Derek Cohen (Perth Oz)
Established Member
This is where we finished last time - the fitting of legs to the apron ...
I had a day in the workshop, and the following is a summary of the work completed today.
The aim was to make and fit the end rails for the table. I decided to use sliding dovetails rather than mortice-and-tenons: There was little room to add a tenon as much of the space in the legs was taken up with large tenons from the aprons (although working with the 1/3 Rule). A sliding dovetail would provide a compact joint.
A few hours were first spent aligning the aprons and legs. The legs had been cut from the centre of a board, to obtain the best grain arrangement. As a result, there were no registration sides. A degree here-or-there difference in the legs threw off their alignment. Tweaking them into parallel took some time.
The ends of the table are different. On one side is a solid stretcher. At the other end are top- and lower rails for a drawer. These are below along with the drawer face, which will resemble a stretcher once completed (it is to be a hidden drawer, disguised as a stretcher) ...
The rails went in this end ...
All is loosely fitted for these photos. Drawbore pegs lock the legs to the apron. The lower rail is actually locked by the apron ...
There is nothing special about the sliding dovetail on the lower rails. They are short and, therefore, were left parallel ..
The top rail is simply dovetailed in ...
The top rail is 10mm high and the lower rail is 20mm high. This leaves 39mm for a drawer. No, it is not going to be high! Still, it is part of the fun, and no doubt will be a interesting talking point and find a use.
At the other end of the table is a solid stretcher. If you look at the left side leg, you will notice that the top of the mortice has broken out. This was caused by attempts to unstick a peg - which I thought was tapped in lightly, but broke off when I tried to twist it out (damn!). After this, I kept it all loose.
This stretcher has a tapered sliding dovetail at each side ...
All of the sockets were marked, sawn and chiselled.
The dovetails were planed with a modified Stanley #79 side rabbet plane. The modification involved an angled fence ...
Finally, this is where I am up to with the sofa table. The front legs need to be rounded, and all the legs are yet to be tapered on the insides. There is clean up to do, a drawer to build, and the tabletop to resaw and shape.
Regards from Perth
Derek
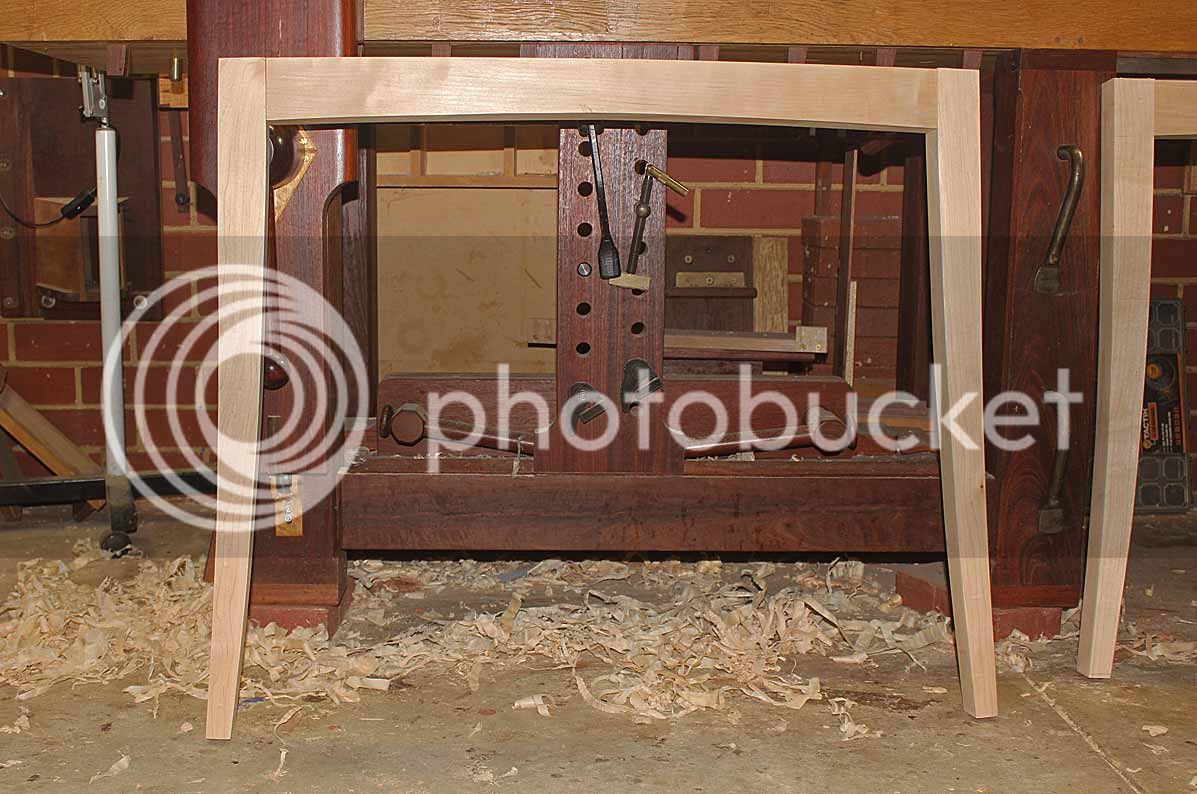
I had a day in the workshop, and the following is a summary of the work completed today.
The aim was to make and fit the end rails for the table. I decided to use sliding dovetails rather than mortice-and-tenons: There was little room to add a tenon as much of the space in the legs was taken up with large tenons from the aprons (although working with the 1/3 Rule). A sliding dovetail would provide a compact joint.
A few hours were first spent aligning the aprons and legs. The legs had been cut from the centre of a board, to obtain the best grain arrangement. As a result, there were no registration sides. A degree here-or-there difference in the legs threw off their alignment. Tweaking them into parallel took some time.
The ends of the table are different. On one side is a solid stretcher. At the other end are top- and lower rails for a drawer. These are below along with the drawer face, which will resemble a stretcher once completed (it is to be a hidden drawer, disguised as a stretcher) ...

The rails went in this end ...
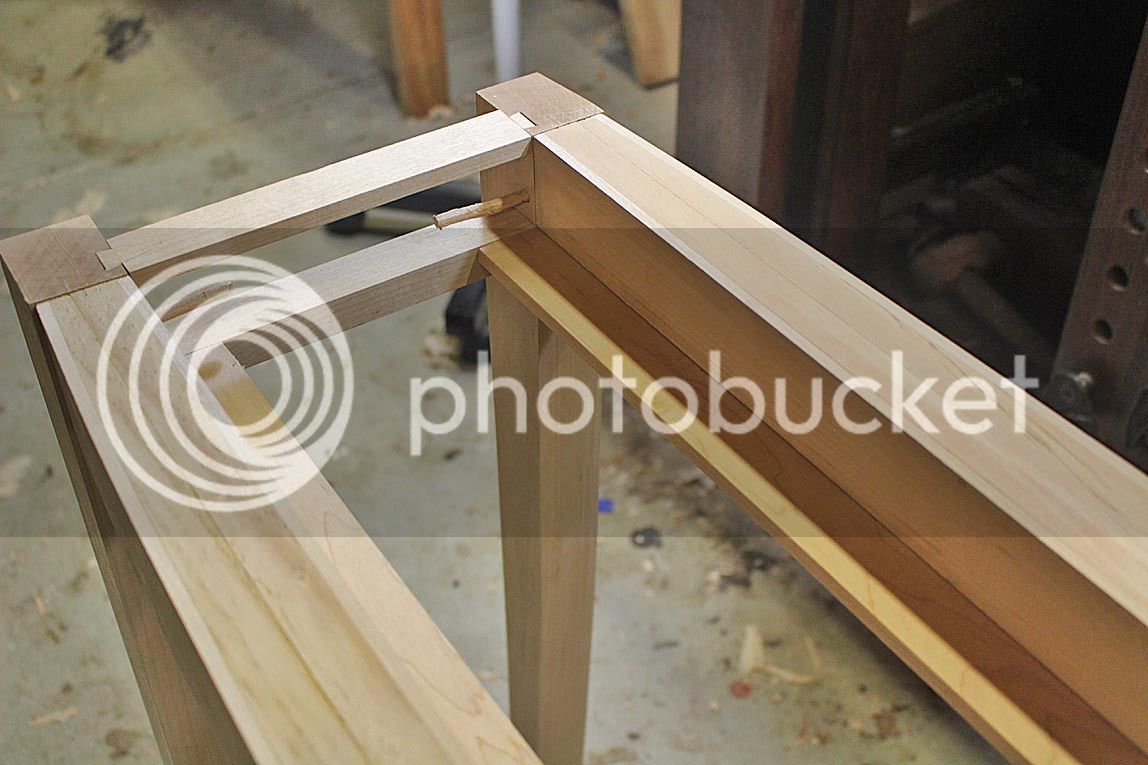
All is loosely fitted for these photos. Drawbore pegs lock the legs to the apron. The lower rail is actually locked by the apron ...
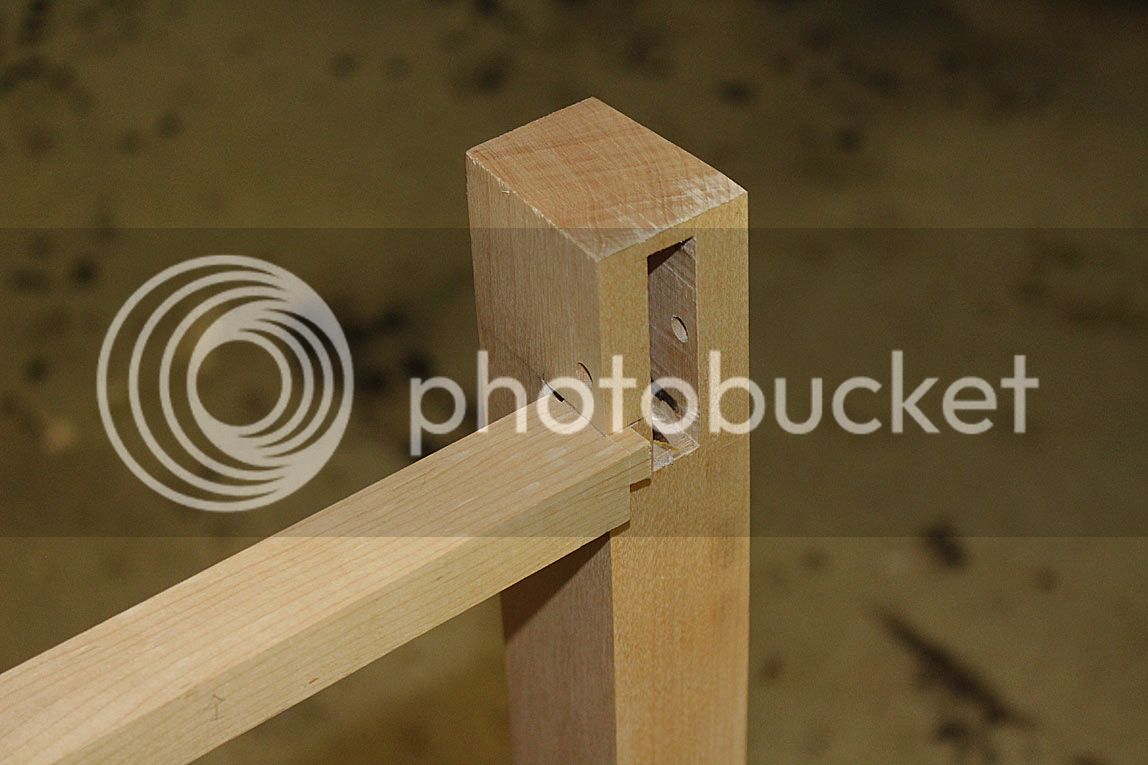
There is nothing special about the sliding dovetail on the lower rails. They are short and, therefore, were left parallel ..
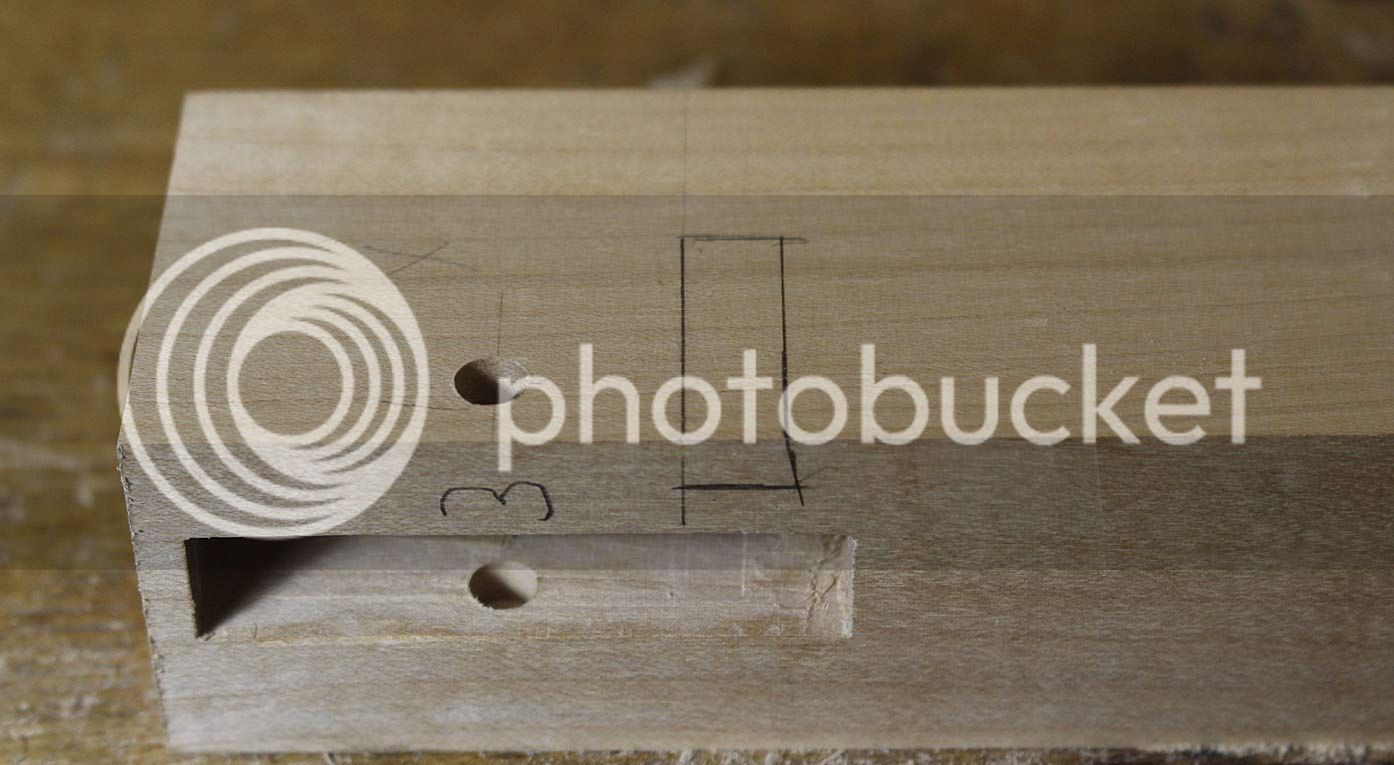
The top rail is simply dovetailed in ...
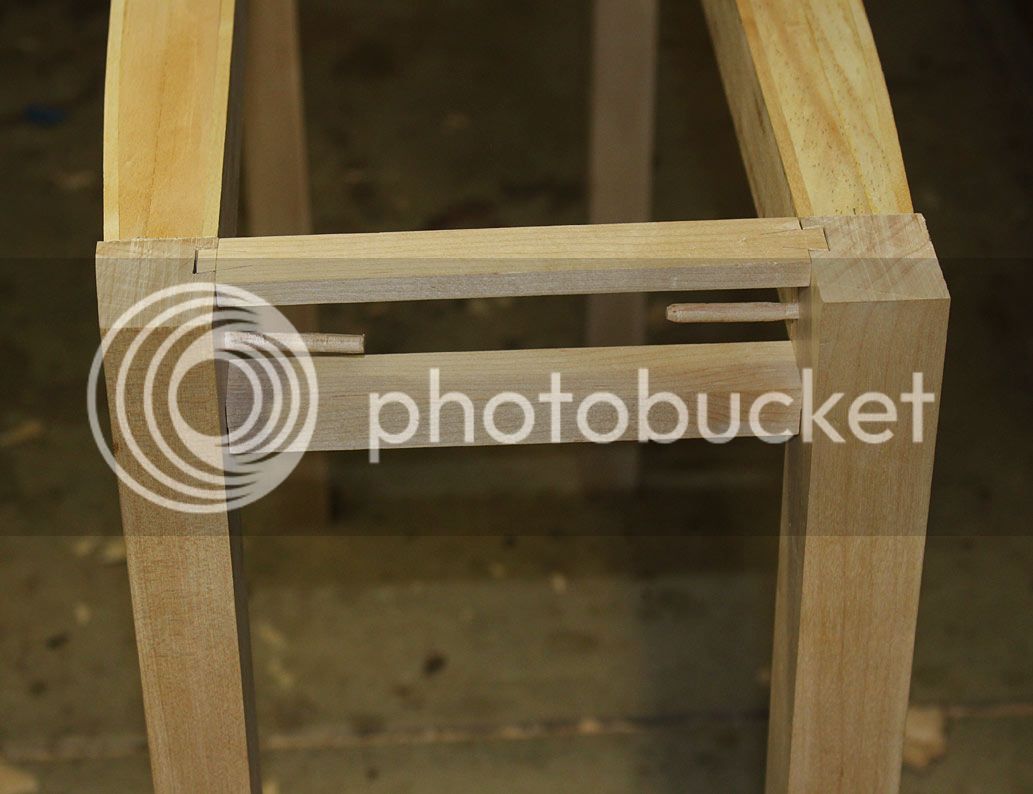
The top rail is 10mm high and the lower rail is 20mm high. This leaves 39mm for a drawer. No, it is not going to be high! Still, it is part of the fun, and no doubt will be a interesting talking point and find a use.
At the other end of the table is a solid stretcher. If you look at the left side leg, you will notice that the top of the mortice has broken out. This was caused by attempts to unstick a peg - which I thought was tapped in lightly, but broke off when I tried to twist it out (damn!). After this, I kept it all loose.
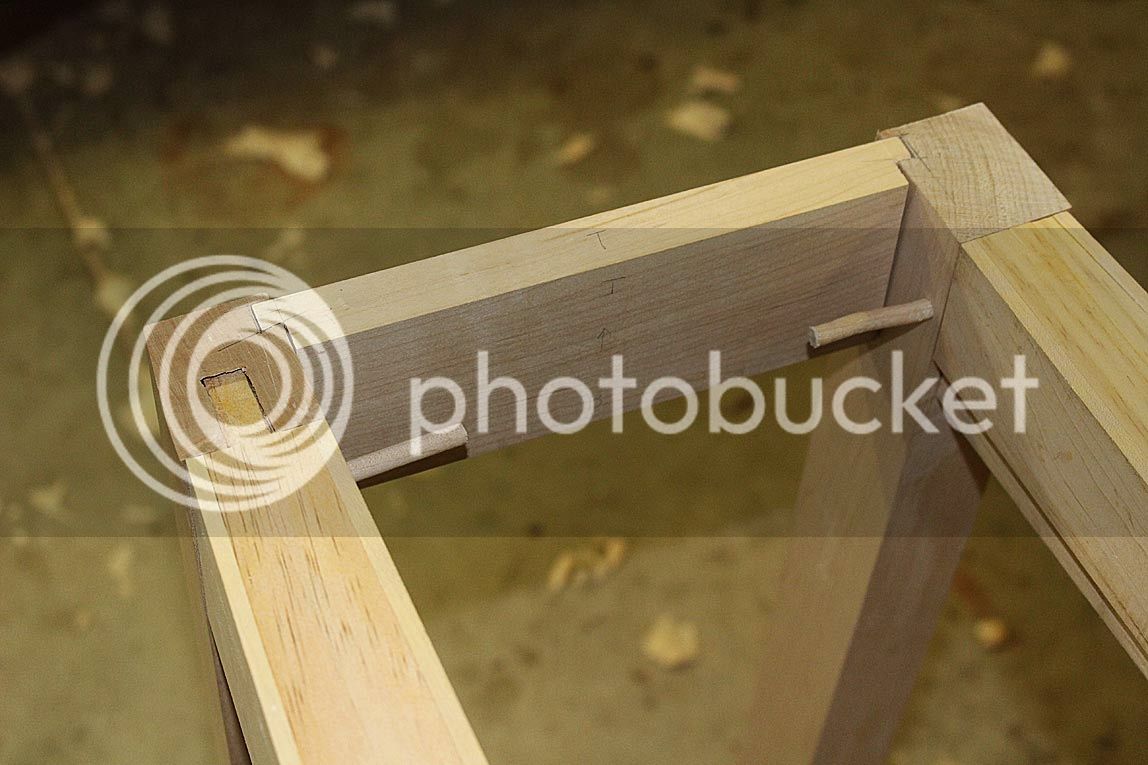
This stretcher has a tapered sliding dovetail at each side ...
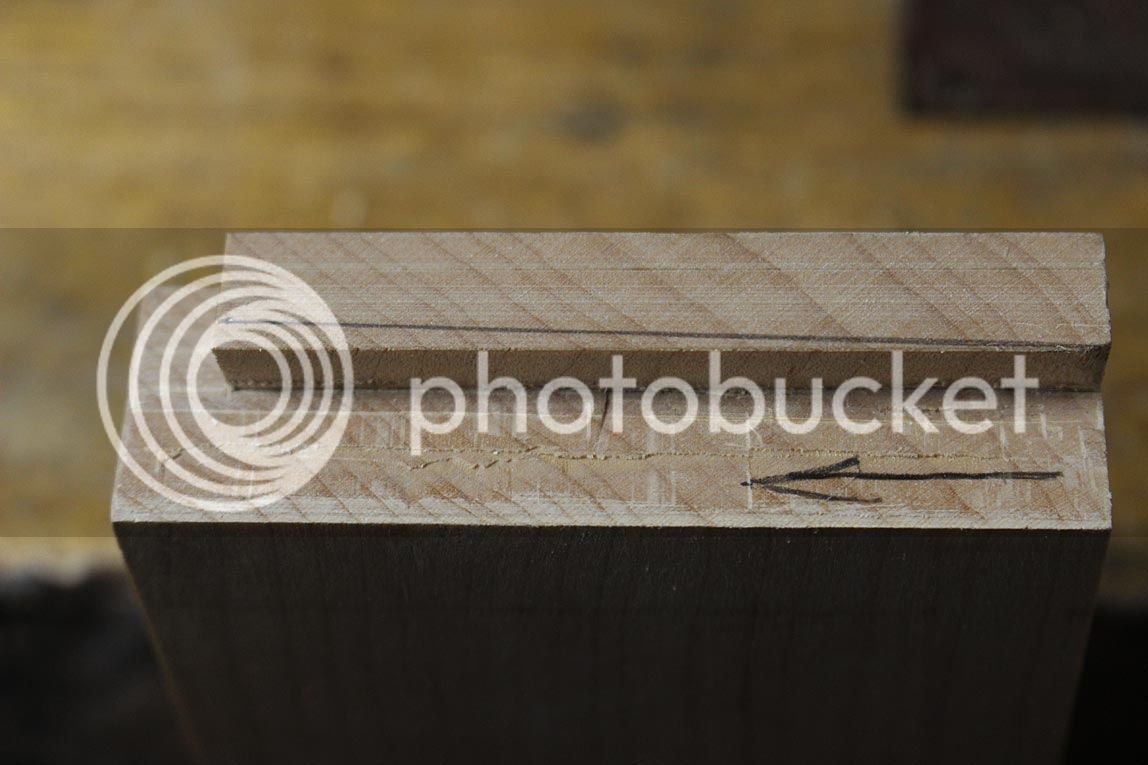
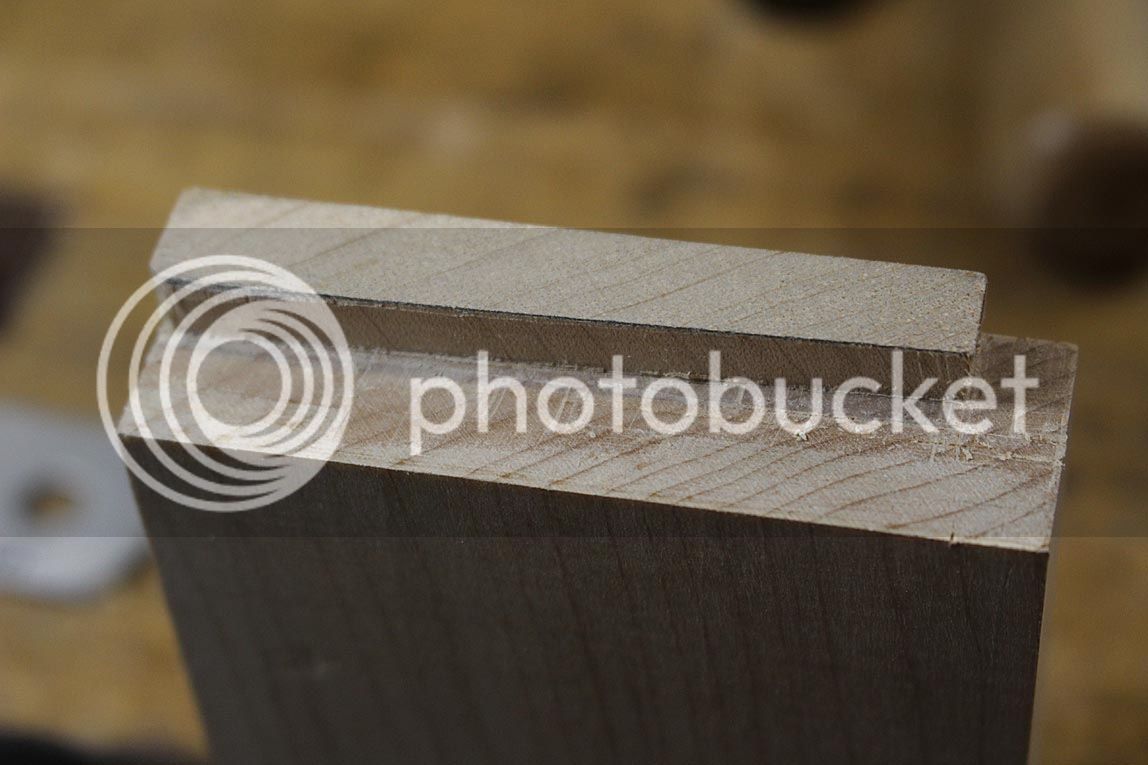
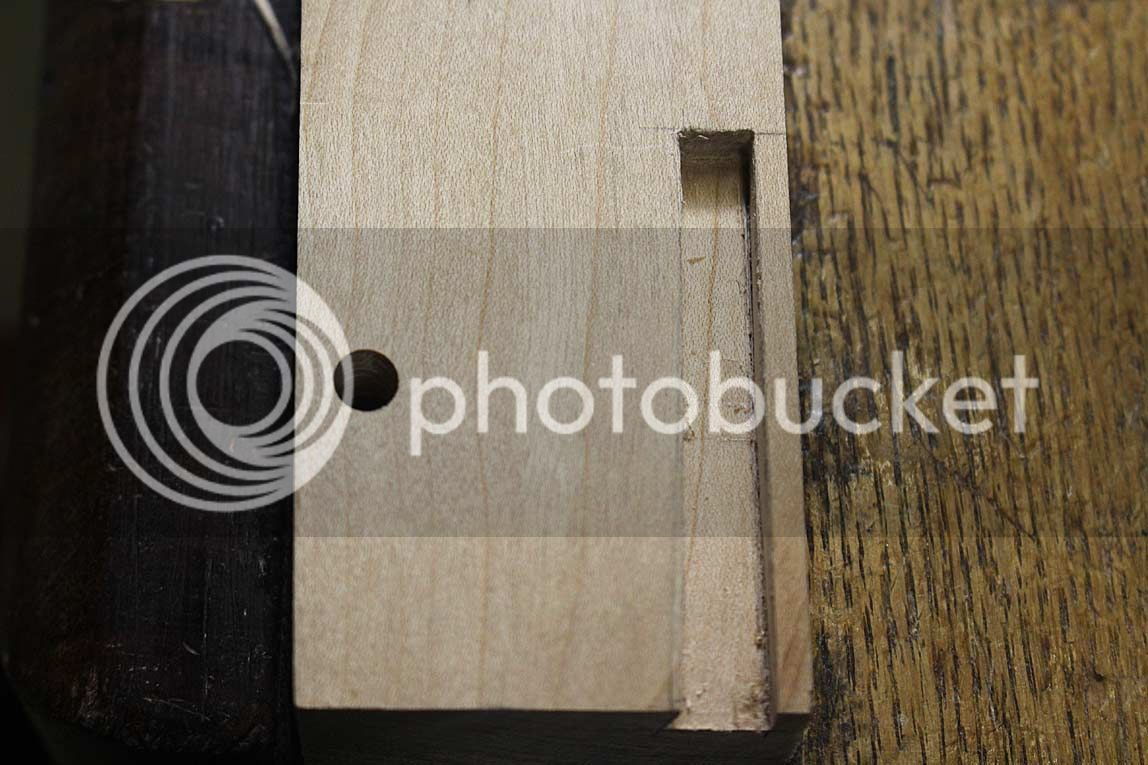
All of the sockets were marked, sawn and chiselled.
The dovetails were planed with a modified Stanley #79 side rabbet plane. The modification involved an angled fence ...
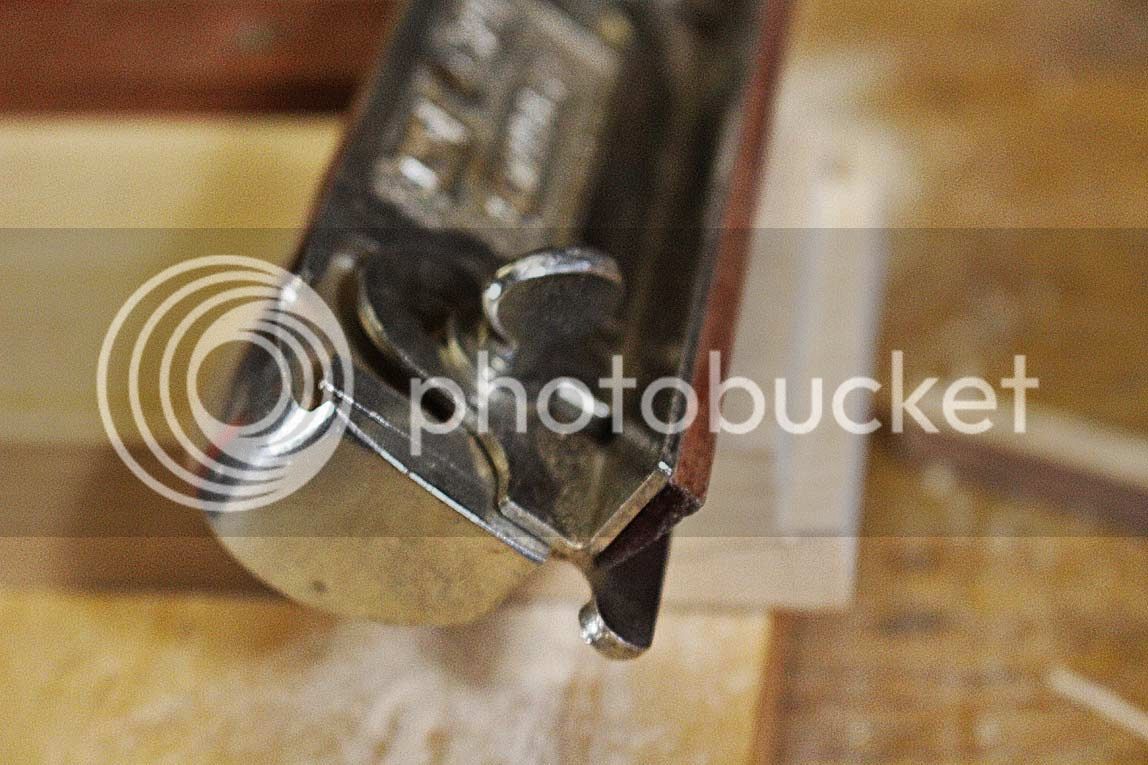
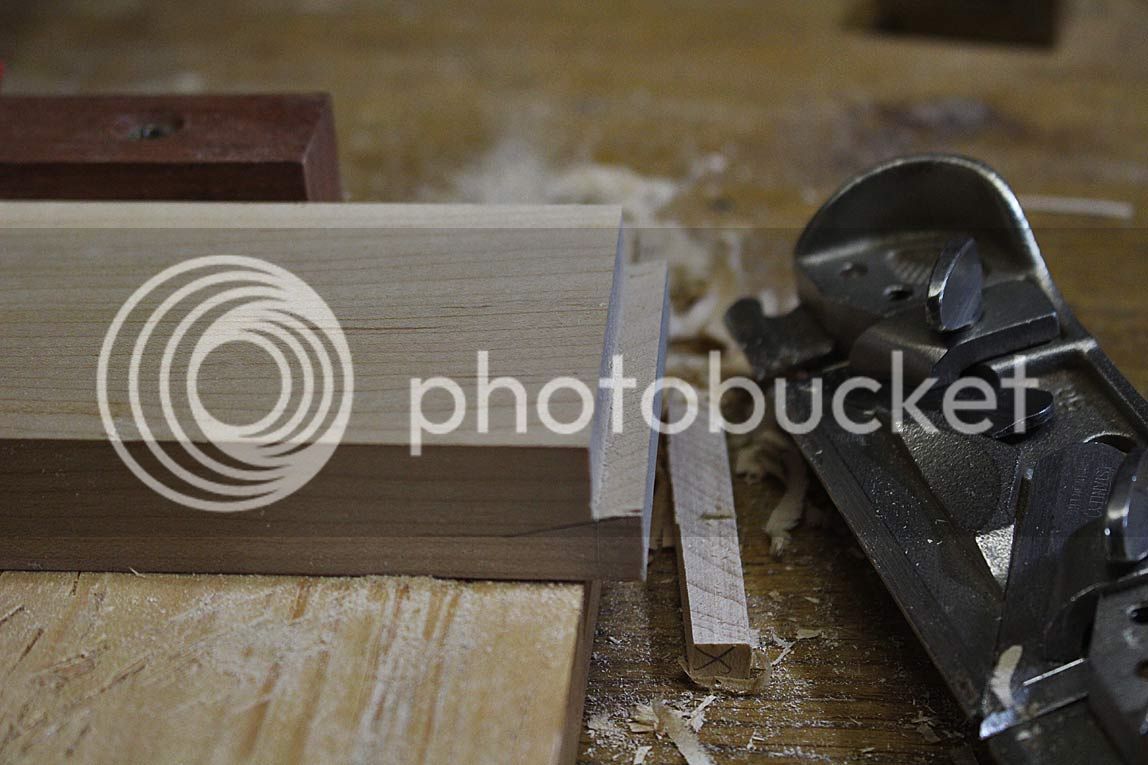

Finally, this is where I am up to with the sofa table. The front legs need to be rounded, and all the legs are yet to be tapered on the insides. There is clean up to do, a drawer to build, and the tabletop to resaw and shape.
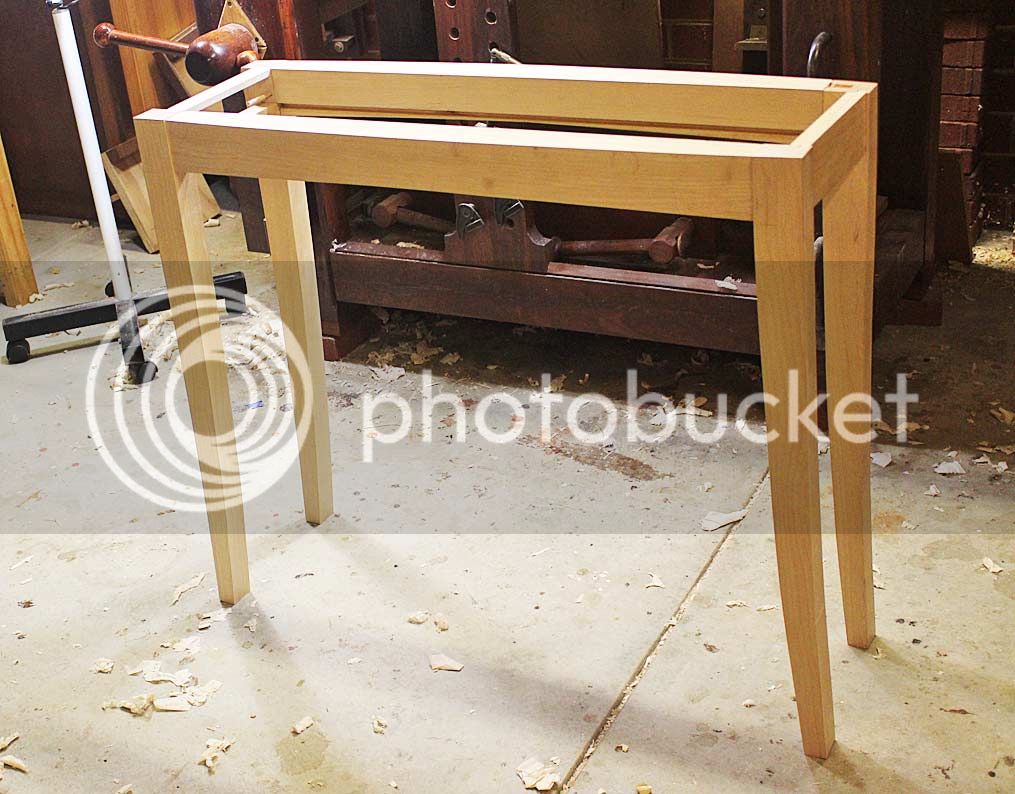
Regards from Perth
Derek