I always thought record t bar clamps were the best general purpose clamps money could buy. Over the years I've acquired quite a few.
I was setting the scriber up on the tenoner, but it was proving alot more difficult than it should be. Pushing the joints together by hand, all was well, introducing the sash clamps caused a slight gap on one of the shoulders, not quite half a mm but still frustrating.
I've known for a while the slidey part of the clamp wasn't square under pressure, just hadn't realised it was quite so much. I've often found I had to leave a clamp on the odd wedged joint, because one shoulder was ever so slightly gappy. The slidey part being out of square, wouldn't help.
That's the worst one, it must be 3mm out of square under pressure !!!!
The threaded end always seemed fine. It's pushing in the middle of the clamp head so even though it's sloppy on the rail, it's always uptight to what ever it's clamping.
The easiest fix would have been to glue a tapered wedge to the offending clamp head, or wedge the head off the rail somehow with a wedge to keep it pushed up tight . Neither of these ideas seemed very good, in terms of durability and ease of use. Ideally replicating the way the threaded end worked, seemed the best solution. It needed something that would put pressure in the middle of the head, but also allow movement of the face of the clamp(to correct the out of square/sloppyness)
These are the clamp heads, centre punched and ready to drill. With the coolant running they drill quite easily.
This was the proto type assembly. I had some 10mm thick steel 50×60mm and tapped a hole right through it to accept an m8 threaded bar. The bar was then welded in position by welding the hole, then grinding flush. The clamp head had a 9.5mm hole which allowed plenty of movement. A couple washers allow the head to pivot easier and the spring washer near the nylon washered nut, just keeps it under a tiny bit of tension.
It's seemed to work really well so didn't hesitate altering the rest.
I've given them a quick wipe of machine wax, so hopefully they'll stay fairly clean. I'd say 80% of the stuff I clamp is either 44 or 57mm thick, so this should really help ! Glued up several doors and sashes over the last few days and so far, it seems like a good modification.
The lighter duty record clamps had the same treatment
They were no where near as bad as the t bars, but thought it worth doing.
Seems odd that a decent branded clamp could cause issues instead of curing them, but it certainly seems to be the case.
Just for a laugh, I tried a square on some really old record clamps. ....
They really don't make em like they use to, do they !?!?!!!! (100% bang on square) :lol:
Cheers
Coley
I was setting the scriber up on the tenoner, but it was proving alot more difficult than it should be. Pushing the joints together by hand, all was well, introducing the sash clamps caused a slight gap on one of the shoulders, not quite half a mm but still frustrating.
I've known for a while the slidey part of the clamp wasn't square under pressure, just hadn't realised it was quite so much. I've often found I had to leave a clamp on the odd wedged joint, because one shoulder was ever so slightly gappy. The slidey part being out of square, wouldn't help.
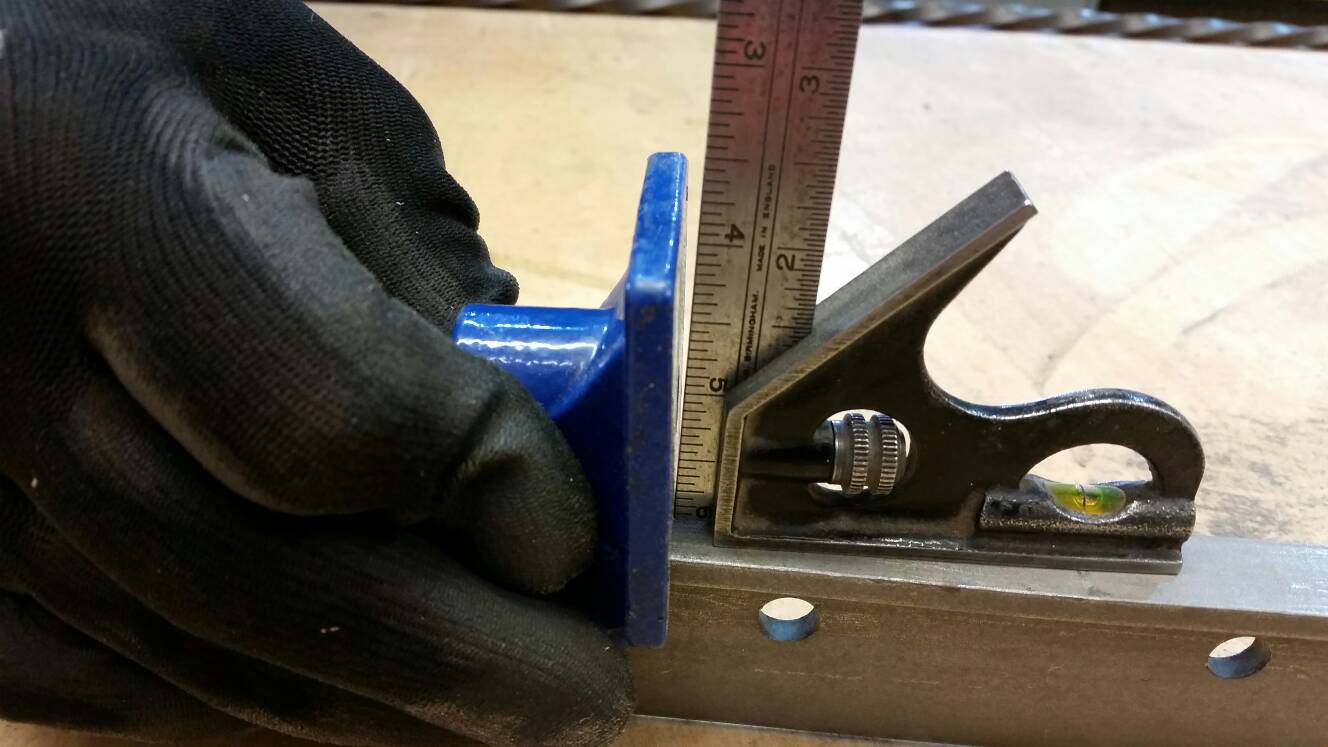
That's the worst one, it must be 3mm out of square under pressure !!!!
The threaded end always seemed fine. It's pushing in the middle of the clamp head so even though it's sloppy on the rail, it's always uptight to what ever it's clamping.
The easiest fix would have been to glue a tapered wedge to the offending clamp head, or wedge the head off the rail somehow with a wedge to keep it pushed up tight . Neither of these ideas seemed very good, in terms of durability and ease of use. Ideally replicating the way the threaded end worked, seemed the best solution. It needed something that would put pressure in the middle of the head, but also allow movement of the face of the clamp(to correct the out of square/sloppyness)
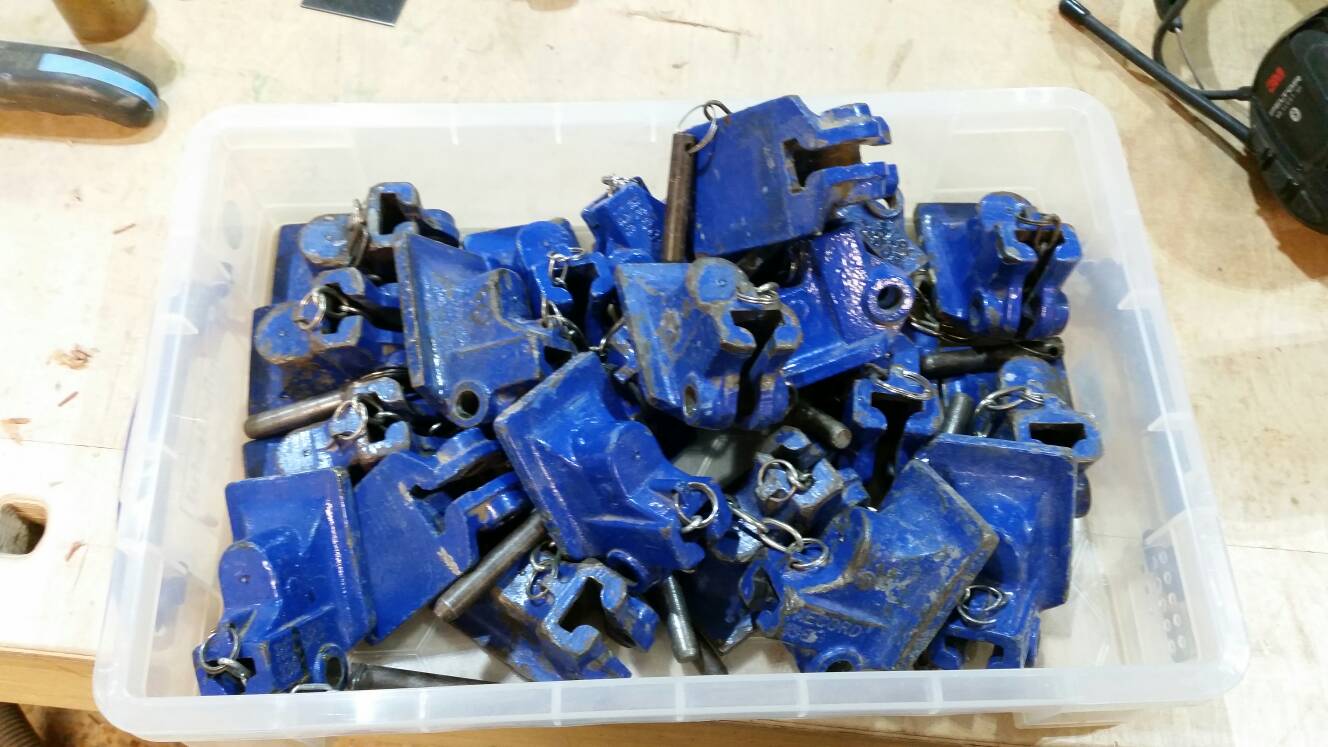
These are the clamp heads, centre punched and ready to drill. With the coolant running they drill quite easily.
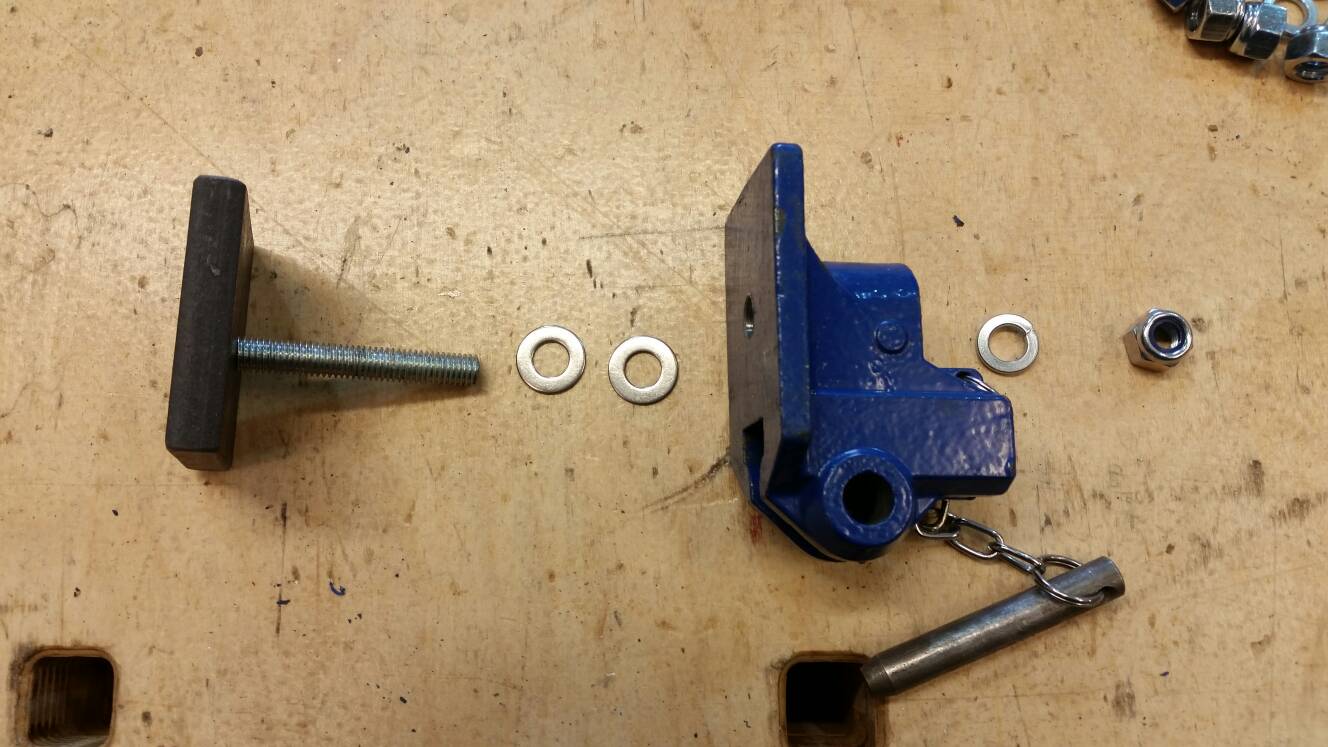
This was the proto type assembly. I had some 10mm thick steel 50×60mm and tapped a hole right through it to accept an m8 threaded bar. The bar was then welded in position by welding the hole, then grinding flush. The clamp head had a 9.5mm hole which allowed plenty of movement. A couple washers allow the head to pivot easier and the spring washer near the nylon washered nut, just keeps it under a tiny bit of tension.
It's seemed to work really well so didn't hesitate altering the rest.




I've given them a quick wipe of machine wax, so hopefully they'll stay fairly clean. I'd say 80% of the stuff I clamp is either 44 or 57mm thick, so this should really help ! Glued up several doors and sashes over the last few days and so far, it seems like a good modification.
The lighter duty record clamps had the same treatment

They were no where near as bad as the t bars, but thought it worth doing.
Seems odd that a decent branded clamp could cause issues instead of curing them, but it certainly seems to be the case.
Just for a laugh, I tried a square on some really old record clamps. ....

They really don't make em like they use to, do they !?!?!!!! (100% bang on square) :lol:
Cheers
Coley