Ian
Established Member
Hi I was hoping someone might be able to help.
I have a frame veneering press, which has a suction hole at each end.
The bed is flat but when I veneer a panel and put a ruler across it looks like this at the ends (the ruler is pretty straight).
I do use a breather fabric
My thoughts are that with the suction being at its strongest at the outside the pressure in the centre of the panel would not be as strong.
Is this right?
If so what would be the solution?
I had thought of making a MDF cover with holes and channels to even this out
Underside view
Upper view
Your thoughts would be very much appreciated
Cheers
Ian
I have a frame veneering press, which has a suction hole at each end.
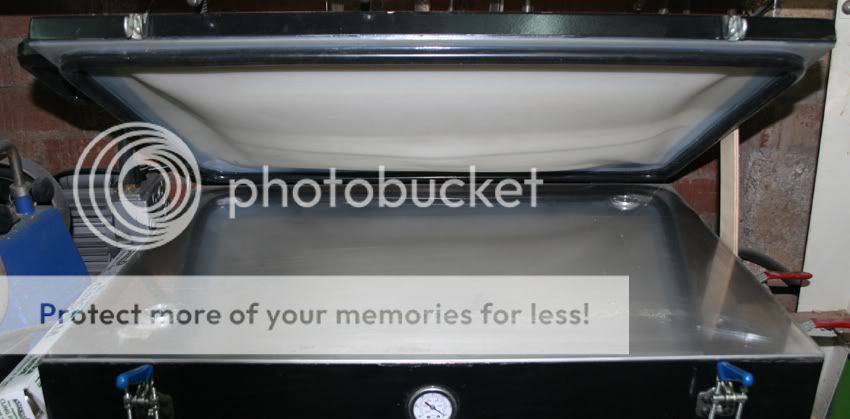
The bed is flat but when I veneer a panel and put a ruler across it looks like this at the ends (the ruler is pretty straight).

I do use a breather fabric
My thoughts are that with the suction being at its strongest at the outside the pressure in the centre of the panel would not be as strong.
Is this right?
If so what would be the solution?
I had thought of making a MDF cover with holes and channels to even this out
Underside view
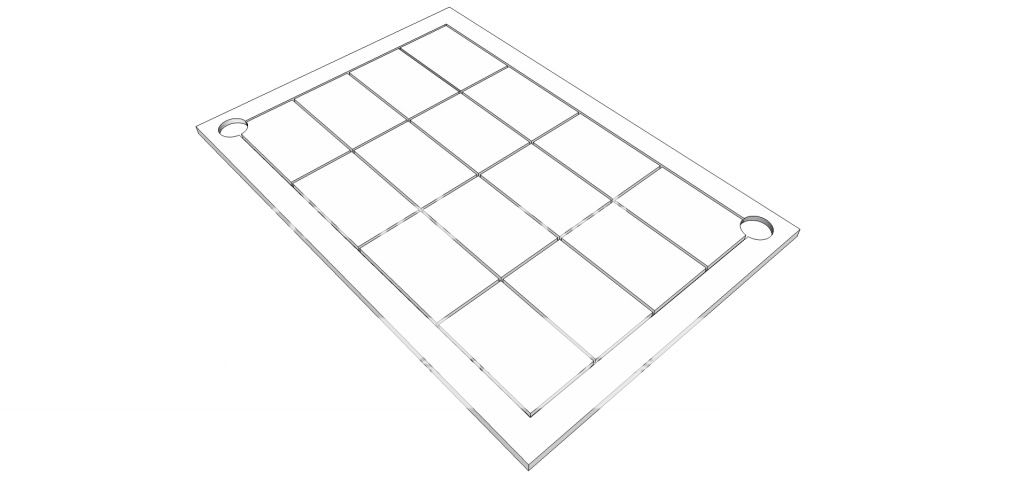
Upper view
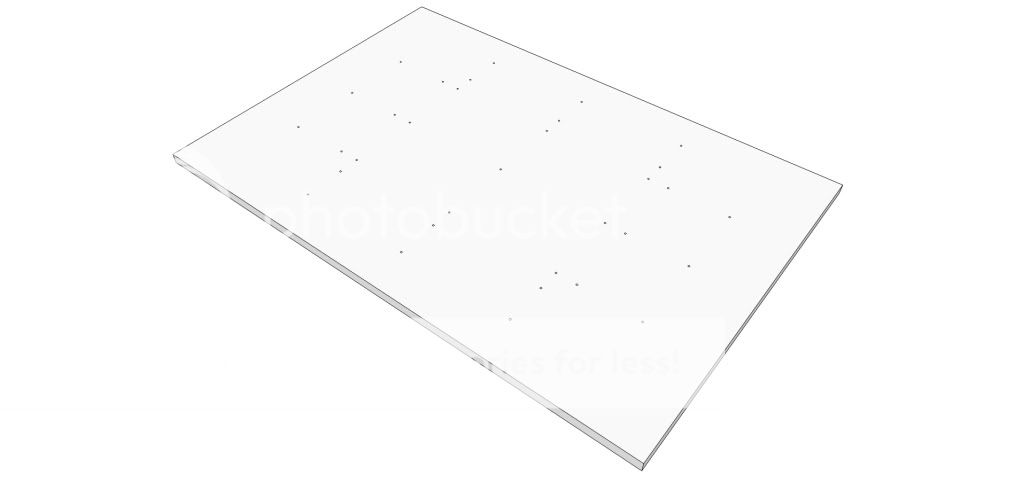
Your thoughts would be very much appreciated
Cheers
Ian