You know The Ten Commandments? The one about "thou shalt not covet", or something like that?
Well I have sinned and I did "covet" a Moxon style vice, but at £130 plus for the hardware kit, well to put it lightly it could stay there in the shop :shock:
So not being the type of guy to give up this "coveting" easily I decided a little "back street mechanicing"( thank you Mr Dibnah for that line) was in order :lol:
In this little lot there's the hardware for a Moxon.
I can "find" most things, but a pair of handwheels was a little difficult. So to the bay of plenty and after letting Mr Wong in HK have some of my hard earned, I ended up with a pair of these.
Some M18 stud/all thread was obtained (don't ask about why M18, I like it okay!) ( Okay I'll tell ya', I snapped Mr M16 and lost somewhere ((see loaned out, never returned :evil
) Mr M20 ((( actually I know which dickless POS has it, but that'll just end in tears. For him , no no no, not me [-X ))) and it's quite common in my line of work).
I've seen some various designs of these Moxon things and one thing I wanted to avoid was the normal locking nuts at the rear. I wanted to be able to mount the vice and not have to get down on the floor messing about with a spanner to lengthen the bars.
I couldn't find a bit of brass big enough to turn down and with my mates lathe being somewhat fubar, this was seeming to be a bit of a stumbling block for that idea :roll:
Not beaten yet! A few 5/8 BSW brass nuts and a few 1" brass washers and we're in business.
I bored out the nuts to 15.5mm then tapped a nice new 18mm thread. All good so far.
I quickly "turned/machined" a little shoulder on the nuts so they fitted the internal dia of the washers, this was for location more than anything else. I was pleasantly surprised how easy this was to do. I'd done some hand turning of metals when I was an apprentice, but that was in a proper workshop set up for the task. I now have to sharpen one of my turning chisels, no biggie. This is one of the benefits of coming from an industry where the words "no" or "can't be done" hold no weight, get it done. End of.
Now, "the man who cleans is the man who solders" is what my old instructor used to say and to be honest he's right. I'm not a stranger to soldering, part of my trade you see, so getting these two lovely bits of brass joined in some kind of matrimony was not going to be a problem 8)
Get the metal clean first, then flux immediately to stop any oxidation. Choose a suitable solder, we're going with plumbers metal (type H if you prefer) and away we go.
How am I going to hold this?? #-o
Drill a hole in a scrap block of wood, tap it, then wind in an offcut of stud/all thread. Place washer over and wind on nut, clamp them up tight and now, away we go.
Get it nice and hot, flux during for luck and work the solder into the joint. All done, solid.
Why plumbers metal? Well it's an excellent all round solder, it will go with lead, copper, brass (obviously), steel and bronze. It's fairly easy to work, no crazy heat and its really quite tough. I once saw an 8T substation dragged about 1.5-2 metres by a Hymac, when he'd caught one of my lovely HV cables. The cable was secured to the substation via a brass gland that was sweated to the cable outer sheath, the gland and sheath stayed together like a lovesick couple. I digress, back on point :lol:
Back onto the lathe for a little more "machining" and a quick rub with a file and these are done. Nearly!
Out with the protractor and pillar drill and a few holes were drilled for the securing of said nuts to the rear jaw of soon to be lovely jubbly vice.
Well it appears Mr Wong didn't send me two of his best handwheels. The centre bore was decidedly not concentric, not to the hub or the rim :roll: . This will not do Mr Wong!! But sending them back considering what I paid was out of the question, they needed some enlargement anyway.
A tip I learned, if you have to bore out somehting that's predrilled, you can use an end mill to try and start again. Trouble with that, is down here in the land of n0legs there's no end mills in the armoury, but we do have some rubbish router bits. They're carbide, right!!
Well, chuck up the handwheel and chuck up a dovetail bit (I have no idea why I settled on this one, I really don't. It just seemed right). This is one of those bits from one of those cutter sets that are like £10 for 40 bits. You know they're going to be cr4p, they are cr4p, but they're so cheap you think "why not?". This is one of the last ones from that set, so no big loss if it goes **** up.
Well it worked, or worked well if you like! Slowly advancing the bit into the cast iron, (and let's remember this is some of China's finest cast), along with a good dose of oil now and again, a hole more concentric than earlier is the result. Not bad, even if I say so myself
These need boring out to the required 15.5mm ready for tapping to the oh so lush M18 I crave.
Well with that little adventure under our belt we're at this point
The two "retained" brass nuts will be held on the inside face of the rear jaw with some CSK stainless M5 screws. It might seem like a faff but it's definitely the way I want to go.
I got a pair of oilite bushes, in the correct size, to insert in the front jaw of the vice for the handwheels to run up against when clamping. I think they'll work well and look quite nice.
I suppose I'd better go get some wood sorted now.
Hope you're enjoying it so far
Well I have sinned and I did "covet" a Moxon style vice, but at £130 plus for the hardware kit, well to put it lightly it could stay there in the shop :shock:
So not being the type of guy to give up this "coveting" easily I decided a little "back street mechanicing"( thank you Mr Dibnah for that line) was in order :lol:
In this little lot there's the hardware for a Moxon.
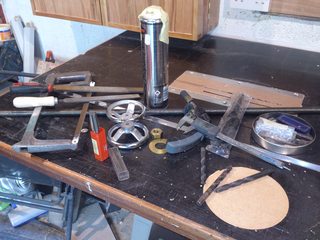
I can "find" most things, but a pair of handwheels was a little difficult. So to the bay of plenty and after letting Mr Wong in HK have some of my hard earned, I ended up with a pair of these.
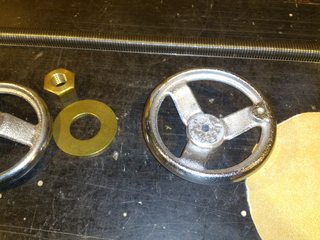
Some M18 stud/all thread was obtained (don't ask about why M18, I like it okay!) ( Okay I'll tell ya', I snapped Mr M16 and lost somewhere ((see loaned out, never returned :evil
I've seen some various designs of these Moxon things and one thing I wanted to avoid was the normal locking nuts at the rear. I wanted to be able to mount the vice and not have to get down on the floor messing about with a spanner to lengthen the bars.
I couldn't find a bit of brass big enough to turn down and with my mates lathe being somewhat fubar, this was seeming to be a bit of a stumbling block for that idea :roll:
Not beaten yet! A few 5/8 BSW brass nuts and a few 1" brass washers and we're in business.
I bored out the nuts to 15.5mm then tapped a nice new 18mm thread. All good so far.
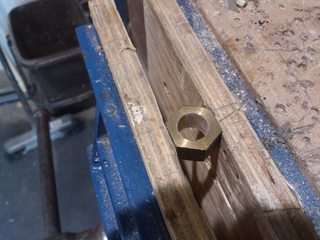
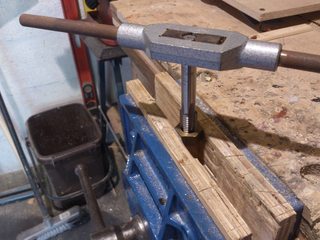
I quickly "turned/machined" a little shoulder on the nuts so they fitted the internal dia of the washers, this was for location more than anything else. I was pleasantly surprised how easy this was to do. I'd done some hand turning of metals when I was an apprentice, but that was in a proper workshop set up for the task. I now have to sharpen one of my turning chisels, no biggie. This is one of the benefits of coming from an industry where the words "no" or "can't be done" hold no weight, get it done. End of.
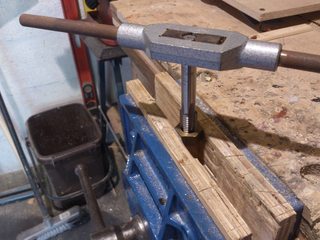
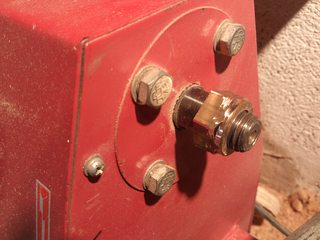
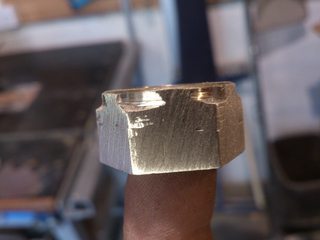
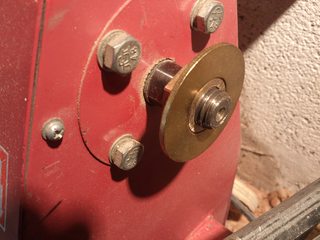
Now, "the man who cleans is the man who solders" is what my old instructor used to say and to be honest he's right. I'm not a stranger to soldering, part of my trade you see, so getting these two lovely bits of brass joined in some kind of matrimony was not going to be a problem 8)
Get the metal clean first, then flux immediately to stop any oxidation. Choose a suitable solder, we're going with plumbers metal (type H if you prefer) and away we go.
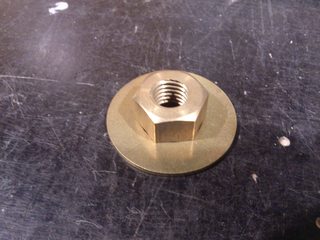
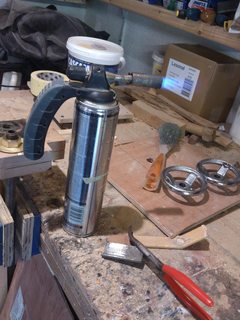
How am I going to hold this?? #-o
Drill a hole in a scrap block of wood, tap it, then wind in an offcut of stud/all thread. Place washer over and wind on nut, clamp them up tight and now, away we go.
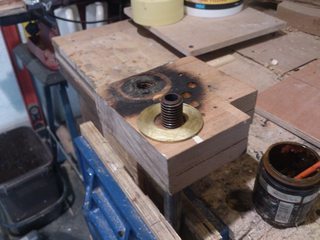
Get it nice and hot, flux during for luck and work the solder into the joint. All done, solid.
Why plumbers metal? Well it's an excellent all round solder, it will go with lead, copper, brass (obviously), steel and bronze. It's fairly easy to work, no crazy heat and its really quite tough. I once saw an 8T substation dragged about 1.5-2 metres by a Hymac, when he'd caught one of my lovely HV cables. The cable was secured to the substation via a brass gland that was sweated to the cable outer sheath, the gland and sheath stayed together like a lovesick couple. I digress, back on point :lol:
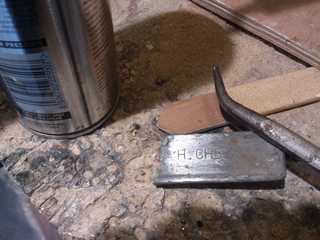
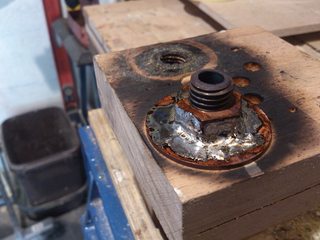
Back onto the lathe for a little more "machining" and a quick rub with a file and these are done. Nearly!
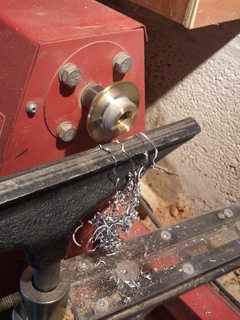
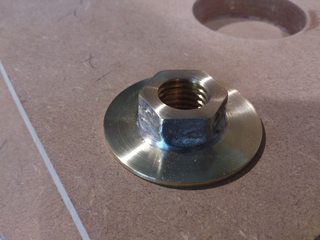
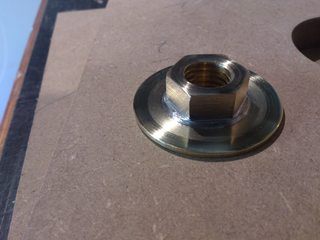
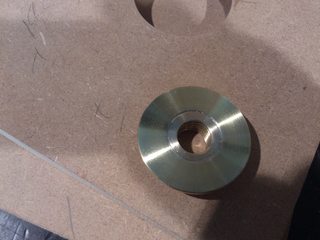
Out with the protractor and pillar drill and a few holes were drilled for the securing of said nuts to the rear jaw of soon to be lovely jubbly vice.
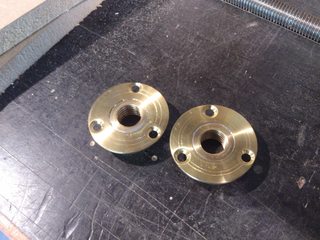
Well it appears Mr Wong didn't send me two of his best handwheels. The centre bore was decidedly not concentric, not to the hub or the rim :roll: . This will not do Mr Wong!! But sending them back considering what I paid was out of the question, they needed some enlargement anyway.
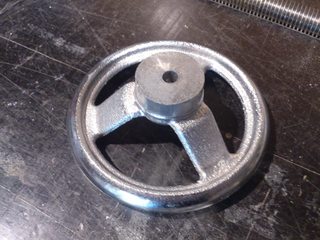
A tip I learned, if you have to bore out somehting that's predrilled, you can use an end mill to try and start again. Trouble with that, is down here in the land of n0legs there's no end mills in the armoury, but we do have some rubbish router bits. They're carbide, right!!
Well, chuck up the handwheel and chuck up a dovetail bit (I have no idea why I settled on this one, I really don't. It just seemed right). This is one of those bits from one of those cutter sets that are like £10 for 40 bits. You know they're going to be cr4p, they are cr4p, but they're so cheap you think "why not?". This is one of the last ones from that set, so no big loss if it goes **** up.
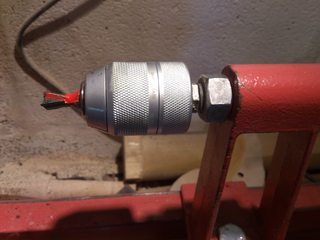
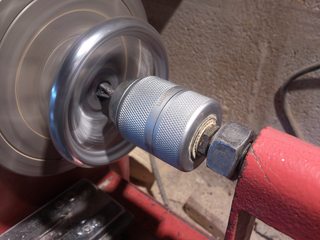
Well it worked, or worked well if you like! Slowly advancing the bit into the cast iron, (and let's remember this is some of China's finest cast), along with a good dose of oil now and again, a hole more concentric than earlier is the result. Not bad, even if I say so myself
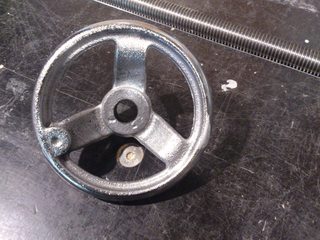
These need boring out to the required 15.5mm ready for tapping to the oh so lush M18 I crave.
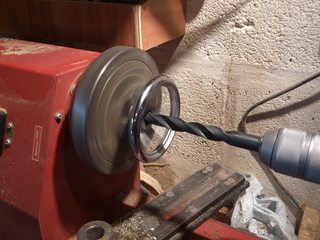
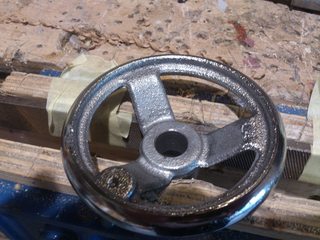
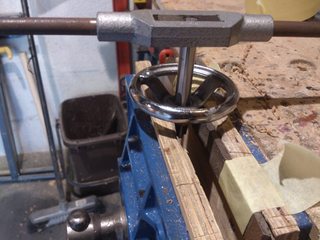
Well with that little adventure under our belt we're at this point
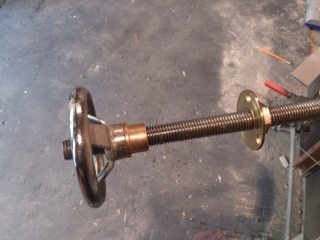
The two "retained" brass nuts will be held on the inside face of the rear jaw with some CSK stainless M5 screws. It might seem like a faff but it's definitely the way I want to go.
I got a pair of oilite bushes, in the correct size, to insert in the front jaw of the vice for the handwheels to run up against when clamping. I think they'll work well and look quite nice.
I suppose I'd better go get some wood sorted now.
Hope you're enjoying it so far