Ironballs
Established Member
Still not carving yet, can't believe it!
Well all the back cavities are routed out and I've rounded over the edge on the back too whilst the top was flat. Before that though I had to hand sand the edges to smooth off and take out the lumps and bumps left by the bobbin sander, not a quick job when you're doing it on 2 bodies. Fair crippled me but at least they only need a finish sand now. Also planed square the heel area where the neck is to join, took a while as it does need to be square and flat.
Then marked the limit of the top carve around the edge - quite a bit of wood to be removed there, it's best not to think about wastage when making guitars :shock:
Also started rough drafting where the various carves are going to be on the top, back is not far off but I need to redo the waist and front as the transition is much sharper in places.
Did some more jig making this week (fed up with making jigs), this one was to enable me to accurately plane the neck angle and pick up angle. Decided to make a little platform that would sit over the body, both clamped in place and then rout from above and cross fingers with tearout. Took me all of this weeks class to make this damn jig, Steve Maskery would not be proud
Once this is done I'll make yet another template and rout out the neck pocket and after that I can put off the carving no longer...
Well all the back cavities are routed out and I've rounded over the edge on the back too whilst the top was flat. Before that though I had to hand sand the edges to smooth off and take out the lumps and bumps left by the bobbin sander, not a quick job when you're doing it on 2 bodies. Fair crippled me but at least they only need a finish sand now. Also planed square the heel area where the neck is to join, took a while as it does need to be square and flat.
Then marked the limit of the top carve around the edge - quite a bit of wood to be removed there, it's best not to think about wastage when making guitars :shock:
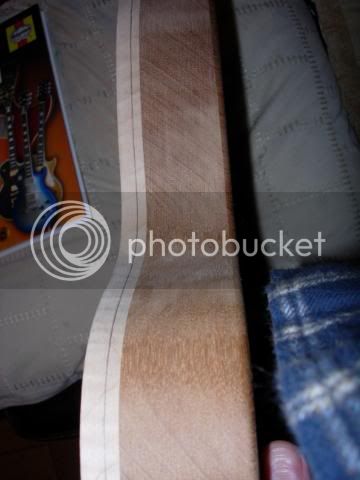
Also started rough drafting where the various carves are going to be on the top, back is not far off but I need to redo the waist and front as the transition is much sharper in places.

Did some more jig making this week (fed up with making jigs), this one was to enable me to accurately plane the neck angle and pick up angle. Decided to make a little platform that would sit over the body, both clamped in place and then rout from above and cross fingers with tearout. Took me all of this weeks class to make this damn jig, Steve Maskery would not be proud
Once this is done I'll make yet another template and rout out the neck pocket and after that I can put off the carving no longer...
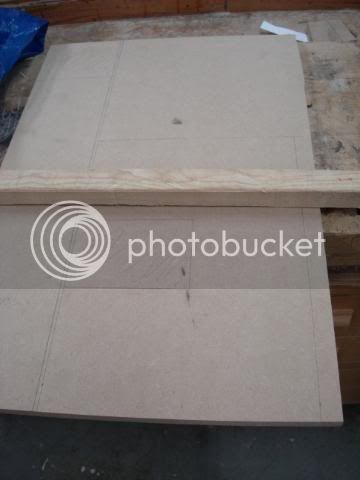
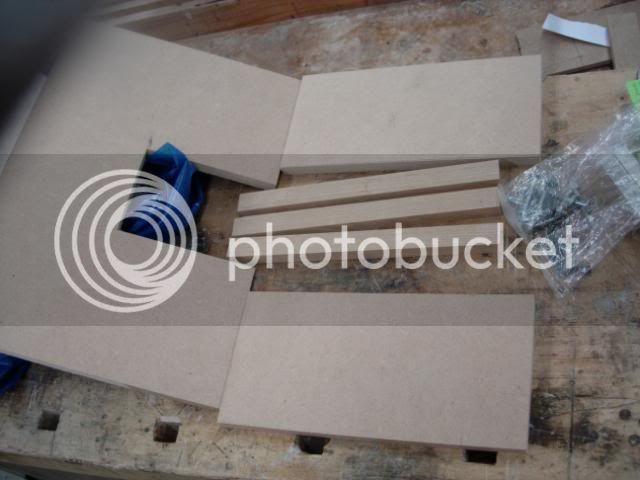
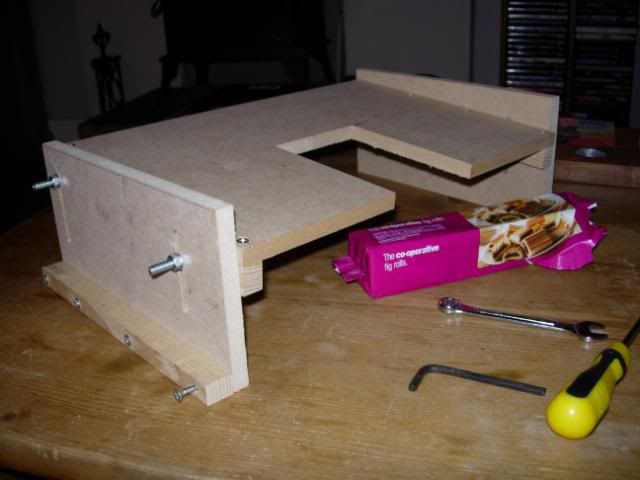