This afternoon someone I know wandered into the workshop and asked for advice on setting-up a small sliding carriage table saw he'd just bought. Apparently he was having difficulties trying to set the back fence on the carriage to cut square and all his pieces were tapered. Anyway I was just doing my monthly exercise of setting and checking my panel saw so I showed him how we do it on bigger machines. The technique is, however, applicable to many smaller saws, so I'll describe it here:
First Some Info
All sawblades vibrate to a greater or lesser extent. The falling teeth will tend to vibrate less as they are supported by the material being cut. A sliding carriage should be set-up to take this into account.
Setting the Free Cut - or the carriage and the saw blade don't line up exactly
Before fine-tuning the fence there must be what is called "free cut" or "freeboard" on the sliding carriage. This means that the sliding carriage doesn't run quite parallel to the blade, but that there is in effect a small amount of "toe-out" to the left of the blade. We set this by ear. The blade is wound-up to maximum height and a shortish piece of MDF (or planed timber) is butted-up against the fence and fed slowly through the blade to make what is called a "dust cut" (i.e. you are only facing a couple of millimetres off the end of the piece). As the piece is fed through listen to the sound of the rising teeth (i.e. the back of the blade) against the material - if the free cut is too small the rising teeth will make a loud noise and the carriage needs to be adjusted to the right. If the rising teeth make no sound at all then the free cut is too large and the opposite adjustment is made. Properly adjusted the rising teeth make only a slight scratching sound on the material being cut
Making the carriage Cut Bang On
Next the fence is checked making what is called a squaring cut. Take a piece of sheet material, 400 to 600 mm square (we use 1m square on a full-size panel saw) and make a dust cut one edge. Turn through 90 degrees (clockwise if the fence is at the infeed side of the carriage, anti-clockwise if it is at the outfeed side) and repeat the cut for the second edge. The idea is that the cut edge against the fence is always the one which has just been cut. Repeat the cuts for the third and fourth edges. Finally make a fifth cut, this time 5 to 10mm wide. Mark the outfeed end of this strip and break it in two. Then compare the width of the two ends of the broken strip. For an outfeed side crosscut fence: if the outfeed end of the strip is narrower then the outboard end of the fence needs to be adjusted anti-clockwise, if the outfeed end of the strip is wider then the fence needs to be adjusted clockwise. For an infeed side crosscut fence: if the outfeed end of the strip is narrower then the outboard end of the fence needs to be adjusted clockwise, if the outfeed end of the strip is wider then the fence needs to be adjusted anti-clockwise.
This is a simple way to set-up a panel saw or indeed any saw with a sliding carriage. Accurate, foolproof and doesn't require any expensive tools :wink: - so, good if you're a cheapskate like me!
Scrit
Edited to try to clarify fence positioning - hope that helps
First Some Info
All sawblades vibrate to a greater or lesser extent. The falling teeth will tend to vibrate less as they are supported by the material being cut. A sliding carriage should be set-up to take this into account.
Setting the Free Cut - or the carriage and the saw blade don't line up exactly
Before fine-tuning the fence there must be what is called "free cut" or "freeboard" on the sliding carriage. This means that the sliding carriage doesn't run quite parallel to the blade, but that there is in effect a small amount of "toe-out" to the left of the blade. We set this by ear. The blade is wound-up to maximum height and a shortish piece of MDF (or planed timber) is butted-up against the fence and fed slowly through the blade to make what is called a "dust cut" (i.e. you are only facing a couple of millimetres off the end of the piece). As the piece is fed through listen to the sound of the rising teeth (i.e. the back of the blade) against the material - if the free cut is too small the rising teeth will make a loud noise and the carriage needs to be adjusted to the right. If the rising teeth make no sound at all then the free cut is too large and the opposite adjustment is made. Properly adjusted the rising teeth make only a slight scratching sound on the material being cut
Making the carriage Cut Bang On
Next the fence is checked making what is called a squaring cut. Take a piece of sheet material, 400 to 600 mm square (we use 1m square on a full-size panel saw) and make a dust cut one edge. Turn through 90 degrees (clockwise if the fence is at the infeed side of the carriage, anti-clockwise if it is at the outfeed side) and repeat the cut for the second edge. The idea is that the cut edge against the fence is always the one which has just been cut. Repeat the cuts for the third and fourth edges. Finally make a fifth cut, this time 5 to 10mm wide. Mark the outfeed end of this strip and break it in two. Then compare the width of the two ends of the broken strip. For an outfeed side crosscut fence: if the outfeed end of the strip is narrower then the outboard end of the fence needs to be adjusted anti-clockwise, if the outfeed end of the strip is wider then the fence needs to be adjusted clockwise. For an infeed side crosscut fence: if the outfeed end of the strip is narrower then the outboard end of the fence needs to be adjusted clockwise, if the outfeed end of the strip is wider then the fence needs to be adjusted anti-clockwise.
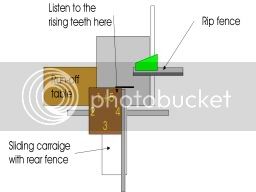
This is a simple way to set-up a panel saw or indeed any saw with a sliding carriage. Accurate, foolproof and doesn't require any expensive tools :wink: - so, good if you're a cheapskate like me!
Scrit
Edited to try to clarify fence positioning - hope that helps