CHJ
Established Member
__________Finishing off one of the small pots today, raised the thought
__________that someone may be interested in my solution to extending the Chuck Jaw range.
_________
___
___
___ click on images for larger view
___________Eight 7/8 x 1/4" pieces of steel, 48 Holes, 32 of them tapped 6mm.
__________Not something you would want to poke a finger in, but no worse than a square or natural edge bowl.
__________that someone may be interested in my solution to extending the Chuck Jaw range.
_________
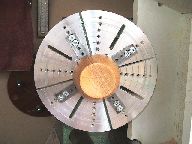
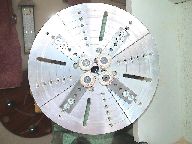
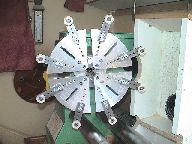
___________Eight 7/8 x 1/4" pieces of steel, 48 Holes, 32 of them tapped 6mm.
__________Not something you would want to poke a finger in, but no worse than a square or natural edge bowl.