frugal
Established Member
I have been away from here for a number of years, in fact I have been away from most forums and social media, but in the meantime I have still been woodworking. One of my problems is that whilst I have a nice big garage for all of the tools and machines, the only surface I have for working with handtools is a Workmate. Which is fine for somethings, but does tend to skitter across the floor as soon as it sees a handplane. Whilst we were on holiday in France last year, we went to a Broconte (French town fair / tractor show / car boot sale) and my wife convinced me to get a hold fast that was going cheap with the comment "now you have to build the bench to go with it".
Well, 6 months later I finally decided to go for it. I had read all of the books (The Workbench by Tolpin; all of Chris Schwarz workbench books), I had watched any number of videos and blogs on workbench builds, I had chosen the size, the shape and the vises that were going to go on it. All I had to do was to summon up the courage to start.
I had decided to go for a Roubo style bench with just a shelf at the bottom. Leg vise on the front and a wagon vise on the end. As I am left handed and as the only feasible spot in the garage is under the window with a wall to the right, I decided to be awkward and put the wagon vise on the left hand side near the front and the leg vise to the right hand end of the front. I am going to break some other rules whilst I am at it: The height will be 36" or so, as I have a bad back and I do not want to bend over too much. I will also be making it 30" deep and 8' long. I am going for 30" deep as I am going to be having cabinets on the walls above the bench, and even shallow cabinets are going to take up some of the depth.
One rule I am going to follow is "make it solid", boy am I following that rule. So the top is going to be 8' long, 30" wide and 4" thick ash, made from 17 1.75" thick boards laminated together. The legs are going to be 6"x5", made up of three boards laminated together. I only intend to make one bench, so I am going to do it right.
So bonus time rolled around this year and I got ready. I knew that my little DW733 thicknesser was not going to cut it, and I would also need a planer, so I splashed out on a AW106PT2 planer/thicknesser from Axminster, and a AT3202FDP floor standing pillar drill. I also ordered a wagon vise and a wooden vise screw from Richard Maguire. The wood was all english ash apart from the vise chop, deadman and breadboards which are Cherry. All of the wood was from Interesting Timbers. 31cu.ft of Ash and 2cu.ft cherry. That hurt the wallet.
I have to say, after picking up most of my stash from auction, the wood from Interesting Timbers was gorgeous. They asked for my cut list and pulled the boards themselves (their yard is only open Mon-Fri and I work full time so I could not go to see them). For reference in the photo, the ruler is 24" long. Most of the ash boards were 16-18" wide, and they were all 12' long. So from each board I was able to get a couple of the 8' bench top pieces, and a couple of the leg pieces.
In fact the wood was so clean and so wide and I recalculated how much I would need. I was expecting to get 2" boards that would be thicknessed down to 1.75", however all of the 2" thick stock was actually 2.25" and so flat that after thicknessing it was still 2 1/8" thick. It was also so wide that I was able to thicken the top from 4" to 5.5", and still have a full board left over as well as a large number of good sized off cuts.
As these boards were all too big to move by myself, I roughed them out with the circular saw on the driveway and moved the smaller planks into the garage.
So now I have 15 8'x5.5"x2" boards for the top; 9 3'x9"x1" board for the bottom shelf; 12 3'x6"x2" boards to laminate up into legs, and some 3" thick stock for the stretchers between the legs.
Unfortunately I also worked out how much this is going to weigh, and it comes in at something over 300lbs...
Well, 6 months later I finally decided to go for it. I had read all of the books (The Workbench by Tolpin; all of Chris Schwarz workbench books), I had watched any number of videos and blogs on workbench builds, I had chosen the size, the shape and the vises that were going to go on it. All I had to do was to summon up the courage to start.
I had decided to go for a Roubo style bench with just a shelf at the bottom. Leg vise on the front and a wagon vise on the end. As I am left handed and as the only feasible spot in the garage is under the window with a wall to the right, I decided to be awkward and put the wagon vise on the left hand side near the front and the leg vise to the right hand end of the front. I am going to break some other rules whilst I am at it: The height will be 36" or so, as I have a bad back and I do not want to bend over too much. I will also be making it 30" deep and 8' long. I am going for 30" deep as I am going to be having cabinets on the walls above the bench, and even shallow cabinets are going to take up some of the depth.
One rule I am going to follow is "make it solid", boy am I following that rule. So the top is going to be 8' long, 30" wide and 4" thick ash, made from 17 1.75" thick boards laminated together. The legs are going to be 6"x5", made up of three boards laminated together. I only intend to make one bench, so I am going to do it right.
So bonus time rolled around this year and I got ready. I knew that my little DW733 thicknesser was not going to cut it, and I would also need a planer, so I splashed out on a AW106PT2 planer/thicknesser from Axminster, and a AT3202FDP floor standing pillar drill. I also ordered a wagon vise and a wooden vise screw from Richard Maguire. The wood was all english ash apart from the vise chop, deadman and breadboards which are Cherry. All of the wood was from Interesting Timbers. 31cu.ft of Ash and 2cu.ft cherry. That hurt the wallet.
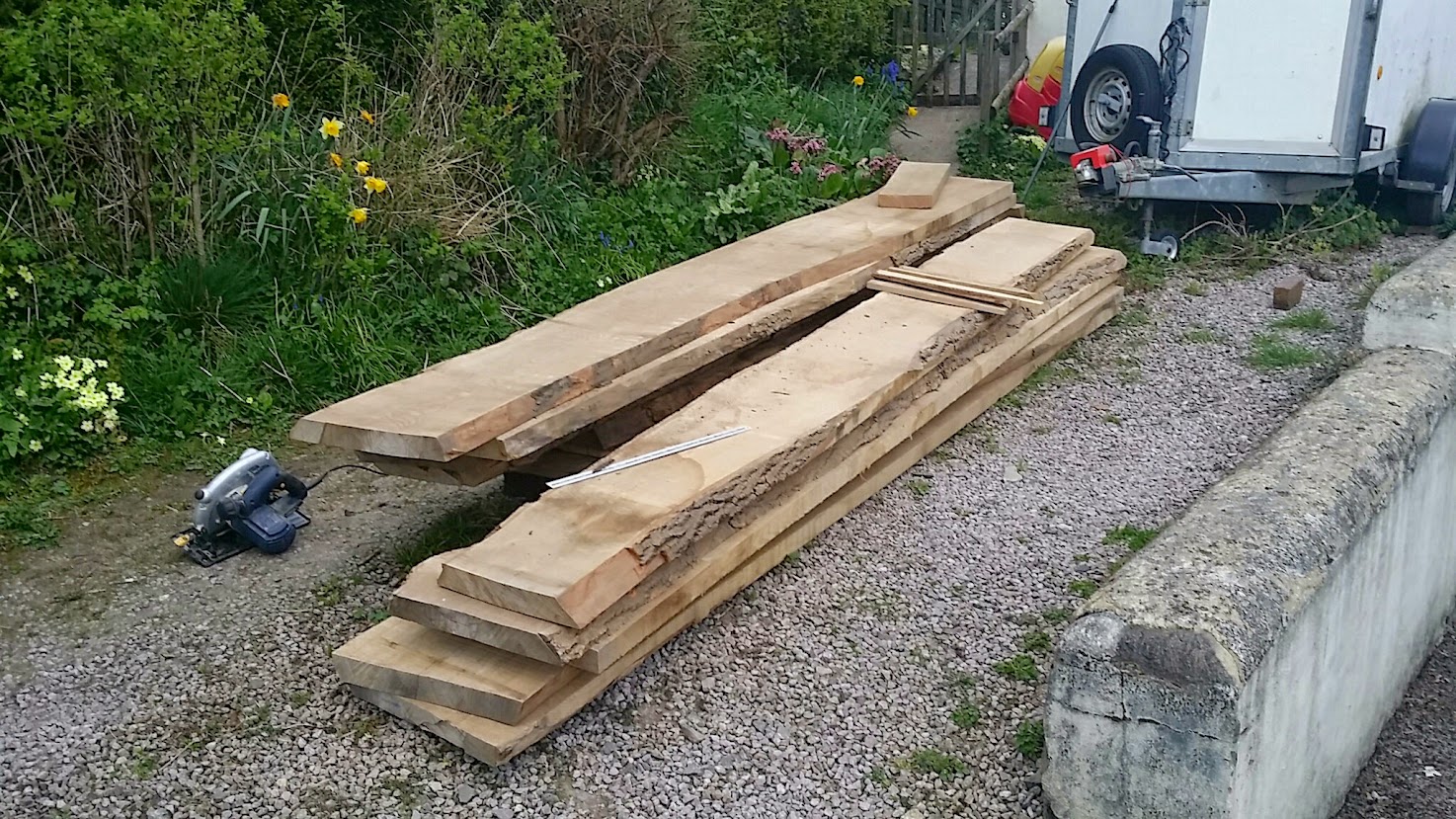
I have to say, after picking up most of my stash from auction, the wood from Interesting Timbers was gorgeous. They asked for my cut list and pulled the boards themselves (their yard is only open Mon-Fri and I work full time so I could not go to see them). For reference in the photo, the ruler is 24" long. Most of the ash boards were 16-18" wide, and they were all 12' long. So from each board I was able to get a couple of the 8' bench top pieces, and a couple of the leg pieces.
In fact the wood was so clean and so wide and I recalculated how much I would need. I was expecting to get 2" boards that would be thicknessed down to 1.75", however all of the 2" thick stock was actually 2.25" and so flat that after thicknessing it was still 2 1/8" thick. It was also so wide that I was able to thicken the top from 4" to 5.5", and still have a full board left over as well as a large number of good sized off cuts.
As these boards were all too big to move by myself, I roughed them out with the circular saw on the driveway and moved the smaller planks into the garage.
So now I have 15 8'x5.5"x2" boards for the top; 9 3'x9"x1" board for the bottom shelf; 12 3'x6"x2" boards to laminate up into legs, and some 3" thick stock for the stretchers between the legs.
Unfortunately I also worked out how much this is going to weigh, and it comes in at something over 300lbs...