memzey
Established Member
Hi gang,
I was wondering if anyone here as any pointers on finding the internal star point on a three phase motor? I’ve opened up one that came with something I bought ages ago, hoping I could wire it delta but there is no obvious internal point where the windings come together. Is there a general place I should be looking or any other pointers on how to find it? Photos below:
Only one end of the tails comes out into the junction box outside (415v). All help much appreciated.
I was wondering if anyone here as any pointers on finding the internal star point on a three phase motor? I’ve opened up one that came with something I bought ages ago, hoping I could wire it delta but there is no obvious internal point where the windings come together. Is there a general place I should be looking or any other pointers on how to find it? Photos below:
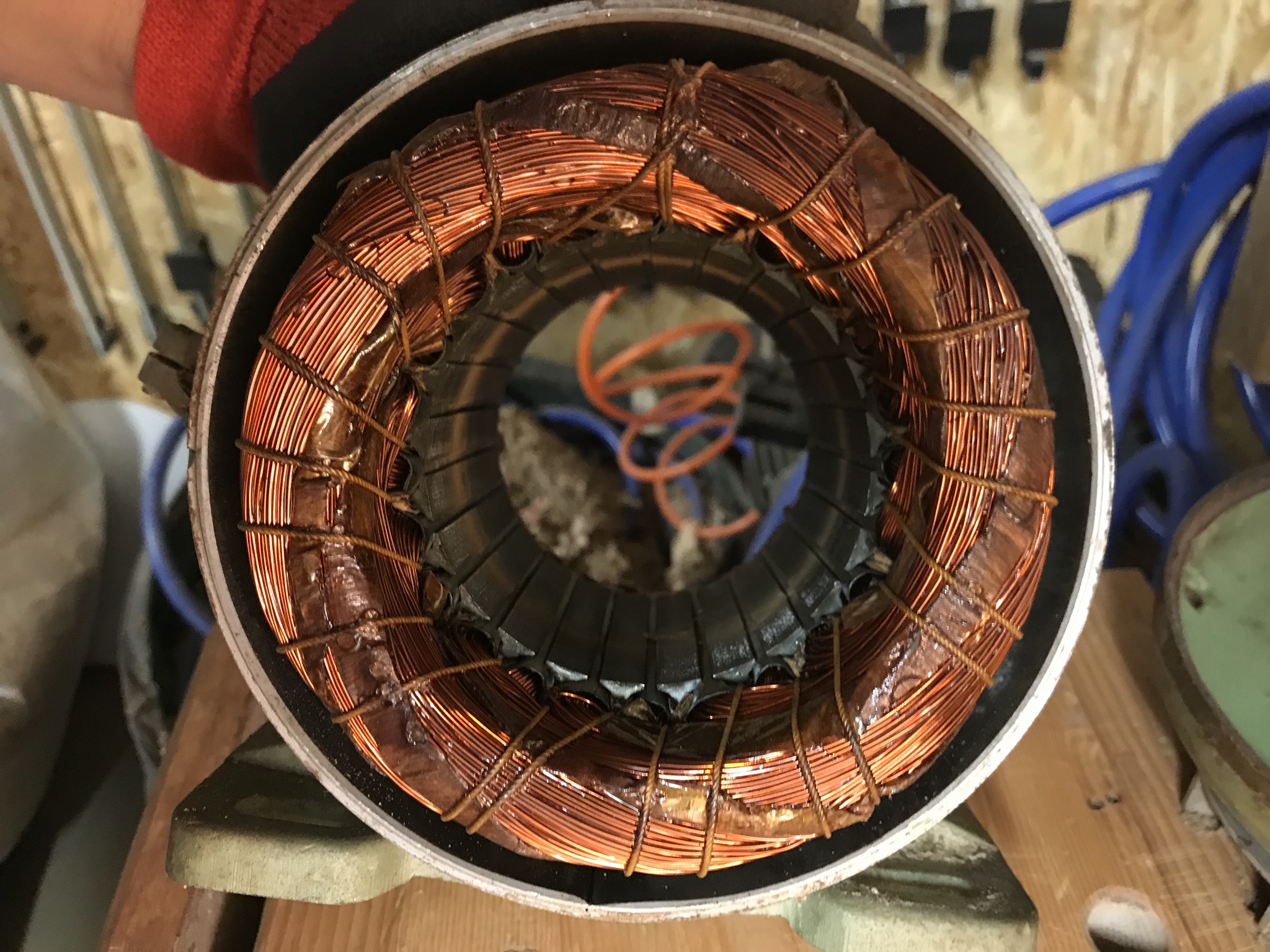
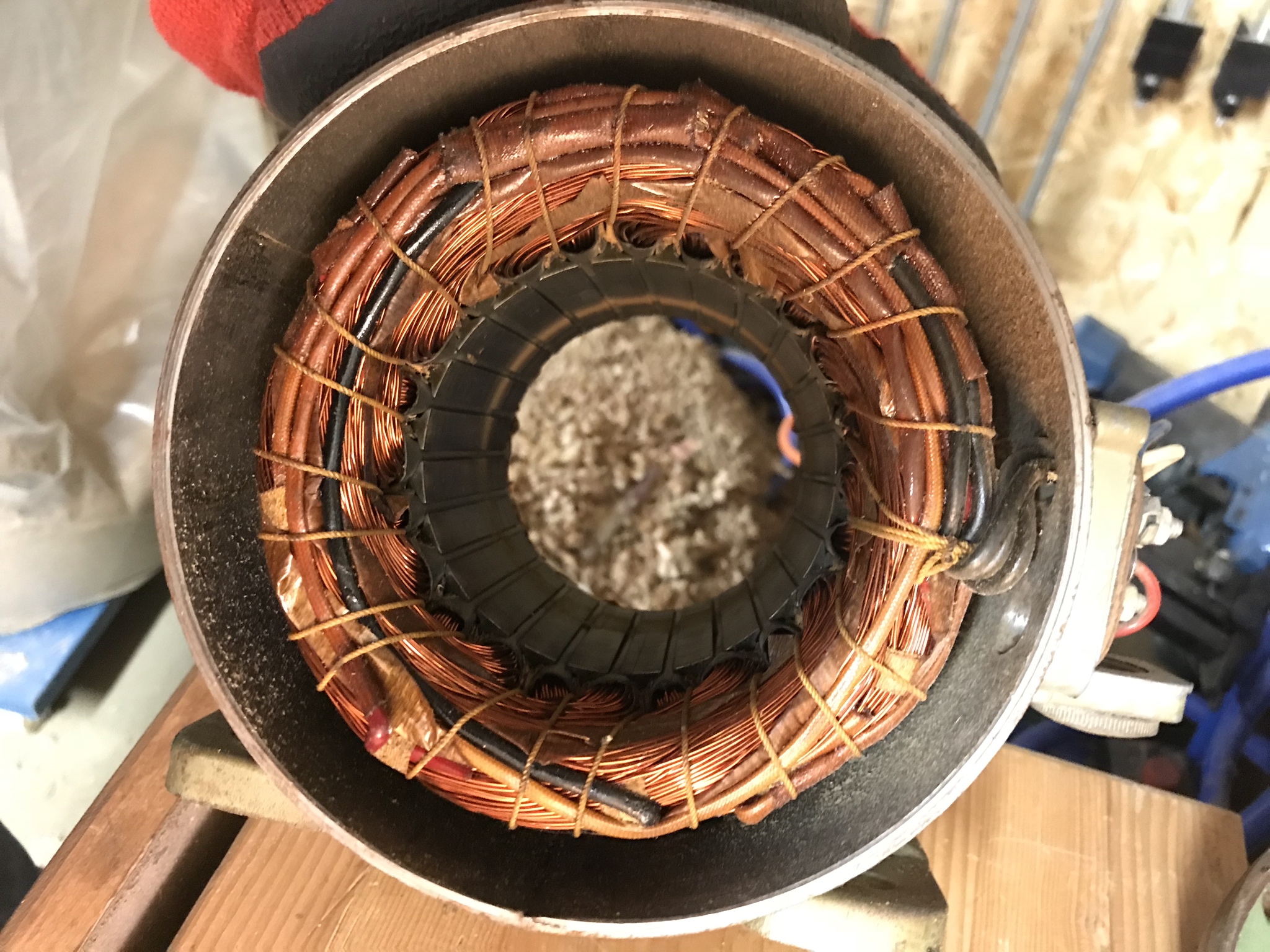
Only one end of the tails comes out into the junction box outside (415v). All help much appreciated.