scholar
Established Member
It's a long story, but we have some complicated projection hinges (all to do with the arched window and the annoying stormproof casements which was nothing to do with me btw). Here is one:
The hinges actually work fine, but were not all installed very well (I did design them to solve a problem, but did not fit them). The fit of quite a few of these hinges needs to be adjusted by bringing the casement tighter in to the frame. This might be achieved by adjusting the hanging of the casement on the cranked hinge, but it will be better to avoid messing with those screws as getting new fixings a few mm away will be tricky (and we don't want them falling out!). I think the better solution and allowing for adjustability when refitting, will be to move the whole hinge in towards the frame. The four screw fixings into the wall reveal cannot be easily moved, so I think making the countersunk holes a countersunk slot would be best.
So the question is how best to machine the slot if I do not have a milling machine (which I don't, although would like, but cannot justify going out to buy one for this job). The screws are 5mm/No 10 and I guess the max lengthening of the slot will be say 6mm. The material is 3mm stainless steel. I have:
- a decent set of HSS countersink bits
- whilst I have a pillar drill at home, this will be 200 miles away, so will be limited to my drill press stand with a mains drill
- I don't mind buying a compound vice or some such if the rest of the set up is going to work.
Ideally I would just take the whole lot off to an engineering shop and get it done, but I am going to have to fettle the windows one by one, so practically it has to be done on site.
My current thinking is to try filing the hole into an elongated hole, then machine the countersinking. Obviously, I am concerned about whether the drill and drill press will withstand the lateral force.
Any views on whether this is doomed to failure?
cheers
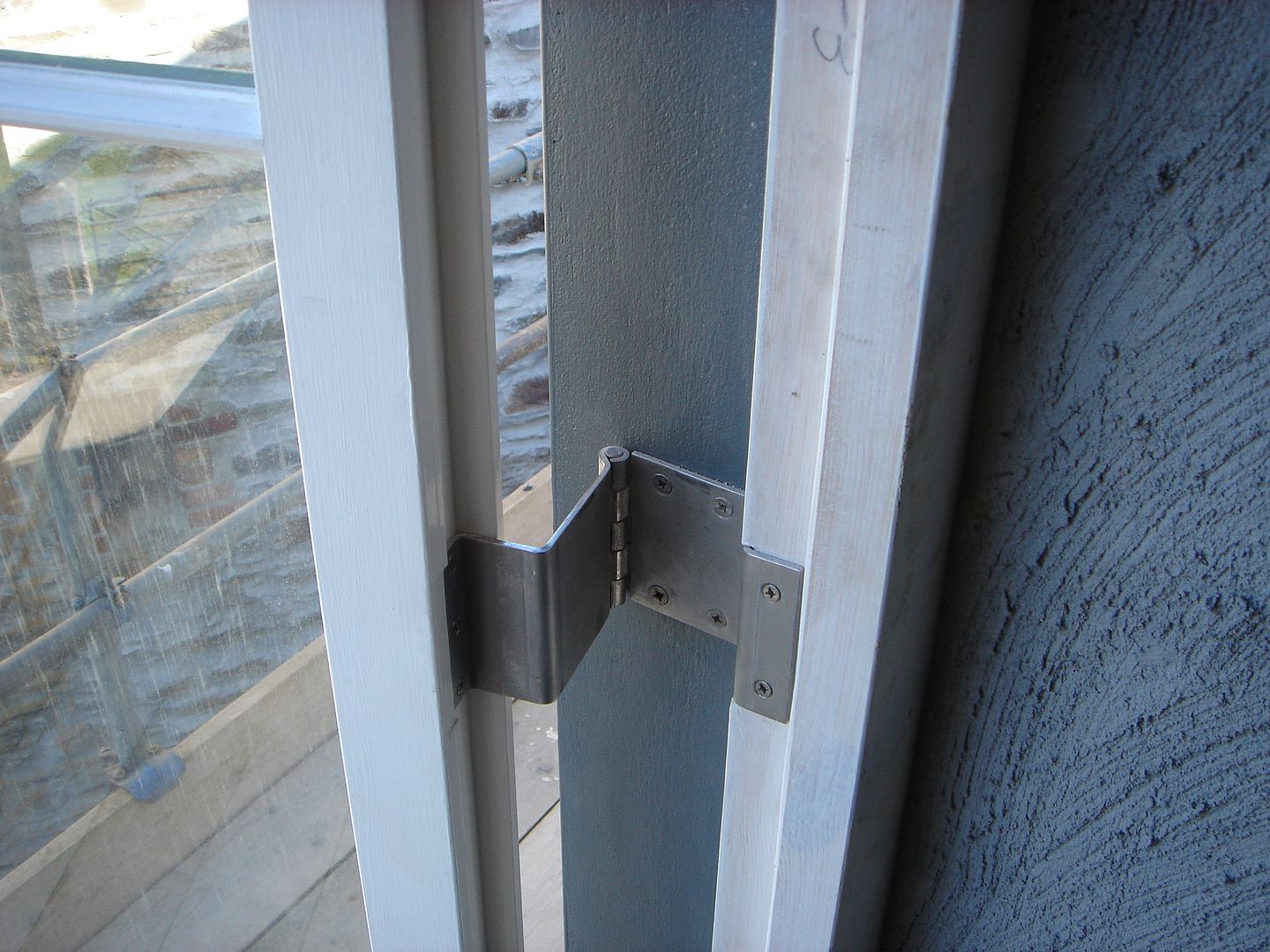
The hinges actually work fine, but were not all installed very well (I did design them to solve a problem, but did not fit them). The fit of quite a few of these hinges needs to be adjusted by bringing the casement tighter in to the frame. This might be achieved by adjusting the hanging of the casement on the cranked hinge, but it will be better to avoid messing with those screws as getting new fixings a few mm away will be tricky (and we don't want them falling out!). I think the better solution and allowing for adjustability when refitting, will be to move the whole hinge in towards the frame. The four screw fixings into the wall reveal cannot be easily moved, so I think making the countersunk holes a countersunk slot would be best.
So the question is how best to machine the slot if I do not have a milling machine (which I don't, although would like, but cannot justify going out to buy one for this job). The screws are 5mm/No 10 and I guess the max lengthening of the slot will be say 6mm. The material is 3mm stainless steel. I have:
- a decent set of HSS countersink bits
- whilst I have a pillar drill at home, this will be 200 miles away, so will be limited to my drill press stand with a mains drill
- I don't mind buying a compound vice or some such if the rest of the set up is going to work.
Ideally I would just take the whole lot off to an engineering shop and get it done, but I am going to have to fettle the windows one by one, so practically it has to be done on site.
My current thinking is to try filing the hole into an elongated hole, then machine the countersinking. Obviously, I am concerned about whether the drill and drill press will withstand the lateral force.
Any views on whether this is doomed to failure?
cheers