I think you're probably joking, but I'm sure someone has tried it somewhere - especially machinists who haven't worked wood.
the person in question who helped me track down more data (than just feet planed, weight planed and pictures) is named Bill Tindall. He was a research chemist/pharmacist here who makes pretty nice furniture in retirement, but aside from wanting to know the answer, he and I don't really operate the same way. He understands the chemistry/physics of everything, formulates what should be, then tries to test a hypothesis. If things don't work right, then he searches for the answer and moves forward.
There are tiny things that make hand tool items work differently than other woodworking, and far different than diemaking or knifemaking, so I have always been of the school "nothing is better than carbon steel, it's easy to sharpen, it wears away sharpening issues as it's planing and it is always just dull and not damaged when it comes time to sharpen".
Bill's view is, look at the data, then get some things made and try them. I'll try things first, see how they work, and then use those to predict something next. I have had poor experience with steels that have great chart toughness and wear resistance but can't hold and wear the intial edge well. There's a very tough steel marketed as SGPS here in the states -if you can sharpen it, you can scrape a pipe with it and it doesn't take much wear. However ,it will literally give up its initial edge to a strop. That's worthless to me. I can only get a good edge on it with a buffer and it has to be rounded over.
To me, most of the steels come with compromises that I can't stand, probably because they have a lot of vanadium. M4 powder metal is very durable, it holds its edge but wears with a lot of friction in the wood. You can *feel* it. It made my wrists sore testing, I wished it wouldn't have lasted nearly as long as it did.
V11 has tiny chromium carbides in it and not much else. It's really slick in the wood, and you end up thinking "maybe I just had a good round sharpening", but I was very deliberate sharpening, and found through repeated iterations that indeed there were visible differences between the slick steels and the ones that experienced friction. japanese blue steel plane blades (the ones that are sold by woodworking suppliers) had surprising surface dullness (I expected them to be the best) compared to V11 and a lot of friction, both in beech and hard maple. Maybe in softwoods, they wouldn't.
Each edge started bright and clear in these pictures, but within 200 feet, the japanese iron edge looked like this:
WTF is that? The little bits that appear to be pulled out of the surface and then scuff the blade as they come out?
Here it is at 600 feet. the blade didn't last much longer than this, but by hardness and alloy, it should've outlasted O1. It didn't, they tied:
But O1 was nicer to use, and while it dulled fairly quickly, it did so uniformly. Here it is at 600 feet - lovely.
Here's V11 after 800 feet - there's a line of wear, and there's some oil and wood dust at the edge, but look how even the edge is. Like carbon steel. Lovely. Surface better at 800 than O1 at 400, but that brightness is just an indicator of sorts, all samples tearout free, so a scraper and sander isn't going to care.
Surface brightness, though, seemed to correlate with planing resistance.
Long story short, Bill has postulated all kinds of wear surfaces on plane irons, but he's finally given up (be it plated diamonds, metalworking tool coatings, etc). A practical test of all of these things together has yielded far more usable data.
And after much searching, Bill finally found a metallurgist who could talk to the difference between cutting steels for wood vs. wear steels for metal, and why vanadium doesn't seem to be that great in wood (despite its superior hardness) vs. chromium (chromium carbides are only a little harder than iron carbides). The answer from the metallurgist was related to size - lots of small carbides are good for cutting softer materials, and lots of bigger harder carbides are good for cutting really hard materials.
I'm still an ardent supporter of carbon steel and no faffing, but I cannot deny that certain high chromium (stainless) steels where vanadium is left out and the carbides are kept small by process are actually better at smooth planing than carbon steel. And tolerable to sharpen.
Everything harder with big carbides (like stellite, rex, etc.) is ideal for metal, not wood.
Oh, here's some ward water hardening for the fans. It only lasted about 550 feet, but it was sharpened on an oilstone. I think it would've gone another 100 with some more refinement - notice its ability to wear evenly despite the larger sharpening scratches from the natural stones. That is a very attractive property that O1 and old steel has. V11 shares it.
This also allows a look at what natural stone grooves look like vs. 1 micron diamond powder. I hate to say it, but when you get into the small oxides and diamonds, you cannot match them with natural stones. I wish that wasn't the case, as I'm a huge fan of the latter, and still using them (instead of the diamonds).
the person in question who helped me track down more data (than just feet planed, weight planed and pictures) is named Bill Tindall. He was a research chemist/pharmacist here who makes pretty nice furniture in retirement, but aside from wanting to know the answer, he and I don't really operate the same way. He understands the chemistry/physics of everything, formulates what should be, then tries to test a hypothesis. If things don't work right, then he searches for the answer and moves forward.
There are tiny things that make hand tool items work differently than other woodworking, and far different than diemaking or knifemaking, so I have always been of the school "nothing is better than carbon steel, it's easy to sharpen, it wears away sharpening issues as it's planing and it is always just dull and not damaged when it comes time to sharpen".
Bill's view is, look at the data, then get some things made and try them. I'll try things first, see how they work, and then use those to predict something next. I have had poor experience with steels that have great chart toughness and wear resistance but can't hold and wear the intial edge well. There's a very tough steel marketed as SGPS here in the states -if you can sharpen it, you can scrape a pipe with it and it doesn't take much wear. However ,it will literally give up its initial edge to a strop. That's worthless to me. I can only get a good edge on it with a buffer and it has to be rounded over.
To me, most of the steels come with compromises that I can't stand, probably because they have a lot of vanadium. M4 powder metal is very durable, it holds its edge but wears with a lot of friction in the wood. You can *feel* it. It made my wrists sore testing, I wished it wouldn't have lasted nearly as long as it did.
V11 has tiny chromium carbides in it and not much else. It's really slick in the wood, and you end up thinking "maybe I just had a good round sharpening", but I was very deliberate sharpening, and found through repeated iterations that indeed there were visible differences between the slick steels and the ones that experienced friction. japanese blue steel plane blades (the ones that are sold by woodworking suppliers) had surprising surface dullness (I expected them to be the best) compared to V11 and a lot of friction, both in beech and hard maple. Maybe in softwoods, they wouldn't.
Each edge started bright and clear in these pictures, but within 200 feet, the japanese iron edge looked like this:

WTF is that? The little bits that appear to be pulled out of the surface and then scuff the blade as they come out?
Here it is at 600 feet. the blade didn't last much longer than this, but by hardness and alloy, it should've outlasted O1. It didn't, they tied:
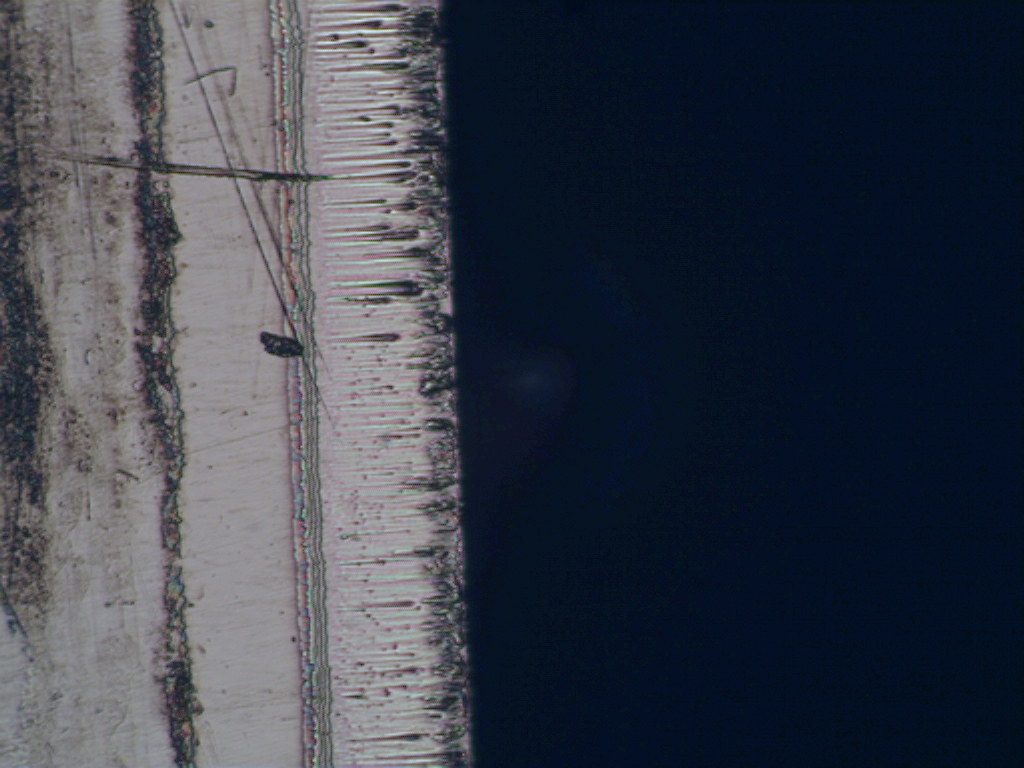
But O1 was nicer to use, and while it dulled fairly quickly, it did so uniformly. Here it is at 600 feet - lovely.

Here's V11 after 800 feet - there's a line of wear, and there's some oil and wood dust at the edge, but look how even the edge is. Like carbon steel. Lovely. Surface better at 800 than O1 at 400, but that brightness is just an indicator of sorts, all samples tearout free, so a scraper and sander isn't going to care.
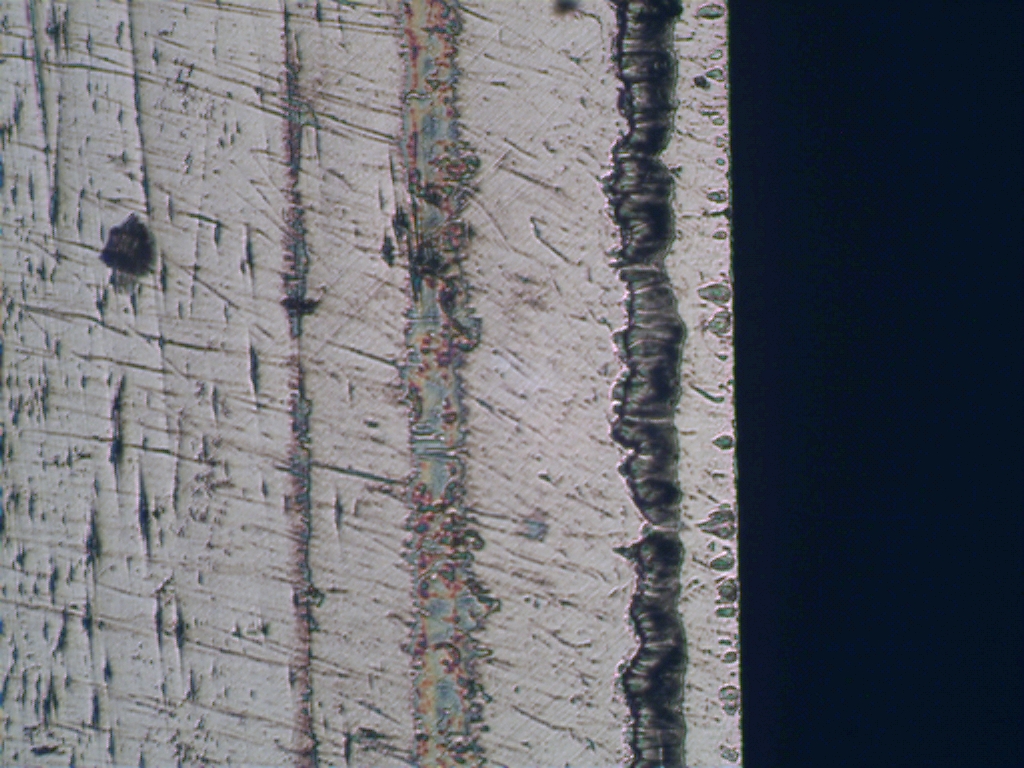
Surface brightness, though, seemed to correlate with planing resistance.
Long story short, Bill has postulated all kinds of wear surfaces on plane irons, but he's finally given up (be it plated diamonds, metalworking tool coatings, etc). A practical test of all of these things together has yielded far more usable data.
And after much searching, Bill finally found a metallurgist who could talk to the difference between cutting steels for wood vs. wear steels for metal, and why vanadium doesn't seem to be that great in wood (despite its superior hardness) vs. chromium (chromium carbides are only a little harder than iron carbides). The answer from the metallurgist was related to size - lots of small carbides are good for cutting softer materials, and lots of bigger harder carbides are good for cutting really hard materials.
I'm still an ardent supporter of carbon steel and no faffing, but I cannot deny that certain high chromium (stainless) steels where vanadium is left out and the carbides are kept small by process are actually better at smooth planing than carbon steel. And tolerable to sharpen.
Everything harder with big carbides (like stellite, rex, etc.) is ideal for metal, not wood.
Oh, here's some ward water hardening for the fans. It only lasted about 550 feet, but it was sharpened on an oilstone. I think it would've gone another 100 with some more refinement - notice its ability to wear evenly despite the larger sharpening scratches from the natural stones. That is a very attractive property that O1 and old steel has. V11 shares it.
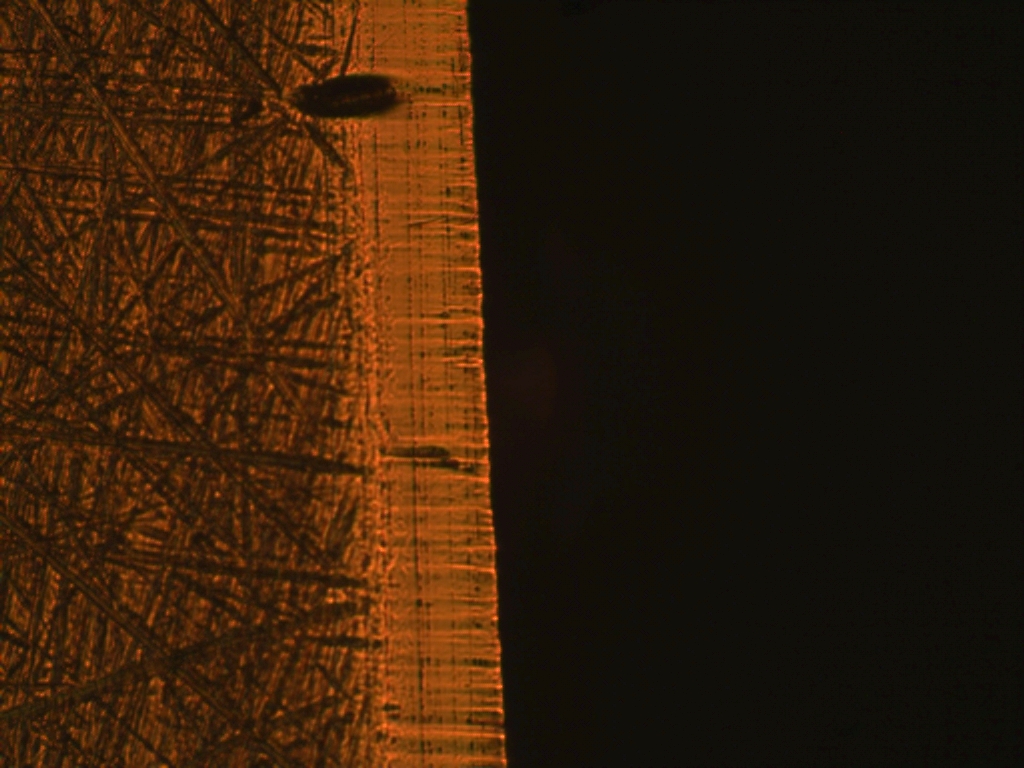
This also allows a look at what natural stone grooves look like vs. 1 micron diamond powder. I hate to say it, but when you get into the small oxides and diamonds, you cannot match them with natural stones. I wish that wasn't the case, as I'm a huge fan of the latter, and still using them (instead of the diamonds).