I've been doing more metalwork jobs than woodwork as of late, so I thought I'd post some stuff up.
My Hobbies wood lathe has a blind morse taper socket in the spindle, so I can't just bump out the centres from the opposite end. Apparently this is quite common on older lathes. Until now I've been twisting the centres out, but I've never been happy with this. Then when Doris bought her Coronet, I realised this has a centre ejector. It screws onto the spindle nose, and simply pulls out the centre when unscrewed. I thought this was a brilliant idea, so I endeavoured to make one....
I started by making a mandrel threaded the same as the Hobbies spindle nose. This will serve as a gauge for the ejector's internal thread, and also as a way of holding the ejector for machining:
Then I hacksawed off a lump of bar for the ejector. I chucked it, faced off one end, then flipped it over and faced off the opposite end. Then I drilled a 1/2" hole straight through (sorry, no photos).
Next I bored the hole out to the tapping size of my spindle nose (7/8 BSW). This is a blind bore, leaving a "cap" at the end of the ejector. Then I screw cut the internal thread. I cut the thread almost to full depth:
And finished the thread with a tap:
Now the ejector can be screwed onto the mandrel and the two are mounted back in the lathe. A skim cut is taken to clean up the outside:
And then the ejector is knurled:
Finally the knurling is tidied up:
The almost-finished ejector. All that's left to do is to drill a hole for a tommy bar, just in case it gets stuck
My Hobbies wood lathe has a blind morse taper socket in the spindle, so I can't just bump out the centres from the opposite end. Apparently this is quite common on older lathes. Until now I've been twisting the centres out, but I've never been happy with this. Then when Doris bought her Coronet, I realised this has a centre ejector. It screws onto the spindle nose, and simply pulls out the centre when unscrewed. I thought this was a brilliant idea, so I endeavoured to make one....
I started by making a mandrel threaded the same as the Hobbies spindle nose. This will serve as a gauge for the ejector's internal thread, and also as a way of holding the ejector for machining:
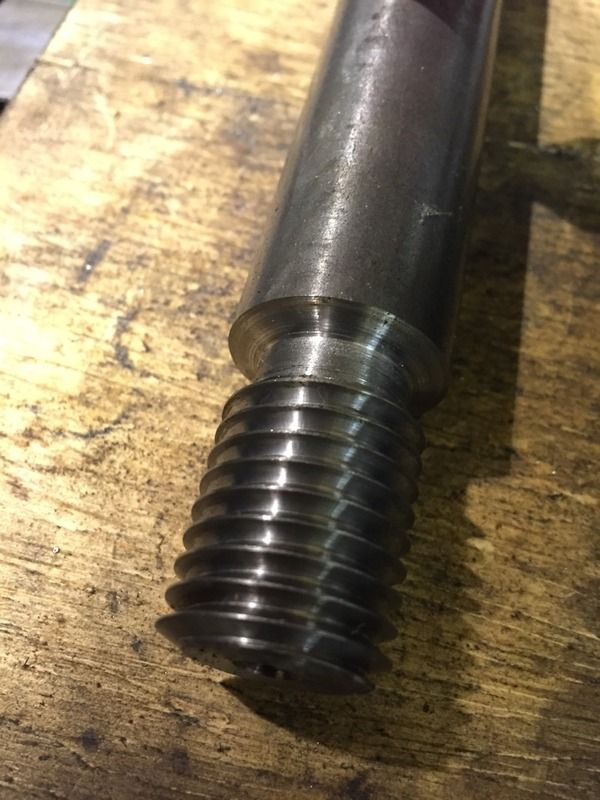
Then I hacksawed off a lump of bar for the ejector. I chucked it, faced off one end, then flipped it over and faced off the opposite end. Then I drilled a 1/2" hole straight through (sorry, no photos).
Next I bored the hole out to the tapping size of my spindle nose (7/8 BSW). This is a blind bore, leaving a "cap" at the end of the ejector. Then I screw cut the internal thread. I cut the thread almost to full depth:
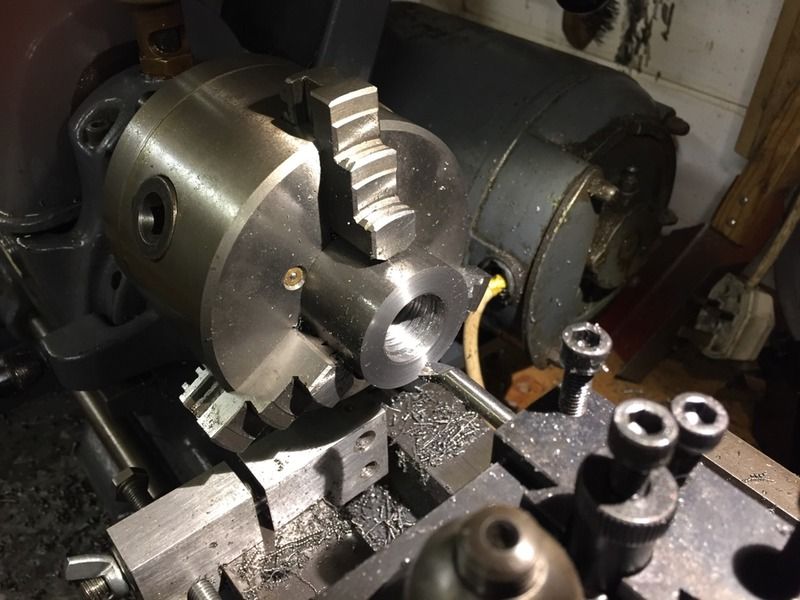
And finished the thread with a tap:
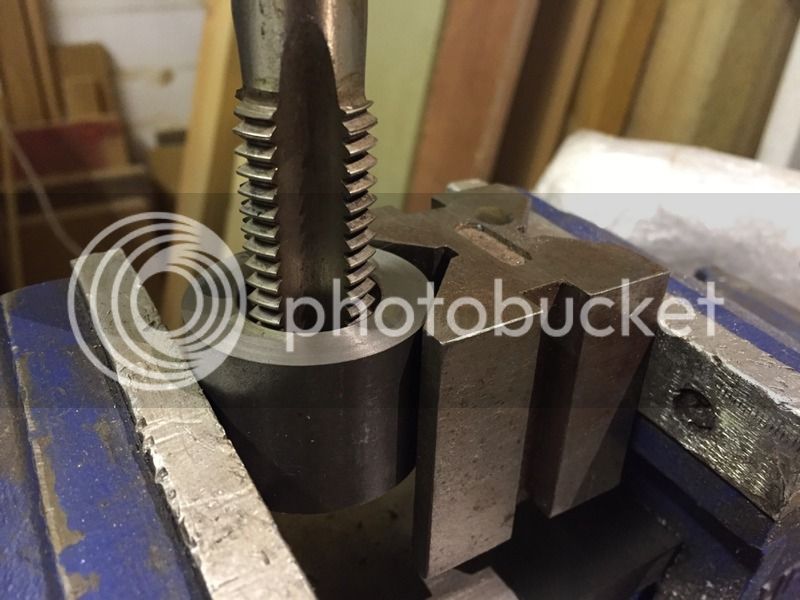
Now the ejector can be screwed onto the mandrel and the two are mounted back in the lathe. A skim cut is taken to clean up the outside:
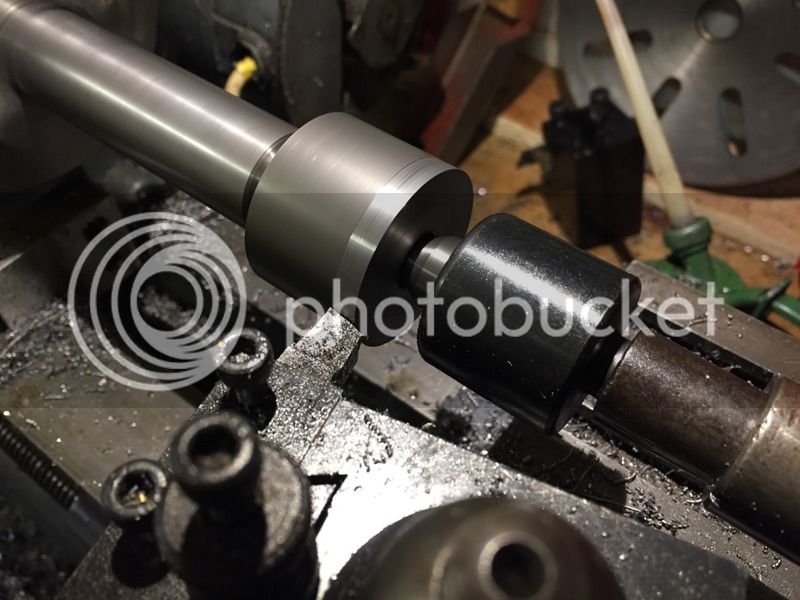
And then the ejector is knurled:
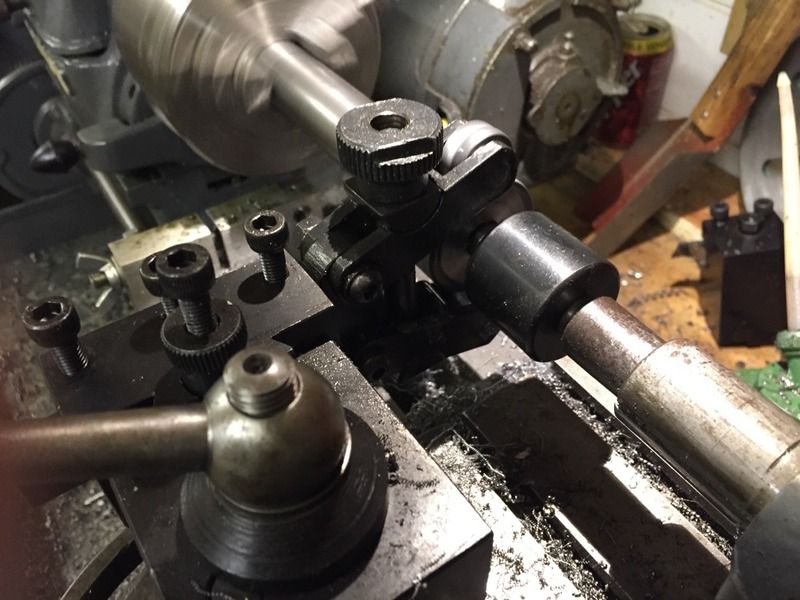
Finally the knurling is tidied up:
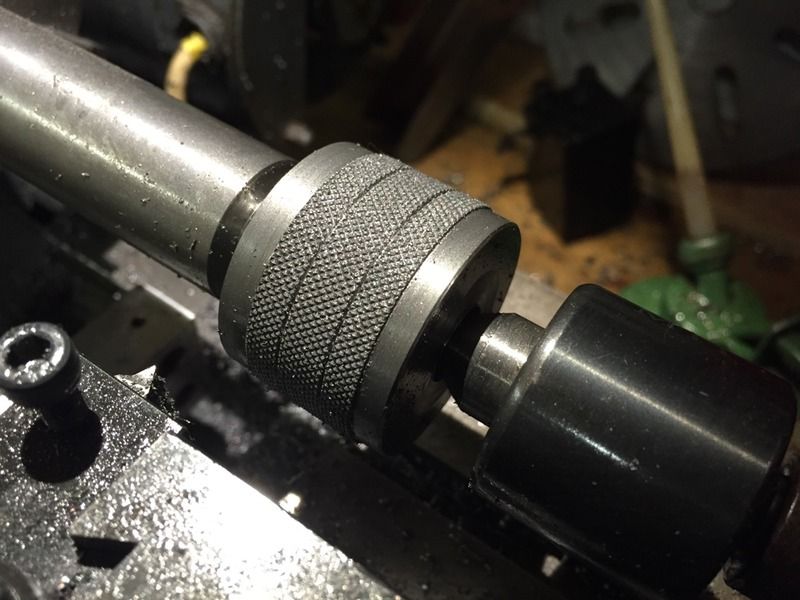
The almost-finished ejector. All that's left to do is to drill a hole for a tommy bar, just in case it gets stuck
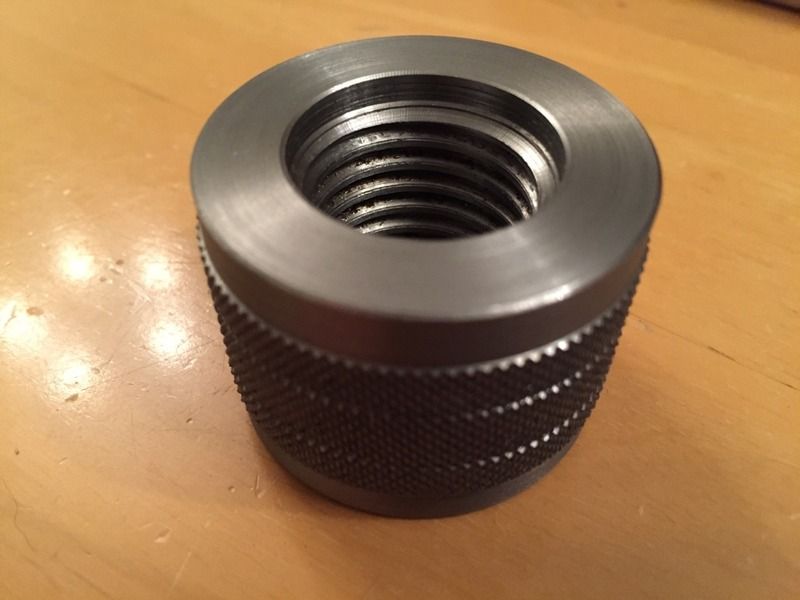