swagman
Established Member
Completed the following 7 inch; double iron smoother 2 days ago. The iron is bedded at 40 degrees; with a 1 degree right to left skew to induce more slicing action of the wood fibres. The body of the plane is made using east indian rosewood, and the wedge is made from merbeu. The mouth opening started off at 1mm, but I decided to increase that to around 2mm to allow the plane to pass a much heavier shaving without clogging. The wear was set at 80 degrees to the bottom line of the abutments (1/4 inch), with the remaining wear (3/4 inch) set at 85 degrees. The cutting edge of the iron has a primary bevel of approx. 24 degrees with a secondary at 25 degrees. The iron was sharpened to 1200 grit from the stone. The front of the chipbreaker was eyeballed to about 0.8mm from the cutting edge of the iron. Enough commentary; here are the photo's of the plane.
Stewie;
Stewie;
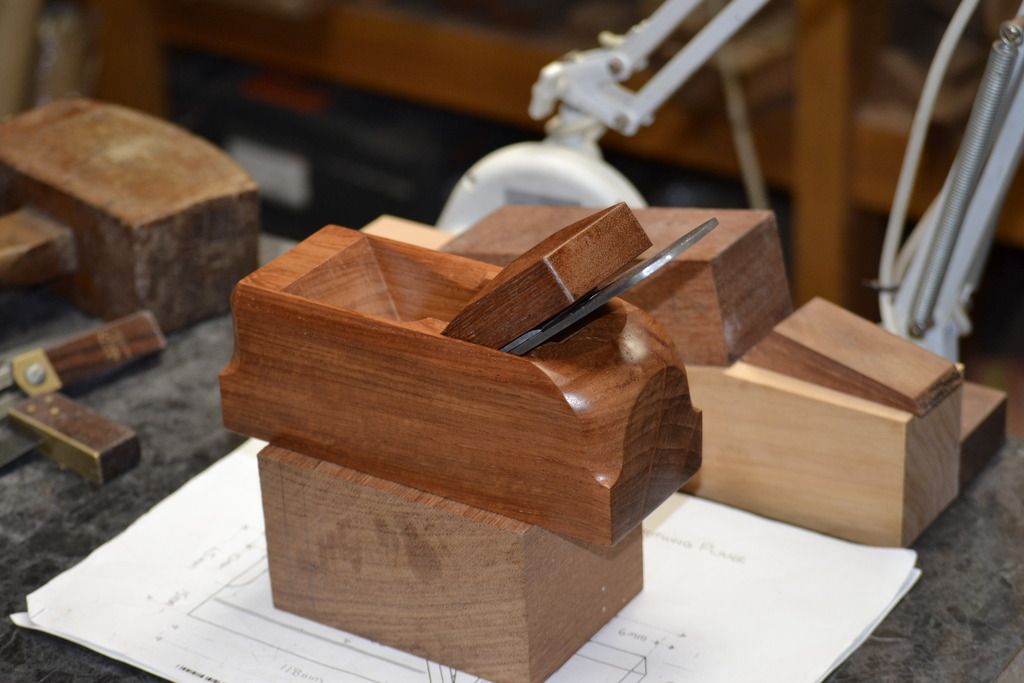
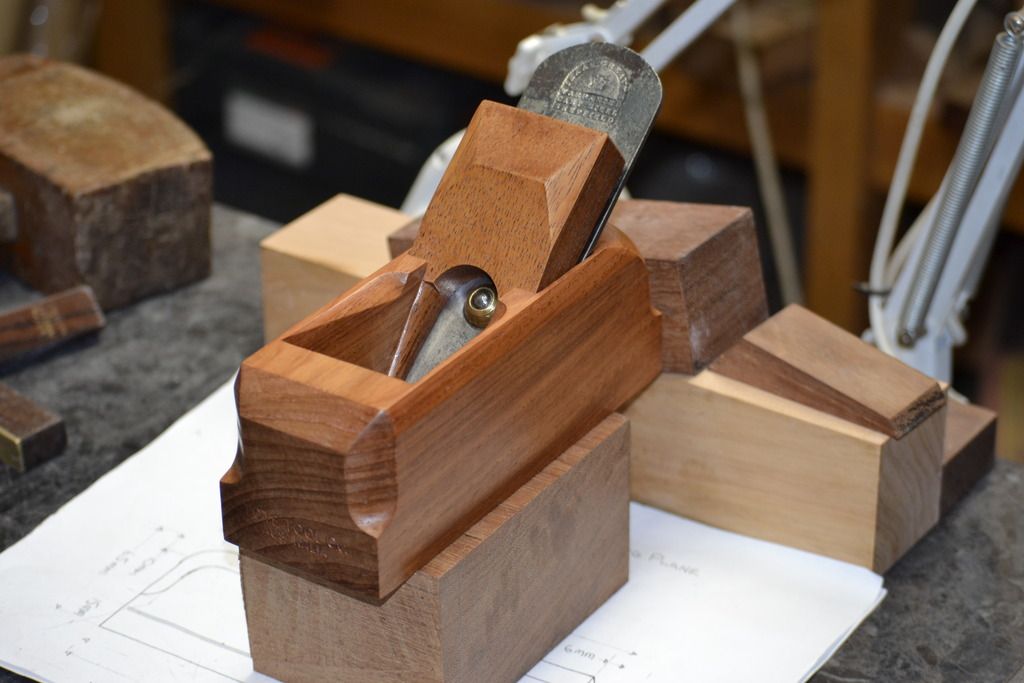
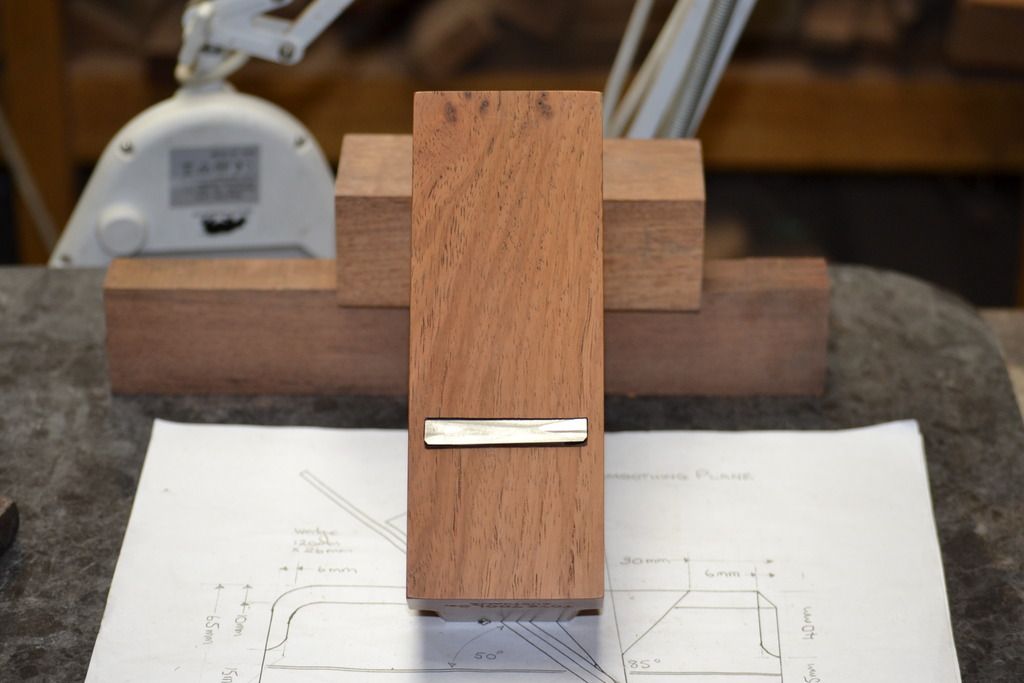