tool613
Established Member
The rain stopped and I was able it get the thread lift for the table in on one side.
the Rm has many plain beaings steel on steel or in cast that are greased with grease cups, these have held up great-infact beter than the ball bearing in there . They are all slow moving parts thought.
here is one side of the table lift.
inside the frame large cast brackets(2.5" thick) set to post out from the frame so that the threads of the table rise and fall can be completely encased from dust under the table. there is a lot of work in pattern making and engineering to do this.
and most planers have there thread lift at the sides.
its starts with the steel sleeve bearing set into the casting bore, you can see the channel cut into interior so grease spreads over the shaft.
this threaded taper pin locks it in and lines up the grease holes in the casting.
next are the thrust bearing that take the load of the Table. there are no way to get at these open bearings other than taking the tables out. the old grease was hardened wax and so i decided to use a synthetic grease EP grade 1.5 for them this time.
a brass grease cap threads into the casting to grease the bearing. I love theses things you fill the cap with grease and give it a turn every 6 months
the thrust bearing is taper pined to the thread lift.
jack
English machines
the Rm has many plain beaings steel on steel or in cast that are greased with grease cups, these have held up great-infact beter than the ball bearing in there . They are all slow moving parts thought.
here is one side of the table lift.
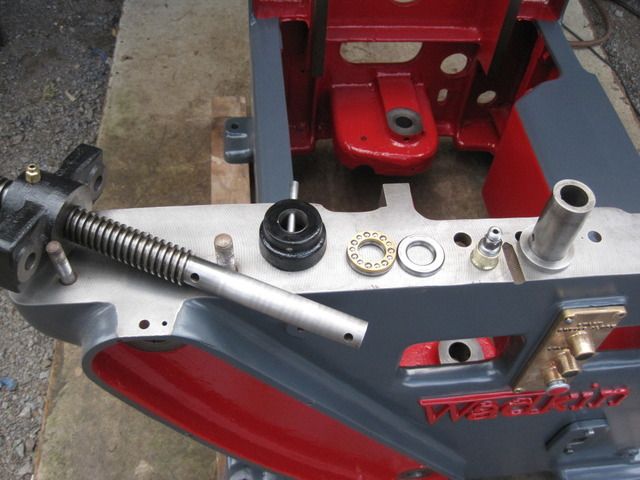
inside the frame large cast brackets(2.5" thick) set to post out from the frame so that the threads of the table rise and fall can be completely encased from dust under the table. there is a lot of work in pattern making and engineering to do this.
and most planers have there thread lift at the sides.
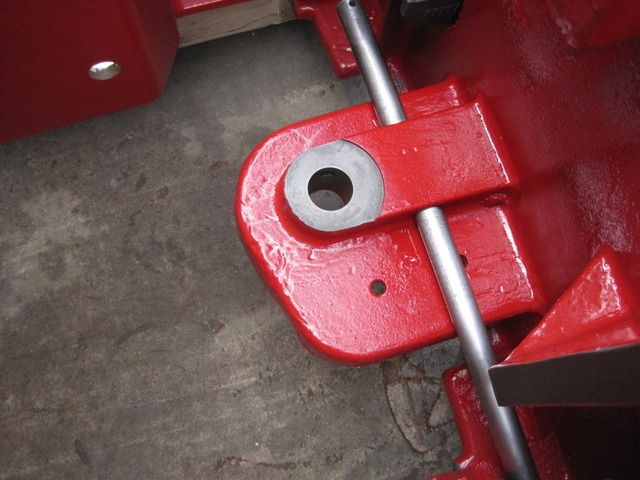
its starts with the steel sleeve bearing set into the casting bore, you can see the channel cut into interior so grease spreads over the shaft.
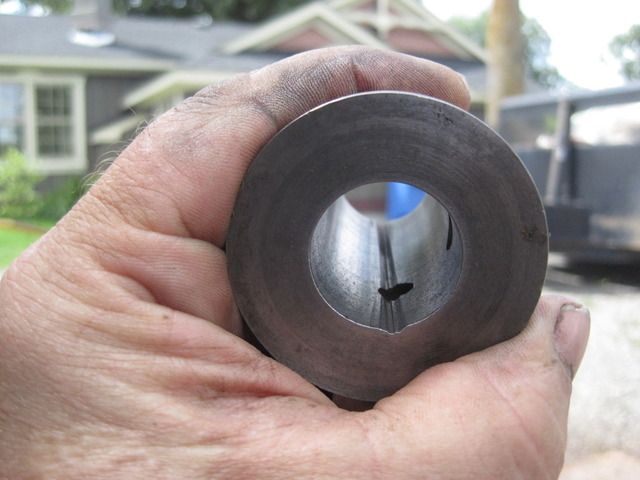
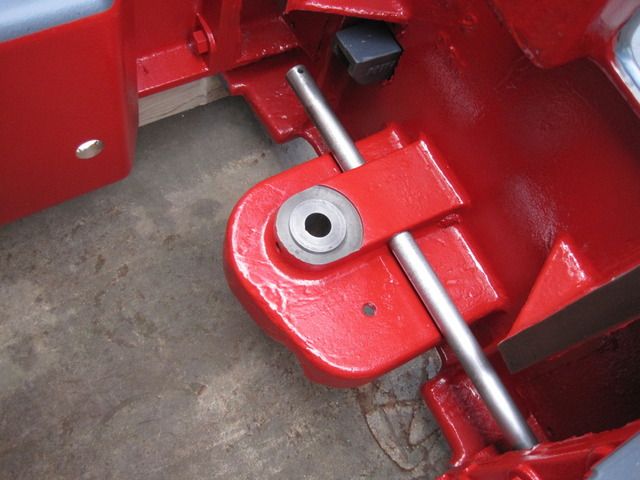
this threaded taper pin locks it in and lines up the grease holes in the casting.
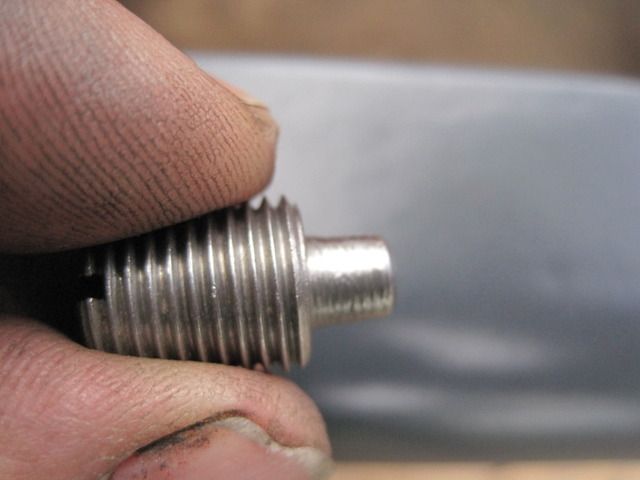
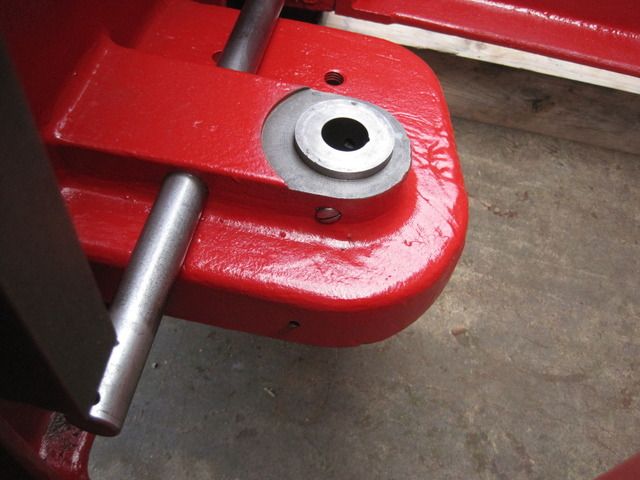
next are the thrust bearing that take the load of the Table. there are no way to get at these open bearings other than taking the tables out. the old grease was hardened wax and so i decided to use a synthetic grease EP grade 1.5 for them this time.
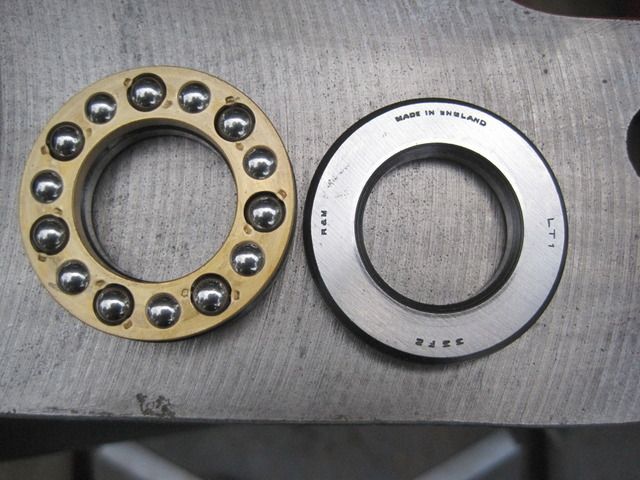
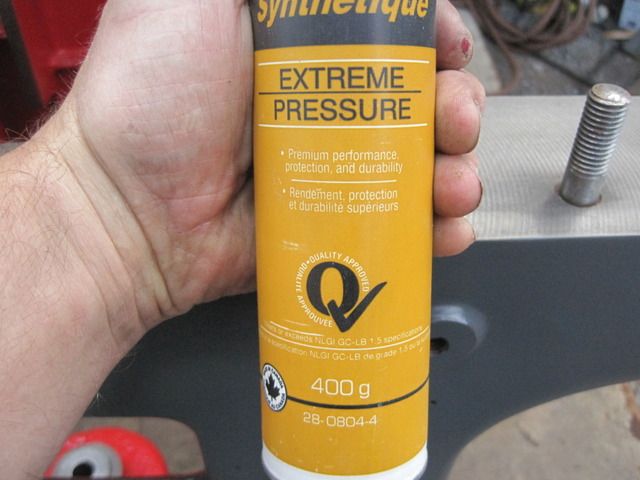
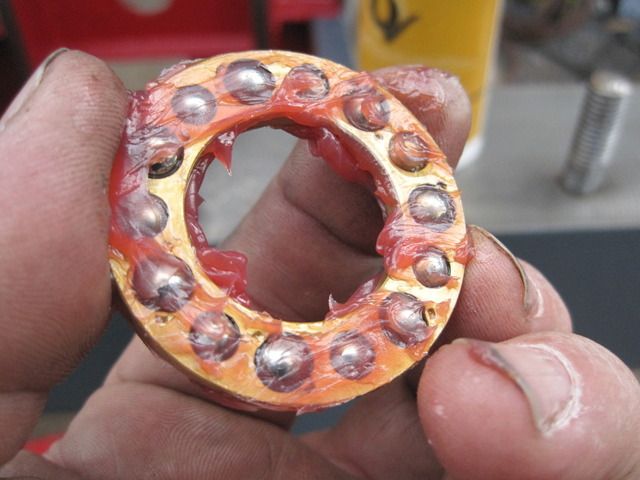
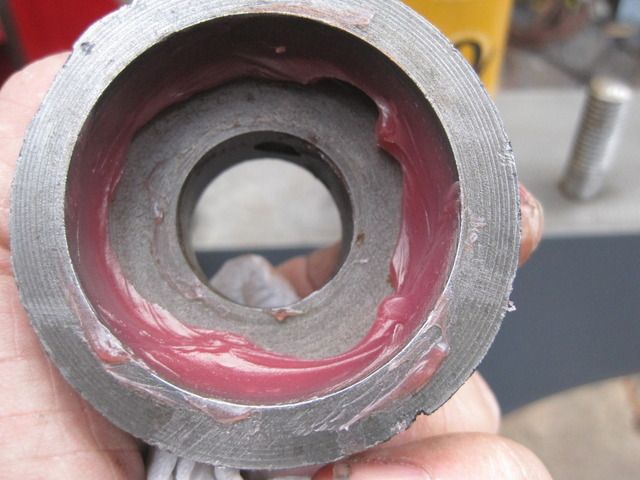
a brass grease cap threads into the casting to grease the bearing. I love theses things you fill the cap with grease and give it a turn every 6 months
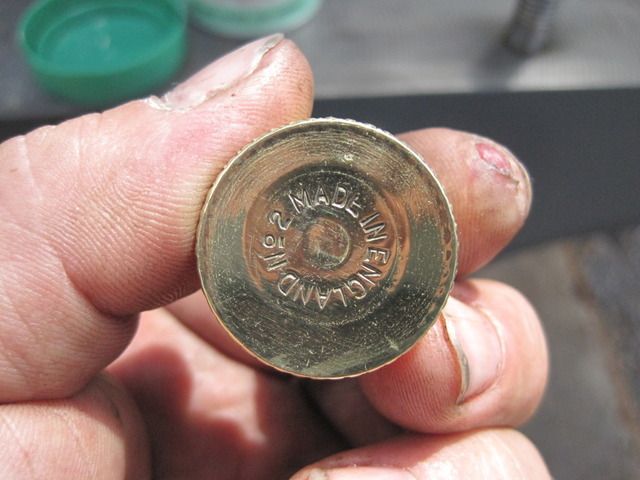
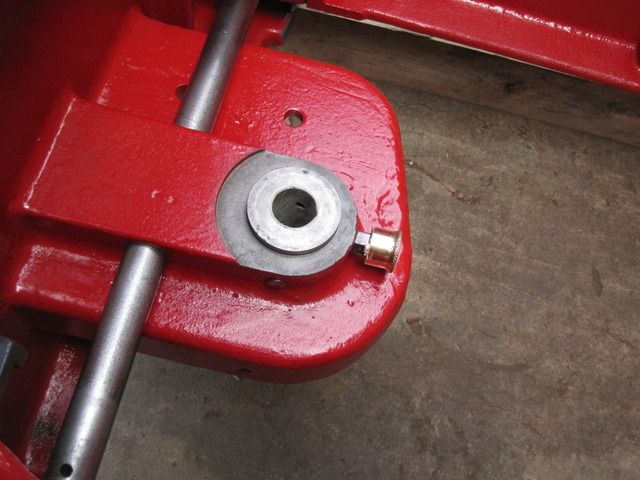
the thrust bearing is taper pined to the thread lift.
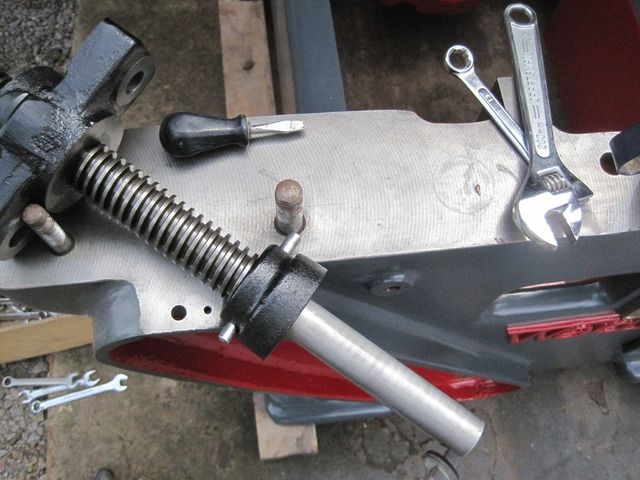
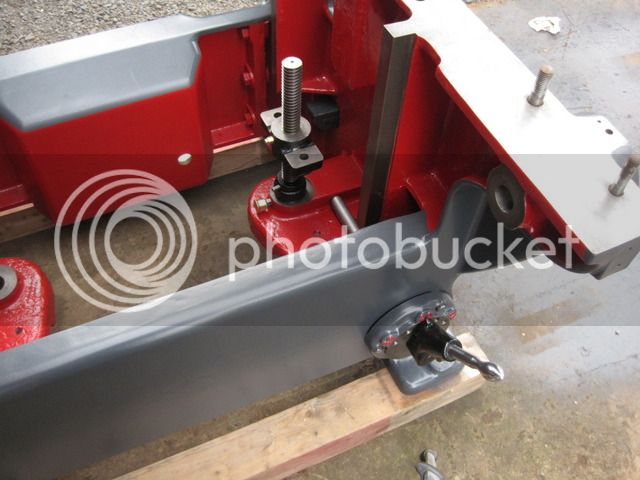
jack
English machines