Bongodrummer
Established Member
Thanks bosshogg.
We are only putting the concrete in the two walled in bays (the insulated area), and perhaps the part of the barn that leads to this area. Should the expansion joints be dowelled to hold the slabs in alignment, or is this overkill? I guess that way the slabs would have to be poured in at least two batches...
Thins kind of thing?
We are only putting the concrete in the two walled in bays (the insulated area), and perhaps the part of the barn that leads to this area. Should the expansion joints be dowelled to hold the slabs in alignment, or is this overkill? I guess that way the slabs would have to be poured in at least two batches...
Thins kind of thing?
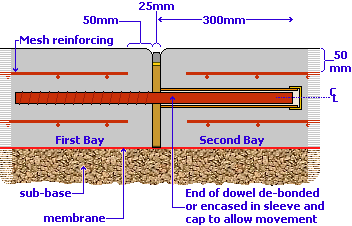