StevieB
Established Member
My design brief was to design a jewellery box in two contrasting timbers with a secret compartment of some description. The design brief also stated a number of drawers or a sliding tray for storage. After sketching out a traditional box with a sliding tray however it became clear that adding a secret compartment to this design was going to be problematic if the compartment was to be of a sufficent size to hold anything useful. Thus, after discussion with SWMBO and a bit of playing with sketchup the design is going to be based on a tower of drawers as shown below.
This is frame of oak with birds eye maple veneered panels. The top will be hinged with a false drawer front. I may also put a removable tray in the top depending on how the frame pans out. The purple is SWMBOs request for felt/velvet in that colour but I am not convinced by the colour yet. The drawers will be oak fronts with solid maple sides and back:
I am aiming for dovetails on these drawers, perhaps optomistically. Handles are yet to be decided, I have not looked for any yet so these are just a rough idea I knocked up in sketchup. I am tending towards brass however rather than timber handles. Overall size will be approximately 400mm high, 250mm wide and 250mm deep.
As for the secret compartment, I currently have two options. The first is to make a false cross-member on the side and have this as a drawer front for a slim drawer that slides out from the side:
The second option is to make the drawers slightly shallower than the carcass and leave a space behind them. This would be accessed by folding back the bottom of the top space. To make this less obvious I could embedd a metal bar under the flap and thus you would need a magnet to open the flap. This avoids the need for a finger hole. Alternatively I could leave a small pilot hole and use a bent piece of wire to lift the flap, or finally I could make it more obvious by using a small lock and having a key hole in the felt ( a drop in tray for that top box would then make this less obvious).
I have a couple of items I am not sure of yet. The first is the veneered panels. I was initially going to have them as floating panels ie set back into the cacass by 2-3mm. For the lid however I wanted to lip the panel so the birds eye panel was flush. I am not sure whether to do this for the side panels or not as well. The second issue is the length of the legs. On the figures above they are approx 50mm. Is that too short to put a taper on them? Should I taper them at all, or should they be longer than 50mm?
All comments welcome!
Steve.
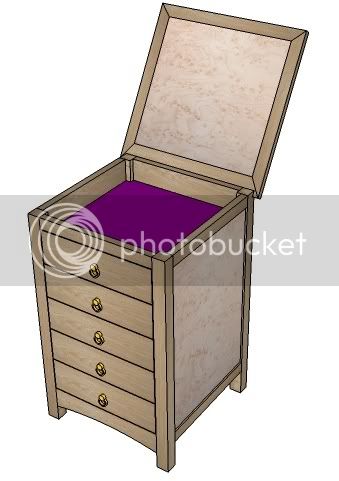
This is frame of oak with birds eye maple veneered panels. The top will be hinged with a false drawer front. I may also put a removable tray in the top depending on how the frame pans out. The purple is SWMBOs request for felt/velvet in that colour but I am not convinced by the colour yet. The drawers will be oak fronts with solid maple sides and back:
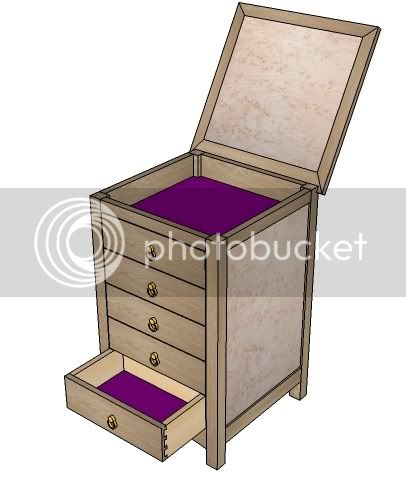
I am aiming for dovetails on these drawers, perhaps optomistically. Handles are yet to be decided, I have not looked for any yet so these are just a rough idea I knocked up in sketchup. I am tending towards brass however rather than timber handles. Overall size will be approximately 400mm high, 250mm wide and 250mm deep.
As for the secret compartment, I currently have two options. The first is to make a false cross-member on the side and have this as a drawer front for a slim drawer that slides out from the side:
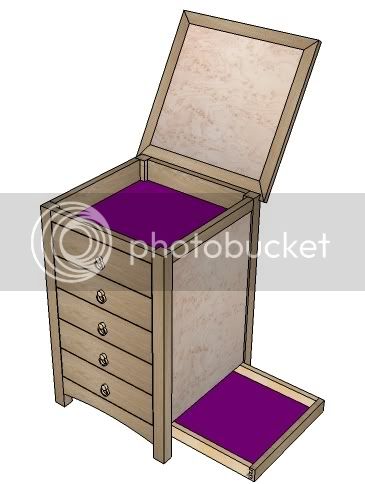
The second option is to make the drawers slightly shallower than the carcass and leave a space behind them. This would be accessed by folding back the bottom of the top space. To make this less obvious I could embedd a metal bar under the flap and thus you would need a magnet to open the flap. This avoids the need for a finger hole. Alternatively I could leave a small pilot hole and use a bent piece of wire to lift the flap, or finally I could make it more obvious by using a small lock and having a key hole in the felt ( a drop in tray for that top box would then make this less obvious).
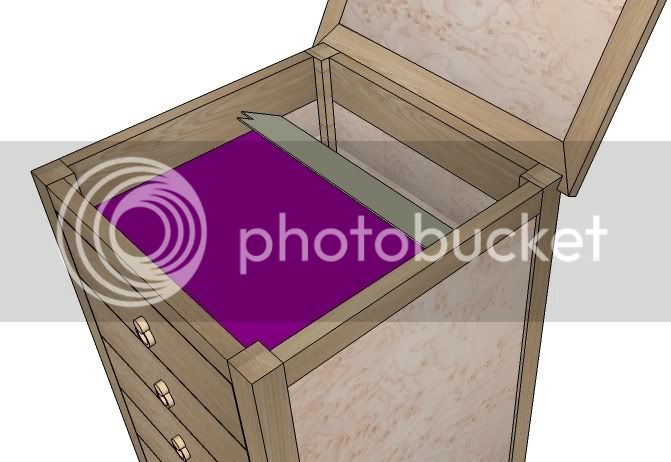
I have a couple of items I am not sure of yet. The first is the veneered panels. I was initially going to have them as floating panels ie set back into the cacass by 2-3mm. For the lid however I wanted to lip the panel so the birds eye panel was flush. I am not sure whether to do this for the side panels or not as well. The second issue is the length of the legs. On the figures above they are approx 50mm. Is that too short to put a taper on them? Should I taper them at all, or should they be longer than 50mm?
All comments welcome!
Steve.