Nigel Taylor
Established Member
The valve is actually rather large compared to the cylinder and crosshead guide. This is the smallest valve I've found to date:
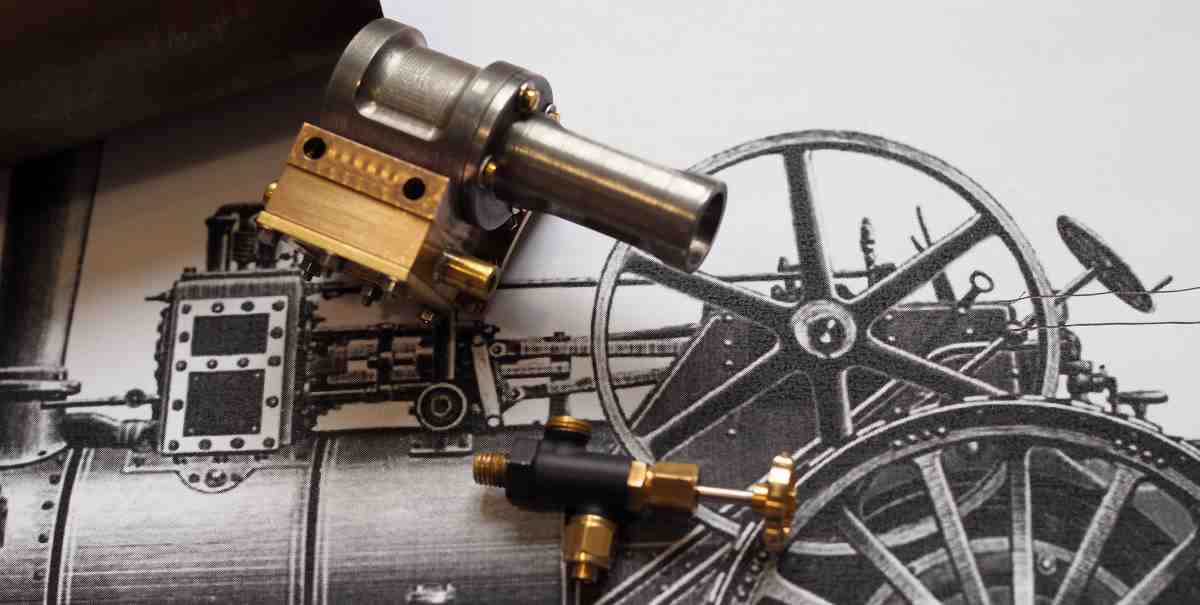
Thanks for the kind words, sometimes I have to make a part 3 times to get it right. So, lots of patience.How did I miss this build. fantastic workmanship. went through this thred & can't wait to see the end product
I used to work as a boiler man ( stoker ) when I was young and fit, we would go to all the potteries
in stoke on trent when they shut down their boilers for cleaning.
It was a dirty wet job, your lungs got full of soot when you went under the boiler to clean out the flues that lead
up to the tall chimney stacks,I will not go into cleaning the stacks, no health & safty back then..lol
Sometimes the soot and ash was still hot, it was so fine it was like shoveling feathers and the guy in the front had to
keep up with you as you shoveld it forward.
The boilers pipes get all fury and calculus/limescale forming on the tubes so you would have to get in and set to scaling them
with a pneumatic air needle gun, took hours to get done & we would work late in the evening as the companys
only shut down for two weeks.
I went with some guy to change the pipes in a massive boiler at a cole mine it was a nerve racking job knocking out the tubes,
the tool was a steel tube with a locator welded on the end, we all took turns holding it with both hands on the end of the pipe while the other
guy hit it with a sledge hammer to force the tube into the boiler, then we had to do it all over again the other end.
Putting the pipes in is easy, you set them in then you expand the pipe to the boiler plate.
We had just got back to the yard after a job cleaning covered in soot & fred dibnah walks past all he said was "how do, ya been at it then lads".
He wanted a quote for a fire box..
Sorry to go on but I do not miss old boiler but I like all the models craftsman like you reproduce.
Most of the old boilers had a coat of asbestos as an insulator there was guys who would come in after
us and do repairs to the coating they did not have any protective gear, so you can see where I am coming from
when I say old boilers where dirty polluters...lol
Hi, yes, he taught me metal and wood working from a young age. We made lots of radio control models as well as tools and some mad stuff. The rivets look interesting. if you email me [email protected] I will send you my address. Very kind, thanks, NigelHis work & attention to detail is astonishing, did he teach you how to metal work.?
I had a friend he used to make steam powered cars, his work was outstanding in every detail & like you spend
days getting it righ. No way would you disturb him when he was on a build..lol
His last project was a steam wire stretching winding machine but he passed away before he finished it, he sad it
was for the science & industry museum in manchester.
Any way I was given a box of brass nuts, bolts, screws and washers. I was having a rummage through & came across
these think they are some sort of brass rivets. If you have any use for them I will send them to you.
Not really a compromise, more concerned about the level of detailed machining that has gone into the saddle. Hence always nervous of next steps such as machining a working steam valve face into it. Plus then finally silver soldering it to the boiler shell.Good luck @Nigel Where's the compromise?
And that attention to detail? Quite admirable.amazing skill and patience from start to finish. I look forward to seeing it running. Well done it is certainly an heirloom piece.
Enter your email address to join: