DavidE
Established Member
Hi there,
This weekend has been spent processing wood (resawing then thicknessing)... then making a frame. It's for a sound desk in a church, and is made from recycled pitch pine pew. It was the subject of a question a while back when I was having a dilemma over how to make a lid. In the end I have decided to go for a piano style lid. I appreciated the various thoughts people had on that as I was in a quandary.
Here's a sketch of the final product. (I have been working from SketchUp drawings and it has worked out spot on which was very pleasing. Is there an easy way of turning off the dimensions in SketchUp?
This is the frame tonight, it is constructed with mortice and tenons. with the exception of the top mitred joint (which is out of line as it is not clamped up - hopefully on the final glue up the panels will help keep things in line)
The next job is making the slots then raising the panels (which can be seen all glued up in the background). I shall add more photos as progress continues.
David
This weekend has been spent processing wood (resawing then thicknessing)... then making a frame. It's for a sound desk in a church, and is made from recycled pitch pine pew. It was the subject of a question a while back when I was having a dilemma over how to make a lid. In the end I have decided to go for a piano style lid. I appreciated the various thoughts people had on that as I was in a quandary.
Here's a sketch of the final product. (I have been working from SketchUp drawings and it has worked out spot on which was very pleasing. Is there an easy way of turning off the dimensions in SketchUp?
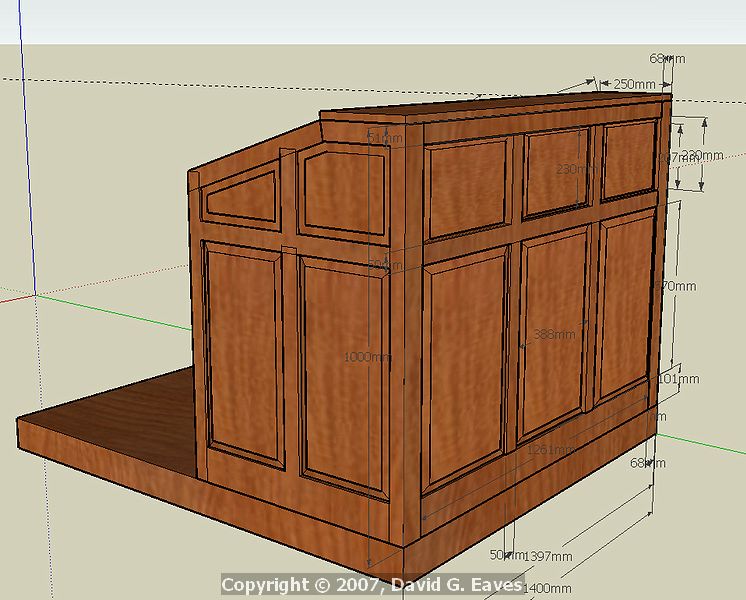
This is the frame tonight, it is constructed with mortice and tenons. with the exception of the top mitred joint (which is out of line as it is not clamped up - hopefully on the final glue up the panels will help keep things in line)
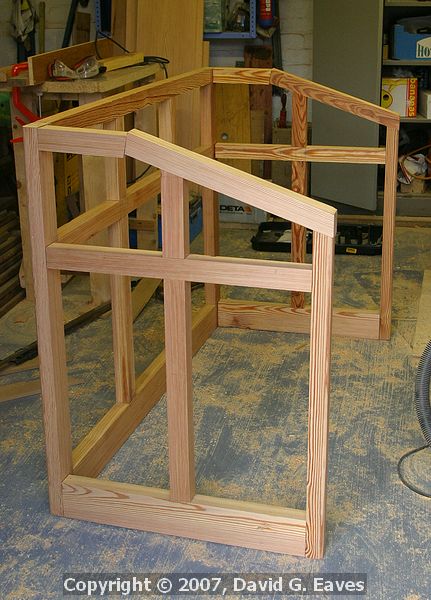
The next job is making the slots then raising the panels (which can be seen all glued up in the background). I shall add more photos as progress continues.
David