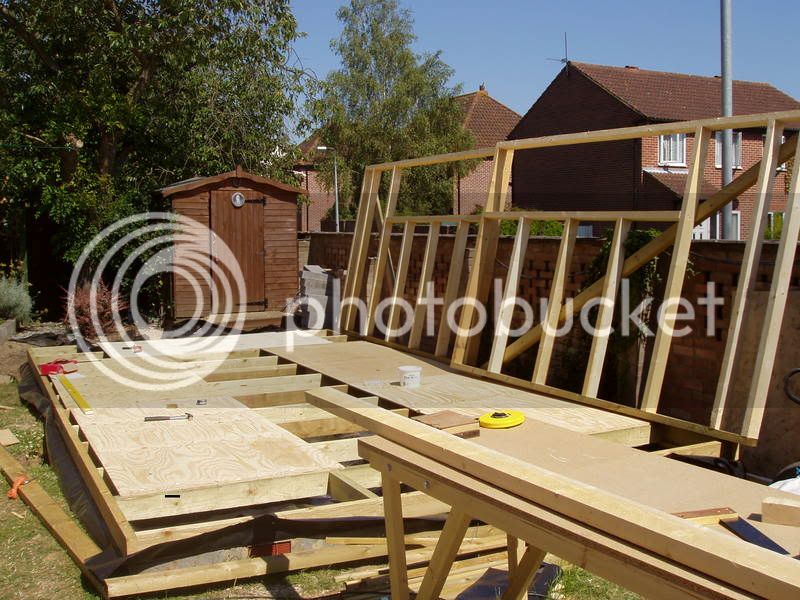
Quite a span to handle
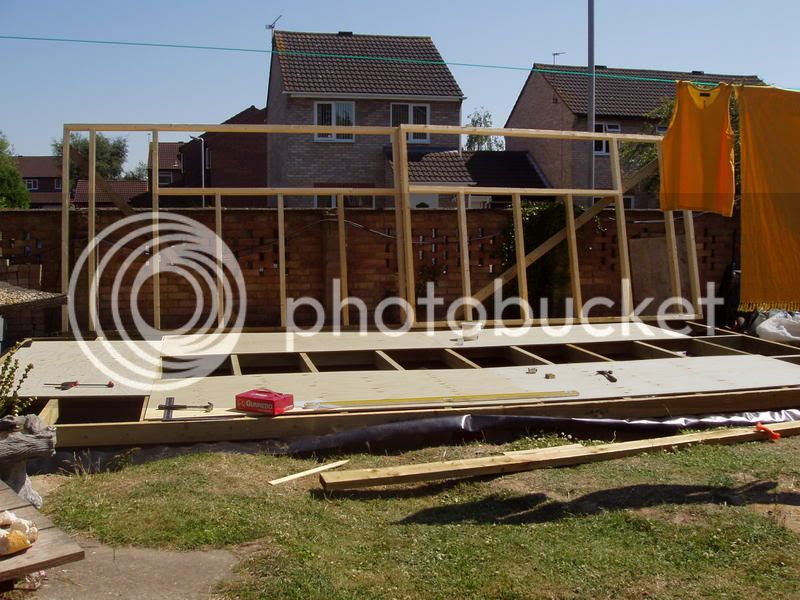
The weather turned
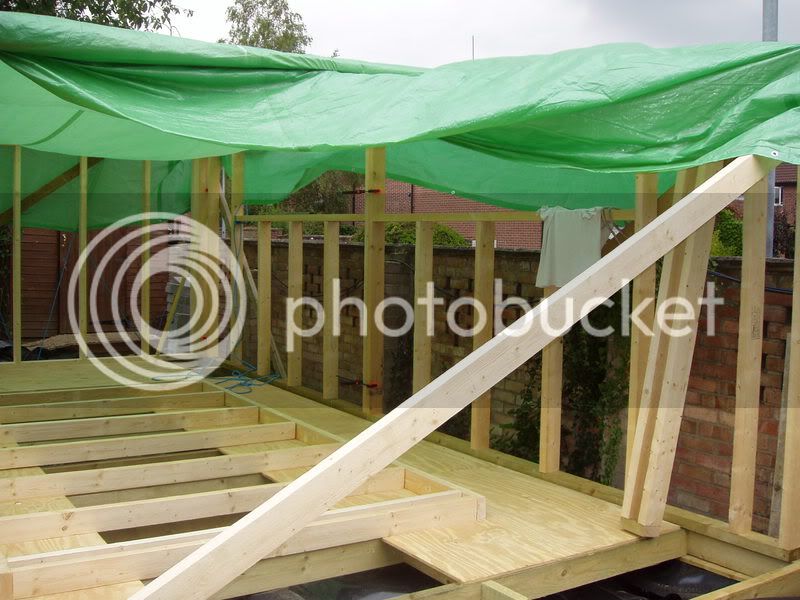
But we had some sun
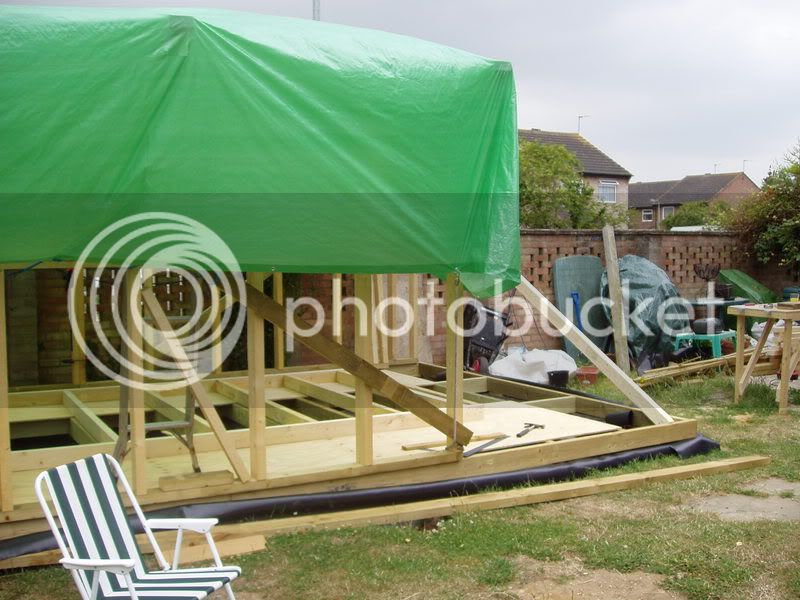
Time for the tarp to come off for the roof
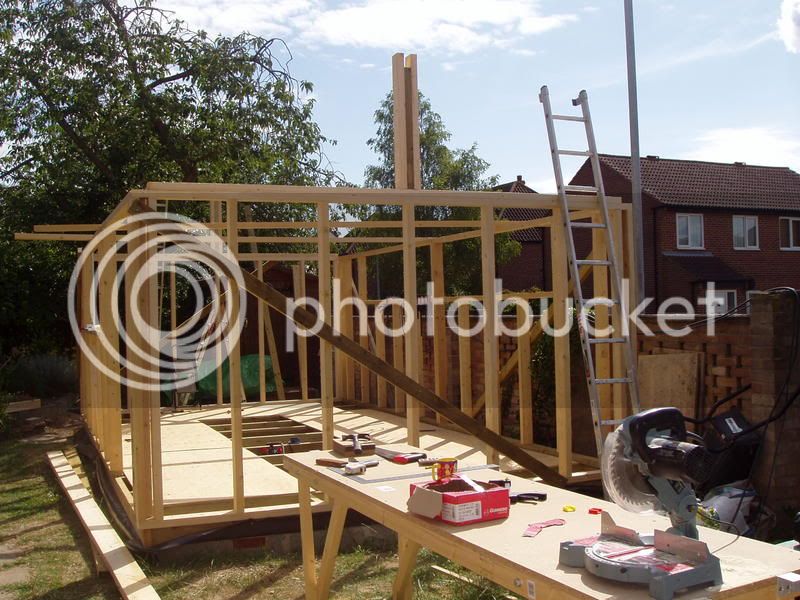
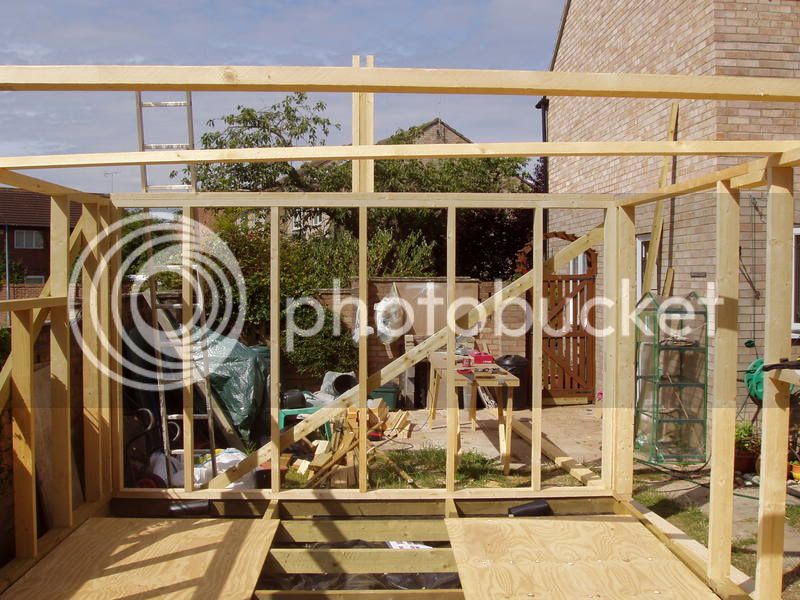
Starting to come together
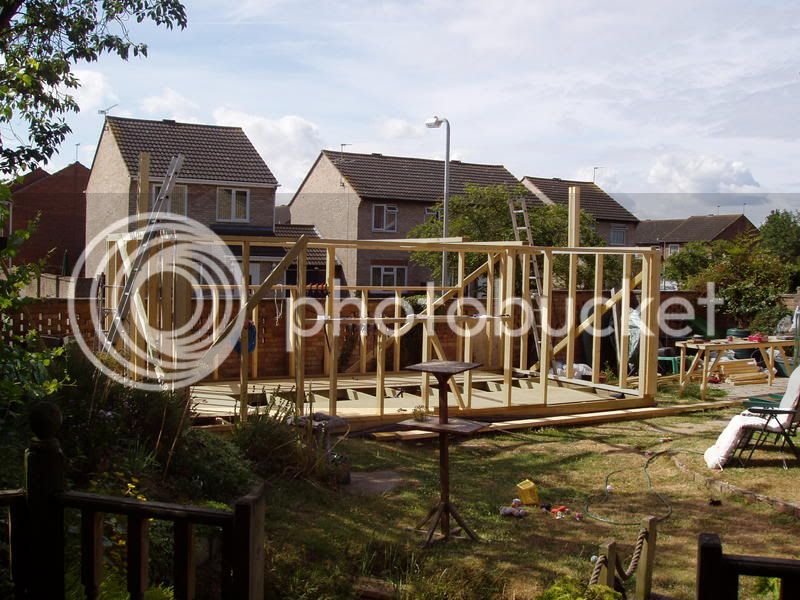
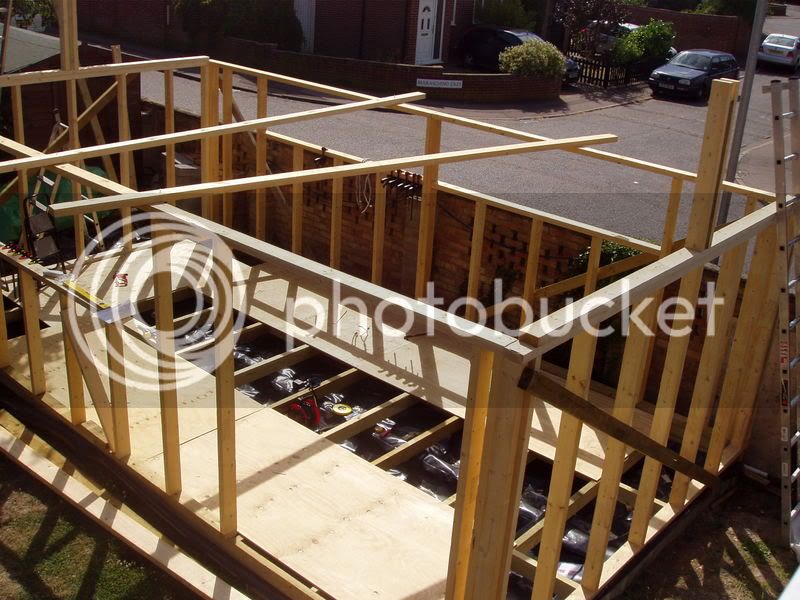
Ridge Beam up and rafters starting to go on
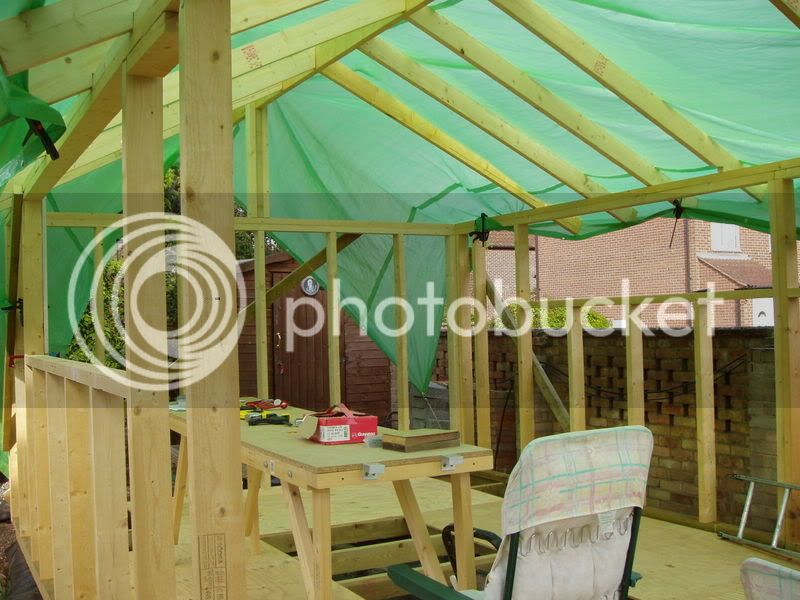
Framing finally complete
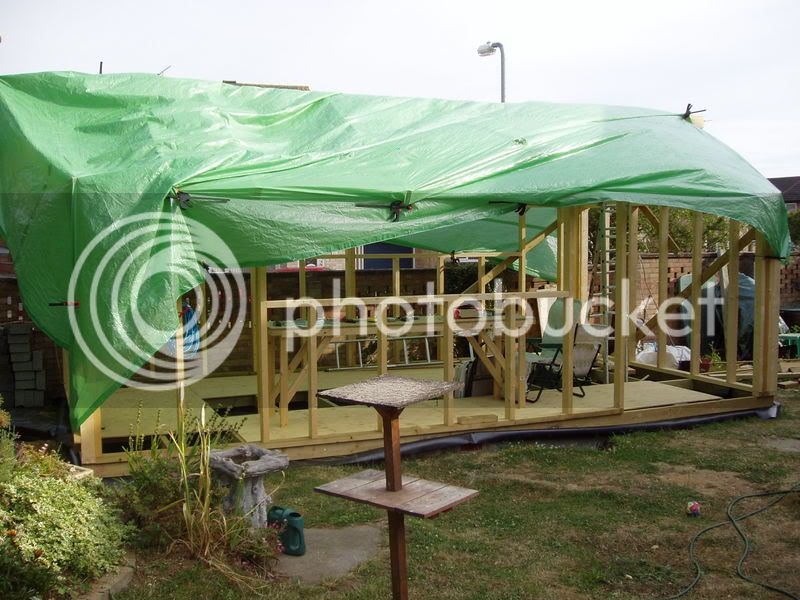
Time to add a skin, oh, and a roof
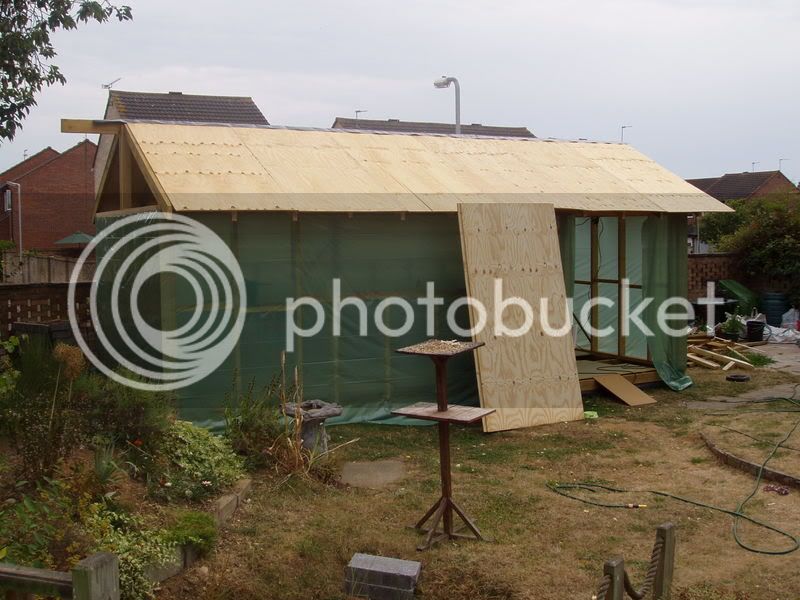
Feels cosy already
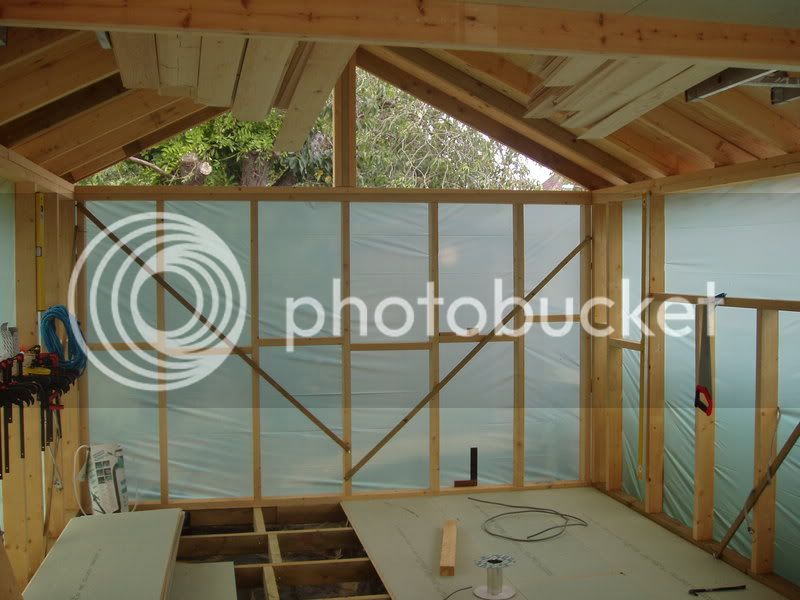
My workbench seems a bit lonely
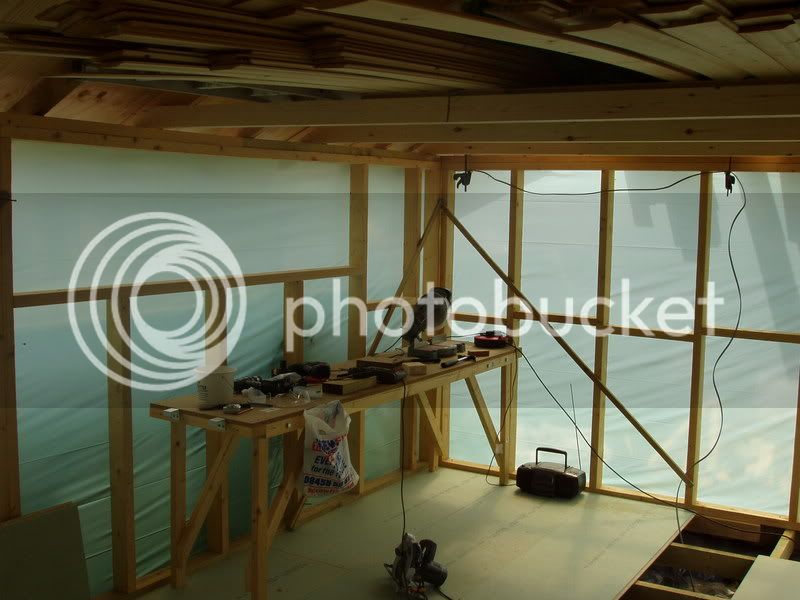
Not bad going on the wasteage
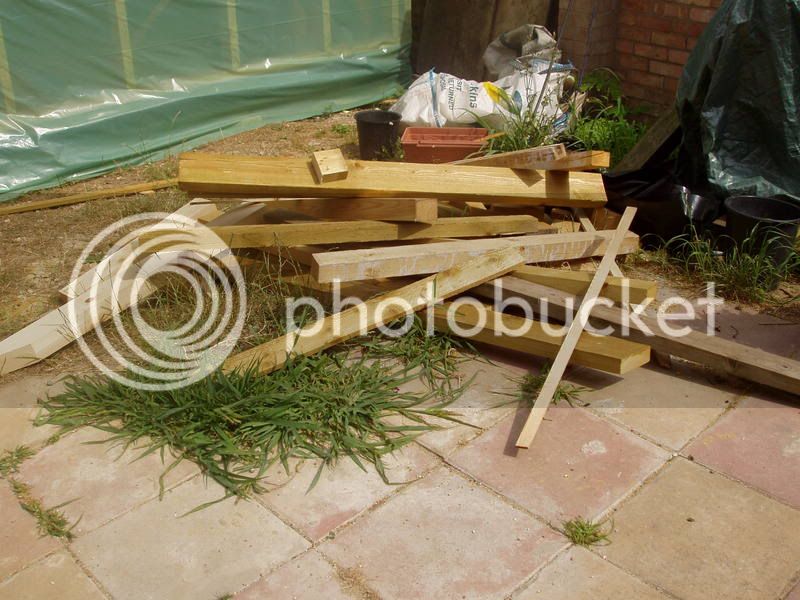
And then the BIG problem
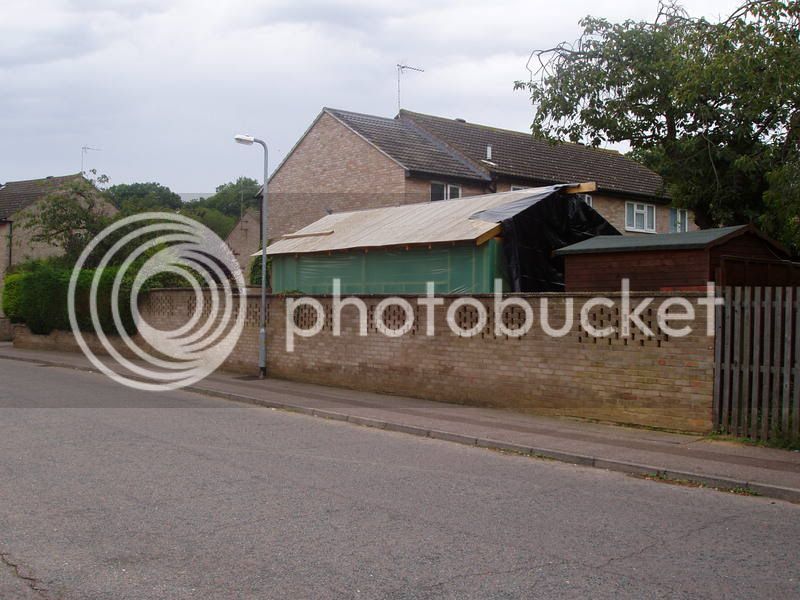
At this point, it was down tools for about 5 months. One of my neighbours wasn't too happy with their new view, so the council got involved. Although I'd gone to some length to check the regs (cheers for the help Dave), they got me on one of them, so I had to go through the whole nine yards.
Although they 'normally wouldn't have passed the plans', as I'd already got the structure up, they were willing to allow me to continue, as long as I adhere to a few requisites regarding materials, colours, etc.
Anyway, off we go again - now early 2006, btw
So, with frame up and vapor barrier on, cladding was next.
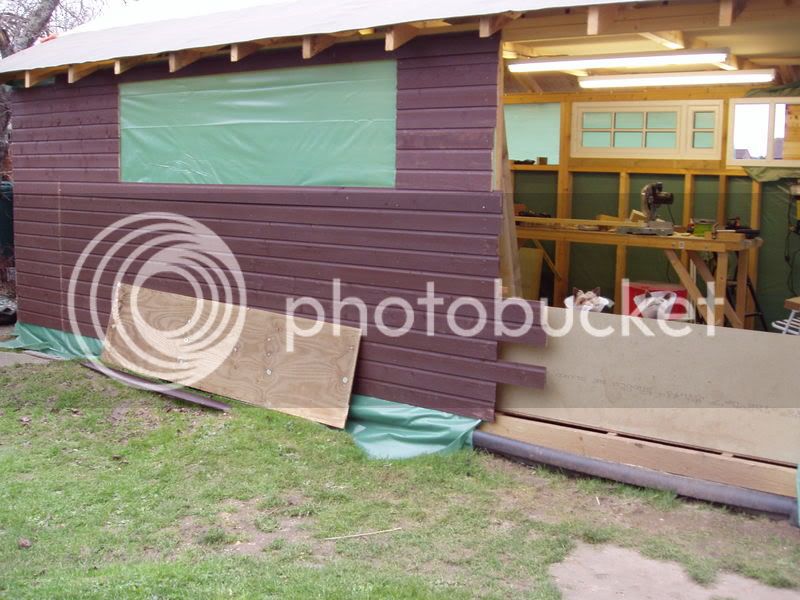
And from the road
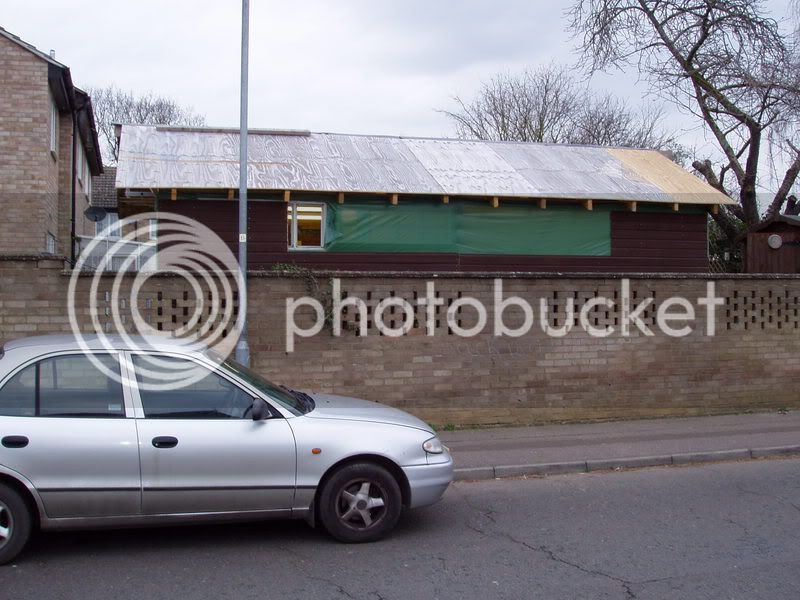
Now it's water tight, time to add some temporary electrics
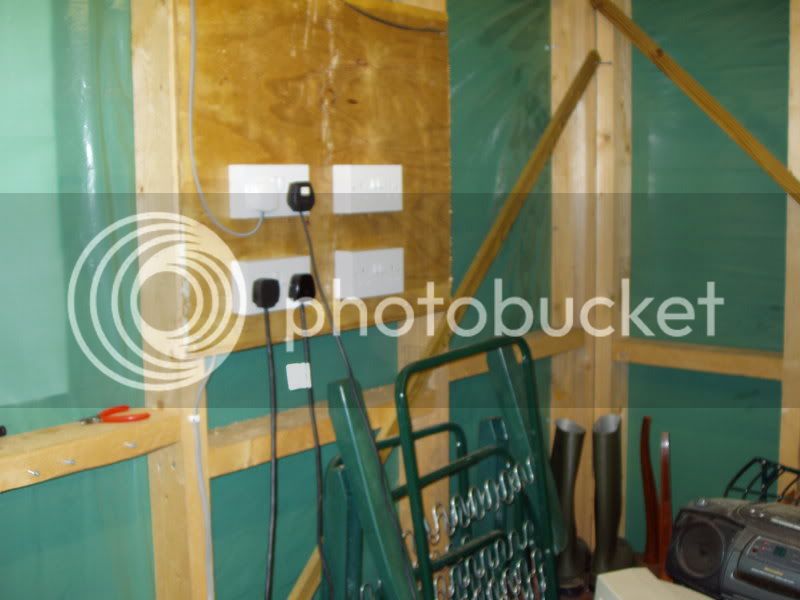
And lighting
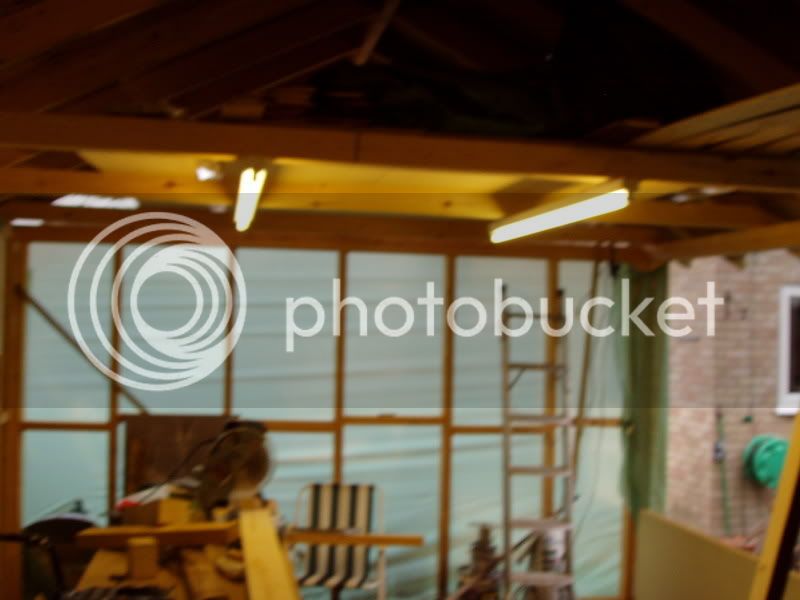
Ran out of cladding
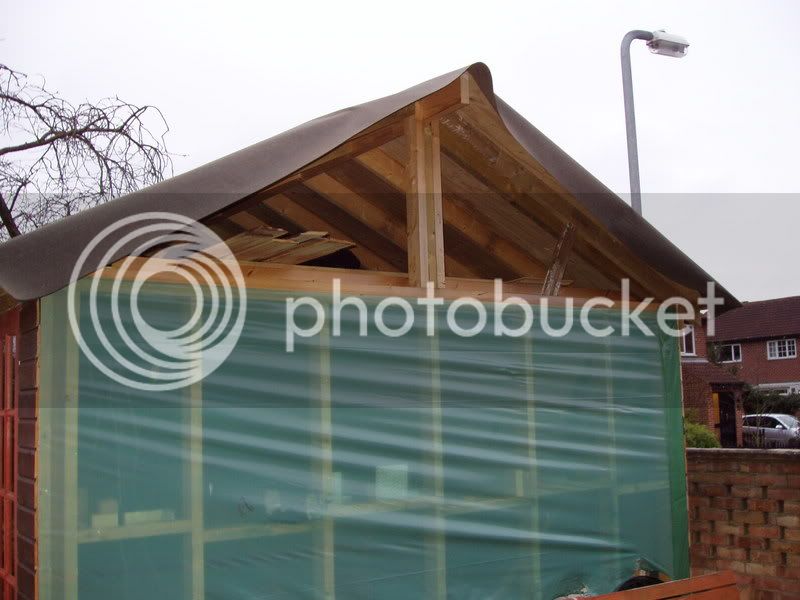
But got some doors instead
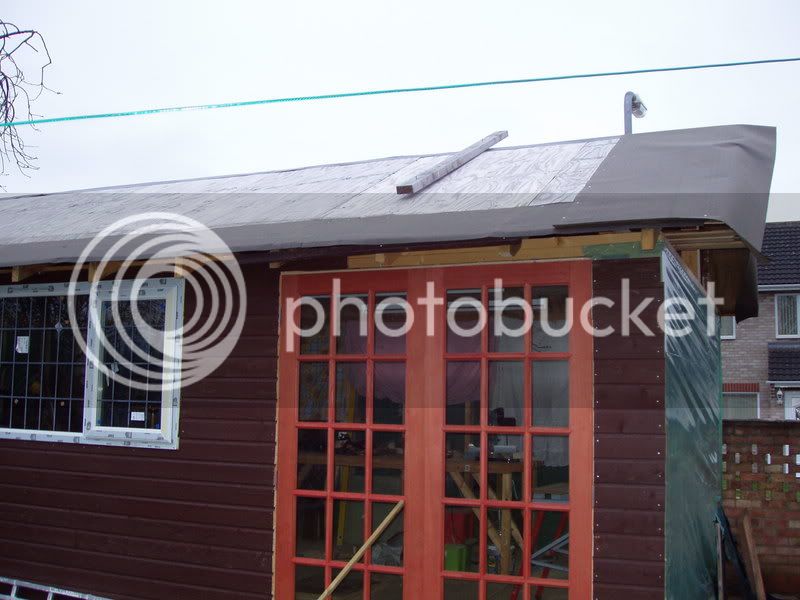
Went with felt shingles for the roof

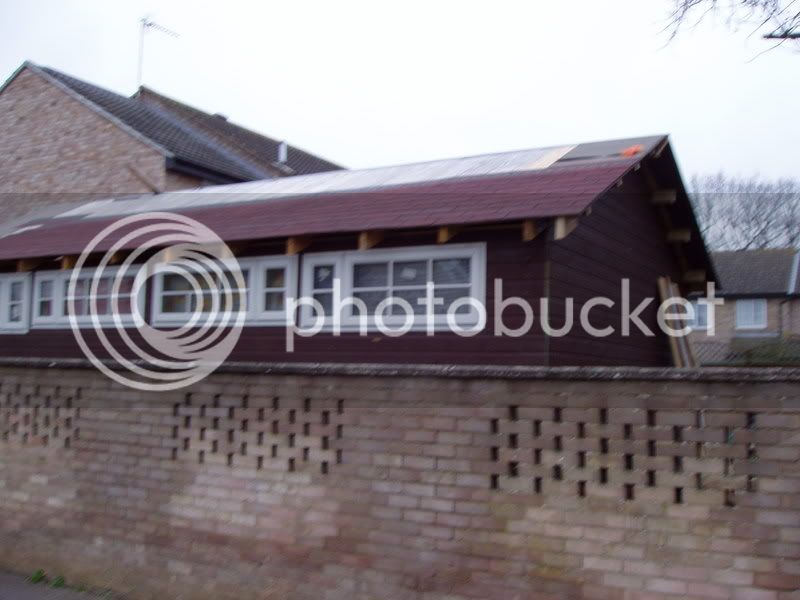
Facias and soffets ready to go on
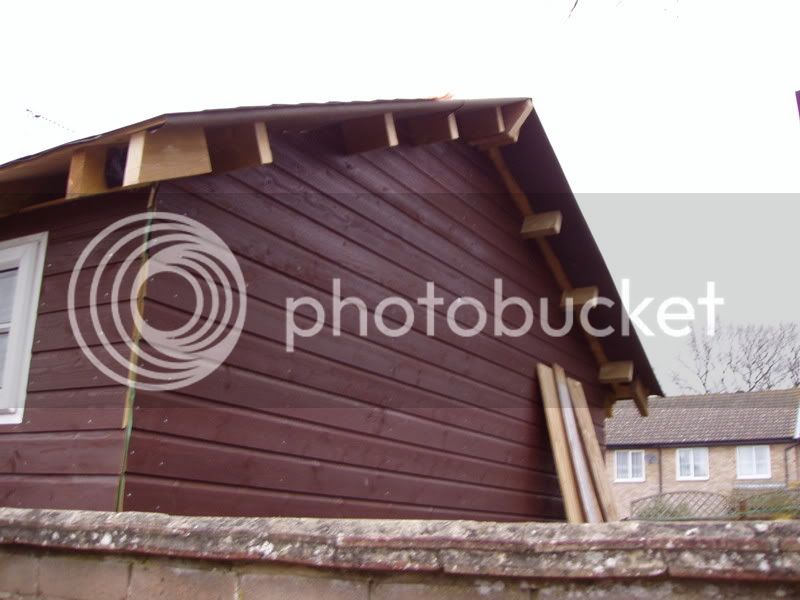
Did I mention the double glazing - £100 for this lot
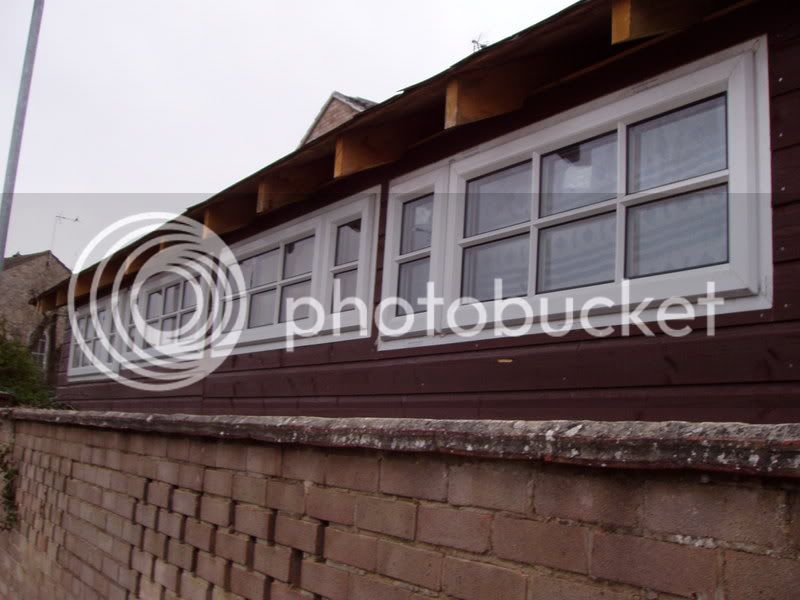
And £42 for this leaded one - Berty Bargain!
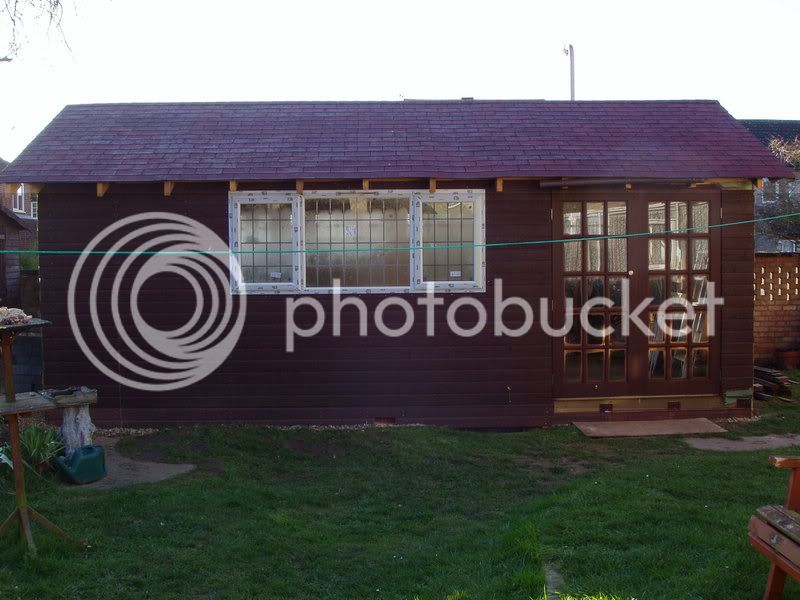
Oh, and got that last bit of cladding up
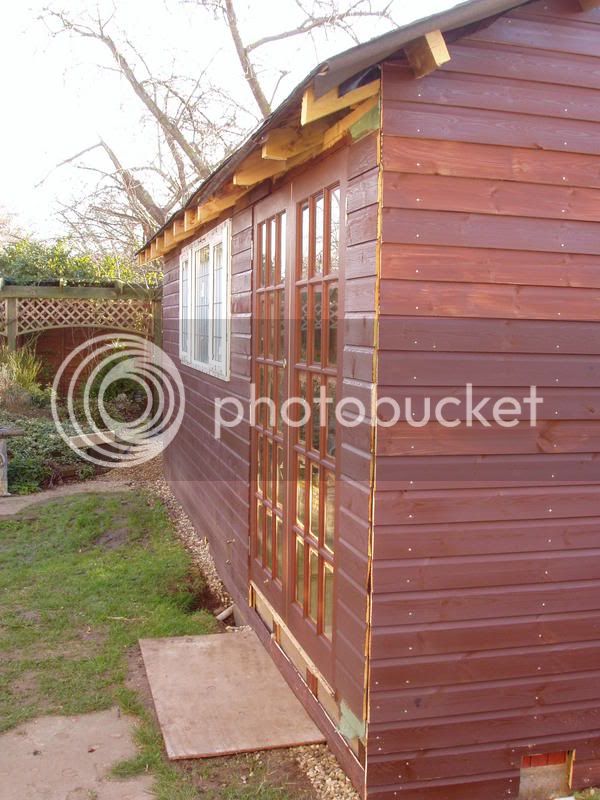
Time to put in some drainage shingle

And make it look a bit better
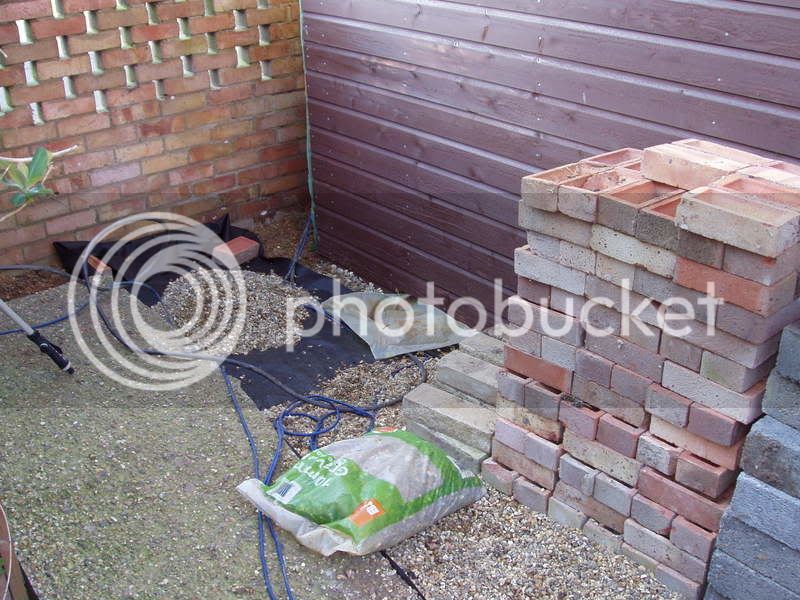
Turning to the inside, first a shiny new Consumer Unit
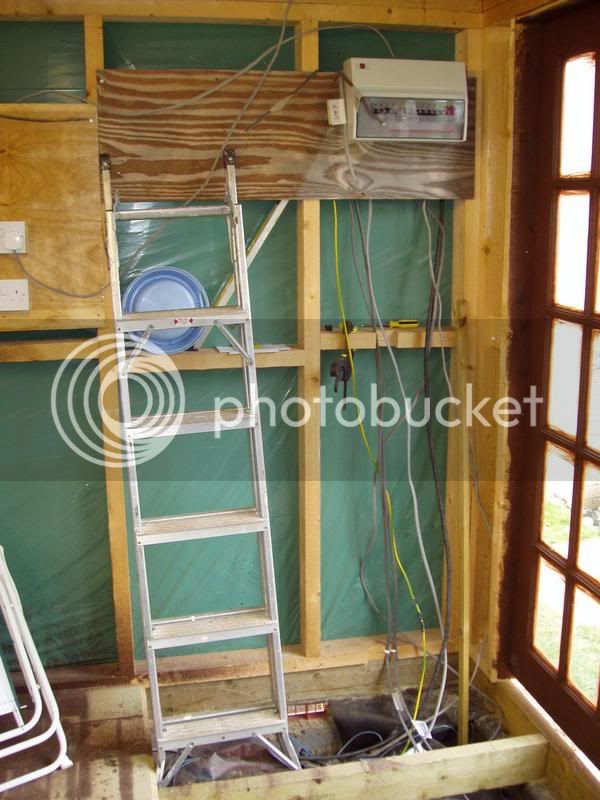
Starting the 1st fit electrics
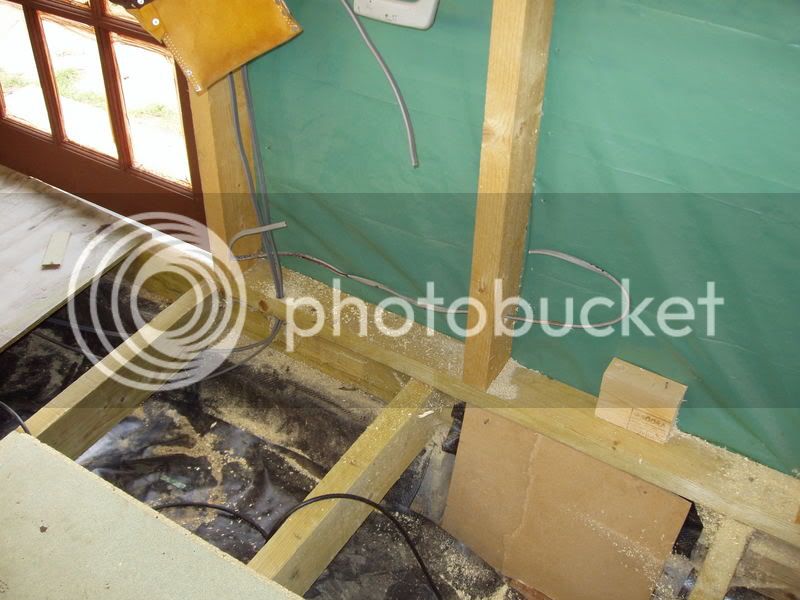
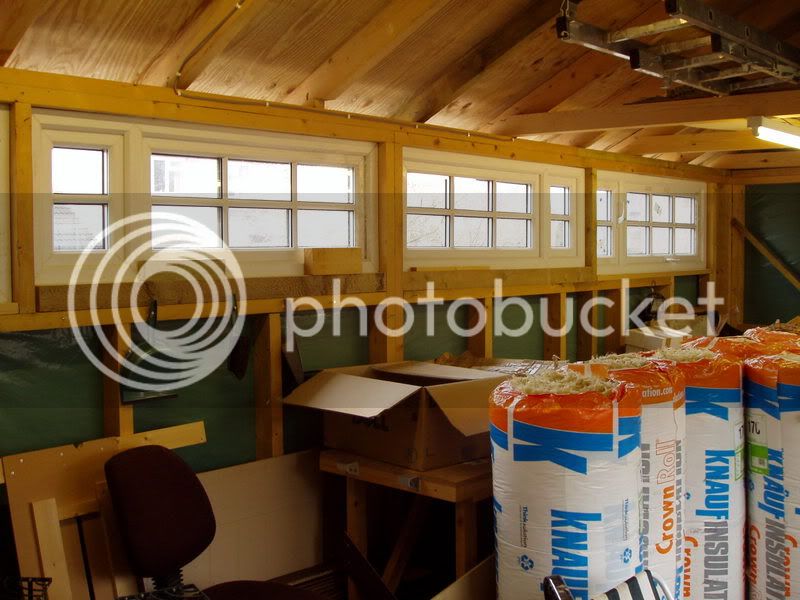
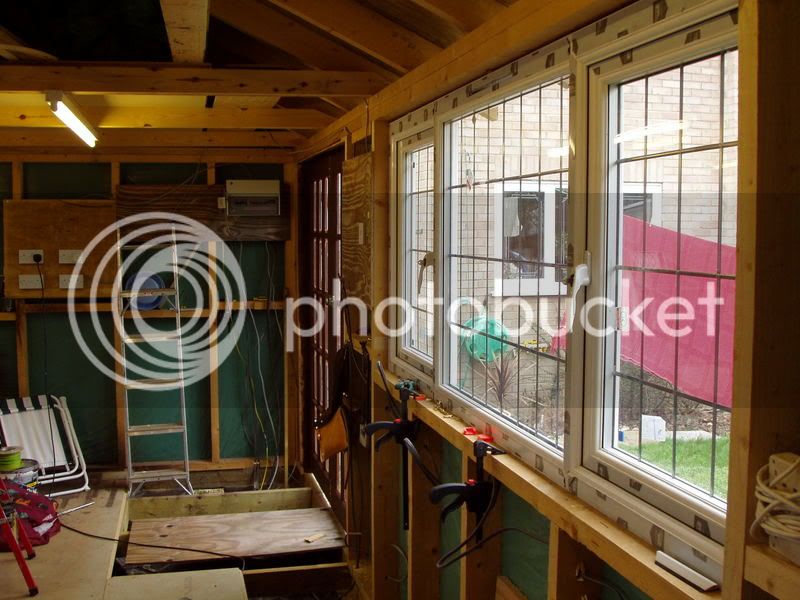
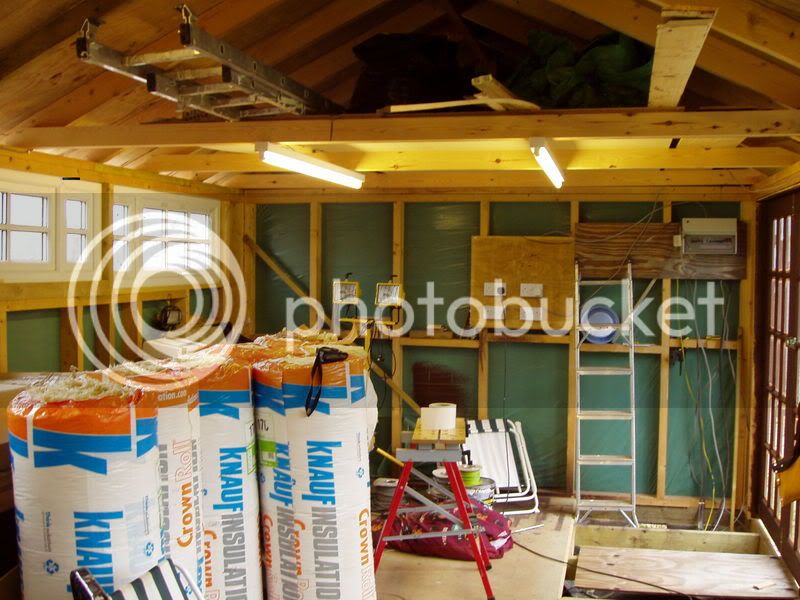
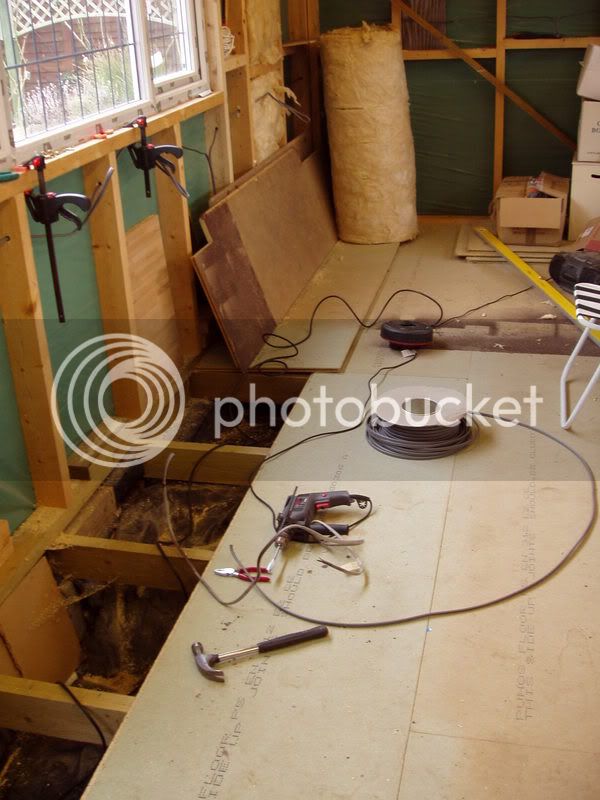
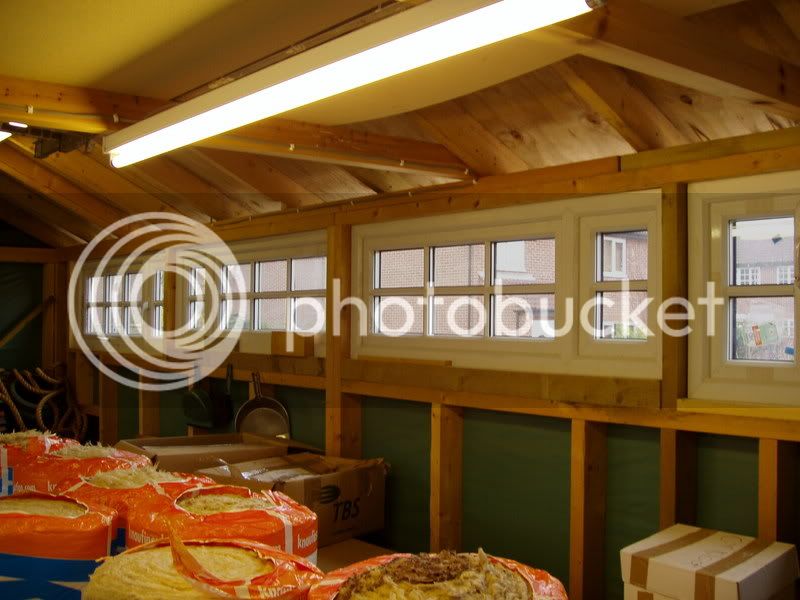
Well, that brings everything up to date.
Still quite a bit to do on the outside, including 2nd coat of Cuprinol on entire skin, facias and soffets still to be made, then guttering.
The good news is that I should be ready for heating to be installed in the next few months, which means I can finally transfer my cast iron power tools into the new shop.
There's a few more pics at http://s51.photobucket.com/albums/f355/ ... /workshop/ if you'd like to see more.