I decided it was time to put this thing together once and for all.
Pegs through the large mortices
I used a long drill bit to put a pilot hole all the way through the mortice then using my 20mm spade bit I carefully drilled the holes all the way through.
I then took my home made 20mm dowel (which I turned earlier) and popped it through - perfect fit.
Capping the screw holes
Took my homemade plugs, smeared on some Titebond and pushed them in the holes. I'll flush cut them next time when they've set properly.
Bench top
Final job for tonight is to glue the bench top up. I previousley cut biscuit slots along all edges so it really wwas a case of just glue up, push together, clamp up and leave it.
Next visit should be a sanding session. I'll probably sand down all the legs etc then attach and plane the top, ready for my cap.
Shall I use 15mm MDF of 15mm birch plywood for the top?
Pegs through the large mortices
I used a long drill bit to put a pilot hole all the way through the mortice then using my 20mm spade bit I carefully drilled the holes all the way through.
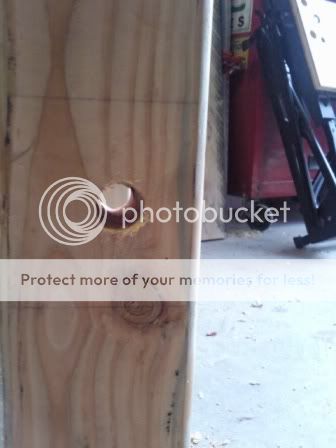
I then took my home made 20mm dowel (which I turned earlier) and popped it through - perfect fit.
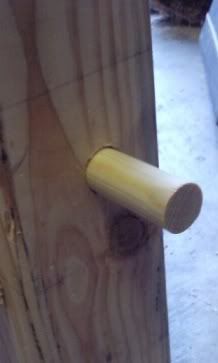
Capping the screw holes
Took my homemade plugs, smeared on some Titebond and pushed them in the holes. I'll flush cut them next time when they've set properly.
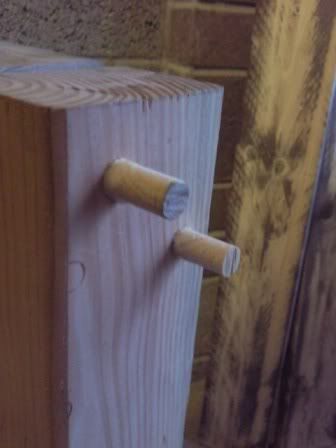
Bench top
Final job for tonight is to glue the bench top up. I previousley cut biscuit slots along all edges so it really wwas a case of just glue up, push together, clamp up and leave it.
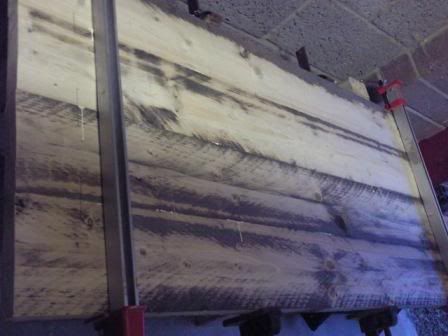
Next visit should be a sanding session. I'll probably sand down all the legs etc then attach and plane the top, ready for my cap.
Shall I use 15mm MDF of 15mm birch plywood for the top?