Derek Cohen (Perth Oz)
Established Member
For many years I have used a Drill Doctor to sharpen drill bits, always feeling a little guilty as I have prided myself in sharpening just about anything freehand. This is excusable for very small bits, but 1/8" and up should be doable by hand ... well, I have seen these demonstrated for some years. Anyway, recently I decided that it was time to learn, and especially with bits 3/8" and up since these were time-consuming on the Drill Doctor.
For woodworking, twist drill bits have a 30 degree slope to each side. One cannot, however, simply grind the side slopes square and expect them to work. The cutting edge requires a relief angle otherwise it will not cut. In other words, sharpening a drill bit is not like sharpening a chisel or plane blade - the drill bit cutting edge needs to be both square (at the face) and rounded (from the face back).
To train my hand, I came up with a guide (or jig). This presents the bit to a bench grinder wheel at 30 degrees, and then holds this constant as the bit is lifted against the wheel to create the relief. Here is the guide ...
The fence lies at 60 degrees to the front, and there is a 19mm (3/4") dowel to rest the bit on.
The jig is clamped to the platform on my bench grinder (which uses an 80 grit CBN wheel here).
The drill bit is pushed along the fence and against the wheel, with the cutting edge on the horizontal ...
Once the cutting face is ground, rotate the drill bit upwards so the the back is ground at an angle (actually, it should be rounded). That is the relief edge ...
The result is like so ...
Proof of the pudding ...
Regards from Perth
Derek
For woodworking, twist drill bits have a 30 degree slope to each side. One cannot, however, simply grind the side slopes square and expect them to work. The cutting edge requires a relief angle otherwise it will not cut. In other words, sharpening a drill bit is not like sharpening a chisel or plane blade - the drill bit cutting edge needs to be both square (at the face) and rounded (from the face back).
To train my hand, I came up with a guide (or jig). This presents the bit to a bench grinder wheel at 30 degrees, and then holds this constant as the bit is lifted against the wheel to create the relief. Here is the guide ...
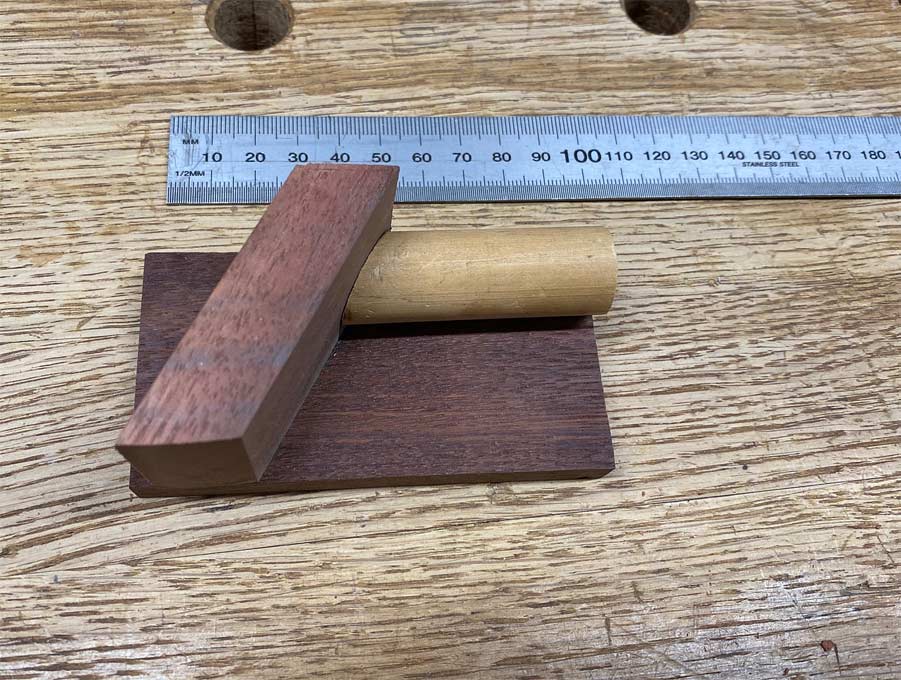
The fence lies at 60 degrees to the front, and there is a 19mm (3/4") dowel to rest the bit on.
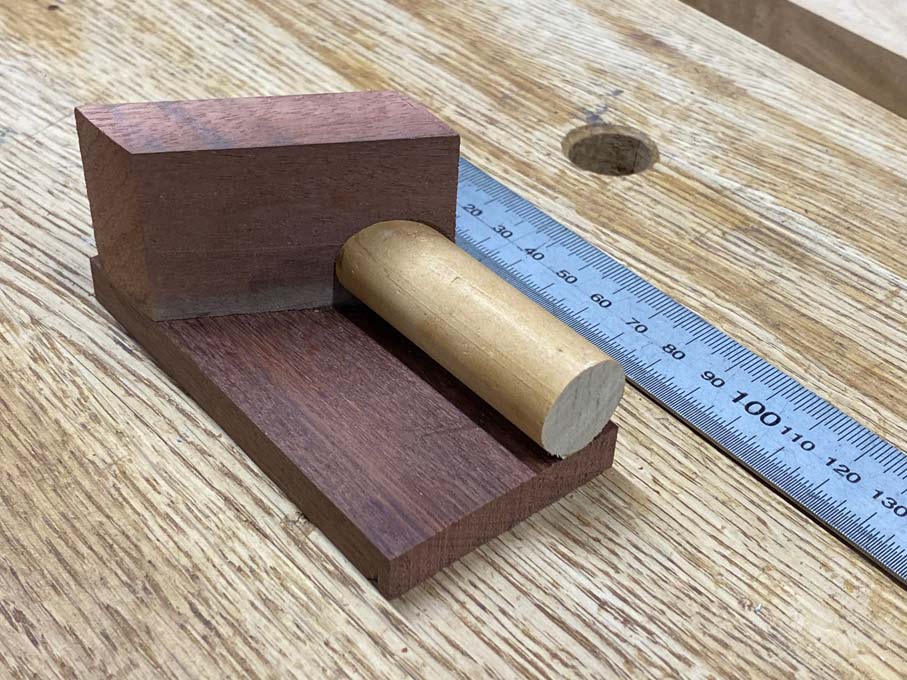
The jig is clamped to the platform on my bench grinder (which uses an 80 grit CBN wheel here).
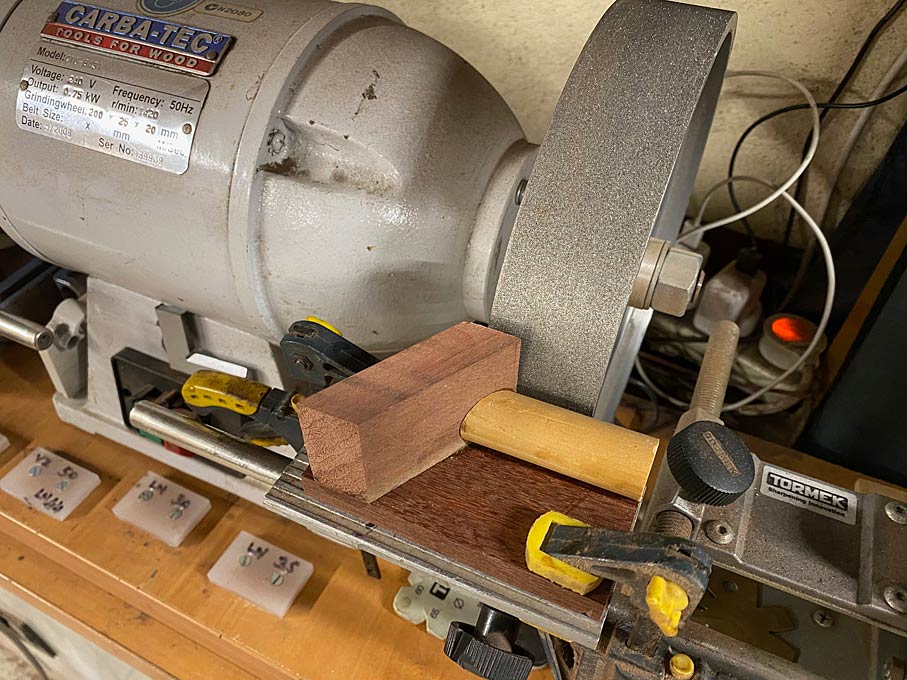
The drill bit is pushed along the fence and against the wheel, with the cutting edge on the horizontal ...

Once the cutting face is ground, rotate the drill bit upwards so the the back is ground at an angle (actually, it should be rounded). That is the relief edge ...
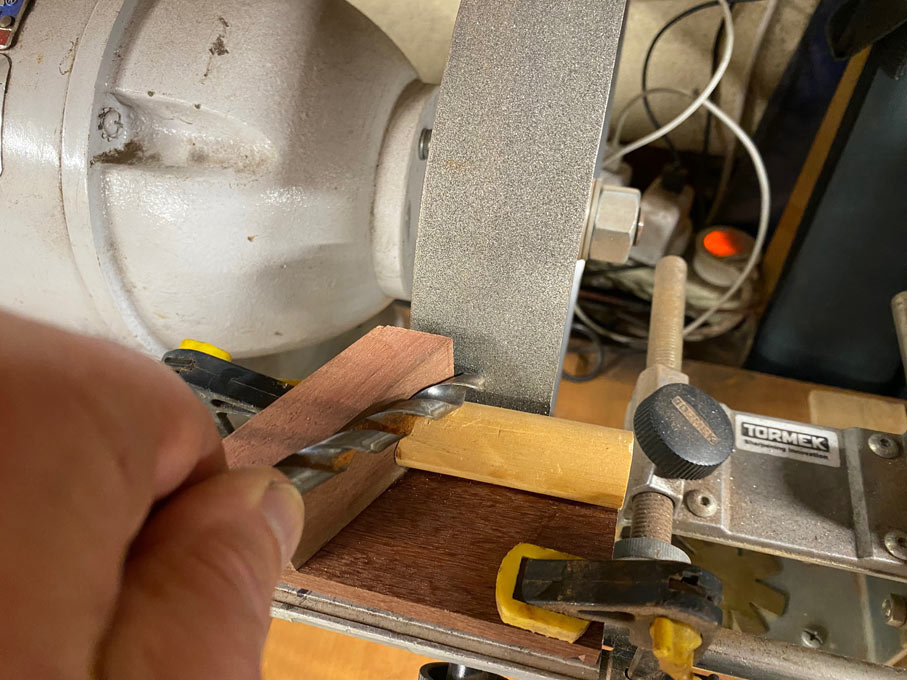
The result is like so ...
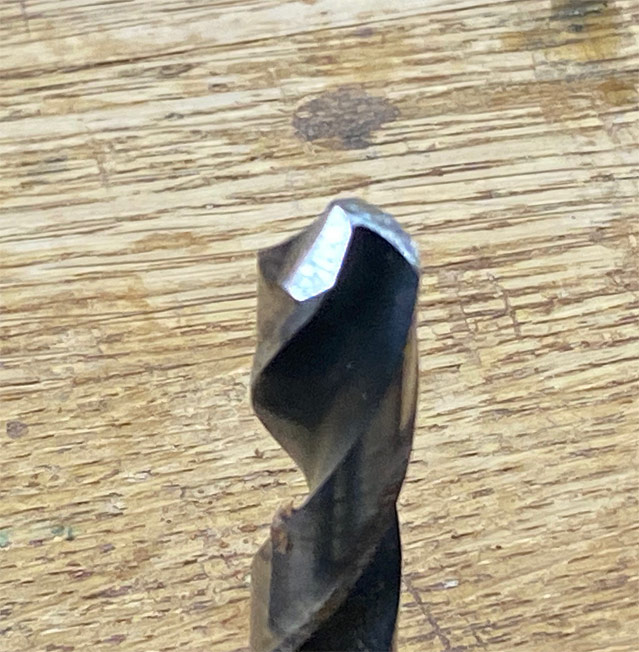
Proof of the pudding ...
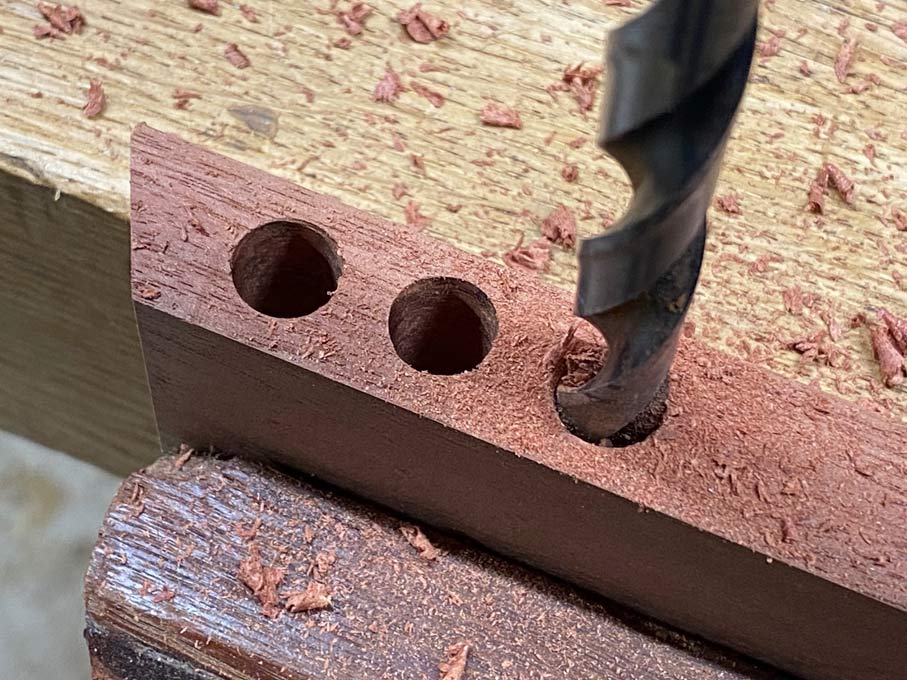
Regards from Perth
Derek