Im wanting to make a small number of boxes, so ive made up a few prototypes.
Below is the first unit i made -
This seems a pretty basic box, however, it seems to be more stable than the following units.
The base was routed out on my cnc machine to recess the sides, hence you see the base from the side. This aids me in gluing too (although ive since made a jig anyhow)
The second unit is, i think, more attractive, but ive got a failed joint -
I made this without the cnc machine. The center is just laminated, and then the ends and base cut from this sheet. I like the way the grain follows round. As i say, i think this is a nicer look than the first unit.
I then made a third. I intended the grain to follow round the sides and across the base, but i assembled the job wrong, so it does not.
I made the base on the cnc machine, and cut the sides to have more complex joints (i dont know the name of any of these!)
But the unit warped, as i left it on a heater, so i did not bother finishing it up. I do not think its a good design at all anyway, as the metal rails that have to be fitted will never work with the grain in this direction.
What im asking from you is basic advice. Im pretty novice with this stuff (i do cnc metal work normally)
Ive worked out for myself that #3 has the grain wrong, but, certainly #1 seems the most stable, but less interesting. #2 is made from thinner material, so i wonder if that is some of my issue? Id like them to be about 12.4mm ish (which #1 is, but #2 is less than 10mm i think)
There will be metal plates screwed on across the rails - so the whole top will be a metal sheet, so the rails will not be able to move relative to one another either.
The size of the opening on the top is 426mm x 128mm
Thank you!
Below is the first unit i made -
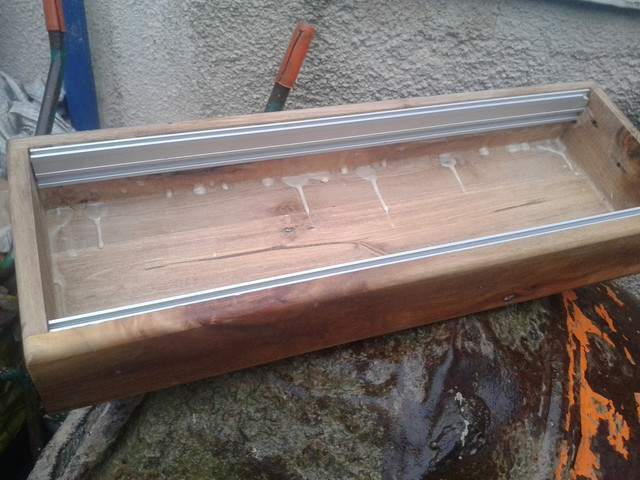
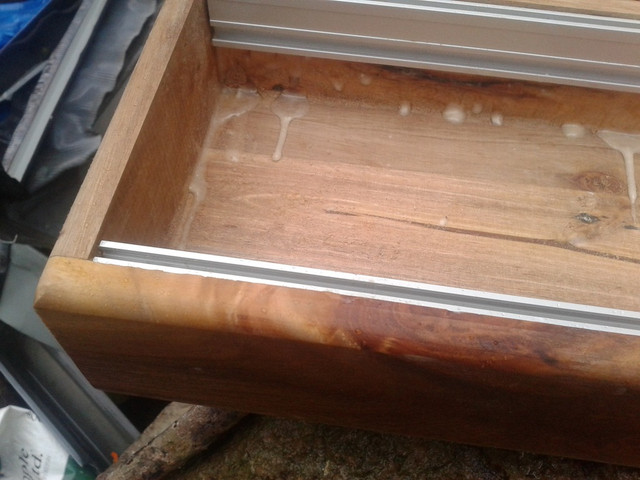
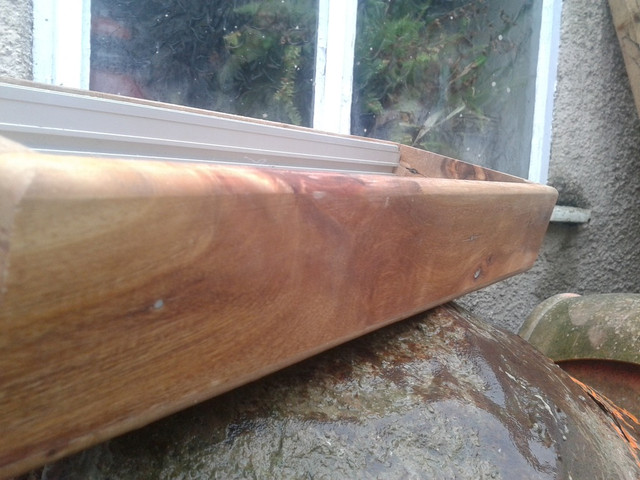
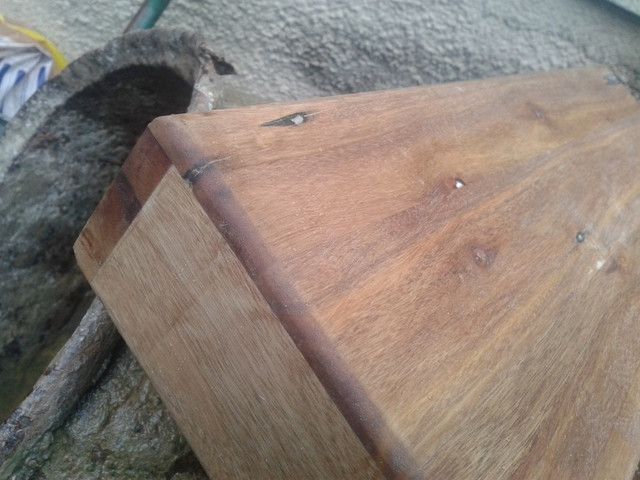
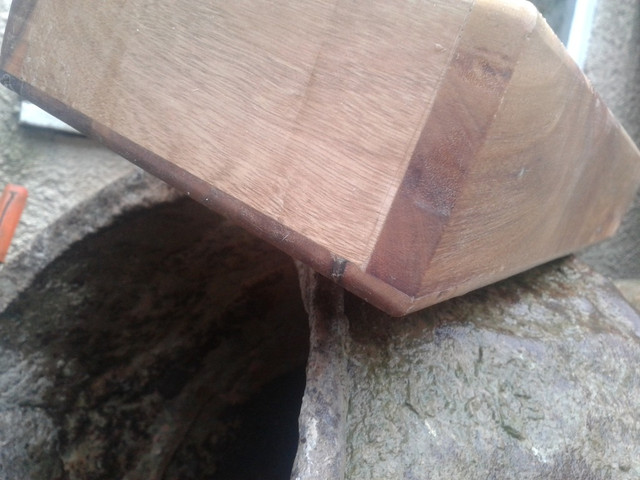
This seems a pretty basic box, however, it seems to be more stable than the following units.
The base was routed out on my cnc machine to recess the sides, hence you see the base from the side. This aids me in gluing too (although ive since made a jig anyhow)
The second unit is, i think, more attractive, but ive got a failed joint -
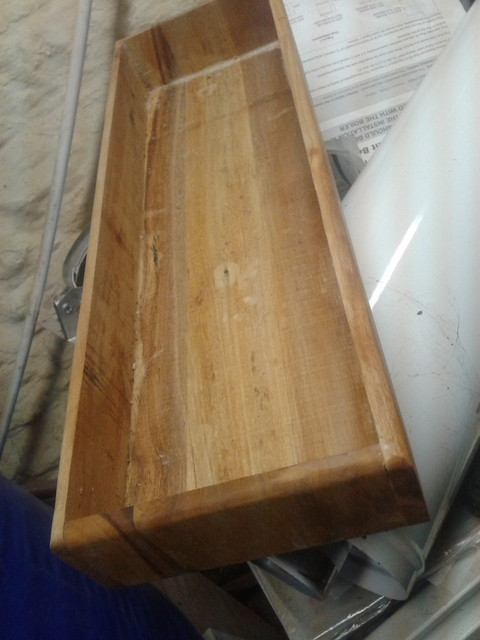
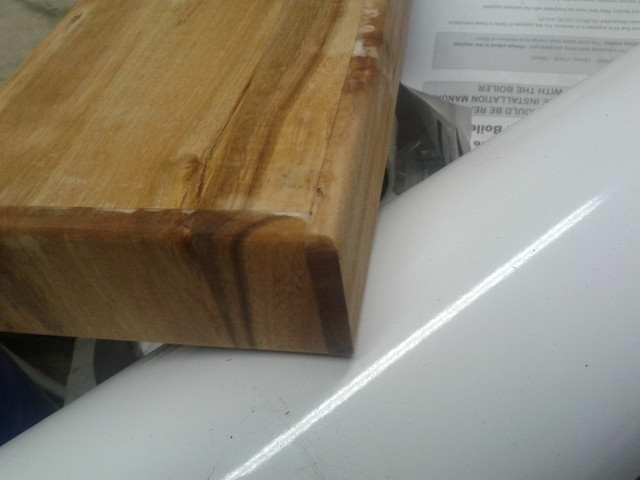
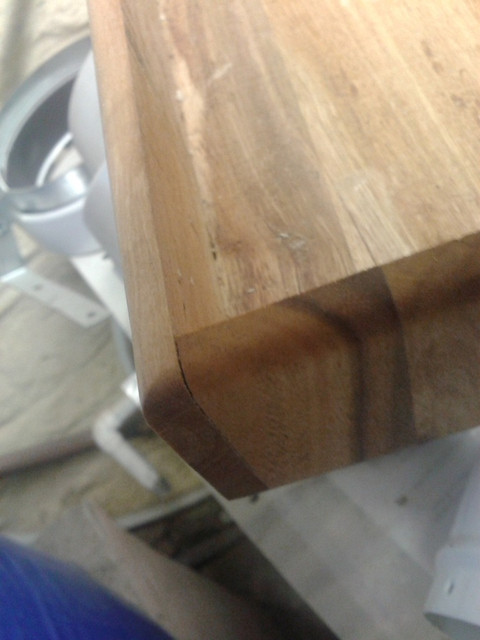
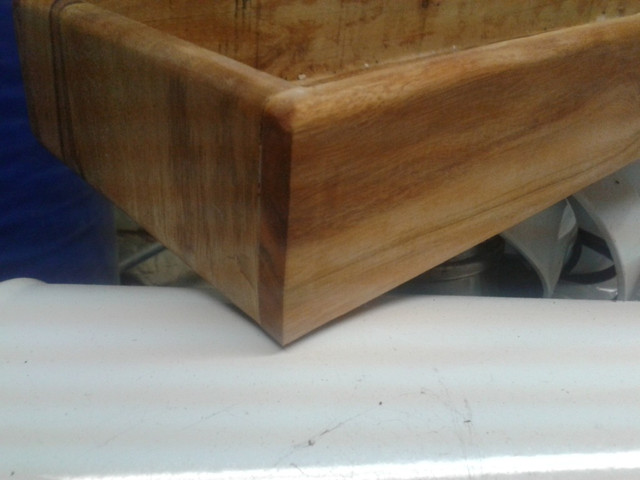
I made this without the cnc machine. The center is just laminated, and then the ends and base cut from this sheet. I like the way the grain follows round. As i say, i think this is a nicer look than the first unit.
I then made a third. I intended the grain to follow round the sides and across the base, but i assembled the job wrong, so it does not.
I made the base on the cnc machine, and cut the sides to have more complex joints (i dont know the name of any of these!)
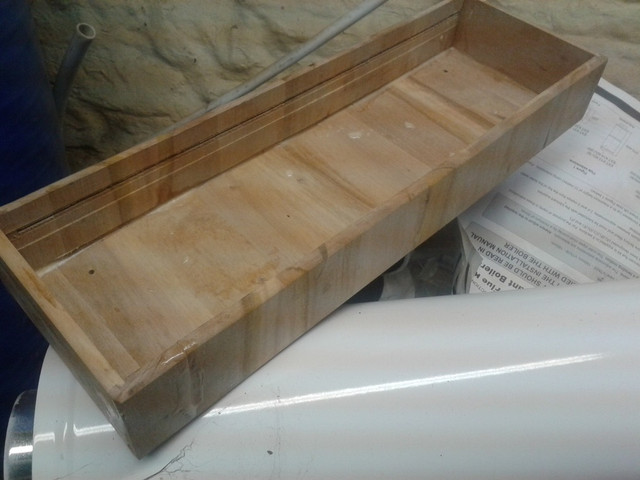
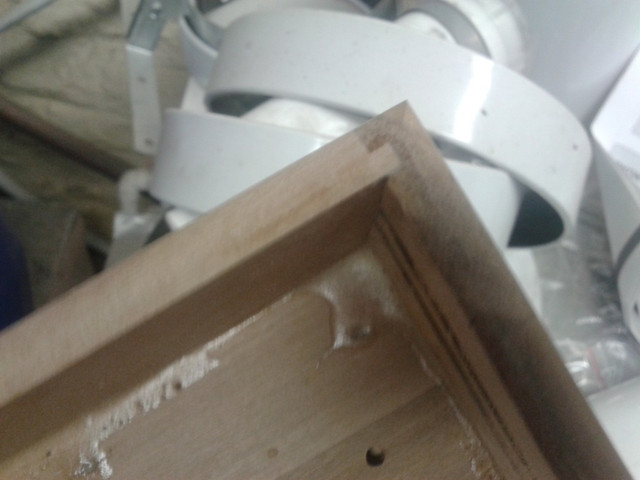
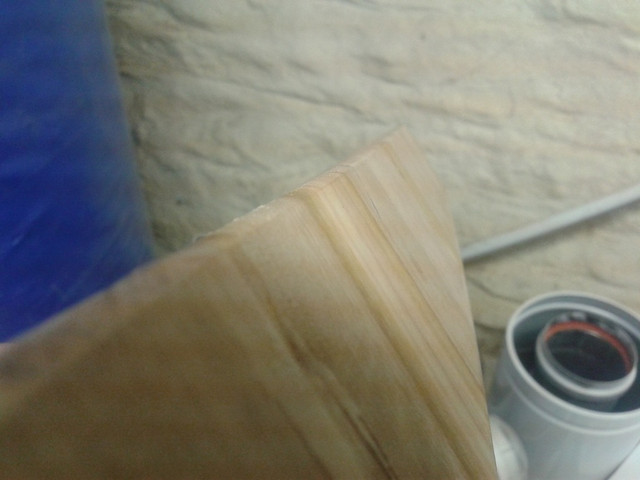
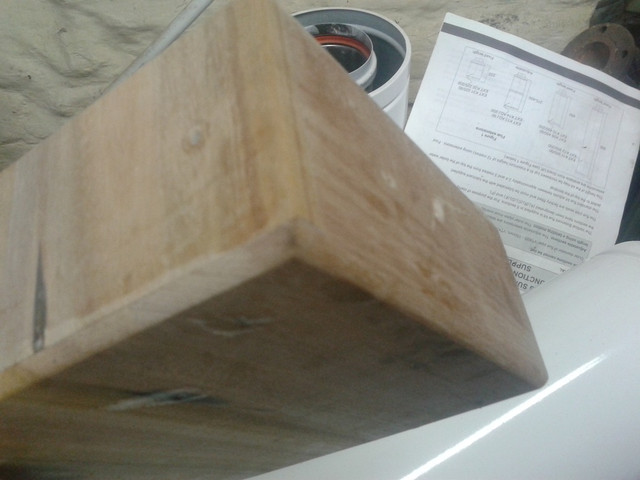
But the unit warped, as i left it on a heater, so i did not bother finishing it up. I do not think its a good design at all anyway, as the metal rails that have to be fitted will never work with the grain in this direction.
What im asking from you is basic advice. Im pretty novice with this stuff (i do cnc metal work normally)
Ive worked out for myself that #3 has the grain wrong, but, certainly #1 seems the most stable, but less interesting. #2 is made from thinner material, so i wonder if that is some of my issue? Id like them to be about 12.4mm ish (which #1 is, but #2 is less than 10mm i think)
There will be metal plates screwed on across the rails - so the whole top will be a metal sheet, so the rails will not be able to move relative to one another either.
The size of the opening on the top is 426mm x 128mm
Thank you!