RogerS
Established Member
Thursday
I was planning to work on the riser readying it for finishing but discovered that the veneer had lifted up slightly and buckled right at the far end and so that needed fixing but no further work due to glue setting. This is the main niggle of this project...too many dependencies, waiting for stuff to dry plus limited assembly/working space in the workshop.
So decided to make up the two outer edge 'mouldings' (for want of a better word.....nosings ?). Decided not to cooper excessively since I had a reasonably wide piece of oak that I could use to make 60-75% of the nosing in one piece. Then it was just a case marking out the remaining pieces, cutting them on the mitresaw, finessing them with the disc sander, using a 4mm domino at each joint and glueing them all up. I use the template as my guide as I decided to glue them all together and router trim and mould them in one go.
I've also decided to domino/glue the veneered 'transition' marker to these mouldings first and then fix them to the subframe as a unit.
Today - Friday
Fixed the smaller nosing to its template, started running it over the bearing guided cutter and all was going very well until…..
It all happened bloody fast and I still don’t know quite what caused it to happen. Just means a bit more faffing about adding and glueing a new piece (if I have enough oak left). Fortunately I still have all my fingers but I’m going to have to think of a better way of holding this.
I was planning to work on the riser readying it for finishing but discovered that the veneer had lifted up slightly and buckled right at the far end and so that needed fixing but no further work due to glue setting. This is the main niggle of this project...too many dependencies, waiting for stuff to dry plus limited assembly/working space in the workshop.
So decided to make up the two outer edge 'mouldings' (for want of a better word.....nosings ?). Decided not to cooper excessively since I had a reasonably wide piece of oak that I could use to make 60-75% of the nosing in one piece. Then it was just a case marking out the remaining pieces, cutting them on the mitresaw, finessing them with the disc sander, using a 4mm domino at each joint and glueing them all up. I use the template as my guide as I decided to glue them all together and router trim and mould them in one go.
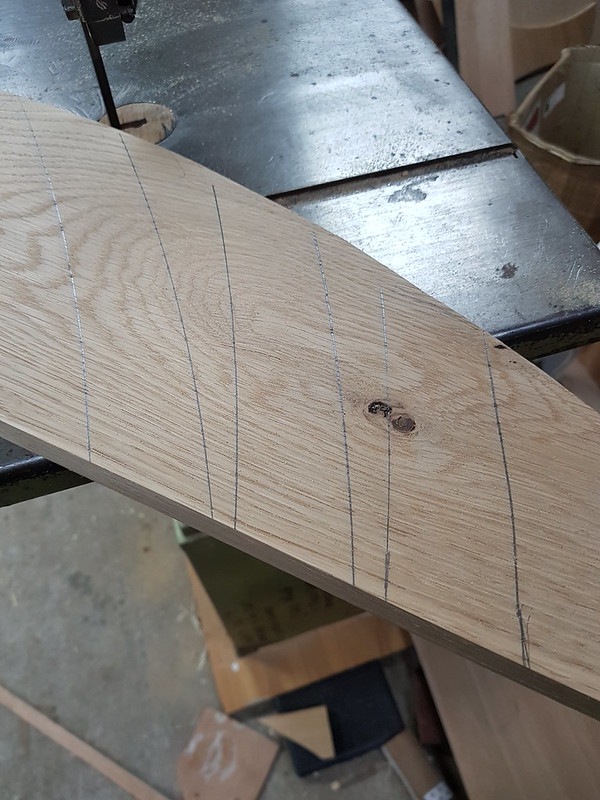
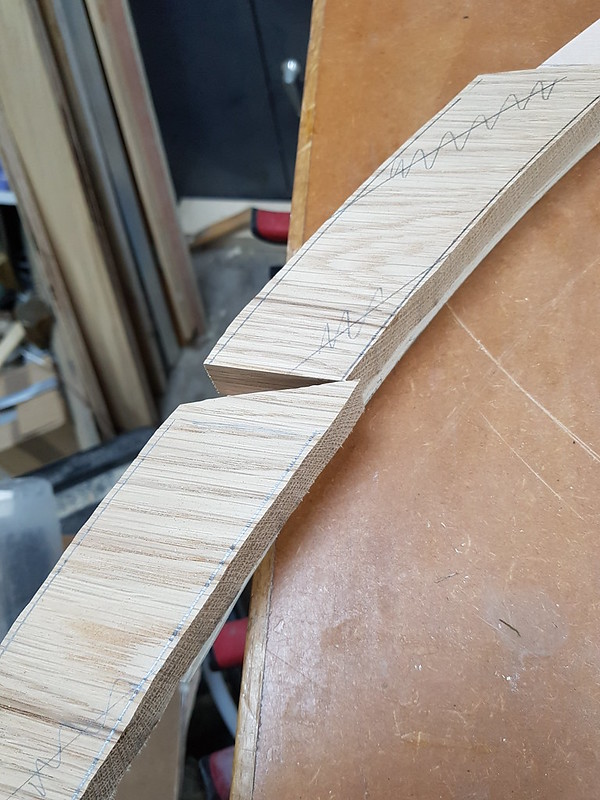
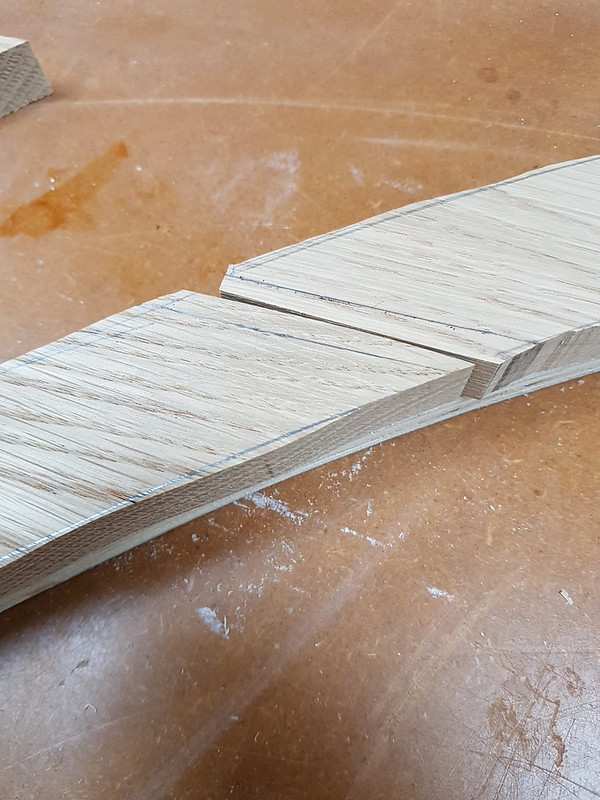
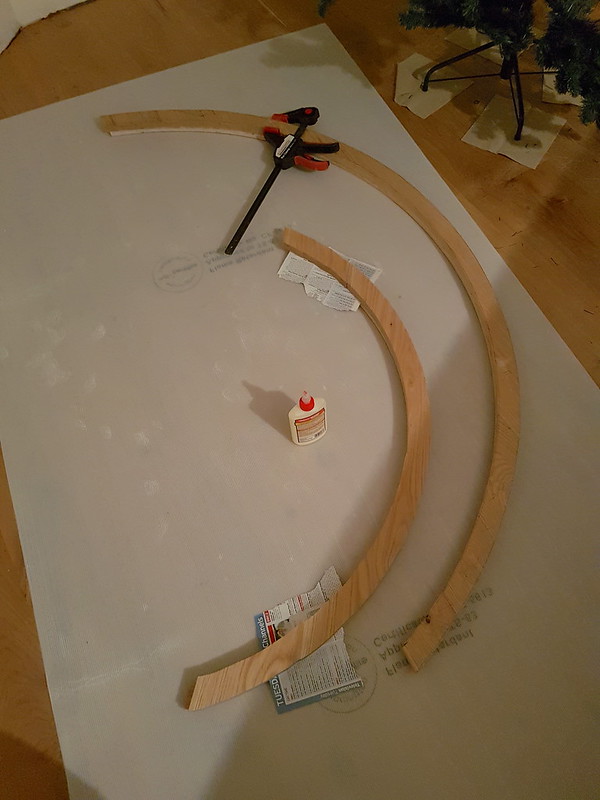
I've also decided to domino/glue the veneered 'transition' marker to these mouldings first and then fix them to the subframe as a unit.
Today - Friday
Fixed the smaller nosing to its template, started running it over the bearing guided cutter and all was going very well until…..
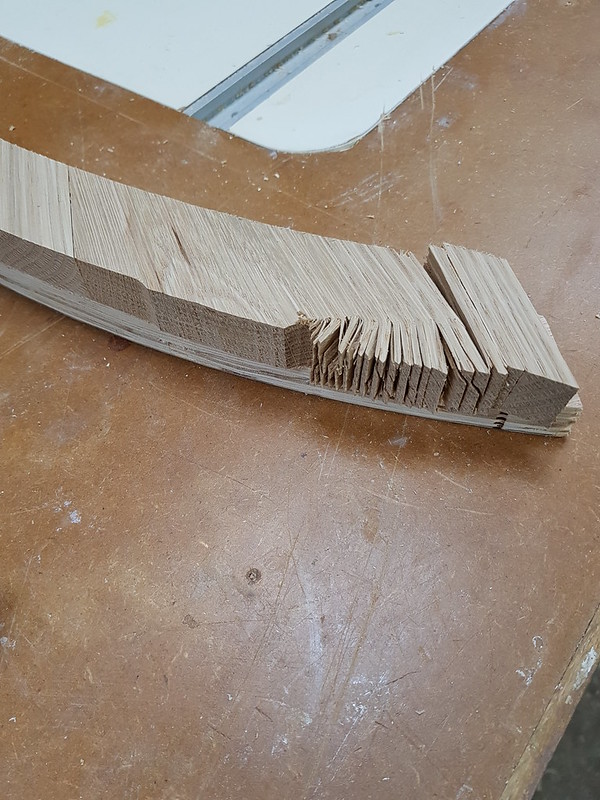
It all happened bloody fast and I still don’t know quite what caused it to happen. Just means a bit more faffing about adding and glueing a new piece (if I have enough oak left). Fortunately I still have all my fingers but I’m going to have to think of a better way of holding this.