MattMoore
Established Member
Evening all,
I've got quite a big order for sash windows at the moment, and with this is a large number of horns.
Usually I've roughed out on the bandsaw and used sandpaper to finish but this time I want to try using a rasp to both speed up the process, and get them more consistent. I've read a little about them and I'm quite unsure which would be the best to go for, and how many (as few as possible) I will need to do the job well. I've attached a drawing below so that you know the dimensions of the piece. I need them by the weekend so will be placing an order tomorrow hopefully.
Thanks
I've got quite a big order for sash windows at the moment, and with this is a large number of horns.
Usually I've roughed out on the bandsaw and used sandpaper to finish but this time I want to try using a rasp to both speed up the process, and get them more consistent. I've read a little about them and I'm quite unsure which would be the best to go for, and how many (as few as possible) I will need to do the job well. I've attached a drawing below so that you know the dimensions of the piece. I need them by the weekend so will be placing an order tomorrow hopefully.
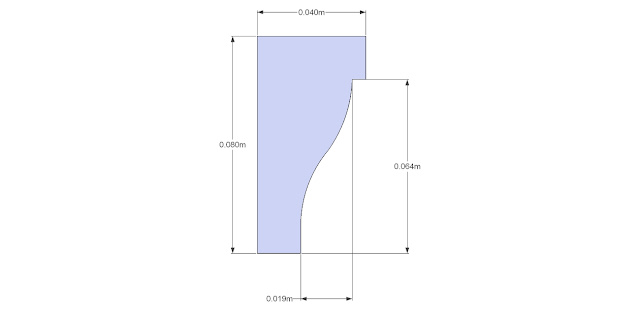
Thanks