Now to split the bush...
Clamped up against an angle plate as I don't have a suitable vice. The foreshortening of the camera makes this setup look a lot more ropey than it actually is
In order to find the "equator", for want of a better word, I've measured the height with a vernier height gauge:
... then subtracted half the diameter and marked the height. My height gauge only goes down to 1.5" so I had to switch to a surface gauge:
Then I lined up the slitting saw with the mark and had at it.
Finally the split bush, and in place on the banjo. The tool rest post is gripped a lot better now:
Yes, I really should make a new banjo...
Clamped up against an angle plate as I don't have a suitable vice. The foreshortening of the camera makes this setup look a lot more ropey than it actually is
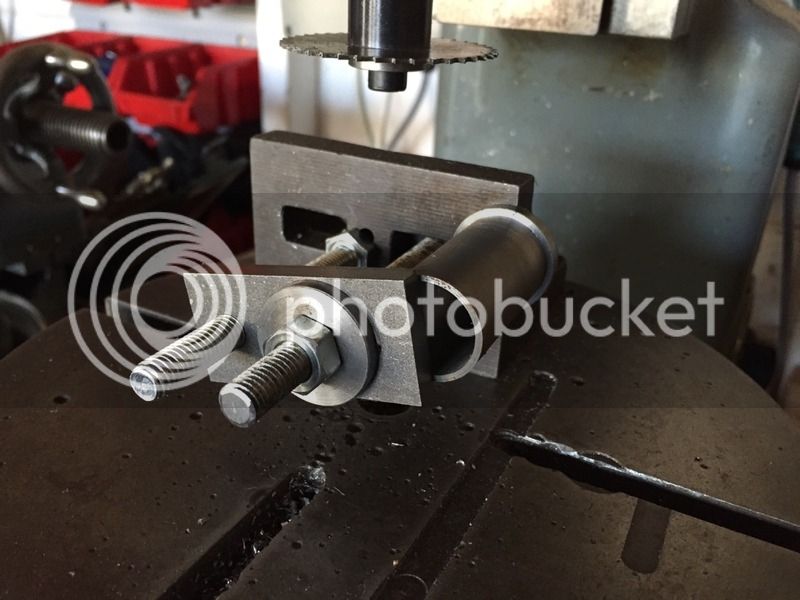
In order to find the "equator", for want of a better word, I've measured the height with a vernier height gauge:
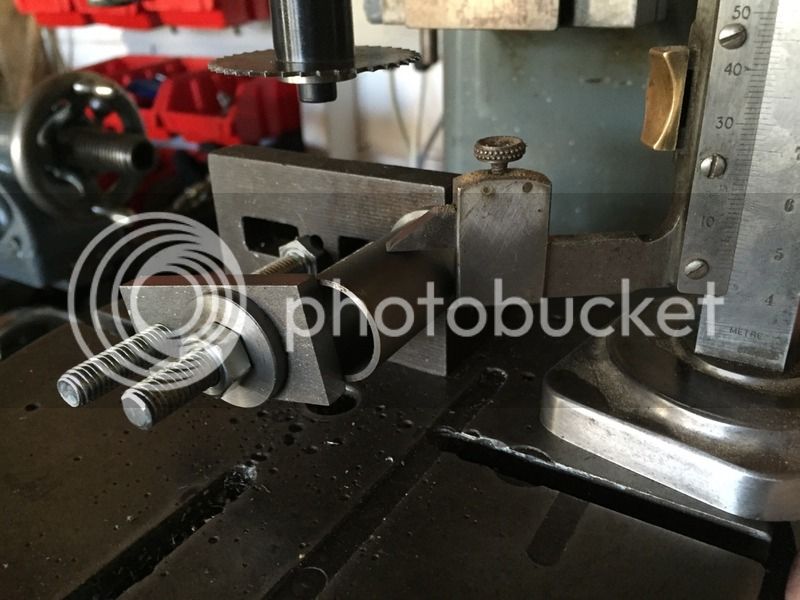
... then subtracted half the diameter and marked the height. My height gauge only goes down to 1.5" so I had to switch to a surface gauge:
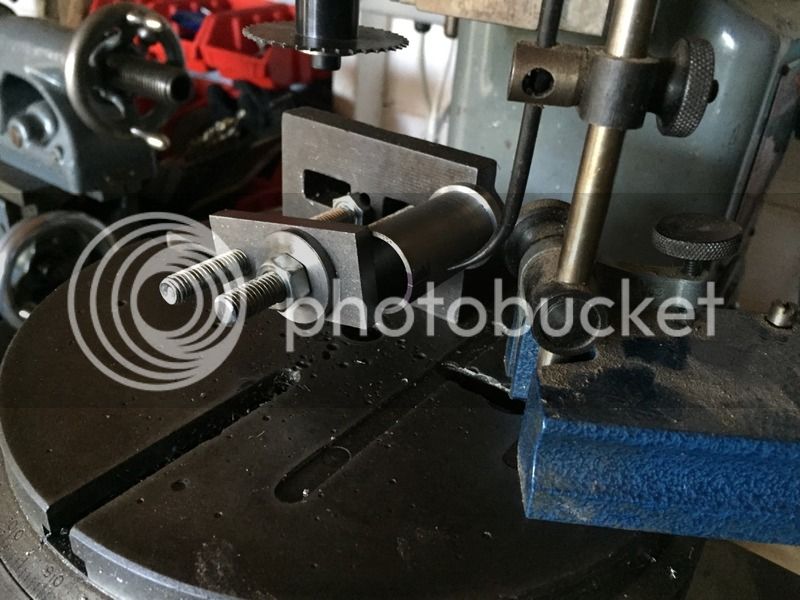
Then I lined up the slitting saw with the mark and had at it.
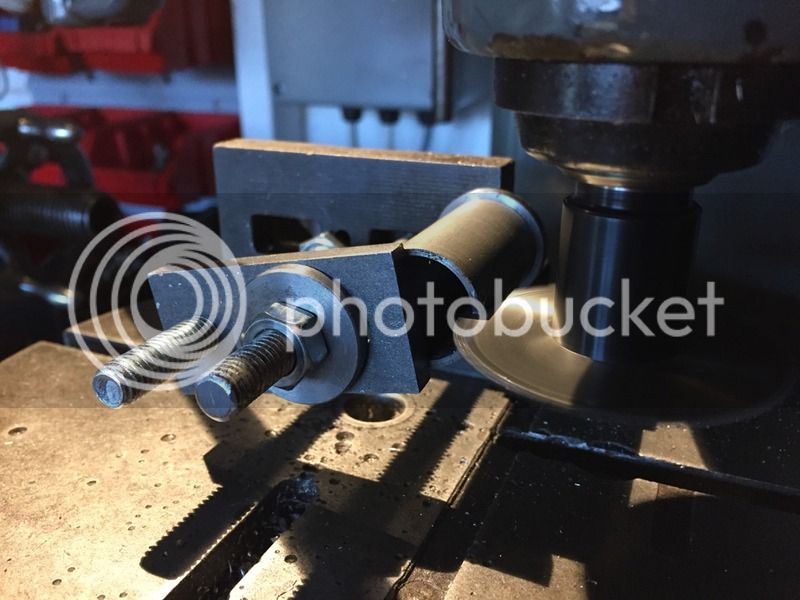
Finally the split bush, and in place on the banjo. The tool rest post is gripped a lot better now:
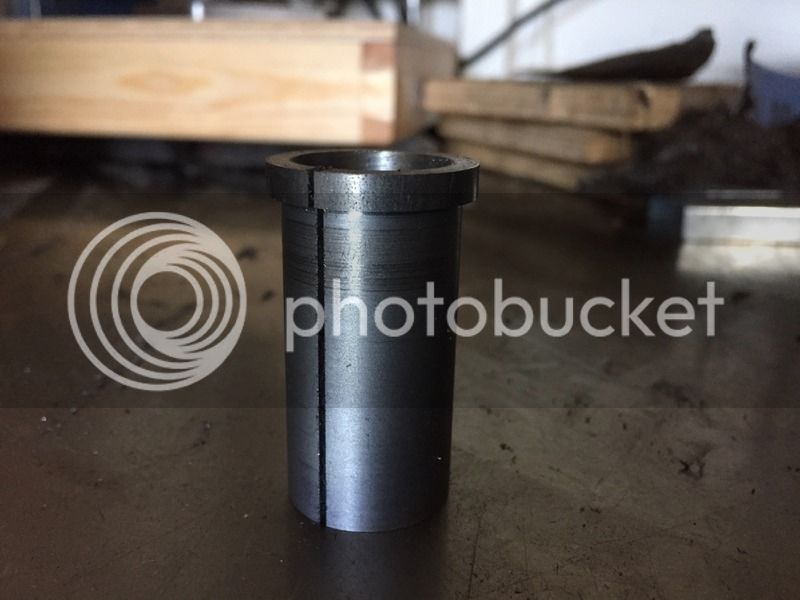
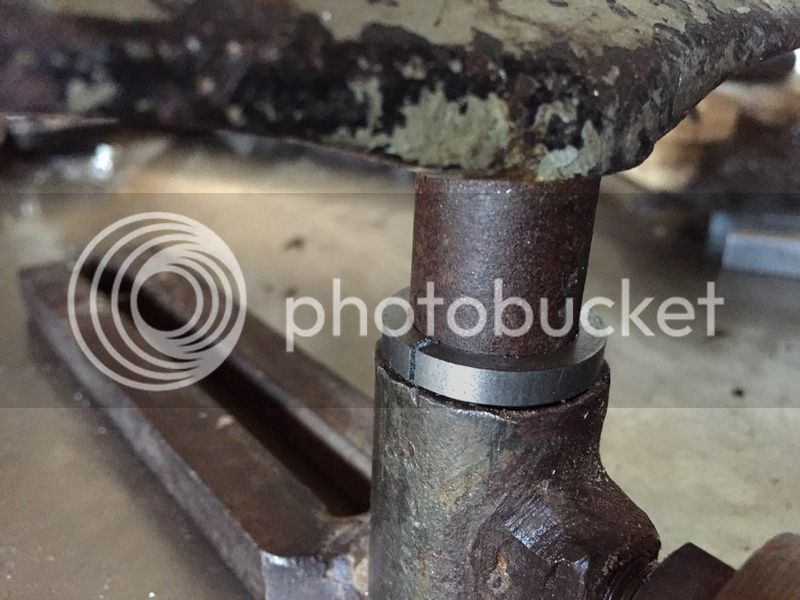
Yes, I really should make a new banjo...