Eric The Viking
Established Member
- Joined
- 19 Jan 2010
- Messages
- 6,599
- Reaction score
- 76
OK, I agree with the consensus that this is a big mistake on the part of the manufacturer, but you may or may not get a fix from them. Assuming this ends up as DIY, I've a thought developing (been watching too much of Steve M. jig-making recently!):
@Tom: Behind the adjustment handwheel, is the machine's cover reasonably flat? Also,do you know what's directly behind the cover (the bit that's behind the wheel)?
My reason for asking is that, assuming it's a flat piece of thin steel sheet, it ought to be possible to make a friction lock. Whether it would stay locked with all the vibration is another matter, but I had in mind something like this:
With a bit of thick steel plate and an M8 tap you could make a lever instead of the locking nut, eliminating the need for a spanner on-hand.
It looks from the Axy pictures though that the handwheel is some distance from the panel - this would be a PITA because of the twisting forces on the stud, and might not work for that reason.
Also, what about clamping the shaft tightly?
This can't be an insurmountable problem, and TBH I'm really surprised the manufacturers aren't helping more - they ought at least to be interested in why it's slipping, and to offer a solution. IMHO, you're being fobbed-off with the comment about the shaft encoder (or whatever it is)...
@Tom: Behind the adjustment handwheel, is the machine's cover reasonably flat? Also,do you know what's directly behind the cover (the bit that's behind the wheel)?
My reason for asking is that, assuming it's a flat piece of thin steel sheet, it ought to be possible to make a friction lock. Whether it would stay locked with all the vibration is another matter, but I had in mind something like this:
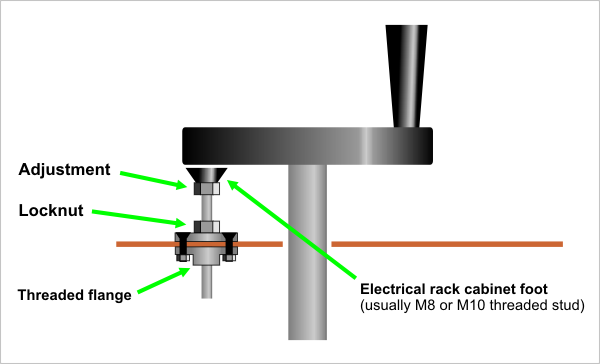
With a bit of thick steel plate and an M8 tap you could make a lever instead of the locking nut, eliminating the need for a spanner on-hand.
It looks from the Axy pictures though that the handwheel is some distance from the panel - this would be a PITA because of the twisting forces on the stud, and might not work for that reason.
Also, what about clamping the shaft tightly?
This can't be an insurmountable problem, and TBH I'm really surprised the manufacturers aren't helping more - they ought at least to be interested in why it's slipping, and to offer a solution. IMHO, you're being fobbed-off with the comment about the shaft encoder (or whatever it is)...