gasman
Established Member
Some progress but a busy day at work on saturday and a bit frustrating on sunday so I ended up behind where I thought I would be and do not think I will finish by this weekend
However, I started by adding the ebony semicircular edging to the sides of the desktop base
and then cleaned it up
Bought it inside to cure the glue properly
Then finished off the small drawers in the top part and cut 1/8 inch grooves ready to take a 1/8th base using a new 1/8" downcutting spiral bit from wealden
The ash surround for the table top was quite difficult to plane - everything I tried resulted in tearout no matter how sharp the blade or from which direction. Tom L-N at Rycotewood was trying to persuade me that a low angle jack plane is the answer to all such problems - certainly it made a very good job of the piece of ash we planed on friday morning which had some tricky grain patterns too... perhaps I will have to save up some pennies!
Anyway I ended up using a scraper plane which I had been given years ago and had never really used in anger until yesterday - it gave a fantastic result and the burr seemed to last for ages: It is the medium cabinet make's scraper plane with a 45 degree bevel and it was a joy to use once I had taken the corners off the blade with a fine diamond stone
Finally I put the leather hide on the table top just to see what it looked like - and I was not disappointed with it - but I will put that away out of harm's way until everything else is finished
Thanks for looking
However, I started by adding the ebony semicircular edging to the sides of the desktop base
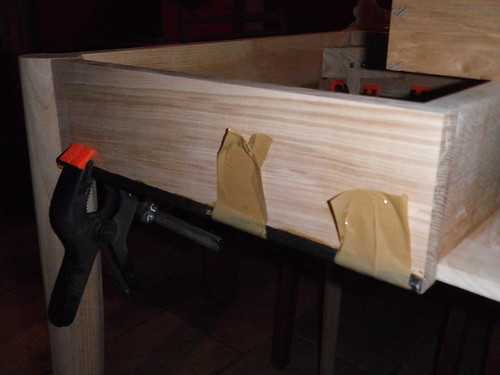
Bought it inside to cure the glue properly
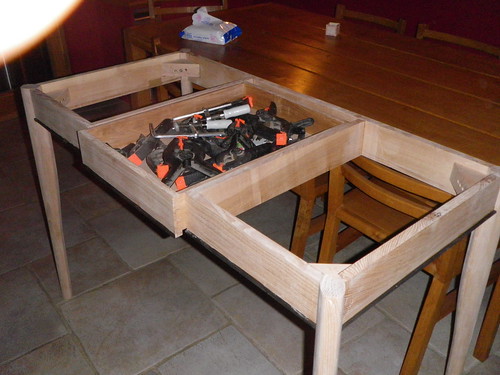
Then finished off the small drawers in the top part and cut 1/8 inch grooves ready to take a 1/8th base using a new 1/8" downcutting spiral bit from wealden
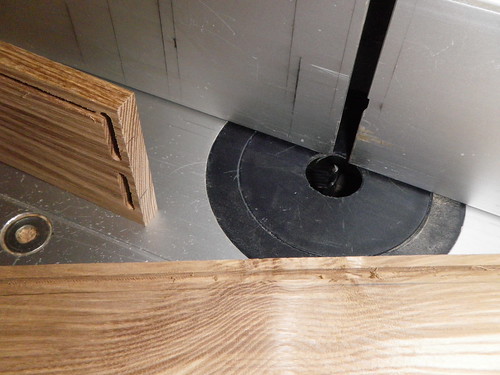
The ash surround for the table top was quite difficult to plane - everything I tried resulted in tearout no matter how sharp the blade or from which direction. Tom L-N at Rycotewood was trying to persuade me that a low angle jack plane is the answer to all such problems - certainly it made a very good job of the piece of ash we planed on friday morning which had some tricky grain patterns too... perhaps I will have to save up some pennies!
Anyway I ended up using a scraper plane which I had been given years ago and had never really used in anger until yesterday - it gave a fantastic result and the burr seemed to last for ages: It is the medium cabinet make's scraper plane with a 45 degree bevel and it was a joy to use once I had taken the corners off the blade with a fine diamond stone
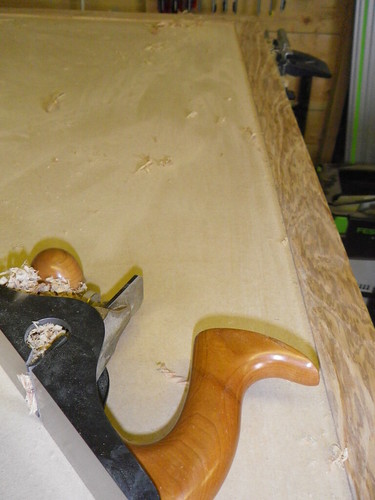
Finally I put the leather hide on the table top just to see what it looked like - and I was not disappointed with it - but I will put that away out of harm's way until everything else is finished
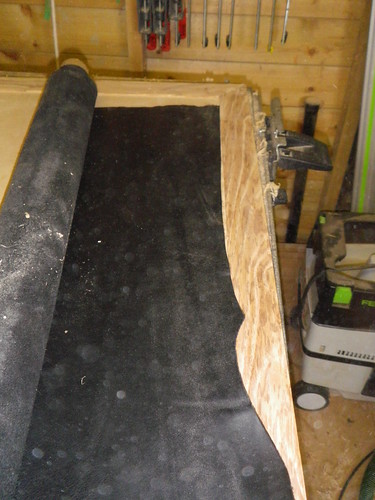
Thanks for looking