wallace
Established Member
Its been far too long since I did a machine so I thought I'd start with something simple to get me back into the swing of things.
I bought this a couple of years ago and its been sat under a tree.
As you can see its pretty crusty
But like most wadkin lumps they come to bits easily
Looks like its been cutting ali for a while
Just about stripped just need to get the turning table off, not sure how to do it yet so the best option is to sleep on it.
I bought this a couple of years ago and its been sat under a tree.
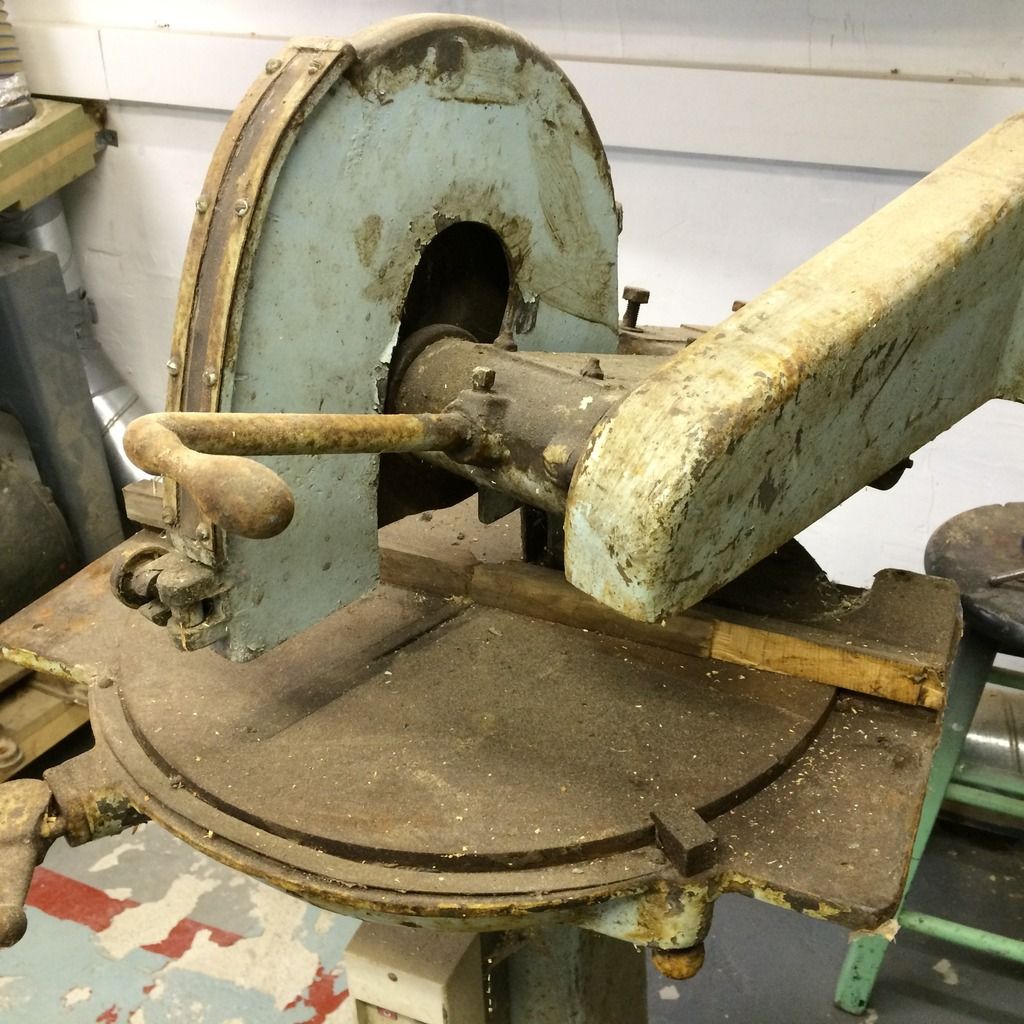
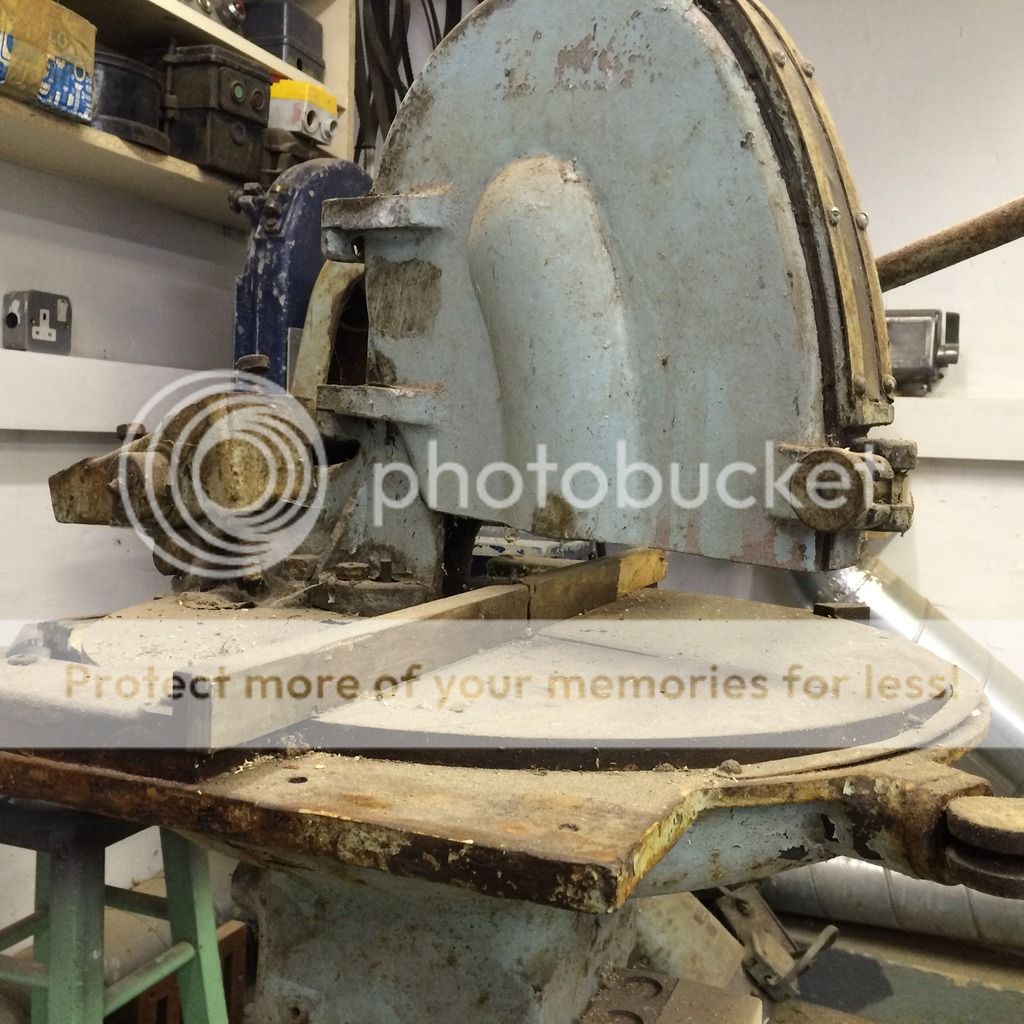
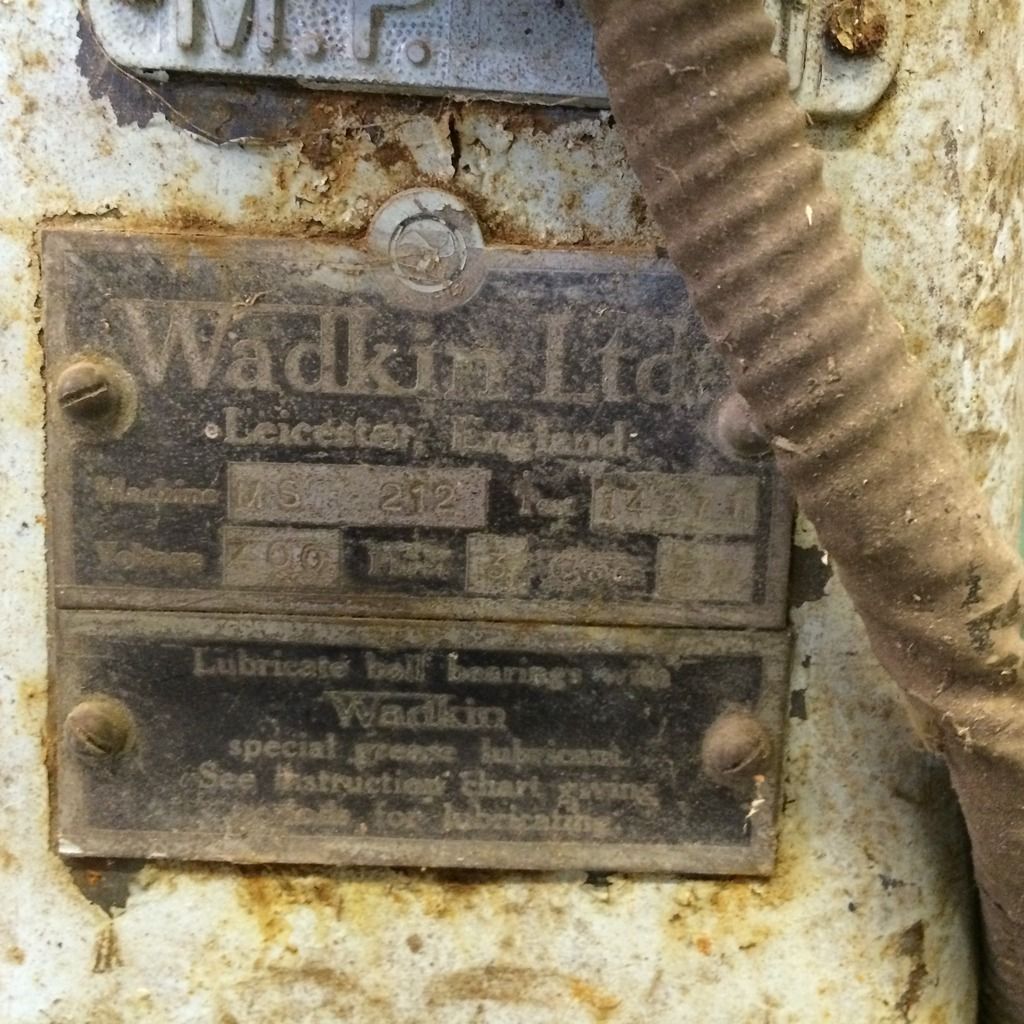
As you can see its pretty crusty
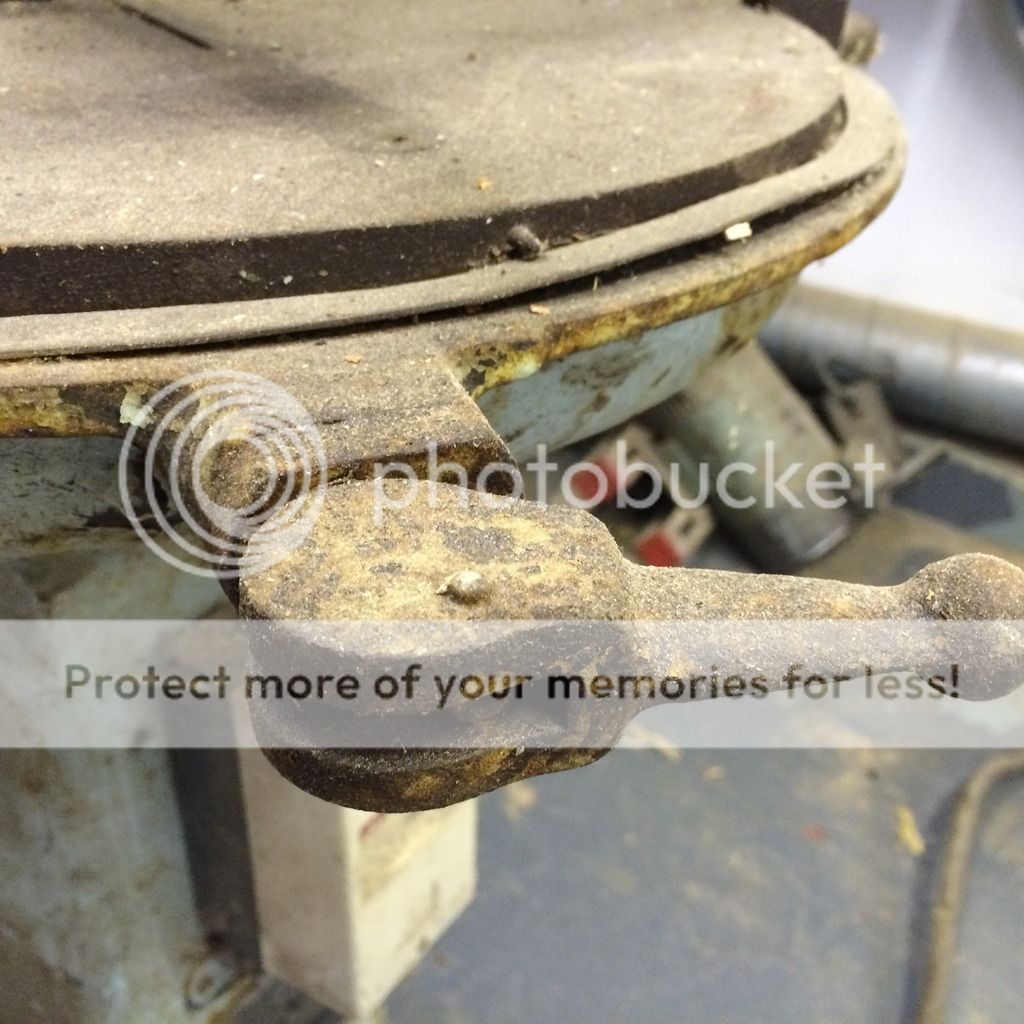
But like most wadkin lumps they come to bits easily
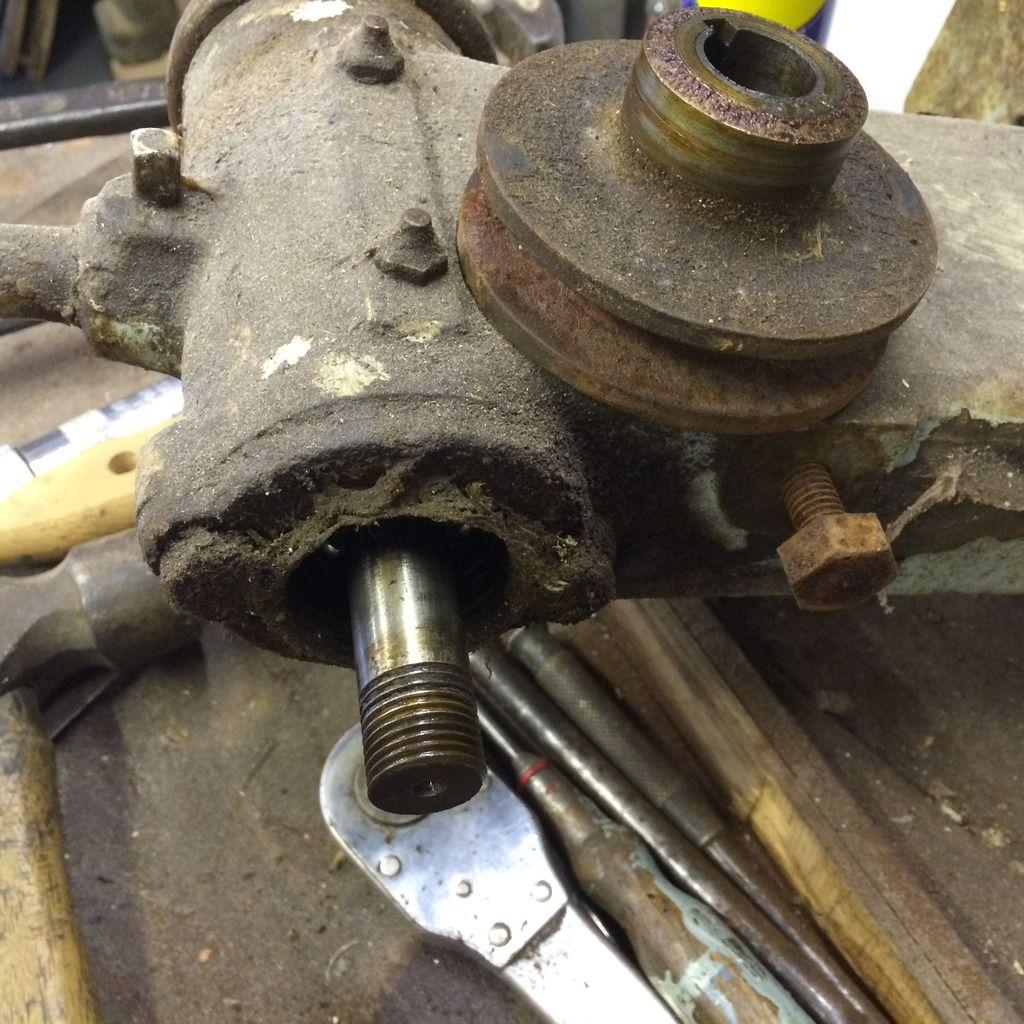
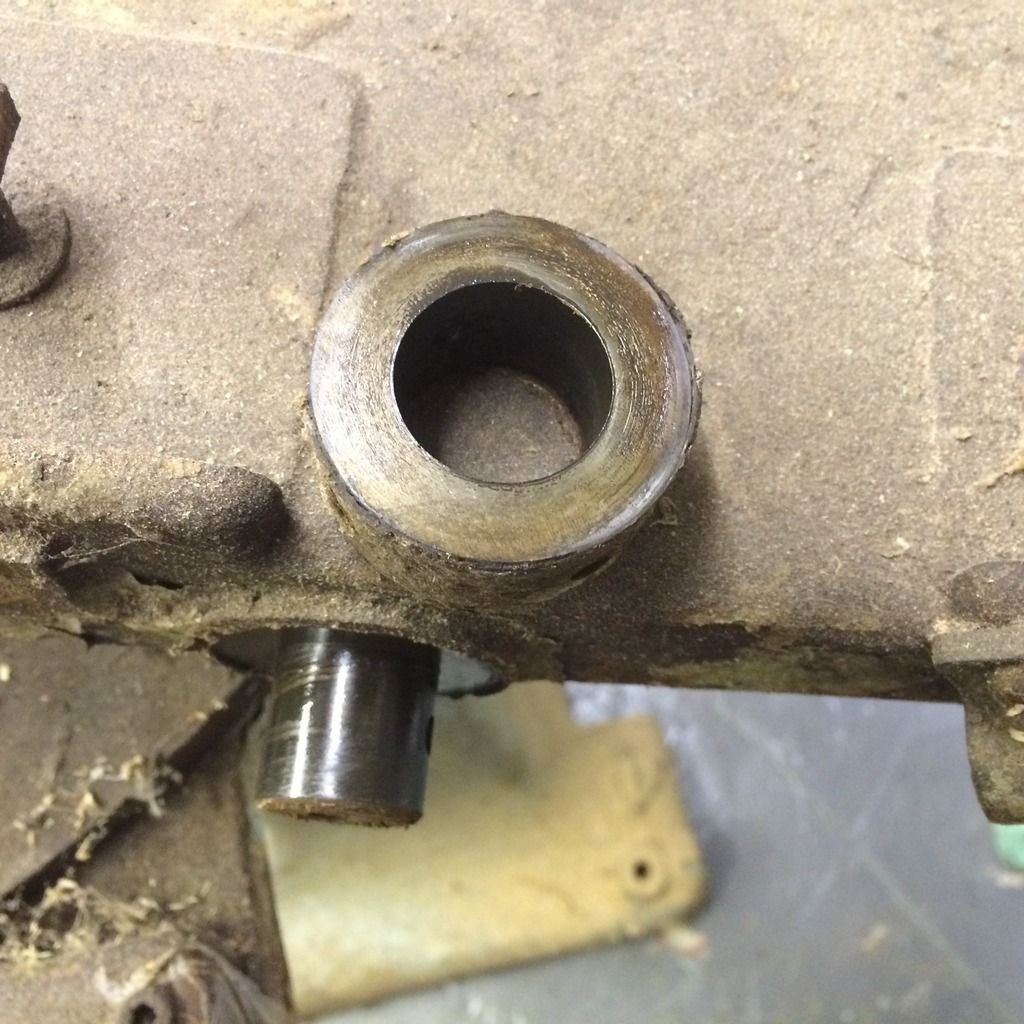
Looks like its been cutting ali for a while
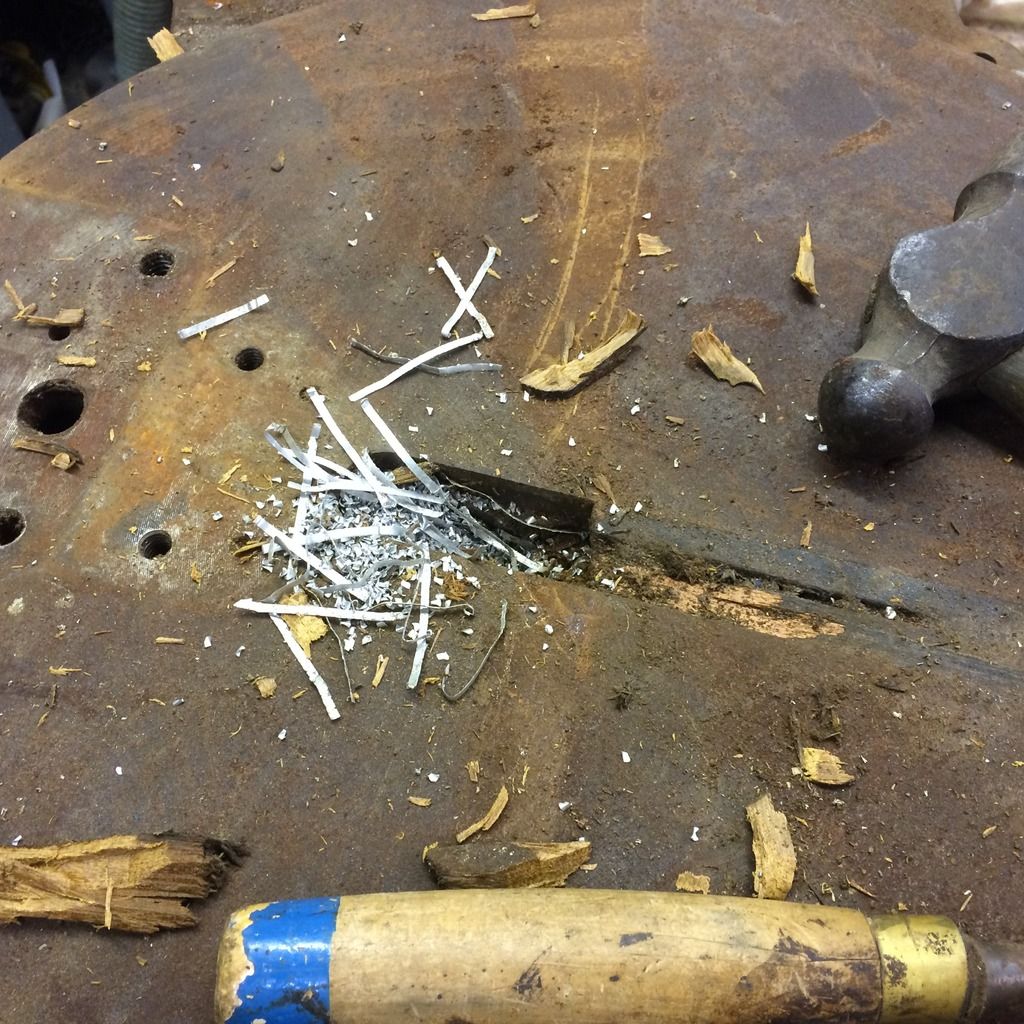
Just about stripped just need to get the turning table off, not sure how to do it yet so the best option is to sleep on it.
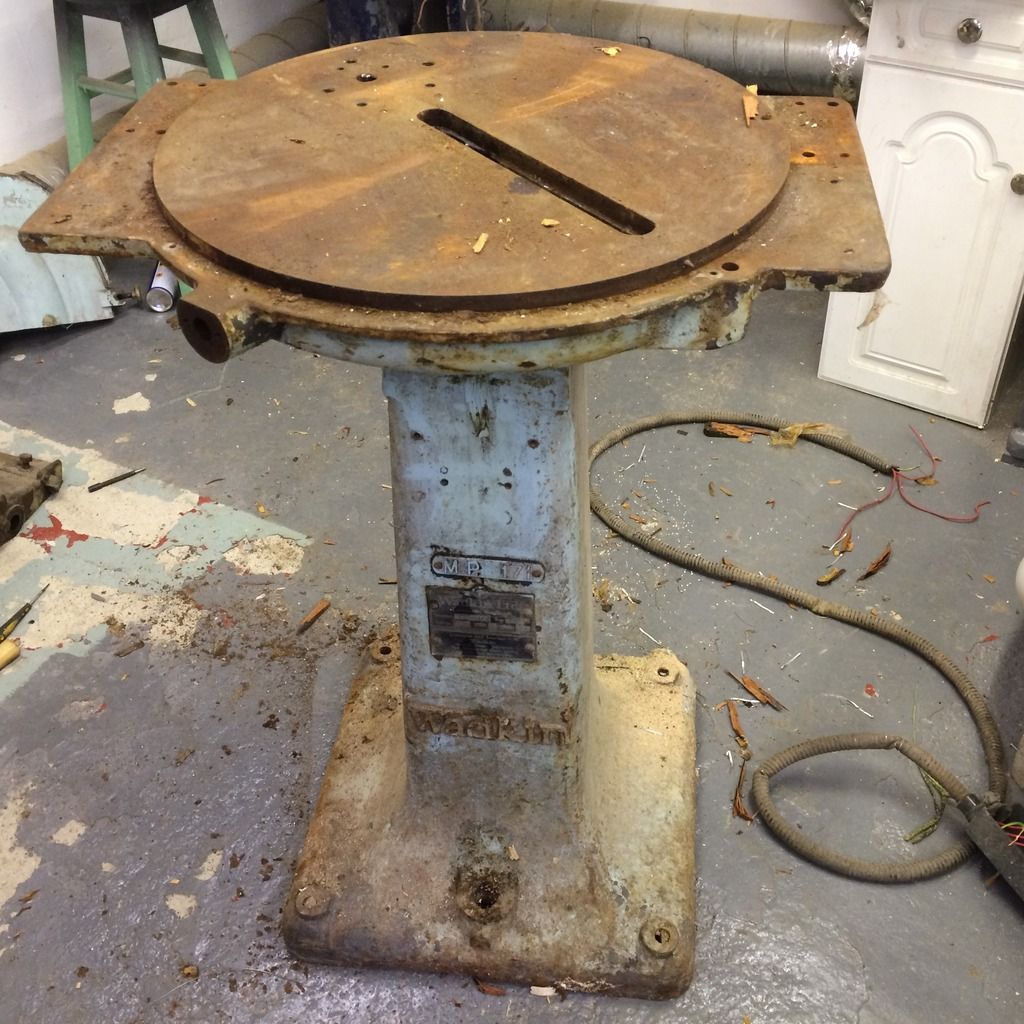
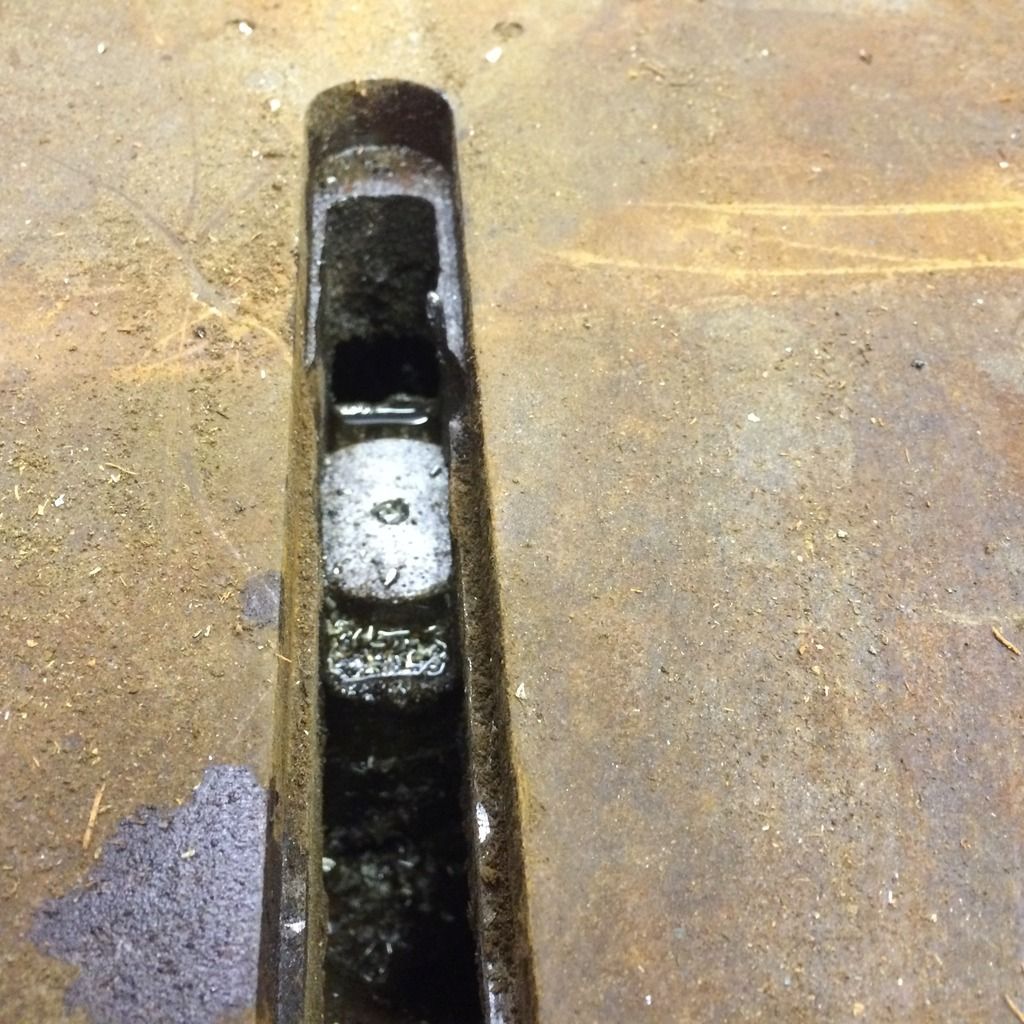