sploo
Somewhat extinguished member
Some years ago I installed a kitchen in our house, using solid oak worktops. On top of the cabinets I have a pair of small speakers made to a Zaph Audio design (http://www.zaphaudio.com/audio-speaker18.html).
The speakers are just rough boxes in MDF, and I'd always planned to use some of the remaining worktop material to make matching speakers. Better late than never I guess.
I ripped up a few sections to the rough sizes I needed, and used a marking gauge to help guide where I'd need to split the ~38mm thick material:
Because of the size and hardness of the material, I decided to try to reduce the load on my bandsaw by taking a series of shallow cuts over the table saw first. It's not a particularly smart thing to do, but I took a number of precautions: using a short but tall fence, a tall featherboard (before the blade), push sticks, and standing to the side of machine.
On this part you can see the small ridge left that was then cut with the bandsaw (the dark section is actually the colour of that bit of wood - it's not a burn):
Some of the parts were too wide for my bandsaw, so once finished on the tablesaw I had to cut them by hand:
Because there was a fair bit of stock, and I really need them to be very consistent in thickness, I put them through my thicknesser (as opposed to hand planing). Here are what will be the side panels:
The drivers I'm using require a 71mm hole and a 90mm rebate for the flange. I couldn't find my circle cutting jig for my old router (the one not in the router table), so I decided to fire up the CNC for the first time in ages, and cut a circle jig (for a 30mm guide bush):
After a couple of tests on some scrap, I found the 71.5mm hole resulted in the best fit (with a rebate bit cutting a 9.5mm wide rebate afterwards). Template lined up (with some scrap underneath to protect my bench):
And the hole cut out:
Front/top/bottom panels (you can see the rebate bit in the router table to the left):
These small drivers really require a chamfer on the rear of the baffle to allow them to "breath", so I then did that on the router table too:
I then ran a 3mm deep rebate along the lengths of the top and bottom panels (not photographed) and loosely put the sides/top/bottom and front baffle together (with the speaker on its side):
The stock is 15mm thick, and the 3mm rebate on the top/bottom panels (left/right in the photo above) is 16mm wide. This is so the edges overhang by ~1mm and can be trimmed off after glueing, for a perfect joint. The front baffle is the same width (and also over-tall) so it overhangs by ~1mm all round; again for trimming after glueing.
There's currently no rebate on the rear of the front baffle - something I'd usually do. I may add a shallow one to just help the seal to the box when glueing. This would reduce the internal volume slightly, but I've allowed for it in the cabinet depth.
Lots still to do - fixing some dampening material to the insides, cutting the rear panels (and making some fixings so they can be removed), glueing, trimming, roundovers, finishing. It may be a while before I get time to progress them but I'll post again when I do.
On a final note: solid wood and loudspeaker cabinets isn't actually a great combination (wood movement vs the need for no air leaks); hence the reason boxes are usually constructed from man made boards, and painted or veneered. With luck I'll get away with it on these boxes, as they're pretty small.
The speakers are just rough boxes in MDF, and I'd always planned to use some of the remaining worktop material to make matching speakers. Better late than never I guess.
I ripped up a few sections to the rough sizes I needed, and used a marking gauge to help guide where I'd need to split the ~38mm thick material:
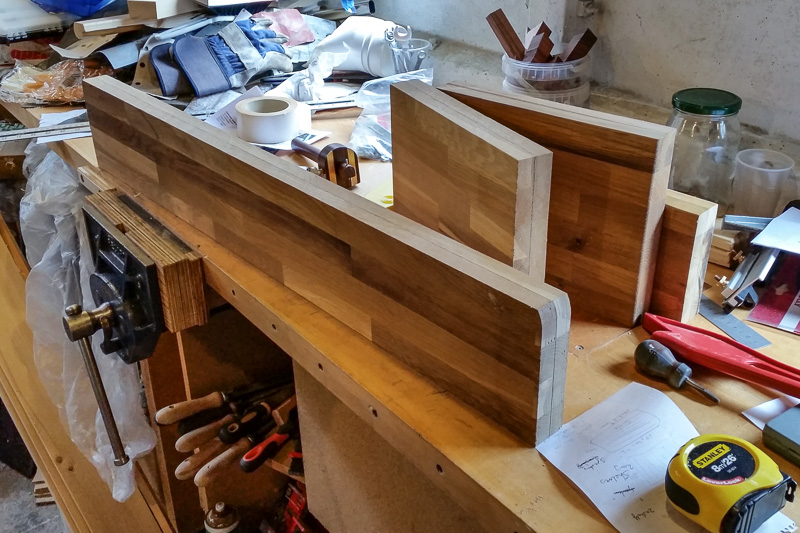
Because of the size and hardness of the material, I decided to try to reduce the load on my bandsaw by taking a series of shallow cuts over the table saw first. It's not a particularly smart thing to do, but I took a number of precautions: using a short but tall fence, a tall featherboard (before the blade), push sticks, and standing to the side of machine.
On this part you can see the small ridge left that was then cut with the bandsaw (the dark section is actually the colour of that bit of wood - it's not a burn):
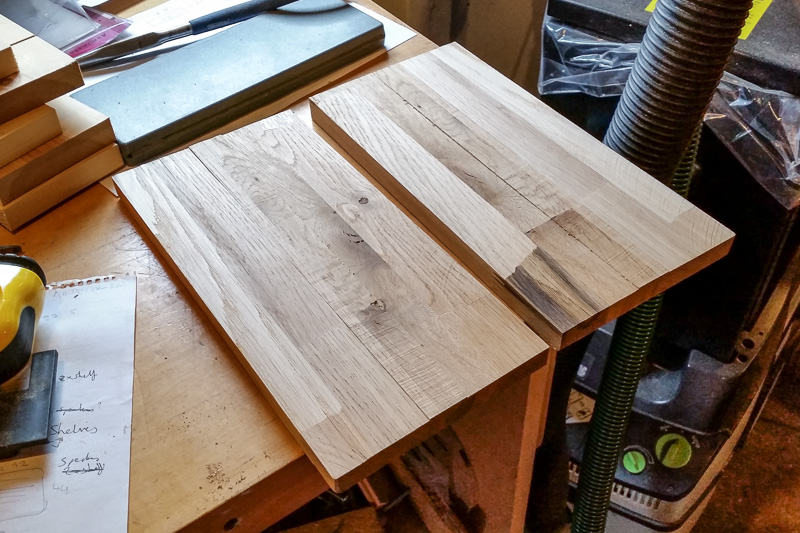
Some of the parts were too wide for my bandsaw, so once finished on the tablesaw I had to cut them by hand:
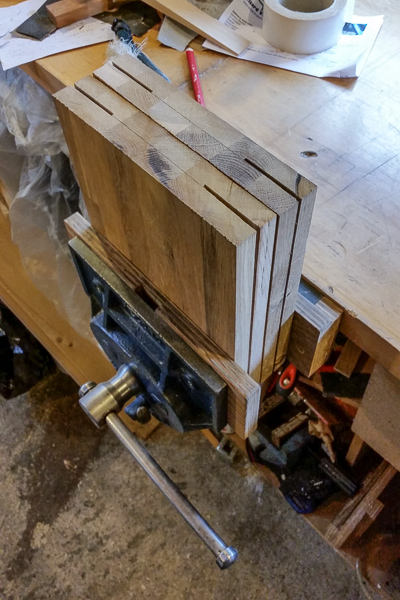
Because there was a fair bit of stock, and I really need them to be very consistent in thickness, I put them through my thicknesser (as opposed to hand planing). Here are what will be the side panels:
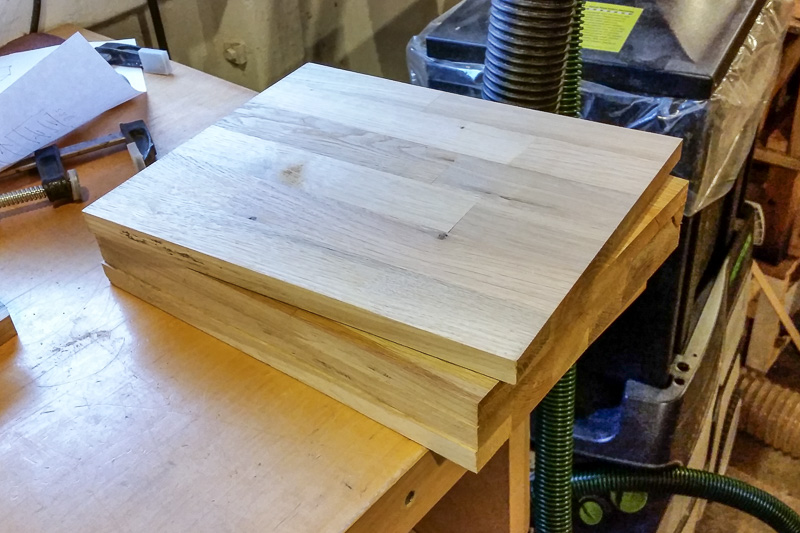
The drivers I'm using require a 71mm hole and a 90mm rebate for the flange. I couldn't find my circle cutting jig for my old router (the one not in the router table), so I decided to fire up the CNC for the first time in ages, and cut a circle jig (for a 30mm guide bush):
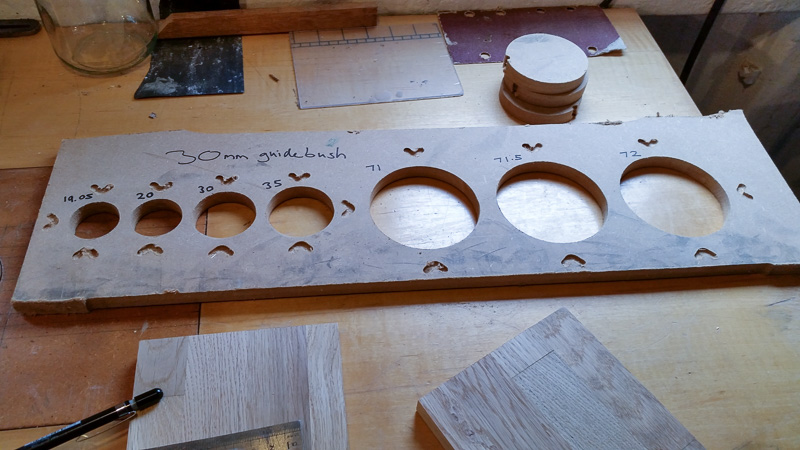
After a couple of tests on some scrap, I found the 71.5mm hole resulted in the best fit (with a rebate bit cutting a 9.5mm wide rebate afterwards). Template lined up (with some scrap underneath to protect my bench):
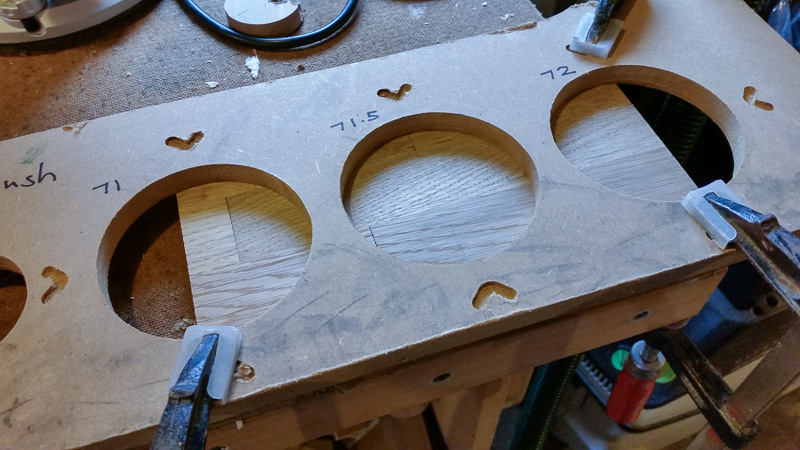
And the hole cut out:
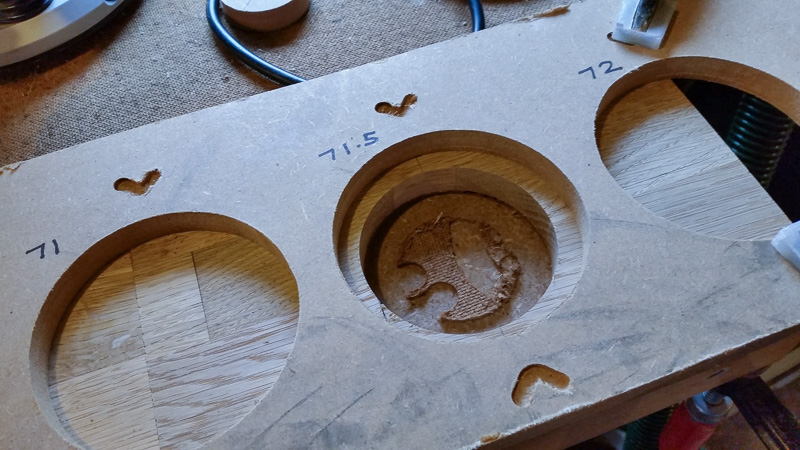
Front/top/bottom panels (you can see the rebate bit in the router table to the left):
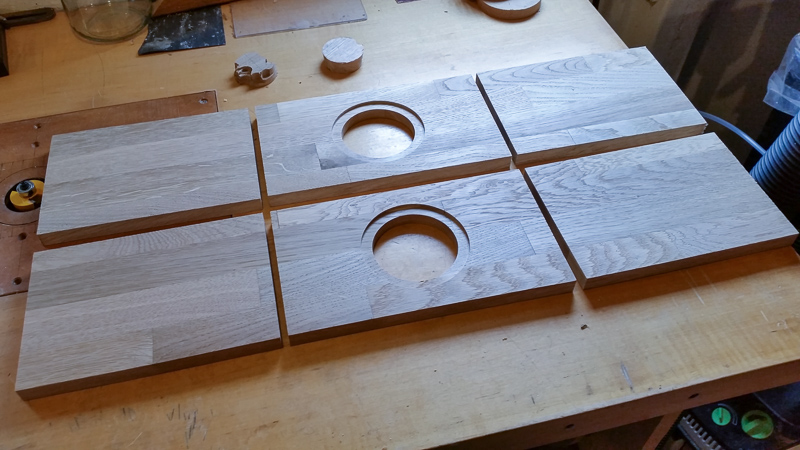
These small drivers really require a chamfer on the rear of the baffle to allow them to "breath", so I then did that on the router table too:
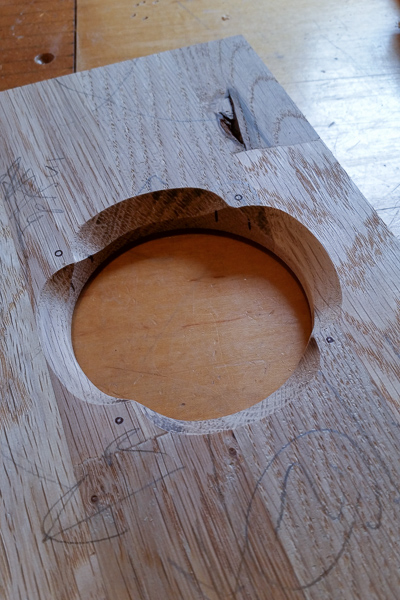
I then ran a 3mm deep rebate along the lengths of the top and bottom panels (not photographed) and loosely put the sides/top/bottom and front baffle together (with the speaker on its side):
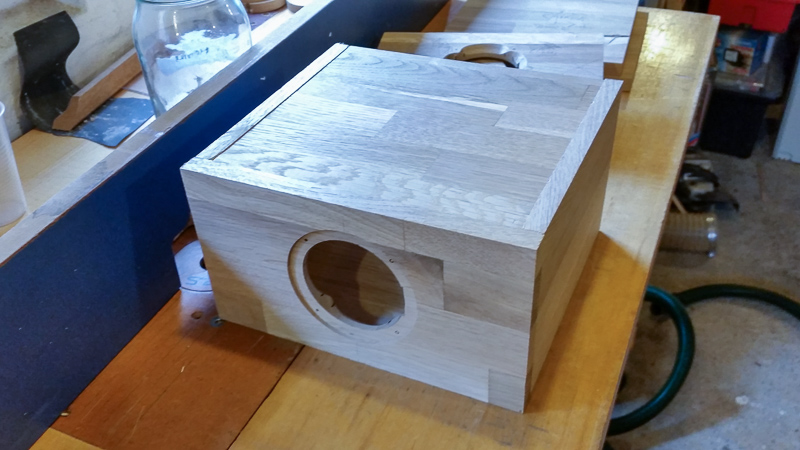
The stock is 15mm thick, and the 3mm rebate on the top/bottom panels (left/right in the photo above) is 16mm wide. This is so the edges overhang by ~1mm and can be trimmed off after glueing, for a perfect joint. The front baffle is the same width (and also over-tall) so it overhangs by ~1mm all round; again for trimming after glueing.
There's currently no rebate on the rear of the front baffle - something I'd usually do. I may add a shallow one to just help the seal to the box when glueing. This would reduce the internal volume slightly, but I've allowed for it in the cabinet depth.
Lots still to do - fixing some dampening material to the insides, cutting the rear panels (and making some fixings so they can be removed), glueing, trimming, roundovers, finishing. It may be a while before I get time to progress them but I'll post again when I do.
On a final note: solid wood and loudspeaker cabinets isn't actually a great combination (wood movement vs the need for no air leaks); hence the reason boxes are usually constructed from man made boards, and painted or veneered. With luck I'll get away with it on these boxes, as they're pretty small.