BradNaylor
Established Member
- Joined
- 17 Oct 2007
- Messages
- 2,311
- Reaction score
- 2
Bloke came in the workshop yesteday with a very blurred photo of this and asked if we could make him one. Of course we said 'Yes!'
A price was agreed (£3,000) and a deposit pocketed. After he'd gone we then retired to the pub!
I've worked out how I would tackle it but I would be grateful for any other suggestions.
Worst of it is that SWMBO has seen the photos and now she wants one too! :shock:
Cheers
Brad
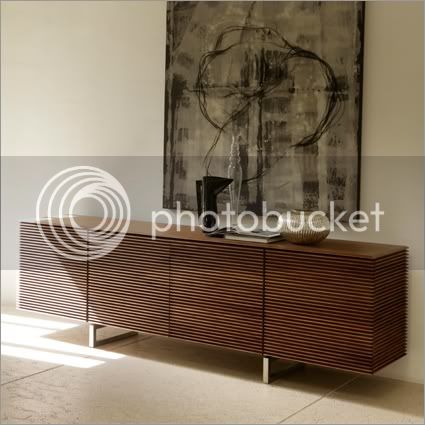
A price was agreed (£3,000) and a deposit pocketed. After he'd gone we then retired to the pub!
I've worked out how I would tackle it but I would be grateful for any other suggestions.
Worst of it is that SWMBO has seen the photos and now she wants one too! :shock:
Cheers
Brad