wallace
Established Member
The switch has been replaced by a modern one but I have a lovely original one which I hope I can use.
Heres the new and old together. Can anyone advise me if I can use the old switch as is or should I just have the modern buttons hid inside and the old buttons to press
I ran out of my usual zinc primer but found a tin of base primer which I don't know where it came from. It covered really well
And then a top coat
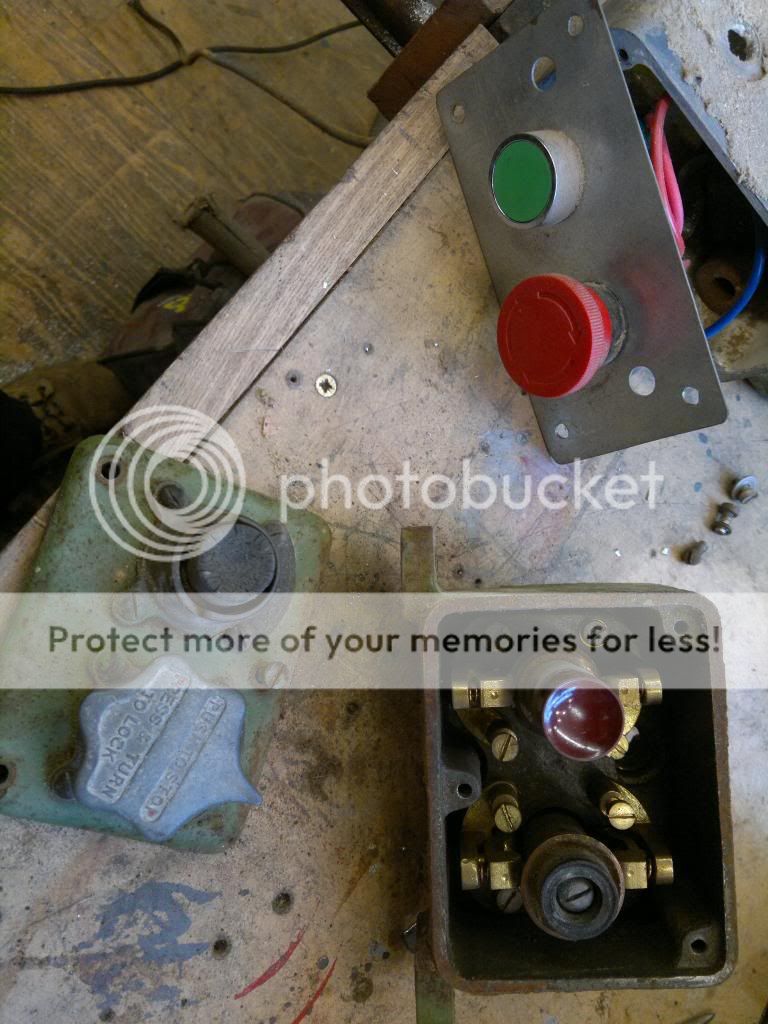
Heres the new and old together. Can anyone advise me if I can use the old switch as is or should I just have the modern buttons hid inside and the old buttons to press
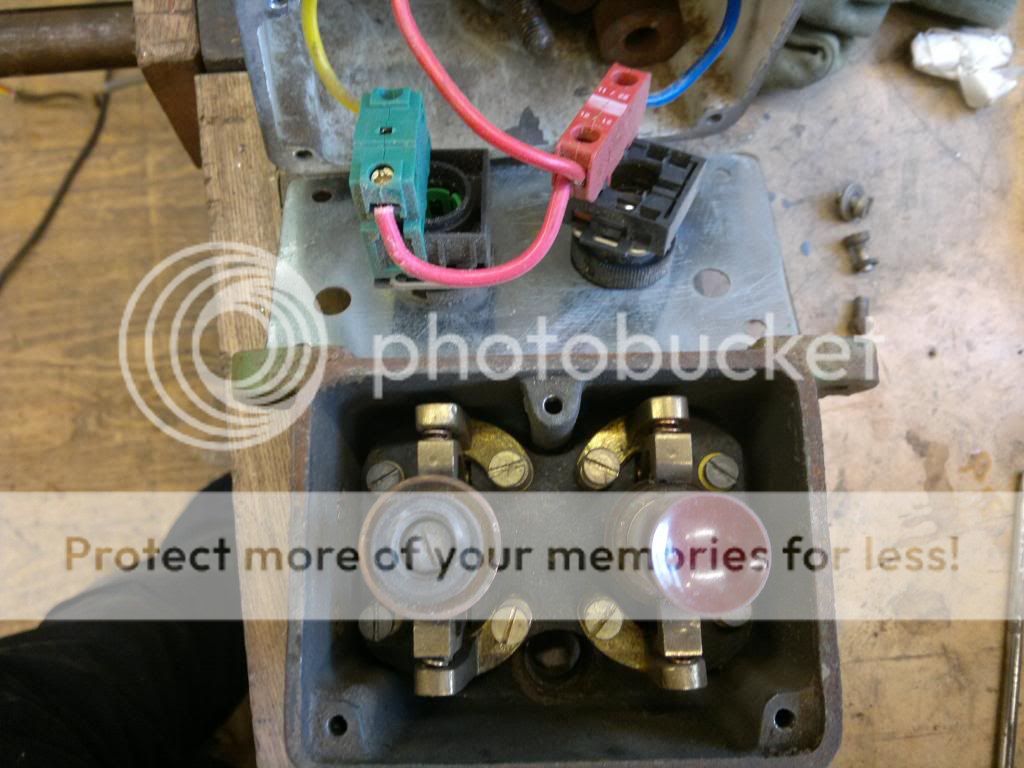
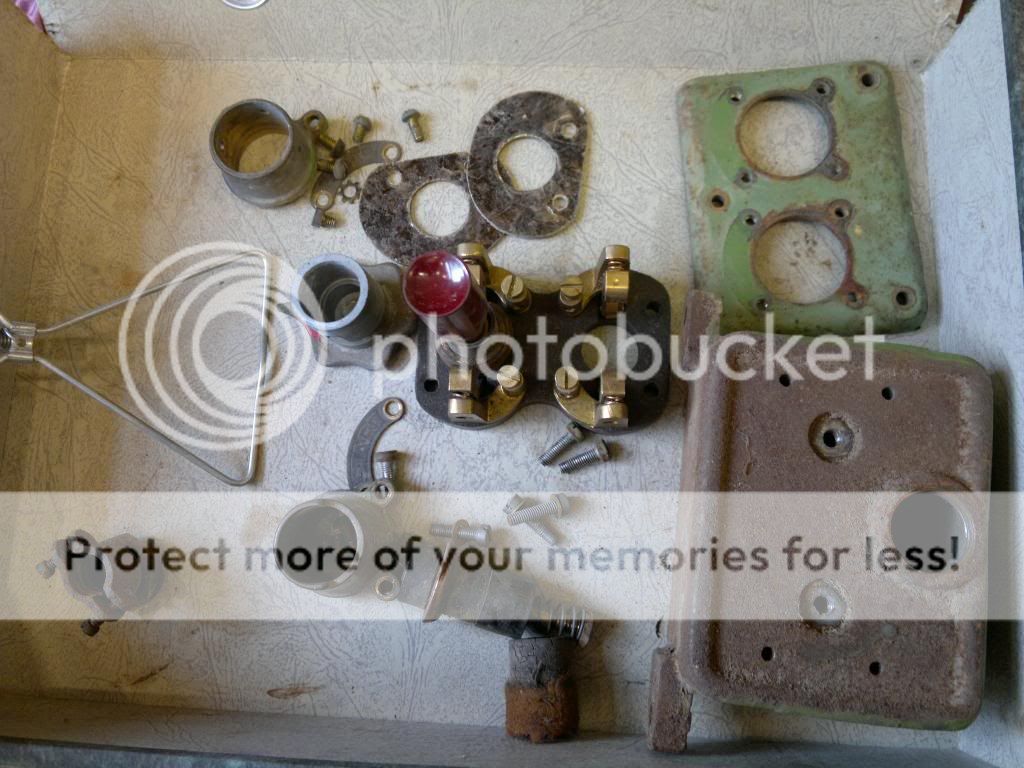
I ran out of my usual zinc primer but found a tin of base primer which I don't know where it came from. It covered really well
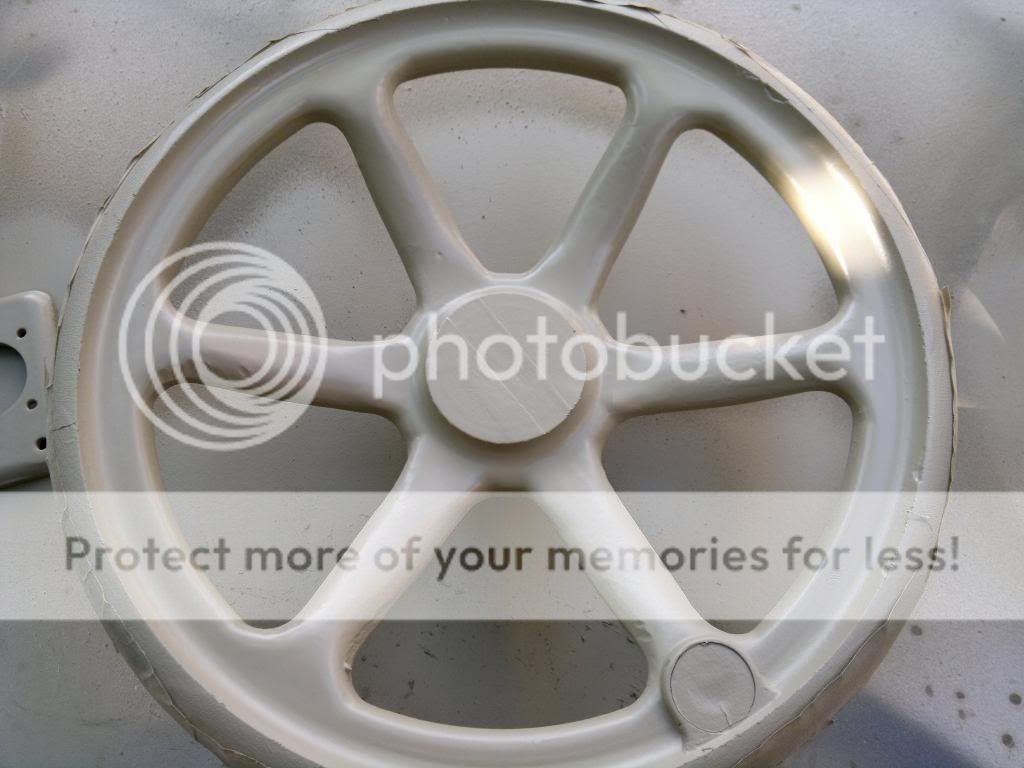
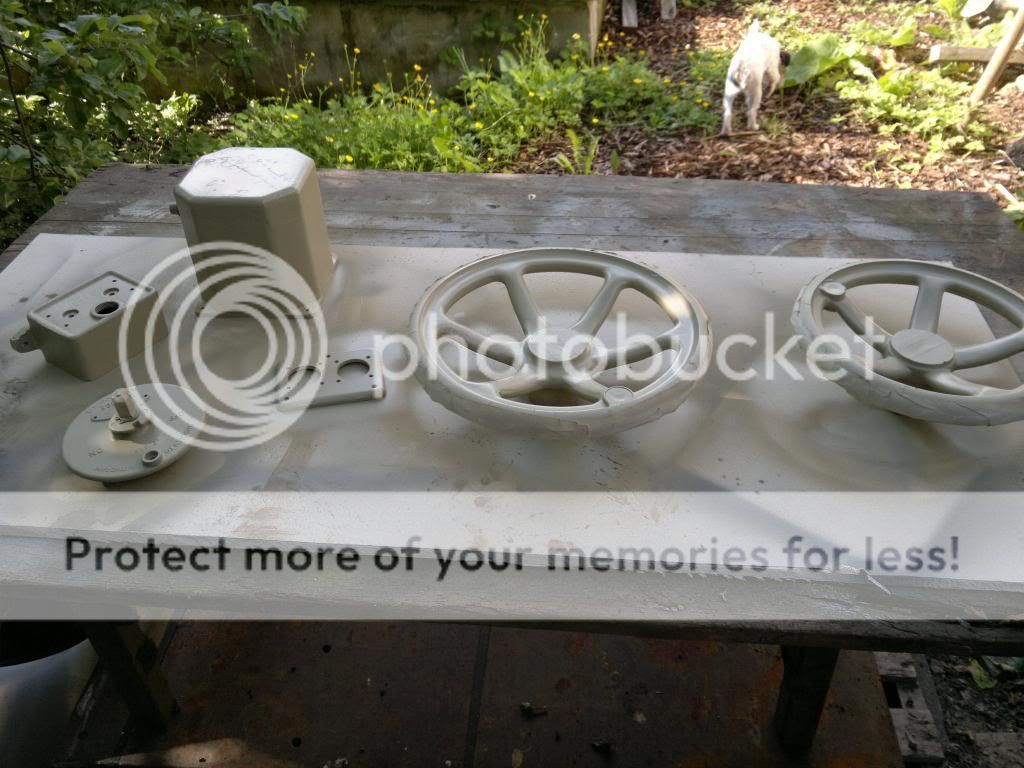
And then a top coat
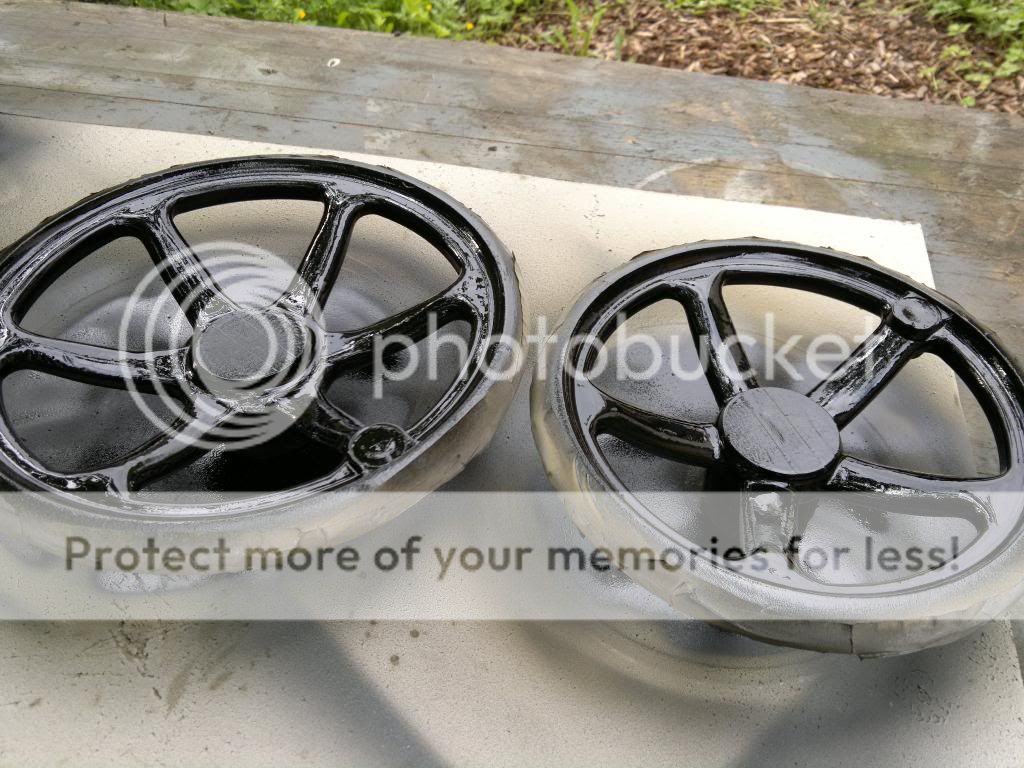