Simo
Established Member
- Joined
- 28 Mar 2009
- Messages
- 186
- Reaction score
- 118
Sorry for the lack of updates, I've had a lot of time away from the workbench lately. Anyway, here's a brief update.. more on the way shortly.
The neck is made from 3 pieces of Maple, with black veneers laminated in between. The headstock is angled (scarf joint), and has Ebony veneers on both sides.
I use some masking tape to make the centre lines easier to line up, then after fitting some alignment pins underneath the fingerboard, it's glued on and left to cure, before being planed flush.
The tuner holes have been drilled, and it's starting to look like a neck (hammer)
The neck is made from 3 pieces of Maple, with black veneers laminated in between. The headstock is angled (scarf joint), and has Ebony veneers on both sides.
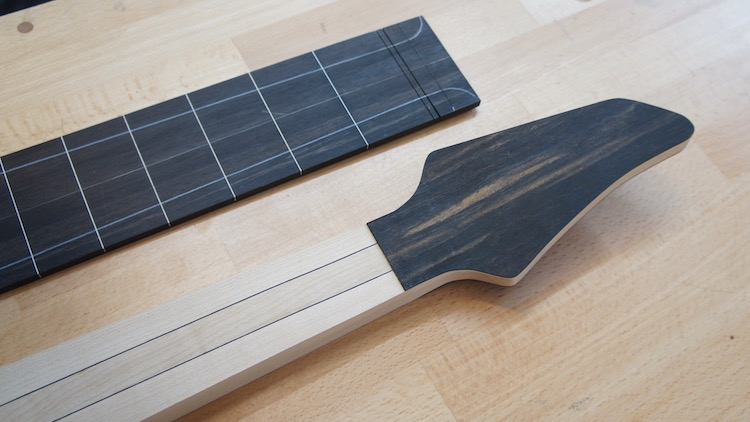
I use some masking tape to make the centre lines easier to line up, then after fitting some alignment pins underneath the fingerboard, it's glued on and left to cure, before being planed flush.
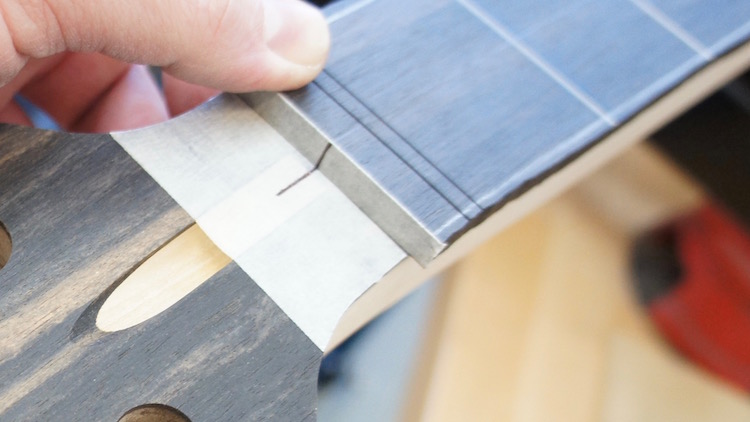
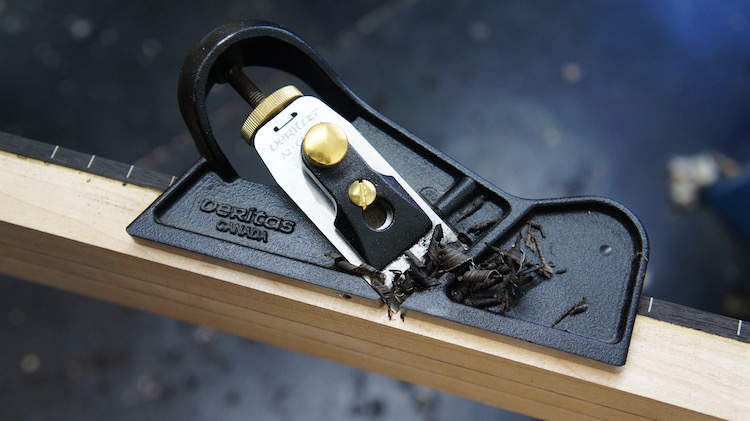
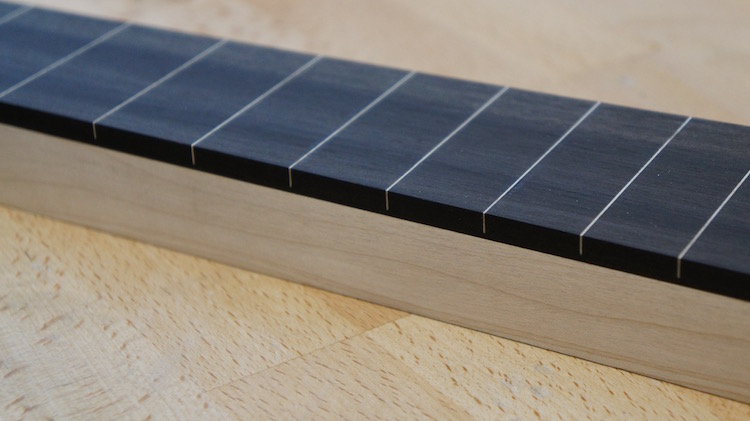
The tuner holes have been drilled, and it's starting to look like a neck (hammer)
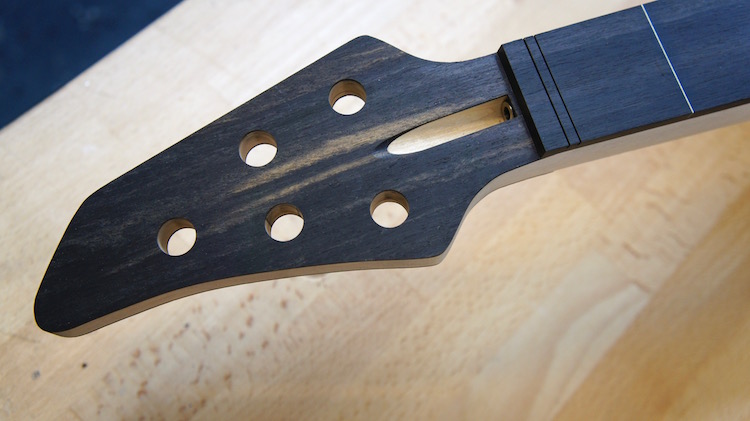