DangerousDave
Established Member
Have been at this a couple of months now, so I thought I'd post some WIP pics.
After a lot of faffing about with different designs (most of which looked like post office pigeon holes) I came up with this
Constructing components on SU as if I would build them in real life (i.e. from individual flat panels) makes it easy to explode each component and import each parts dimensions into the cutting list program;
Ordered up the MDF sheets. When they arrived, I stacked them flat on the bench. Then its only a matter of sticking a couple of 4x2's under the top sheet and start cutting;
And thats all the components cut. In total, 10 sheets of 18mm and 5 sheets of 6mm (for the backs)
Next thing to do is to mark out the templates for the top arched rails of the face frames. I call this 'The Curvulator'
Its a length of 6mm MDF in a big clamp. Simply tighten the clamp to tighten the radius. By using this I can mark out curves one-handed without faffing around with bending the MDF around nails etc...
The bulk is then removed at the band saw...
...and carefully sanded to the line
I then screwed the template to the rail (with the bulk removed at the bandsaw) and used a bearing guided straight cutting bit in the router table
Face frames assembled using Kreg pocket screws
And an ogee profile routed on the face
Next I machined the groove in the side panels to accept the back panels, using the biscuit jointer. I found this to be the quickest, most accurate and dust-free way of doing it. Just make sure the fence is tight against the panel, the jointer is flat on the surface and the jointer is moved right to left (against the rotation of the blade). I also tried cutting the groove with a router and kerfing with a circ. saw but neither was as accurate as the biscuit jointer and both created much more dust.
Next up was sealing the fluffy cut edges of the shelves that will be painted. I found I got excellent results by applying a 50% aqueous solution of PVA with a roller bottle, letting it dry then knocking it back with 180 grit. This gave an almost glassy smooth surface that took the paint really well
Finishing was next. 1 coat of Dulux Trade U/C and 2 coats of Dulux Trade High Gloss applied with a small gloss roller. I was really impressed with the finish, although I had to take care when striking off to avoid getting 'tram lines'. Here's some shelves in a home made drying rack;
And I'm now in the middle of assembly;
I'll post more WIP pics after the units are fitted. I know it's not exactly fine furniture making and prob not to everyone's tastes but I've learnt quite a bit and I really like the painted finish.
DD
After a lot of faffing about with different designs (most of which looked like post office pigeon holes) I came up with this
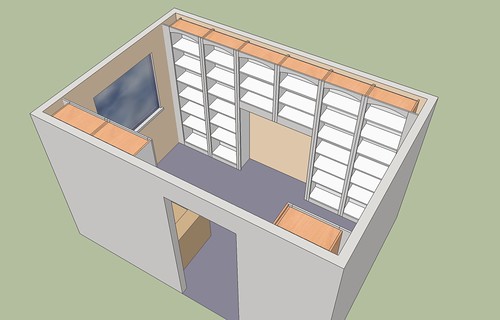
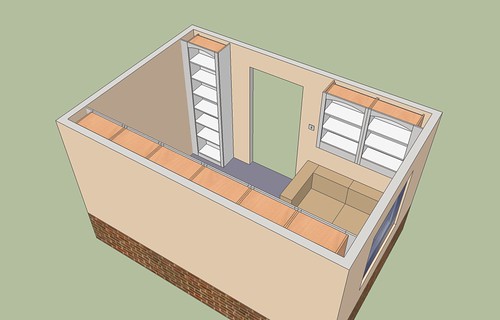
Constructing components on SU as if I would build them in real life (i.e. from individual flat panels) makes it easy to explode each component and import each parts dimensions into the cutting list program;
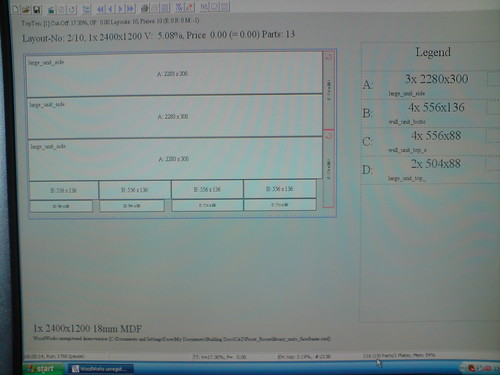
Ordered up the MDF sheets. When they arrived, I stacked them flat on the bench. Then its only a matter of sticking a couple of 4x2's under the top sheet and start cutting;
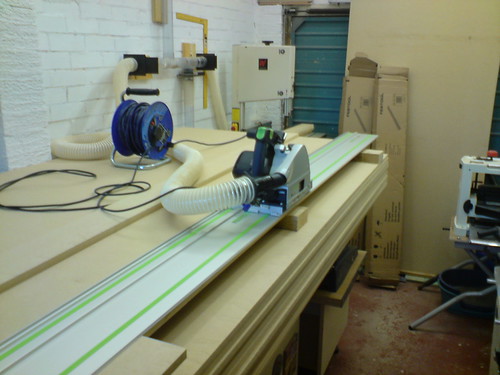
And thats all the components cut. In total, 10 sheets of 18mm and 5 sheets of 6mm (for the backs)
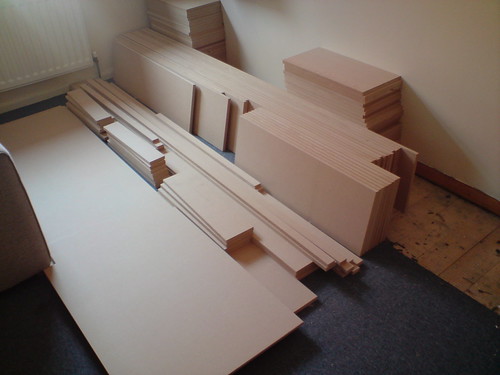
Next thing to do is to mark out the templates for the top arched rails of the face frames. I call this 'The Curvulator'
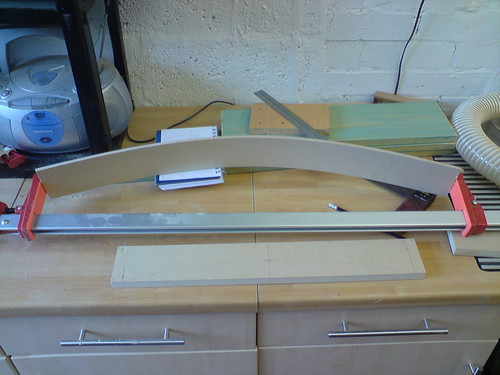
The bulk is then removed at the band saw...
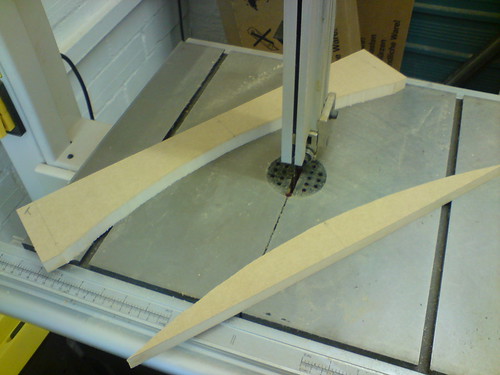
...and carefully sanded to the line
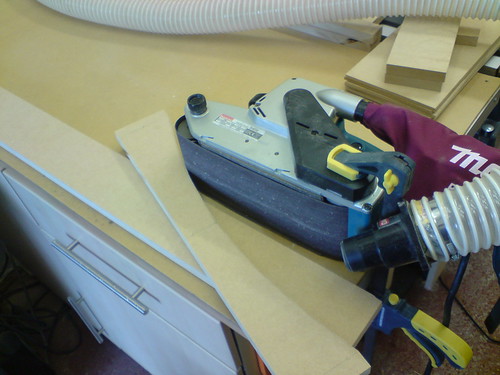
I then screwed the template to the rail (with the bulk removed at the bandsaw) and used a bearing guided straight cutting bit in the router table
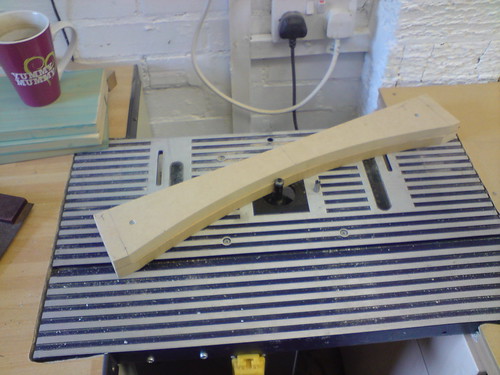
Face frames assembled using Kreg pocket screws
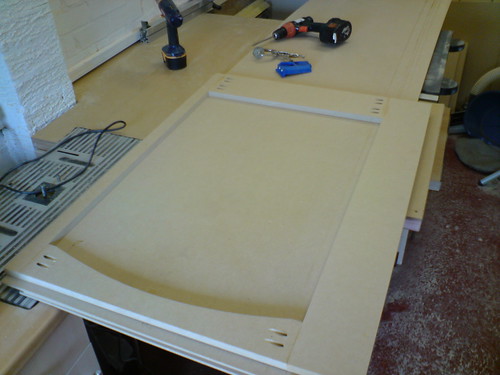
And an ogee profile routed on the face
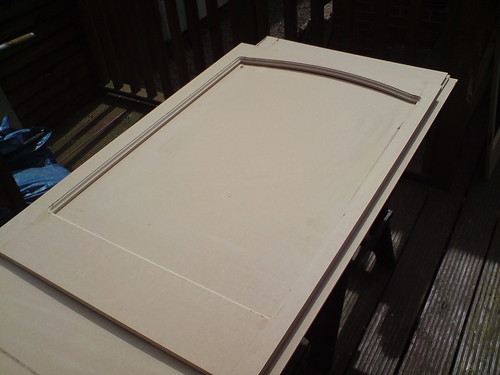
Next I machined the groove in the side panels to accept the back panels, using the biscuit jointer. I found this to be the quickest, most accurate and dust-free way of doing it. Just make sure the fence is tight against the panel, the jointer is flat on the surface and the jointer is moved right to left (against the rotation of the blade). I also tried cutting the groove with a router and kerfing with a circ. saw but neither was as accurate as the biscuit jointer and both created much more dust.
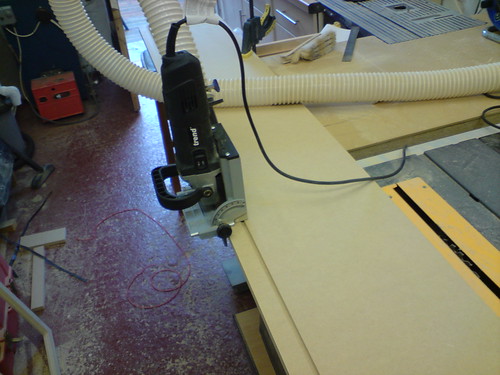
Next up was sealing the fluffy cut edges of the shelves that will be painted. I found I got excellent results by applying a 50% aqueous solution of PVA with a roller bottle, letting it dry then knocking it back with 180 grit. This gave an almost glassy smooth surface that took the paint really well
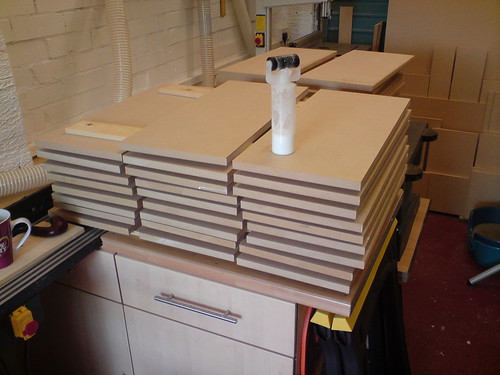
Finishing was next. 1 coat of Dulux Trade U/C and 2 coats of Dulux Trade High Gloss applied with a small gloss roller. I was really impressed with the finish, although I had to take care when striking off to avoid getting 'tram lines'. Here's some shelves in a home made drying rack;
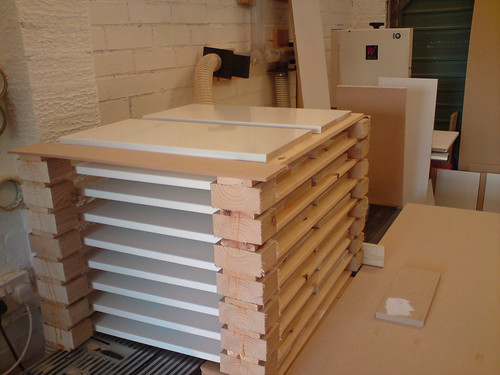
And I'm now in the middle of assembly;
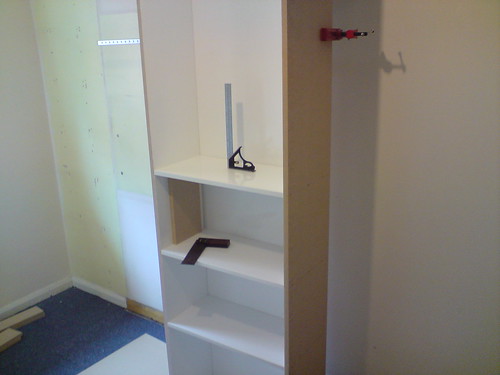
I'll post more WIP pics after the units are fitted. I know it's not exactly fine furniture making and prob not to everyone's tastes but I've learnt quite a bit and I really like the painted finish.
DD