OPJ
Established Member
Hi all,
I mentioned this briefly in another thread this week but, I think this would be the better place for any discussion.
You may recall that, last year, I built a Mobile Mitre Saw Station, following a set of plans from Popular Woodworking (sorry, I can't find the link).
While the tables on either side offer generous support, It's a real bother having to roll the saw forwards and then clear a space beside just to swing them up when you don't have much space - especially when I'm part-way through tenonning on the router table (which is one of the things I'd have to move!) and I just want to quickly cut a few rails to length.
I don't think cutting the tables down to length is the right answer - it'd be a waste of materials and I may decided to sell this one day, if I decide I do need a table saw instead (longer tables would have more appeal).
So, I'm looking for ideas on an alternative, more convenient means of supporting timber.
Looking closely in the last issue of British Woodworking [new one's due out next week :wink:], I notice that Steve Maskery (who else?! :roll:
) has fitted a longer fence to one side and appears to use a roller stand for support. Although I was about to sell my two roller stands as I never use them, this idea actually has a lot of appeal to me. In particular, the long fence idea. This would be good for cutting repeat lengths against a stop, as I generally don't work with anything longer than 1200mm.
During the initial stages of working with wood, when I bring a load of sawn timber in to the 'shop, I don't mind swinging the table then. It's only when I'm part-way through a build with other machines/tools already set up.
So, with Steve's approach in mind, does any one have an alternative suggestion? LeeJ recently made a 'station' with drawer-slide supports. I quite like this but, I would be better off building a new unit instead of trying to retro-fit them to my current one.
While others frown upon the use of these saws in the home workshop, I know there are those of you out there who do own and use them - what is your solution?
Your thoughts would be appreciated.
Thanks for looking,
Olly.
I mentioned this briefly in another thread this week but, I think this would be the better place for any discussion.
You may recall that, last year, I built a Mobile Mitre Saw Station, following a set of plans from Popular Woodworking (sorry, I can't find the link).
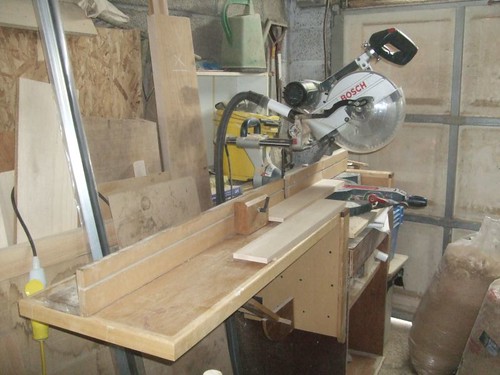
While the tables on either side offer generous support, It's a real bother having to roll the saw forwards and then clear a space beside just to swing them up when you don't have much space - especially when I'm part-way through tenonning on the router table (which is one of the things I'd have to move!) and I just want to quickly cut a few rails to length.
I don't think cutting the tables down to length is the right answer - it'd be a waste of materials and I may decided to sell this one day, if I decide I do need a table saw instead (longer tables would have more appeal).
So, I'm looking for ideas on an alternative, more convenient means of supporting timber.
Looking closely in the last issue of British Woodworking [new one's due out next week :wink:], I notice that Steve Maskery (who else?! :roll:
During the initial stages of working with wood, when I bring a load of sawn timber in to the 'shop, I don't mind swinging the table then. It's only when I'm part-way through a build with other machines/tools already set up.
So, with Steve's approach in mind, does any one have an alternative suggestion? LeeJ recently made a 'station' with drawer-slide supports. I quite like this but, I would be better off building a new unit instead of trying to retro-fit them to my current one.
While others frown upon the use of these saws in the home workshop, I know there are those of you out there who do own and use them - what is your solution?
Your thoughts would be appreciated.
Thanks for looking,
Olly.