RobertMP
Established Member
Changed thread title to make a bit more sense 
changed it again now to include making a stand for it.
................
I've taken the saw apart and cleaned out the accumulated sawdust.
Then I removed the internal blade guard
blade has seen better days
The black strip that moves (rotates it about the blade axis) the riving knife bracket was a little bent but is straight now.
I didn't fancy destroying the original blade guard so i made a flat plate version from sheet aluminium. I had some threaded bushes so i used a couple of those as spacers and superglued them against vibration. then a bit of black spray so it looks the part
Now this is where it gets interesting.... When the blade is in the fully lowered position the riving knife bracket stops the travel before the adjusting thread on the handwheel bottoms out. That means the little black strip is in compression when you hit resistance on the handwheel. Continue winding to try and get the blade flush or just below flush and the black strip bends. You can see the hole near centre of the picture has travelled past the end of the banana slot below it when the handwheel reaches the end of its thread.
here's the same hole from the other side
Closer look
What I'm thinking is if I can extend the movement slot a little, the blade will lower under flush easily and the black strip that rotates the riving knife bracket cannot get bent again.
Not an easy spot to work in though. Worth the effort?
Edit... Oh and I found the 'problem' as described in the ebay listing - the belt was loose and slipping so i tightened it
I could turn the blade mount whilst holding the motor stopped before but can't now.
changed it again now to include making a stand for it.
................
I've taken the saw apart and cleaned out the accumulated sawdust.
Then I removed the internal blade guard
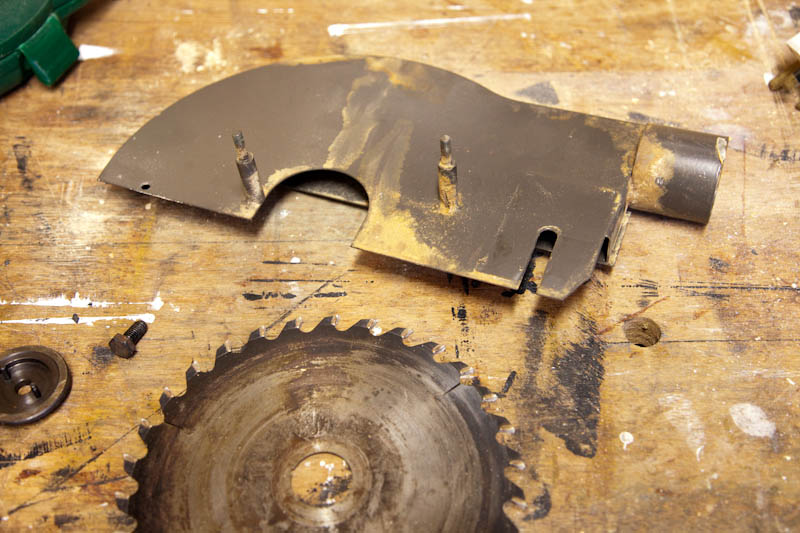
blade has seen better days
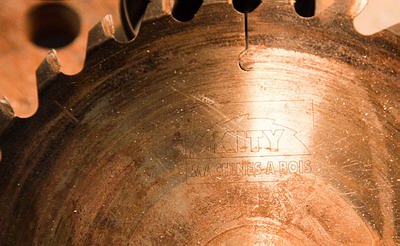
The black strip that moves (rotates it about the blade axis) the riving knife bracket was a little bent but is straight now.
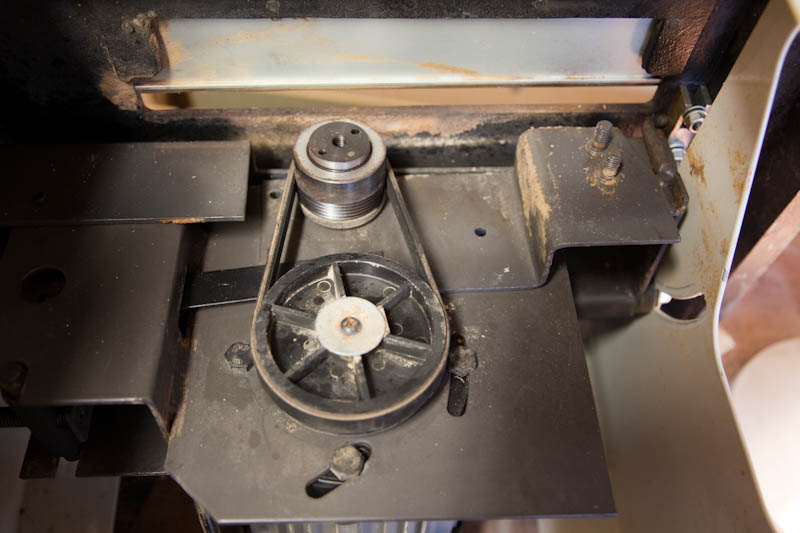
I didn't fancy destroying the original blade guard so i made a flat plate version from sheet aluminium. I had some threaded bushes so i used a couple of those as spacers and superglued them against vibration. then a bit of black spray so it looks the part
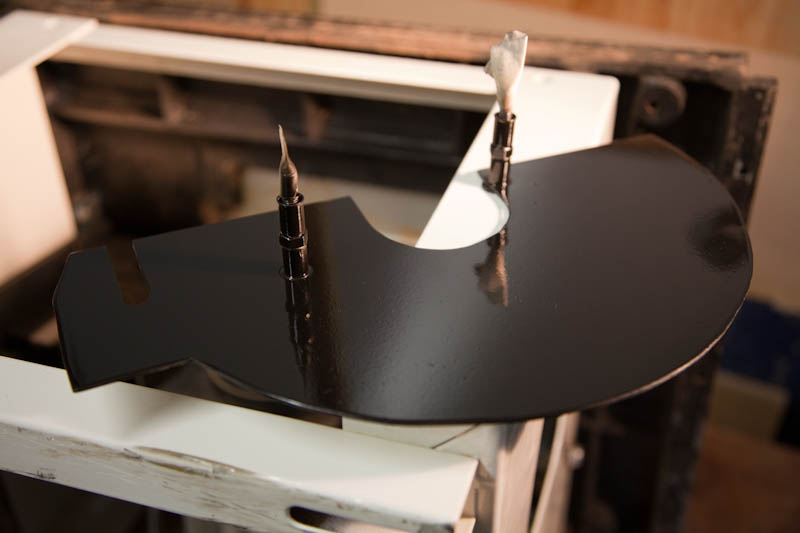
Now this is where it gets interesting.... When the blade is in the fully lowered position the riving knife bracket stops the travel before the adjusting thread on the handwheel bottoms out. That means the little black strip is in compression when you hit resistance on the handwheel. Continue winding to try and get the blade flush or just below flush and the black strip bends. You can see the hole near centre of the picture has travelled past the end of the banana slot below it when the handwheel reaches the end of its thread.
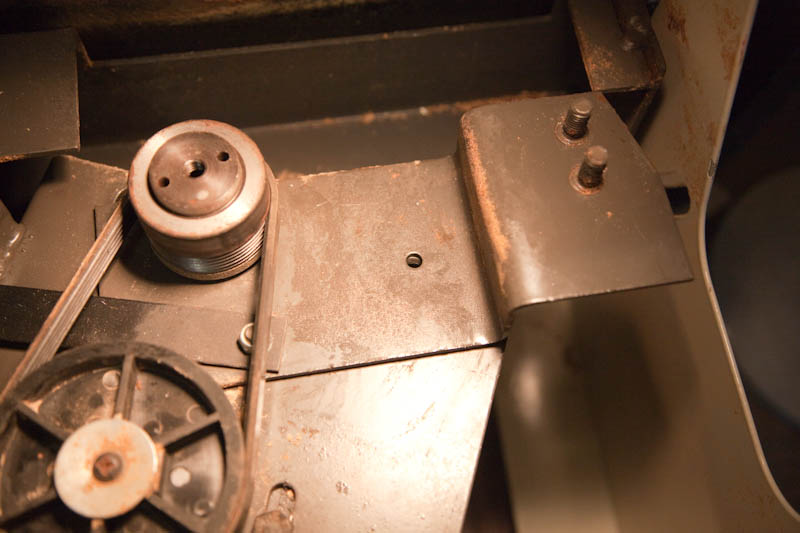
here's the same hole from the other side
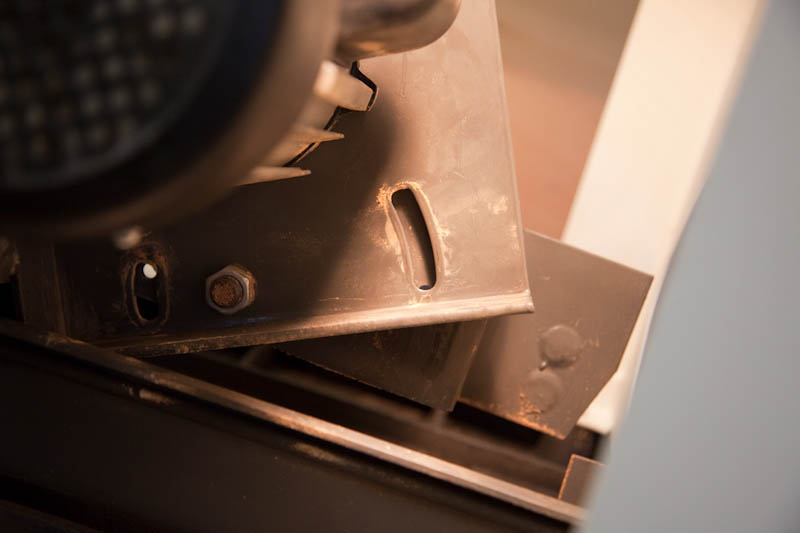
Closer look
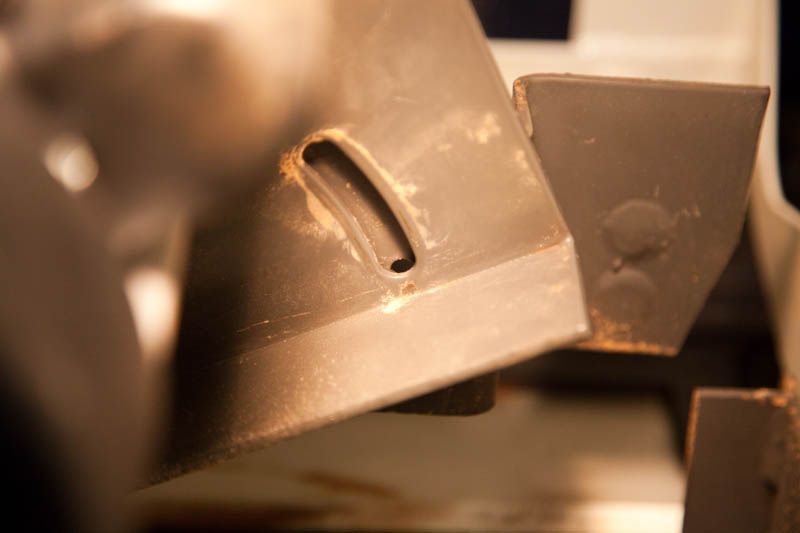
What I'm thinking is if I can extend the movement slot a little, the blade will lower under flush easily and the black strip that rotates the riving knife bracket cannot get bent again.
Not an easy spot to work in though. Worth the effort?
Edit... Oh and I found the 'problem' as described in the ebay listing - the belt was loose and slipping so i tightened it