cmwatt
Established Member
Hi folks,
This is my first real attempt at wood working since school days (I'm 25 now), I always enjoyed it at school but never really pursued it as a hobby until now. I thought I'd start off with something small in case I make a mess of it, so it wont be at too much expense! I bought some Elm a couple of months back from a local supplier of hardwood and started working on it a couple of weeks ago now. I've just been doing an hour here and there when I can, with my limited tool selection and have been learning a lot and made a few small mistakes but nothing irrecoverable I think.
Here's progress so far:
_MG_5412 by Craig Watt, on Flickr
Nothing it glued together yet, so I can replace bits if needs be. You can probably notice the top has slightly warped since cutting it. I took the wood into the house for about a week before working with it, should I have left it longer? Is there any way to sort it now, or will I just need to cut a new top? :-k
_MG_5419 by Craig Watt, on Flickr
My bandsaw isn't big enought to cut the box after assembly so I had to cut each side individually. That was a nerve racking moment! :shock: Thankfully they all even out pretty level with each other!
_MG_5420 by Craig Watt, on Flickr
This just shows how the bottom is slotted into the sides. Should I glue this in, or just leave it dry fitted to allow for movement?
_MG_5418 by Craig Watt, on Flickr
A detail photo of some of my first go's at doing dovetails in hardwood! Some have minor gaps, which I plan to fill with either sawdust or tiny slithers of elm.
_MG_5417 by Craig Watt, on Flickr
Finally this was a mistake I made when routing the rebate for the top to sit into! Always make sure your work is firmly clamped down! #-o
Think I need to invest in more clamps/different types!
Anyway, still lots to do yet. Need to fit the Neat hinges I got from Ian and a nice wee mortice lock! Might be tricky as I don't have a router table or drill press yet, but I hope to get either/both soon. I also plan to do a small inlay on the top to a daisy design which I am using from a photo. I got some sections of veneer which I intend to use for that. Then I plan to make an internal tray and that sits on ledges all the way around and line it with velvet or something. That's about it for now. If anyone's got suggestions/recommendations, I'd be glad to hear them!
This is my first real attempt at wood working since school days (I'm 25 now), I always enjoyed it at school but never really pursued it as a hobby until now. I thought I'd start off with something small in case I make a mess of it, so it wont be at too much expense! I bought some Elm a couple of months back from a local supplier of hardwood and started working on it a couple of weeks ago now. I've just been doing an hour here and there when I can, with my limited tool selection and have been learning a lot and made a few small mistakes but nothing irrecoverable I think.
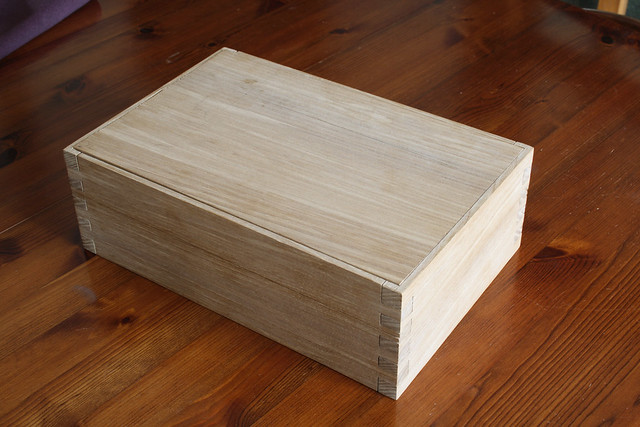
_MG_5412 by Craig Watt, on Flickr
Nothing it glued together yet, so I can replace bits if needs be. You can probably notice the top has slightly warped since cutting it. I took the wood into the house for about a week before working with it, should I have left it longer? Is there any way to sort it now, or will I just need to cut a new top? :-k
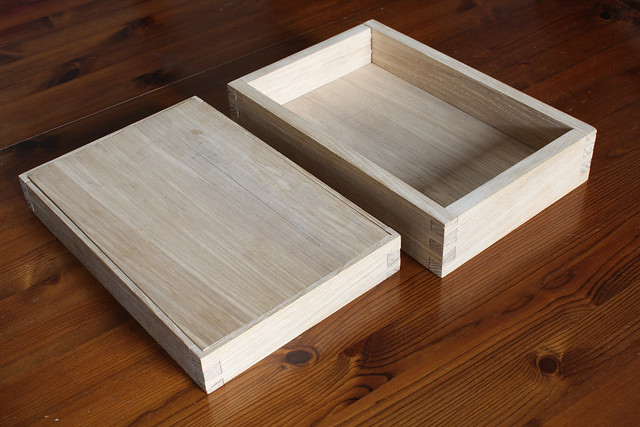
_MG_5419 by Craig Watt, on Flickr
My bandsaw isn't big enought to cut the box after assembly so I had to cut each side individually. That was a nerve racking moment! :shock: Thankfully they all even out pretty level with each other!
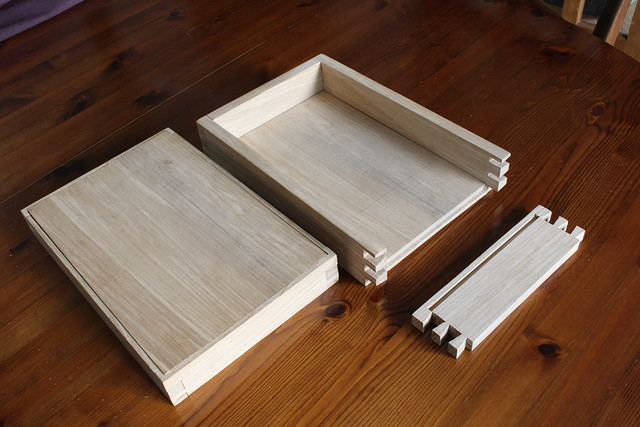
_MG_5420 by Craig Watt, on Flickr
This just shows how the bottom is slotted into the sides. Should I glue this in, or just leave it dry fitted to allow for movement?
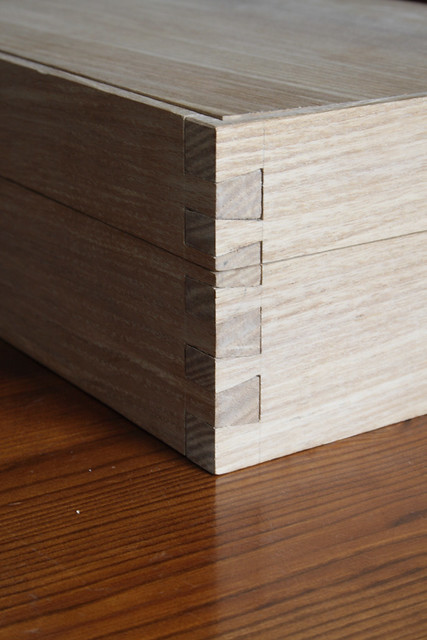
_MG_5418 by Craig Watt, on Flickr
A detail photo of some of my first go's at doing dovetails in hardwood! Some have minor gaps, which I plan to fill with either sawdust or tiny slithers of elm.
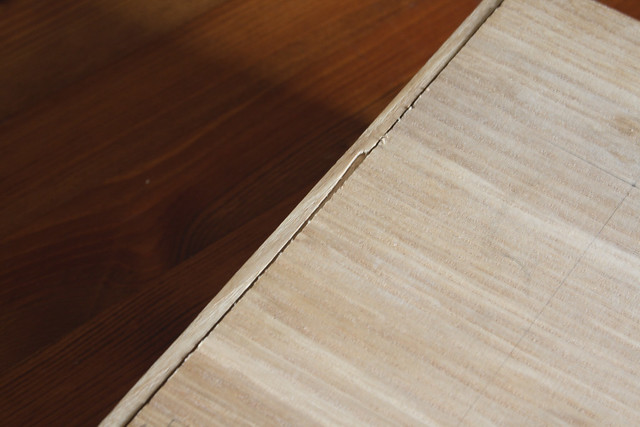
_MG_5417 by Craig Watt, on Flickr
Finally this was a mistake I made when routing the rebate for the top to sit into! Always make sure your work is firmly clamped down! #-o
Anyway, still lots to do yet. Need to fit the Neat hinges I got from Ian and a nice wee mortice lock! Might be tricky as I don't have a router table or drill press yet, but I hope to get either/both soon. I also plan to do a small inlay on the top to a daisy design which I am using from a photo. I got some sections of veneer which I intend to use for that. Then I plan to make an internal tray and that sits on ledges all the way around and line it with velvet or something. That's about it for now. If anyone's got suggestions/recommendations, I'd be glad to hear them!