sploo
Somewhat extinguished member
A couple of months ago, I snapped the tensioning rod on my Record Power BS300 bandsaw. I'd just about gotten enough tension in the blade, and needed the saw for a project, so didn’t want to risk stripping it down immediately (on the assumption I might have difficulties getting it back together).
I’ve finally gotten around to fixing it, and it turned out to be a whole lot easier than I thought. I had a replacement rod from Record, but realised I could make my own - thus avoiding the weak link in their design. Hopefully this post might be useful to fellow BS300 owners.
Here's the starting point:
This shot shows the top of the tensioning rod. It turns out it’s just an 8mm threaded rod, with a short section turned to a smaller diameter and pinned into a sleeve that takes the plastic knob. The pinned link strikes me as an odd design, and it’s where mine snapped (hence the fact the sleeve and knob are not in this photo).
Here’s what it looks like with the wheel removed.
The actual tensioning cradle mechanism as a whole isn’t bad - it pivots on a rod, that allows a lever to quickly release the blade tension. In this photo you can just see the bolt in the back of the machine body (that pushes at the back of the cradle to adjust tracking).
The system appears pretty simple: at the bottom there’s a plate that compresses a spring, with a trapped nut (for the threaded rod). There’s the silver (aluminium, I guess) block with the wheel spindle, then a washer/tube/washer arrangement is held in place by two nuts that are locked together.
Here it is dismantled, along with the top sleeve and plastic knob not shown in the original image.
I realised that the sleeve just rests on the top of the black cradle (with a washer underneath), but there’s no tension on that part of the rod (mine snapped due to twisting movement). That meant I could just use an M8 threaded rod, and another pair of nuts (locked together) to rest on top of the cradle, and add a new handle/knob on the top of machine - thus I’d avoid using the original design with its weak link. I’ve just realised I’ve used a sentence with the words "nuts" and "knob" and wasn’t trying to be crude :mrgreen:.
I made new winder handle from a piece of oak. It has a tee nut on the bottom, and the dowel is loose, so can be spun.
The gap between the original pair of locked nuts and the bottom of the sleeve looked to be about 15mm, so I replicated that with the extra pair. The end result is pretty good, and much easier to tension than with the old round plastic knob.
There’s a reasonably large hole at the top of the machine (for the sleeve and knob), and it’s elongated to account for the fact the cradle could be tipped with the tracking bolt.
With no sleeve/knob in place I’d noticed that the machine does put a fair bit of dust out the top, so I put a thin plate over the hole with a section that fits into the hole (as the winder handle does cause the rod to wobble around a bit when being spun). I'm hoping that will reduce the lateral movement.
And finished...
A good clean and tuneup, and she's running sweetly again.
I’ve finally gotten around to fixing it, and it turned out to be a whole lot easier than I thought. I had a replacement rod from Record, but realised I could make my own - thus avoiding the weak link in their design. Hopefully this post might be useful to fellow BS300 owners.
Here's the starting point:
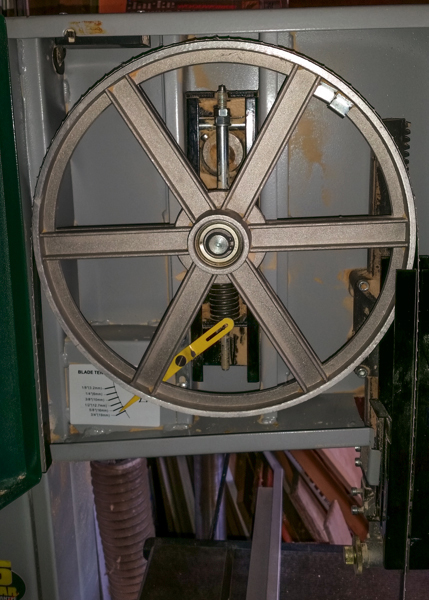
This shot shows the top of the tensioning rod. It turns out it’s just an 8mm threaded rod, with a short section turned to a smaller diameter and pinned into a sleeve that takes the plastic knob. The pinned link strikes me as an odd design, and it’s where mine snapped (hence the fact the sleeve and knob are not in this photo).
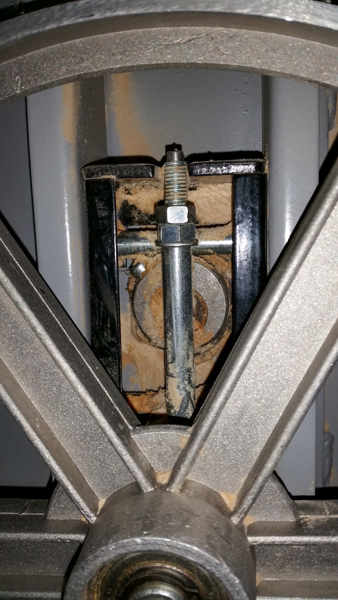
Here’s what it looks like with the wheel removed.
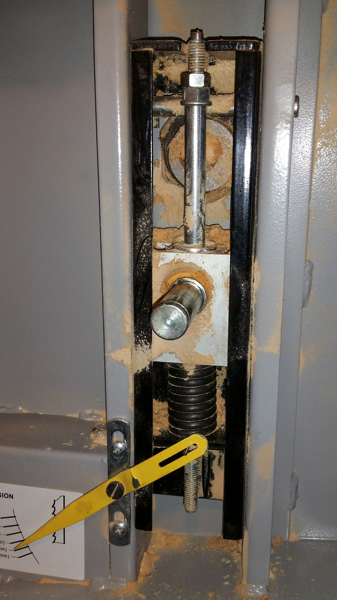
The actual tensioning cradle mechanism as a whole isn’t bad - it pivots on a rod, that allows a lever to quickly release the blade tension. In this photo you can just see the bolt in the back of the machine body (that pushes at the back of the cradle to adjust tracking).
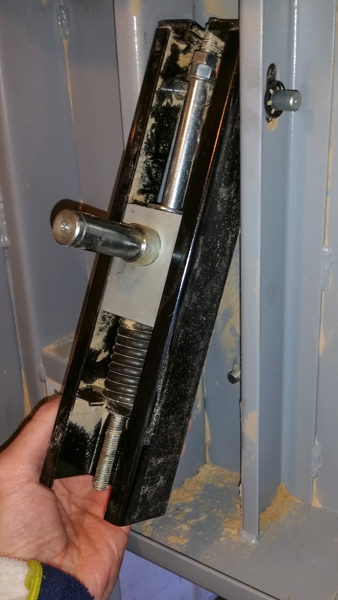
The system appears pretty simple: at the bottom there’s a plate that compresses a spring, with a trapped nut (for the threaded rod). There’s the silver (aluminium, I guess) block with the wheel spindle, then a washer/tube/washer arrangement is held in place by two nuts that are locked together.
Here it is dismantled, along with the top sleeve and plastic knob not shown in the original image.
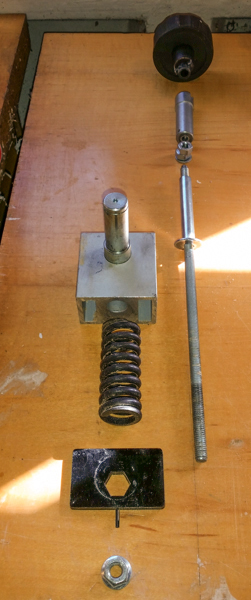
I realised that the sleeve just rests on the top of the black cradle (with a washer underneath), but there’s no tension on that part of the rod (mine snapped due to twisting movement). That meant I could just use an M8 threaded rod, and another pair of nuts (locked together) to rest on top of the cradle, and add a new handle/knob on the top of machine - thus I’d avoid using the original design with its weak link. I’ve just realised I’ve used a sentence with the words "nuts" and "knob" and wasn’t trying to be crude :mrgreen:.
I made new winder handle from a piece of oak. It has a tee nut on the bottom, and the dowel is loose, so can be spun.
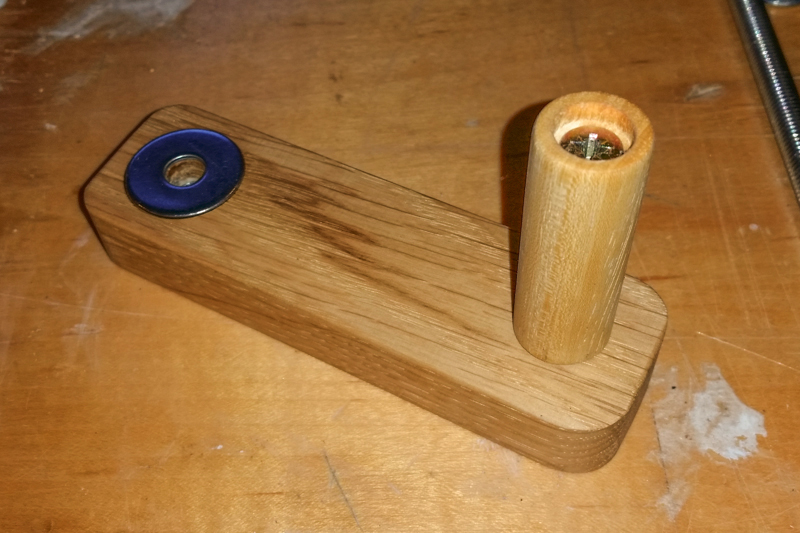
The gap between the original pair of locked nuts and the bottom of the sleeve looked to be about 15mm, so I replicated that with the extra pair. The end result is pretty good, and much easier to tension than with the old round plastic knob.
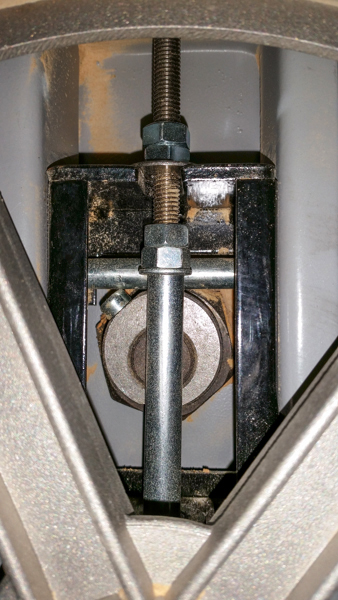
There’s a reasonably large hole at the top of the machine (for the sleeve and knob), and it’s elongated to account for the fact the cradle could be tipped with the tracking bolt.
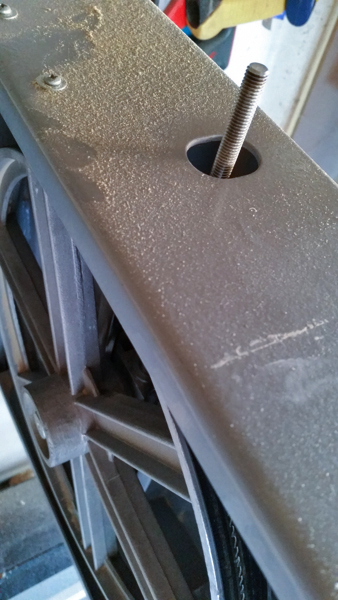
With no sleeve/knob in place I’d noticed that the machine does put a fair bit of dust out the top, so I put a thin plate over the hole with a section that fits into the hole (as the winder handle does cause the rod to wobble around a bit when being spun). I'm hoping that will reduce the lateral movement.
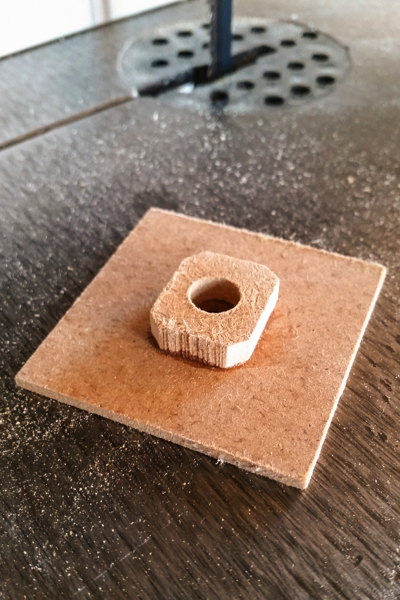
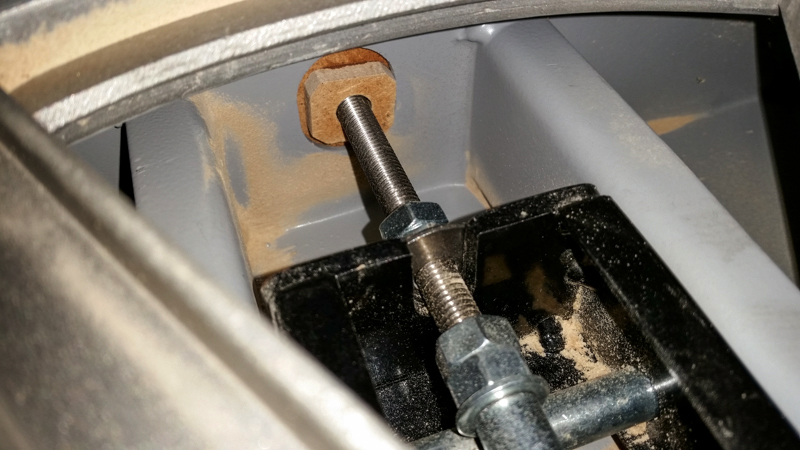
And finished...
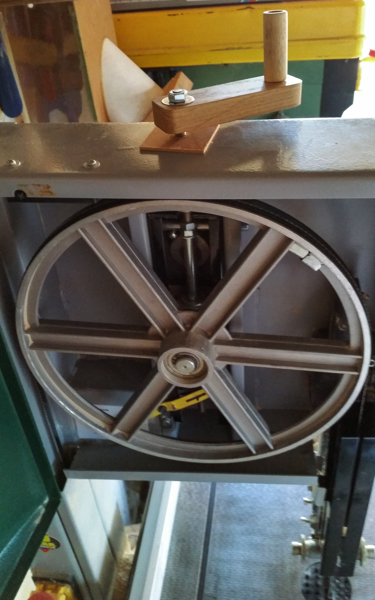
A good clean and tuneup, and she's running sweetly again.