mailee
Established Member
Just started another 'quickie' job so I thought it might be worth a WIP this time. It is a toybox seat in Pine this time. It has been a while since I used the dovetail jig so I dusted it off and ran a test piece. Once I was happy with it I got on with cutting the pieces.
Glad to say I still remembered how to use it. :lol: After cutting the pins on the ends I cut the tails on the front and back pieces carefully marking out where each one would fit.
I then set about cutting a curve and hand holes on each end. Then a run around the edge with a half round cutter to soften the edge.
my customer wanted the child's name on it so it was out with the router again to 'carve' the name on the front piece.
With the name on and a light sanding I then got it in a glue up.
Tomorrow I shall make the top and the plinth and put the base in.....hopefully.
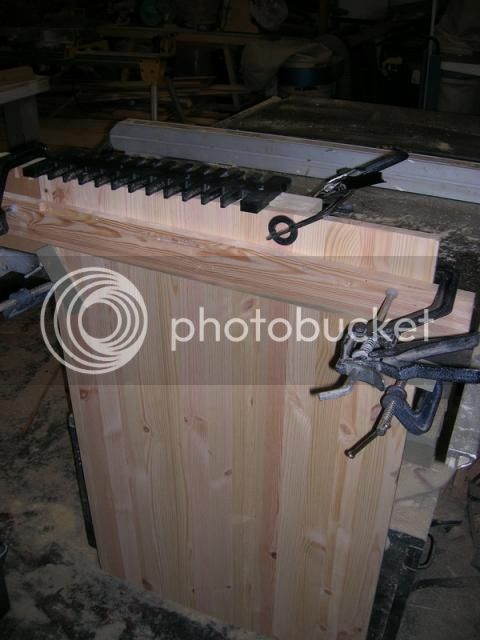
Glad to say I still remembered how to use it. :lol: After cutting the pins on the ends I cut the tails on the front and back pieces carefully marking out where each one would fit.
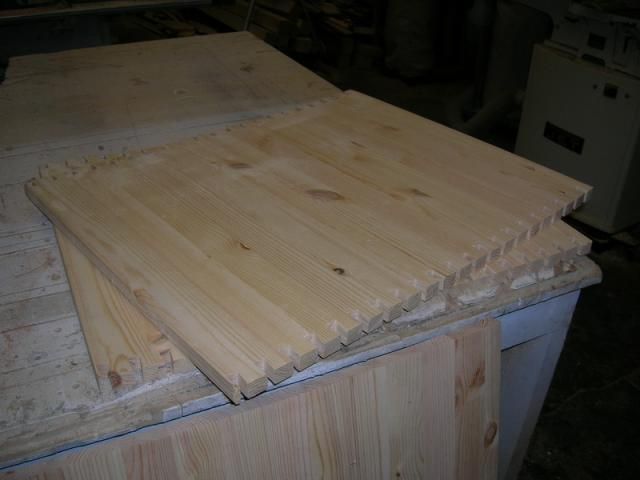
I then set about cutting a curve and hand holes on each end. Then a run around the edge with a half round cutter to soften the edge.
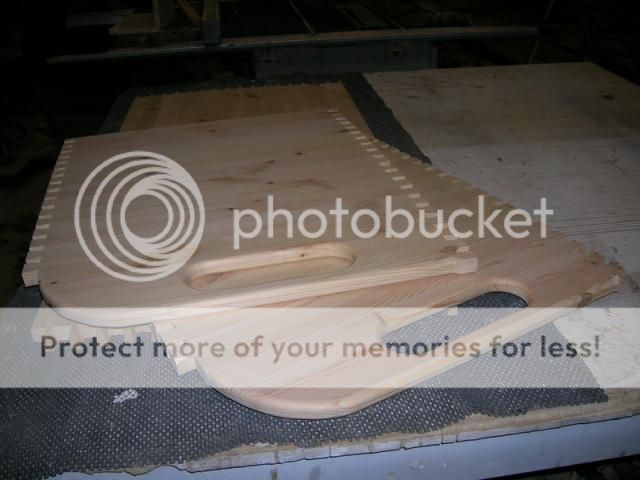
my customer wanted the child's name on it so it was out with the router again to 'carve' the name on the front piece.
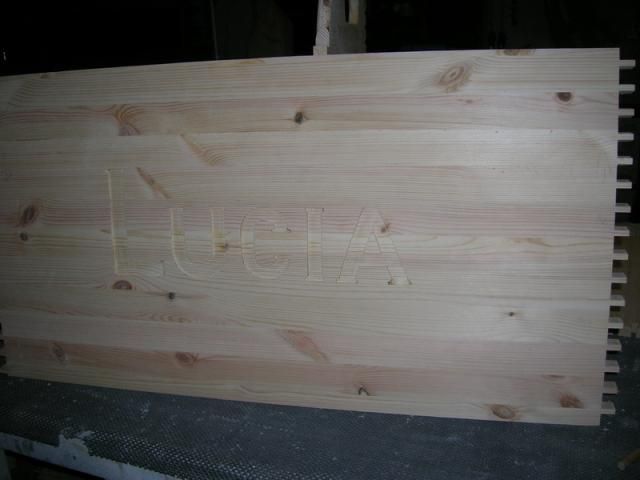
With the name on and a light sanding I then got it in a glue up.
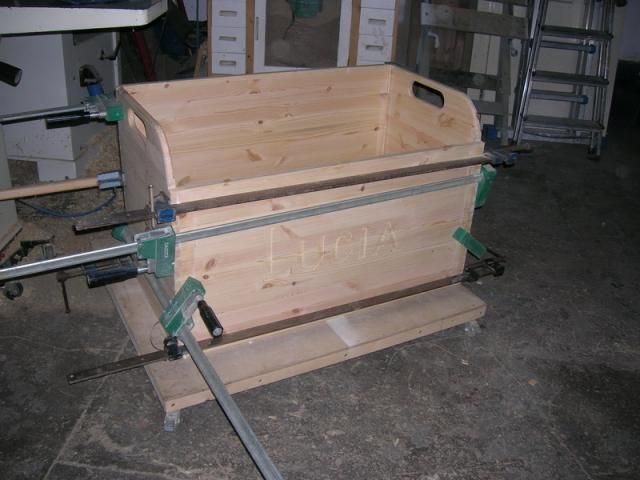
Tomorrow I shall make the top and the plinth and put the base in.....hopefully.