jimi43
Established Member
Ok...today was the monthly trip to Axminster...as usual I had to come back with something...SO...following a chat with Peter who was busy grinding and honing planes for customers...I was persuaded into trying out some waterstones at last.
Now...I have always been an advocate of using 3M MicroMesh also known as the "Scary Sharp" system, and to date have been very satisfied.
But...as others greater than me have said MANY times before...there is always another sharpening system around the corner....so here are my thoughts...
BIG apologies for those of you who are fed up to the back teeth with sharpening chat...just ignore me!
Ok so...what did Peter con me into buying...well it was this kit:
The whole lot was £55 which I think is rather steep...it would keep me in 3M paper for about a year...but I was assured by Peter's results that it was good value. Well he works there so he would say that I guess!
I have read that some do not get on with waterstone...nor do they produce a particularly sharp edge...but I wanted to see for myself..being an obstinate pipper.
The two stones that come with the kit are 800 and 6000 grit. The 800 is sold as "for grinding" and the 6000 is for polishing/honing.
The kit also comes with a rather nifty rubber stand which works brilliantly! It is so simple but really really effective and the stones don't budge an inch.
I had a feeling that the flattening of the back would be more successful than papers...as the stone is perfectly flat...and indeed it was. My old Stanley iron was a tad out of flat..but the 800 grit soon sorted that out bringing one of the edges of the cutting face into true.
I then mounted the iron in the Veritas honing jig and tried to sharpen the bevel. This I found too slow...and I got bored really quickly. In the end I resorted to using some 1500 mesh 3M cloth first....THEN moving on to the 800 grit stone. This worked perfectly...and I finished off the bevel with the 6000 and then a microbevel with the knob on the jig...just a few strokes.
The results?
MESSY! Very very very messy!
I felt like a blinkin' potter who has had an accident with a pot at a thousand revs.....
But was the iron sharper than before?
Absolutely YES!
Using my acid test of the same old piece of pine...and the pot..the transparency was greatly improved:
Now you can't feel this but I can assure you...this is paper..and very thin paper at that...
Even with beech!
And the smoothness of the final stock is just like silk...
So...am I convinced that these things work...
Well let's just say...THANKS PETER!!
I think this combination of the Micro-mesh and the waterstone is a good marriage...I may even ditch the finer meshes and just get a large sheet of 1500 mesh then move to waterstones in future...we shall see.
Now I am off for another hour to sharpen my No.4 1/2....I can hardly wait to see how that turns out!
I would be interested in any experiences of others here...
I guess "Ice Bear" are fairly "middle-of-the road" as far as quality is concerned...but I think it was money well spent...
Jim
Jim
Now...I have always been an advocate of using 3M MicroMesh also known as the "Scary Sharp" system, and to date have been very satisfied.
But...as others greater than me have said MANY times before...there is always another sharpening system around the corner....so here are my thoughts...
BIG apologies for those of you who are fed up to the back teeth with sharpening chat...just ignore me!
Ok so...what did Peter con me into buying...well it was this kit:
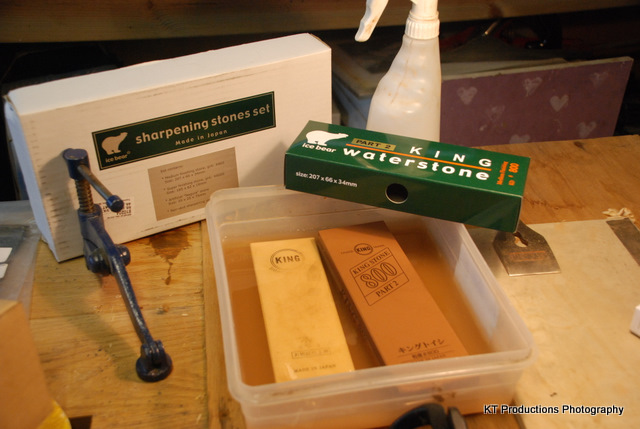
The whole lot was £55 which I think is rather steep...it would keep me in 3M paper for about a year...but I was assured by Peter's results that it was good value. Well he works there so he would say that I guess!
I have read that some do not get on with waterstone...nor do they produce a particularly sharp edge...but I wanted to see for myself..being an obstinate pipper.
The two stones that come with the kit are 800 and 6000 grit. The 800 is sold as "for grinding" and the 6000 is for polishing/honing.
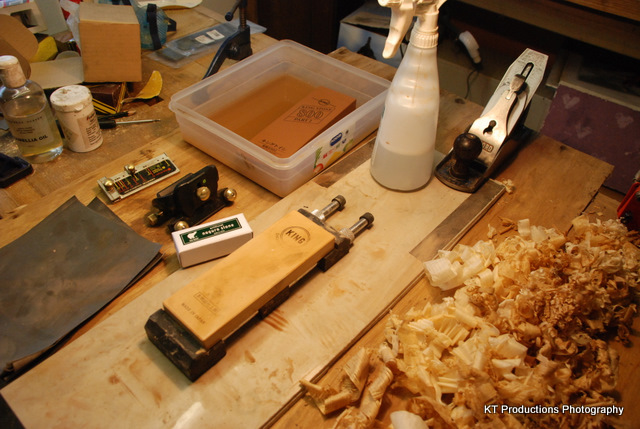
The kit also comes with a rather nifty rubber stand which works brilliantly! It is so simple but really really effective and the stones don't budge an inch.
I had a feeling that the flattening of the back would be more successful than papers...as the stone is perfectly flat...and indeed it was. My old Stanley iron was a tad out of flat..but the 800 grit soon sorted that out bringing one of the edges of the cutting face into true.
I then mounted the iron in the Veritas honing jig and tried to sharpen the bevel. This I found too slow...and I got bored really quickly. In the end I resorted to using some 1500 mesh 3M cloth first....THEN moving on to the 800 grit stone. This worked perfectly...and I finished off the bevel with the 6000 and then a microbevel with the knob on the jig...just a few strokes.
The results?
MESSY! Very very very messy!
I felt like a blinkin' potter who has had an accident with a pot at a thousand revs.....
But was the iron sharper than before?
Absolutely YES!
Using my acid test of the same old piece of pine...and the pot..the transparency was greatly improved:
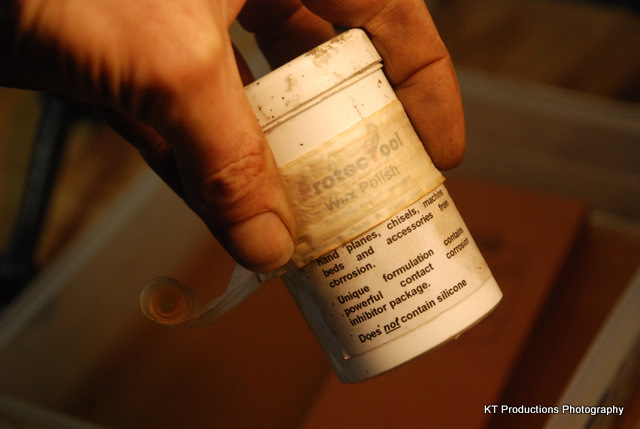
Now you can't feel this but I can assure you...this is paper..and very thin paper at that...
Even with beech!
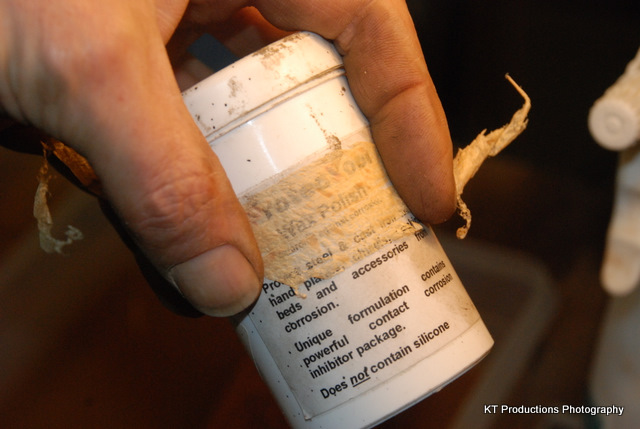
And the smoothness of the final stock is just like silk...
So...am I convinced that these things work...
Well let's just say...THANKS PETER!!
I think this combination of the Micro-mesh and the waterstone is a good marriage...I may even ditch the finer meshes and just get a large sheet of 1500 mesh then move to waterstones in future...we shall see.
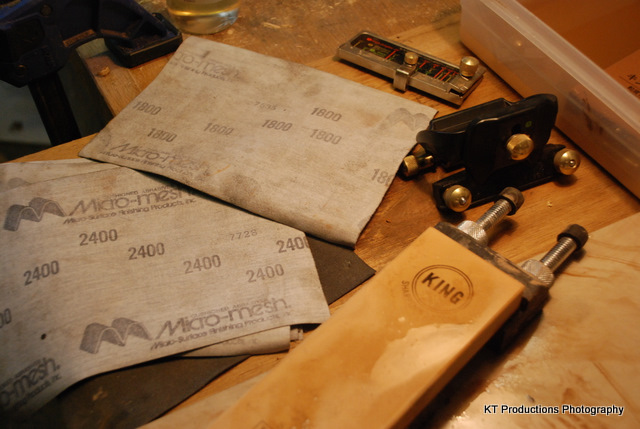
Now I am off for another hour to sharpen my No.4 1/2....I can hardly wait to see how that turns out!
I would be interested in any experiences of others here...
I guess "Ice Bear" are fairly "middle-of-the road" as far as quality is concerned...but I think it was money well spent...
Jim
Jim