RobinBHM
Established Member
personally I would start by getting your routing process as accurate as possible -Im not sure what jig you imported -maybe you could improve on the accuracy by building your own -there a loads of linear guide rails now available for CNC making that are super accurate. If you built one with a lead screw and a stepper motor you could get it motorised -that would make the movement far more consistent.I think you are right, something rigid and more aggressive for this stage would be great. The top has to be super flat, resin flush with wood and even. If not, when the resin is polished at the final stage, it reflects light like a plastic window rather than a glass window if that makes sense, obscure reflections highlight concave areas.
If you can get the machining accuracy to around 0.2mm then you will have far less cleaning up to do....and you could do that without a CNC.
what tooling are you using?
something like this:
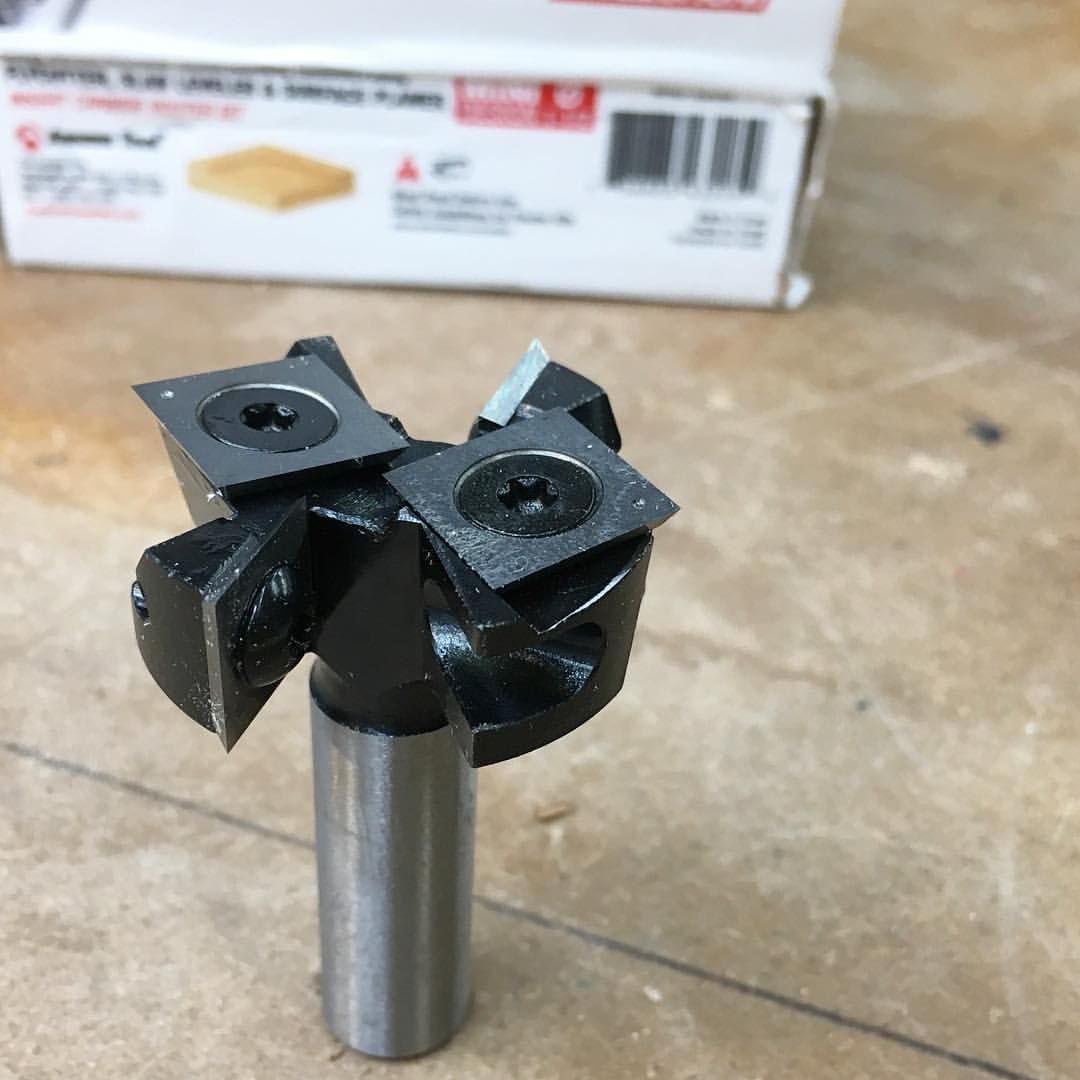
Wealdon tools sell a similar one
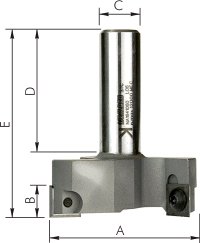
Last edited: