the time has come to try and make an actual bit of furniture using hand tools. I am attempting a suitably straightforward piece given my inexperience (a side table) and will be ably assisted by Richard Maquire, albeit virtually:
http://www.theenglishwoodworker.com/the ... le-guides/
I cheated and got a bit of sawn elm from St Albans Wood Recycling - a far less intimidating place to rifle through bits of wood than a proper timber yard, but not a cheap place for non-reclaimed stuff. There are two large knots about a 1/3rd of the way down, but I was just able to get enough for the bits I need from it. I *nearly* managed to avoid the sap wood for the top, but there is a small amount on one edge which I hope will be removed when I finish the top.
I did use sap wood for two of the legs, but there is not a lot of difference in colour between it and the heartwood and they will be stained black anyhow, so I hope this won't be a problem. Not a lot to report about prepping the wood other than remembering what I had learned (and subsequently forgotten) when making my bench, which is when 'being careful' starts to become 'being tentative' then things tend to work out badly. But after doing the top (slowly!) my confidence was restored somewhat and I did a more efficient job of the other bits.
This was my first attempt at jointing and gluing two boards - I added a bit of 'spring' as instructed and held it together with one clamp. I think the resulting glue line is ok but I should probably reserve judgment until I finish the top
. Having looked in the morning the glued board now has a fairly noticeable cup in it - I hope this is just the wood moving after I planed it (the boards were flat originally, honestt!) rather than incompetent jointing, but tbh I am not sure.
The joinery is going to be with bridle joints, which are a bit a mortice and tennon but with the top of the mortice lopped off. This is quite exciting as I have never done a m&t joint, and if I can pull off some of these I think I will be about 2/3rds of the way to the real thing!
Apparently bridle joints can be time consuming because you need to get an accurate fit to avoid it looking tatty and can't rely so much on compressing the wood fibres as you might with a m&t (too tight fit will cause the sides of the mortice to push apart).
To simply matters Mr Maquire has devised some simple guides to cut these joints with, so the next job is to make those. If you want more details on the guides, plans etc they can be found in the excellent video series above, which can be downloaded for a modest fee of £26.
http://www.theenglishwoodworker.com/the ... le-guides/
I cheated and got a bit of sawn elm from St Albans Wood Recycling - a far less intimidating place to rifle through bits of wood than a proper timber yard, but not a cheap place for non-reclaimed stuff. There are two large knots about a 1/3rd of the way down, but I was just able to get enough for the bits I need from it. I *nearly* managed to avoid the sap wood for the top, but there is a small amount on one edge which I hope will be removed when I finish the top.
I did use sap wood for two of the legs, but there is not a lot of difference in colour between it and the heartwood and they will be stained black anyhow, so I hope this won't be a problem. Not a lot to report about prepping the wood other than remembering what I had learned (and subsequently forgotten) when making my bench, which is when 'being careful' starts to become 'being tentative' then things tend to work out badly. But after doing the top (slowly!) my confidence was restored somewhat and I did a more efficient job of the other bits.
This was my first attempt at jointing and gluing two boards - I added a bit of 'spring' as instructed and held it together with one clamp. I think the resulting glue line is ok but I should probably reserve judgment until I finish the top
The joinery is going to be with bridle joints, which are a bit a mortice and tennon but with the top of the mortice lopped off. This is quite exciting as I have never done a m&t joint, and if I can pull off some of these I think I will be about 2/3rds of the way to the real thing!
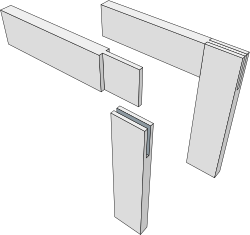
Apparently bridle joints can be time consuming because you need to get an accurate fit to avoid it looking tatty and can't rely so much on compressing the wood fibres as you might with a m&t (too tight fit will cause the sides of the mortice to push apart).
To simply matters Mr Maquire has devised some simple guides to cut these joints with, so the next job is to make those. If you want more details on the guides, plans etc they can be found in the excellent video series above, which can be downloaded for a modest fee of £26.