wallace
Established Member
Its been 10 minutes since my last restoration so I think its time to start another one. This one was originally a line shaft machine dating from 1920's but a motor was added in the 40's 50's judging by the type of motor. I got this delivered a little while ago but because it ended up falling off the pallets it came on, and then I hurt my back. Its been sat outside. I managed to get it in the workshop and began work. I was thinking of trying a different approach with this one, instead of stripping it down completely and then starting to refurb. I thought I'd try takeing a piece of at a time and doing it.
I think this might of hindered its performance the last time it was used, a knot well and truly wedged
I got this nice whitworth brittool socket set from a car boot recently, well pleased £5. It should help with my old iron


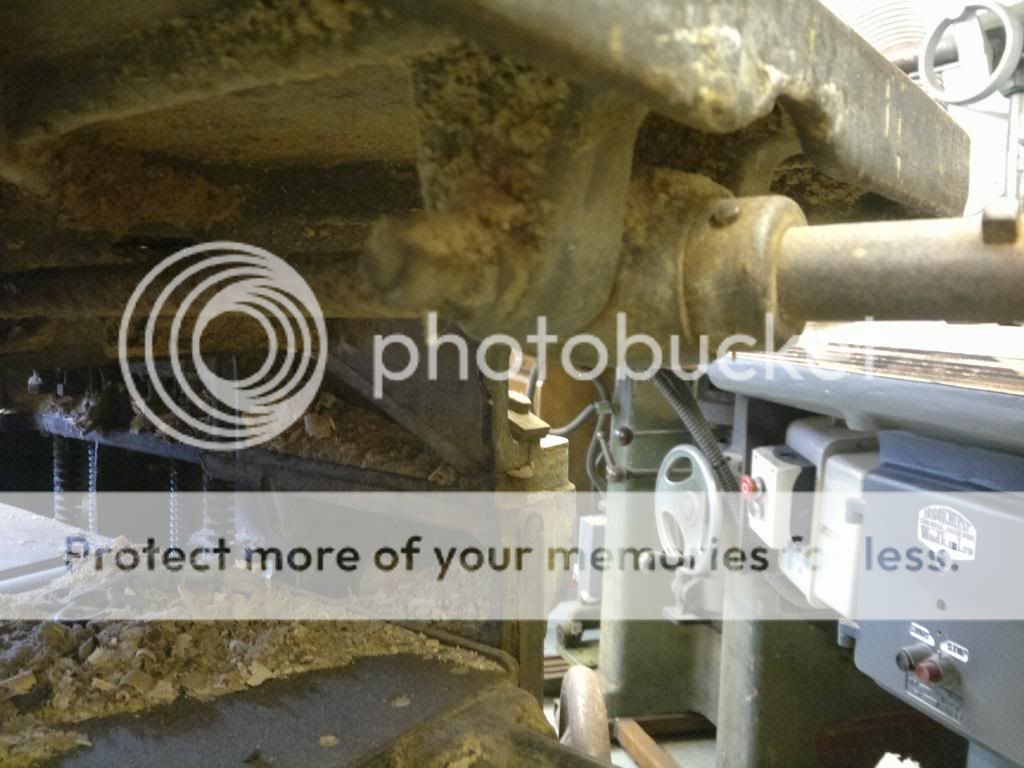
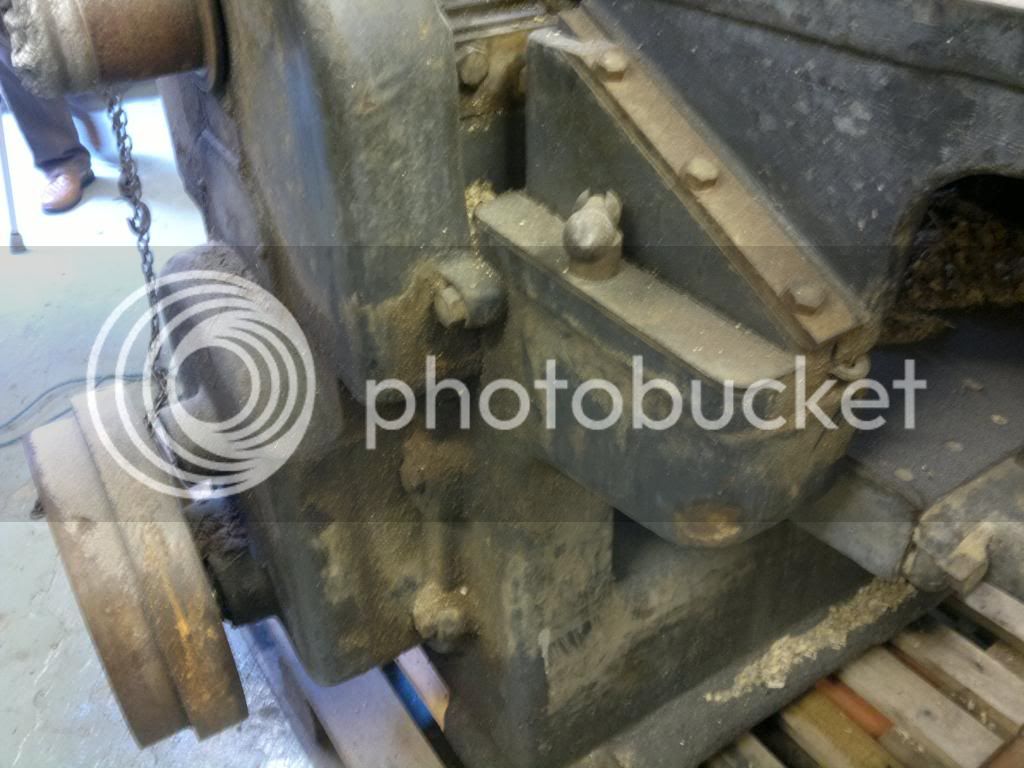

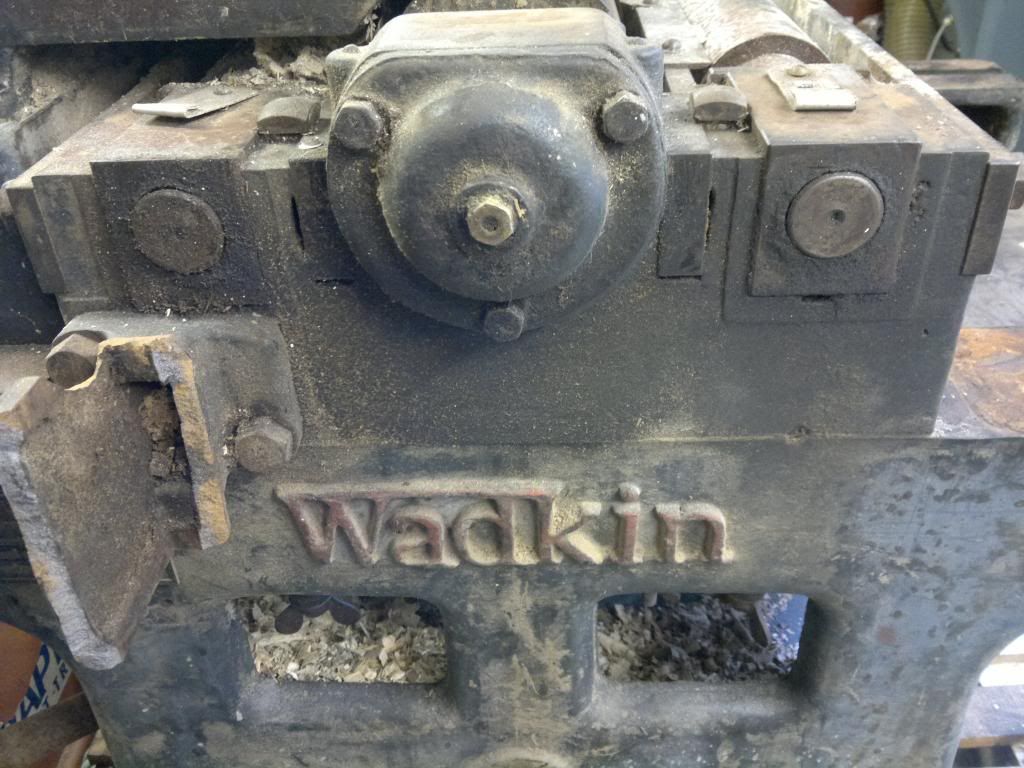
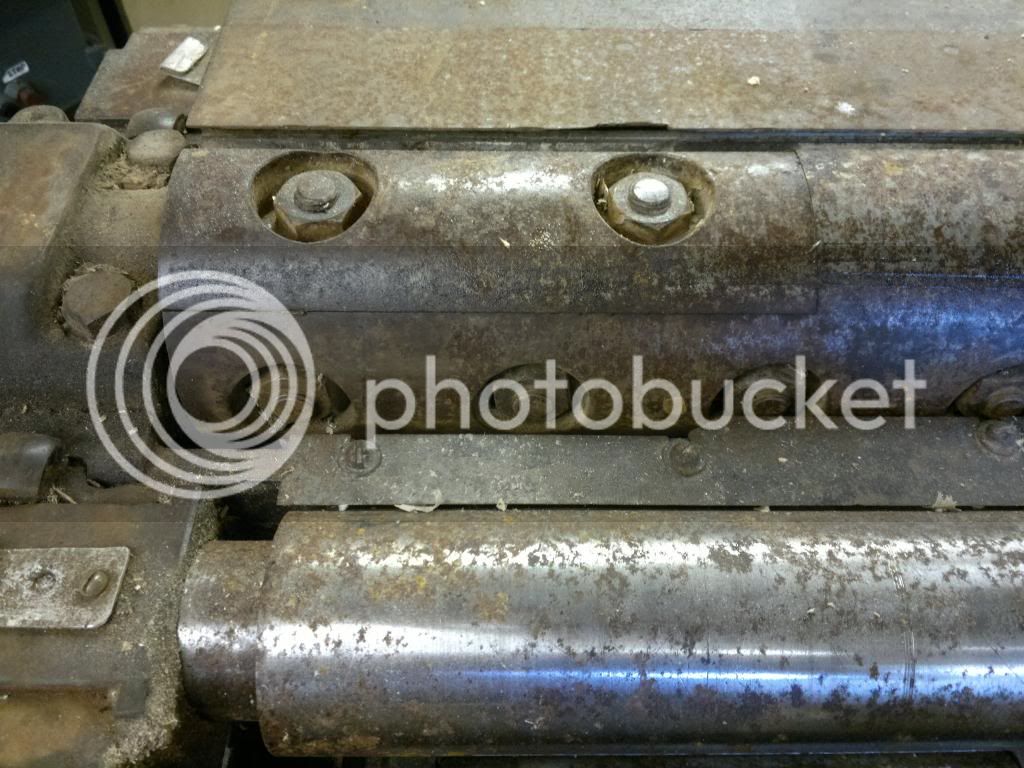
I think this might of hindered its performance the last time it was used, a knot well and truly wedged

I got this nice whitworth brittool socket set from a car boot recently, well pleased £5. It should help with my old iron
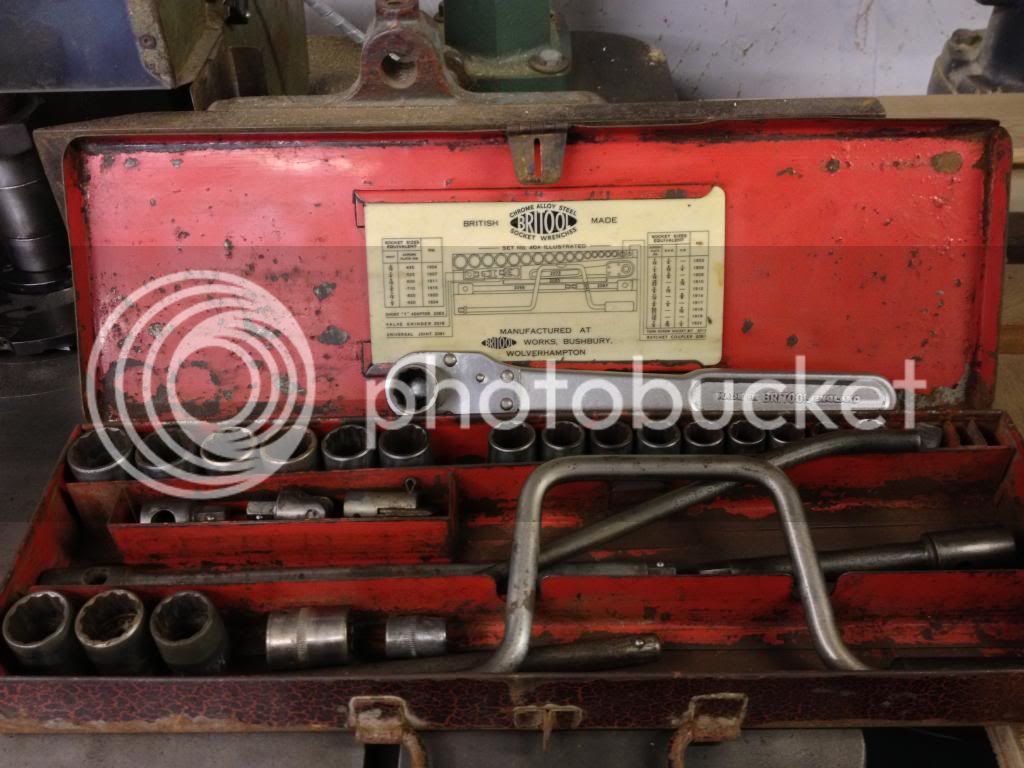