Corset
Established Member
After having a bit of a go at banging out some wardrobes which turned out ok'ish. I got some credit from the wife.
At this point I decided to start work on a wall tool chest. I have for some time kept my tools on a wall mounted plywood box which while crude has worked well for the last couple of years. It stops me losing stuff and with the inclusion of a low voltage bulb stops the rust. However i made it to long and it hardly clears my bench and was a bit ugly. Clearly this is a slightly indulgent project and the old box would work fine however...
I would like at this point to state that i do have too many tools, i don't need half of them and clearly a more talented person would produce more and collect less, but you can't help who you are and I have always loved tool chests and tools. I therefore have ended up with lots of shiny brass and metal things. When i saw the Studley tool chest many years ago I wanted to have a go at making a slightly less impressive one. Here is my attempt.
I am not a great photograper and as my attempts are in two hour evening chunks I have sometimes forgotton to whip out the iphone. I will post a few photos and hope people might be interested in my attempts.
I have had to buy very little wood so far as I have had some black walnut left over form a project so I decided to make the casework from this. Clearly it was rough sawn and i thicknessed it down and jointed it make the carcass.
I decided to dovetail the joints for the carcass selecting the best board orientation and allowing for the unit to be cut in half.
Chisels ahoy
Chopping out waste with some ground back chisels.
Using some blue tape for visual aid on the pins. Thanks for the tip whoever posted this a while back cracking.
Planing back dovetails, drive by shot of plane. I am hoping to use all the tools on the project that are going in the tools chest
Next I got frame for the front made up, i used some dominos
tightjoint
Next i picked up some idiand grey silver wood planks from a tool auction fo 20 quid. no idea what it was but i thought i would veneer with it. it turned out nice from some murky grey planks
so far so good. i have got more photos as i progress if anyone is interested?
owen
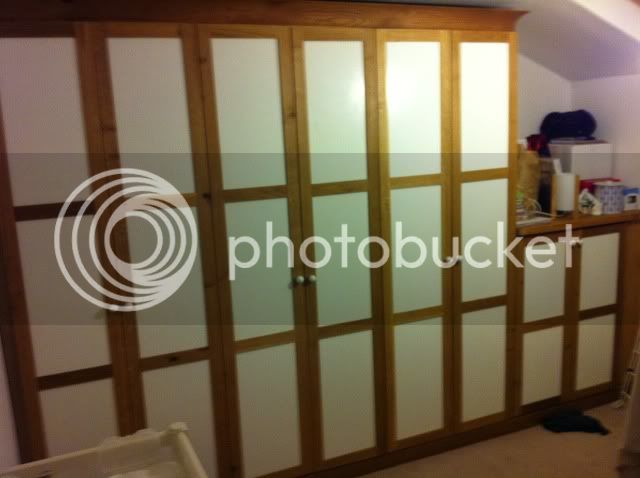
At this point I decided to start work on a wall tool chest. I have for some time kept my tools on a wall mounted plywood box which while crude has worked well for the last couple of years. It stops me losing stuff and with the inclusion of a low voltage bulb stops the rust. However i made it to long and it hardly clears my bench and was a bit ugly. Clearly this is a slightly indulgent project and the old box would work fine however...
I would like at this point to state that i do have too many tools, i don't need half of them and clearly a more talented person would produce more and collect less, but you can't help who you are and I have always loved tool chests and tools. I therefore have ended up with lots of shiny brass and metal things. When i saw the Studley tool chest many years ago I wanted to have a go at making a slightly less impressive one. Here is my attempt.
I am not a great photograper and as my attempts are in two hour evening chunks I have sometimes forgotton to whip out the iphone. I will post a few photos and hope people might be interested in my attempts.
I have had to buy very little wood so far as I have had some black walnut left over form a project so I decided to make the casework from this. Clearly it was rough sawn and i thicknessed it down and jointed it make the carcass.
I decided to dovetail the joints for the carcass selecting the best board orientation and allowing for the unit to be cut in half.
Chisels ahoy
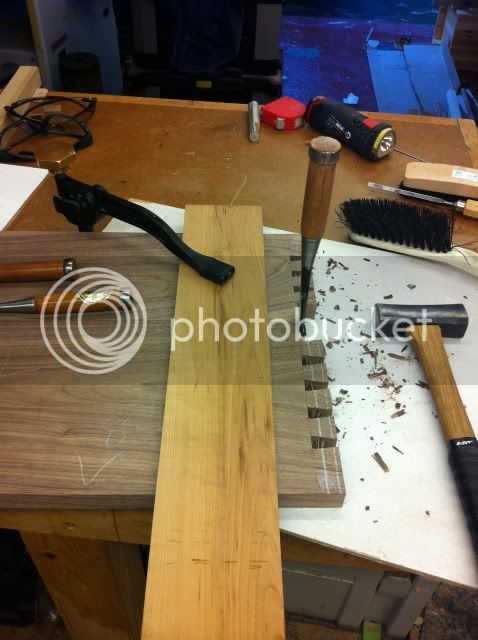
Chopping out waste with some ground back chisels.
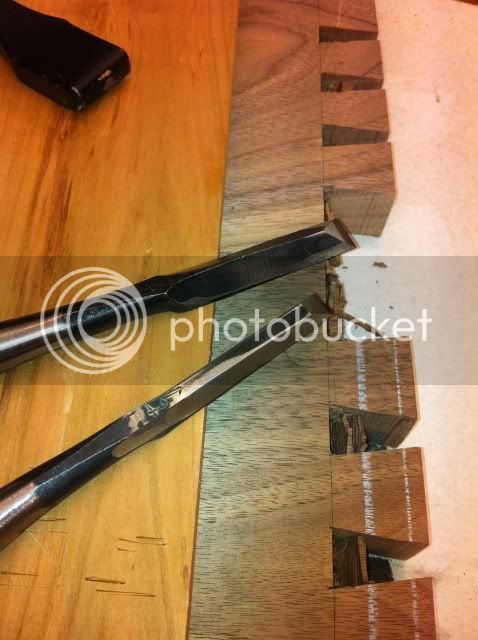
Using some blue tape for visual aid on the pins. Thanks for the tip whoever posted this a while back cracking.
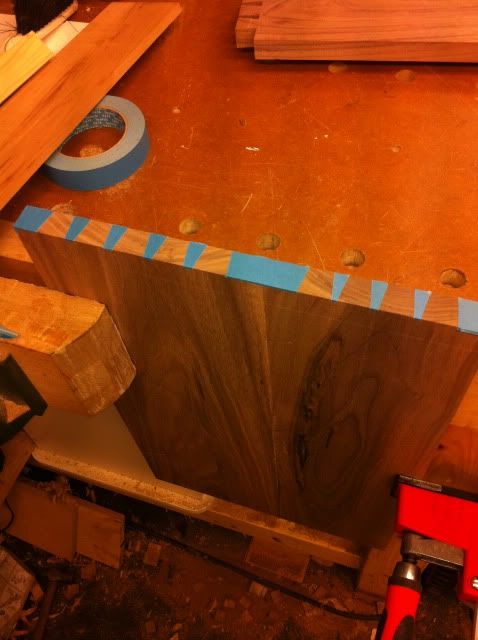
Planing back dovetails, drive by shot of plane. I am hoping to use all the tools on the project that are going in the tools chest
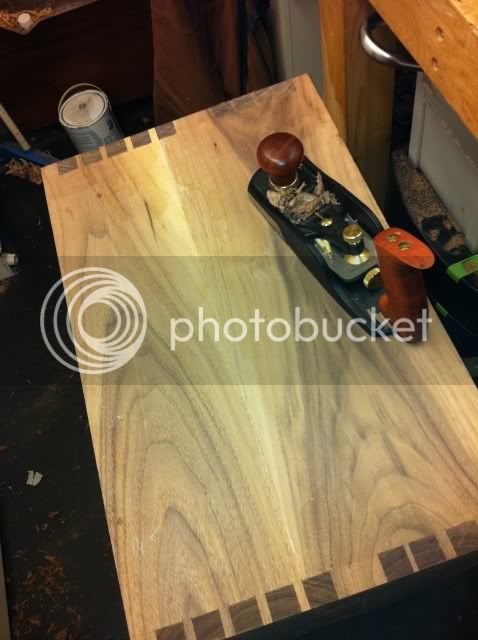
Next I got frame for the front made up, i used some dominos
tightjoint
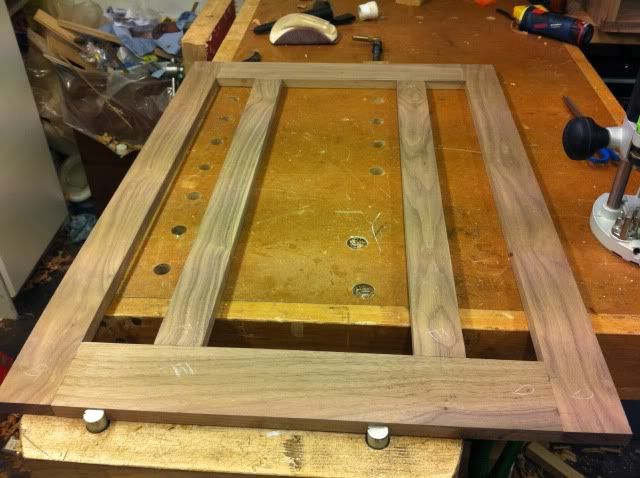
Next i picked up some idiand grey silver wood planks from a tool auction fo 20 quid. no idea what it was but i thought i would veneer with it. it turned out nice from some murky grey planks
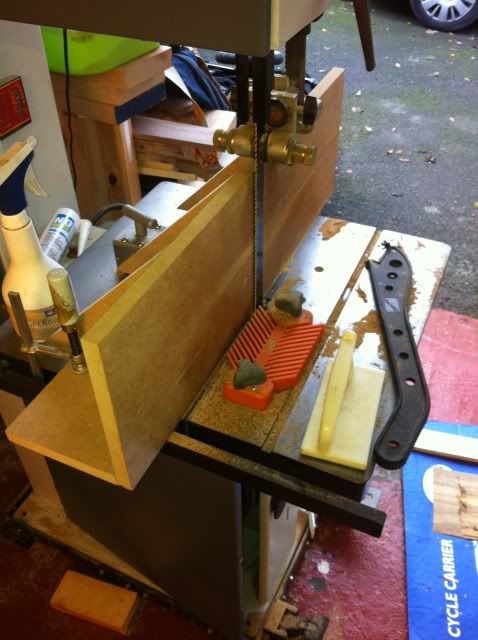
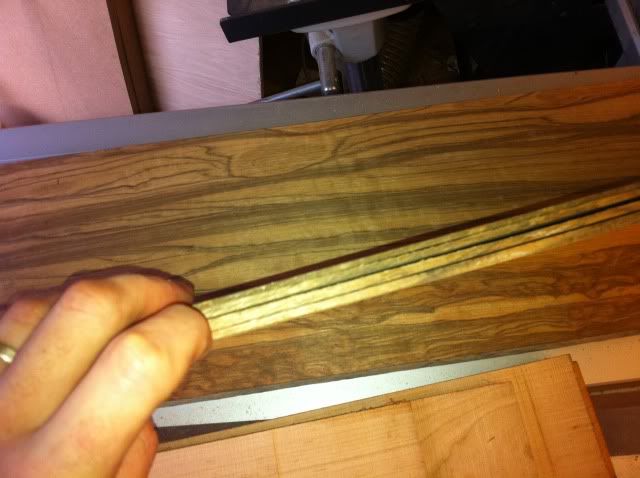
so far so good. i have got more photos as i progress if anyone is interested?
owen
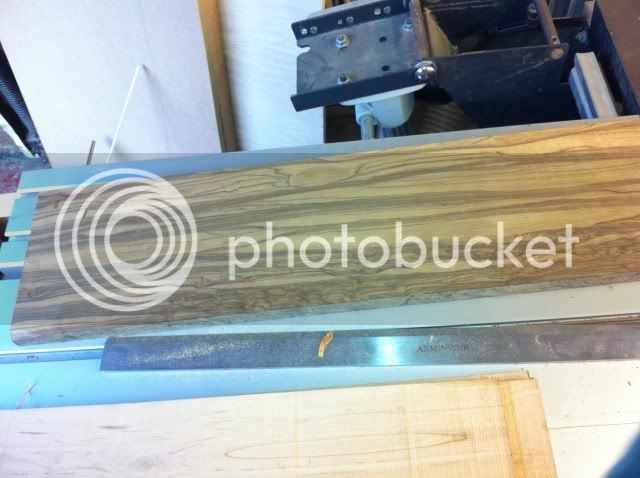